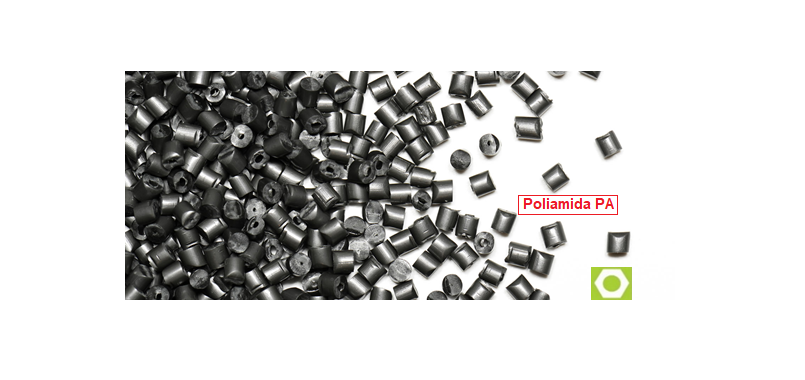
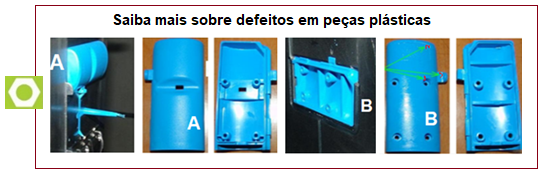
Indicações para processamento de diferentes materiais plásticos – 01
Poliestireno PS — Poliestireno de alto Impacto SB — Copolímeros de estireno-acrilonitrilo SAN — Polímeros ABS — Poliamida PA — Polietileno PE – Polipropileno PP –
1 – Poliestireno PS
Densidade: 1,05 glcm3
Características do material: duro, rígido, frágil, excelentes propriedades elétricas e dielétricas, baixa absorção de umidade, elevada estabilidade dimensional, transparente, brilhante, facilmente pigmentável, insípido e inodoro.
Resistente á: ácidos, bases, álcool, graxas, óleos, soluções salinas.
Não resistente à: gasolina, benzol, muitos dissolventes, risco de ruptura por tensão.
Reconhecimento do material: PS é facilmente inflamável, queima com forte luz, deixa muita fuligem e cheiro tipicamente adocicado.
Pressão de injeção: por sua boa fluidez não precisa de pressões muito elevadas.
Recalque: tempo de recalque relativamente curto. Pressões geralmente a 30 -60 % da pressão de injeção.
Contrapressão: 100 .200 bar. Com contrapressão muito baixa, sobreaquecimento de ar na massa.
Temperatura do cilindro
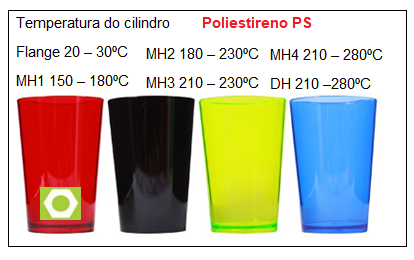
Velocidade de injeção: depende da geometria da peça. Para peças de parede fina, tão rapidamente quanto possível.
Rotações da rosca: são possíveis altas rotações da rosca, se bem que é preferível plastificar de acordo com o tempo de resfriamento.
Enchimento de material: 2 – 6 mm, segundo volume de dosagem.
Temperatura do molde: 10 – 500C.
Pré-secagem: não é necessário.
Reaproveitamento: pode reaproveitar – 100% como material moído.
Contração: aproximadamente 0,45%.
Volume de injeção: 5 – 95% do volume do cilindro podem ser aproveitados.
Equipamento do cilindro: bico aberto, válvula de retenção (RSP).
Parada da máquina: não é necessário passar nenhum material para limpar o cilindro. Material térmico insensível.
Injeção das peças: canal de entrada em ponto, canal câmara quente, canal isolante, câmara prévia. São suficientes seções relativamente pequenas.
2 – Poliestireno de Alto Impacto – SB
Densidade: 1,05 glcm3
Características do material: duro, rígido, pouco frágil. pelo conteúdo em butadieno é opaco, pigmentável absorção de umidade maior que o poliestireno. Processado como o potiestireno normal, eventualmente pré-secado.
Resistente à: ácidos, bases, álcoois, graxas, óleos, soluções salinas, detergentes.
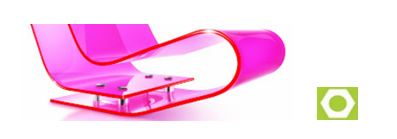
3 – Copolímeros de estireno-acrilonitrilo. SAN
Características do material: duro, rígido, brilhante, resistente a trocas térmicas, mais resistente que o PS. Cristalino, transparente e opaco, colorável (tingível), maior absorção de umidade, hidratação que o PS. Sem risco para a saúde, colável e soldável.
Resistente à: ácidos, bases, álcoois, graxas, óleos, soluções salinas, gasolina. Processado como o Poliestireno.
4 – Polimeros ABS – Polimerizados mistos
Densidade: 1.06 – 1,1 g/cm3
Caracteristicas do material: Duro, tenaz até -40°C1 alta resistência à temperatura, resistente ao frio e ao calor (1SOOC). opaco, coberto em cor, resistência à intempérie, condicional baixa absorção de umidade, sem risco à saúde, metalizável galvanicamente.
Resistente à: ácidos, bases, hidrocarbonetos, óleos, graxas, (material especial também cristalino).
Não resistente à: acetona, éter, benzoletílico, cio reto etílico, cloretoetilênico, anilina, essência de anis.
Temperatura do cilindro
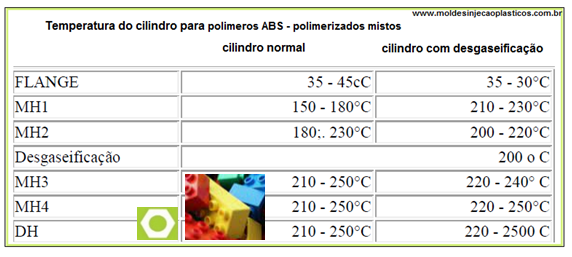
Pressão de injeção: 1.000 – 1.500 bar.
Recalque: pressão de recalque relativamente curta, aproximadamente 30 – 60% da pressão da injeção.
Contrapressão: Cilindro normal. 100.250 bar. Com baixa contrapressão, sobre aquecimento de ar na massa.
Desgaseificação: 20 – 50 bar. Em caso de contrapressão muito alta, ocorre saída de massa de material pela chaminé de desgaseificação.
Velocidade de injeção: escalonamento vantajoso, primeiro lento, depois injeção rápida.
Rotação da rosca: o uso da rotação máxima é possível. Recomendamos plastificar com uma velocidade tal, que esta termine durante o processo de resfriamento.
Enchimento de material: 2.6 mm, de acordo com volume de dosagem.
Temperatura do molde: 30 -80. Quanto mais elevada a temperatura do molde, melhor será a qualidade da superfície. Ao mesmo tempo, a incidência de junções diminui de acordo com o aumento da temperatura do molde.
Pré-secagem: em geral pode ser usado diretamente da embalagem original sem pré-secagem. Se necessário, pré-secar por 4 h a 80°c. Material granulado hidroscópico provoca bolhas. marcas de estrias, etc. Não é necessário como cilindro de desgaseificação.
Material recuperado: caso não afetado termicamente, poderá ser adicionado até 30% com material virgem.
Contração: 0,4 .0,7°/0.
Volume de injeção: Cilindro normal. 10 – 90% do volume do cilindro é aproveitável.
Desgaseificação: 20.80% do volume do cilindro.
Preparação do cilindro: bico aberto e válvula de bloqueio (RSP).
Desligamento da máquina: Não é necessário limpar o cilindro com outro material.
Ponto de injeção: é possível a injeção em ponto, como também o canal de calor e de isolamento. A espessura mínima de parede não deve ser menor que 0,7 mm.
5 – Poliamida PA
Densidade: 1,14 g/cm3
Características do material: tenaz em estado úmido (2 – 30ío), frágil em estado seco. Duro, rígido, resistente ào atrito. bom comportamento em deslizes, opaco, amarelo, bom tingimento, sem risco para a saúde, soldável, colável.
Resistente à: óleos. gasolina, benzol, bases dissolventes. detergente, hidrocarboneto clorado, ésteres. cetonas, água.
Não resistente à: ozônio, ácido clorídrico, ácido sulfúrico, superóxido de hidrogênio.
Reconhecimento do material: PA é inflamável, continuando aceso depois de retirar o foco do fogo, goteja em borbulhas, puxa fios. A chama é azulada de contorno amarelo. Cheiro de osso queimado.
Pressão de Injeção e de recalque: não deixe nem muito alta e nem longa.
Contrapressão: Cilindro normal. Ajuste muito precisamente a 50 – 150 bar.
Desgaseificação 20 -50 bar. No caso de contrapressão muito alta ocorre saída de massa de material pela chaminé de desgaseificação.
Velocidade de injeção: injete relativamente rápido. Promova a ventilação do molde (exaustão), pois caso contrário ocorrerá combustão da peça.
Rotação da rosca: possibilidade de altas rotações da rosca. É melhor regular o número de rotações da rosca, de modo que o processo de plastificação acabe um pouco antes do resfriamento.
Enchimento de material: 2-6mm, conforme o volume de dosagem.
Temperatura do molde: 60-900C.Em peças técnicas de baixa tolerância até 1000c.
Pré secagem: com o cilindro de desgaseificação MO é necessário. As poliamidas alo hidroscópicas, por isso devem ser armazenadas em recipientes fechados e impermeáveis. Feche a tampa do funil com umidade maior que 0,250/0 dificuldades de processamento. Processe diretamente dos tonéis, caso contrário, submeta a uma pré-secagem a BO e durante 16 horas.
Reaproveitamento: é possível adicionar 10 – 20% de recuperado ao material.
Volume de injeção: Cilindro normal. Pode-se aproveitar entre 15 – 80% do volume do cilindro.
Desgaseificação: 20 – 800e do volume do cilindro.
Equipamento do cilindro: bico valvulado e bico aberto, válvula de retenção (RSP).
Parada da máquina: não é necessário passar outro material pelo cilindro.
Possibilidade de um tempo de permanência da massa de até 20 minutos, depois disso o material deteriora-se.
Injeção das peças: canal de
entrada por pontos, (canal submarino também pos¬sivel), canal contraste por
filme, ângulo cônico 3,5 – 5°e. Recomenda-se labirintos para recolher gotículas
frias. As peças com uma temperatura de trabalho superior a 600 e devem ser
temperadas (condicionamento em vapor de água é o mais favorável).
Os artigos de poliamida podem ser testados, em relação às tensões, com ácido de
soldar.
6 – Polietileno PE
Densidade: 0,92.0,96 glcm3
Características do material: Material bastante flexível, até macio, de acordo com a densidade. Resistente ao frio até -400e, resistente a golpes, inquebrável, boas propriedades dielétricas, baixa hidroscopia, sem risco à saúde, sem cheiro forte.
Resistente à: ácidos, bases, dissolventes, álcoois, gasolina, água, óleo, sumo de frutas.
Não resistente à: aromatizantes, hidrocarbonetos clorados, com risco de ruptura por tensão.
Reconhecimento do material: PE é
facilmente inflamável, continuando aceso, goteja, chama clara com núcleo
azulado. Cheira como parafina (vela apagada).
Exemplos de aplicação: artigos domésticos, baldes, brinquedos, recipientes,
tubos.
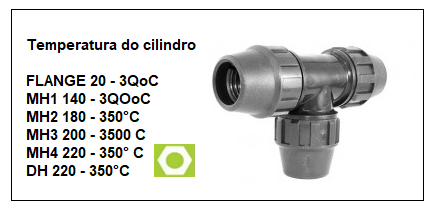
Pressão de injeção: devido à sua boa fluidez, não é necessário ser alta.
Recalque: devido à contração relativamente alta, é necessário longo tempo de recalque nas peças técnicas, aproximadamente de 30 – 60°/0 da pressão de injeção.
Contrapressão: 100 – 250 bar. Com baixa pressão, peso da peça desigual
Velocidade de injeção: para artigos de embalagem com paredes finas, precisam-se altas velocidades de injeção. Em outros casos a velocidade de injeção já é mais vantajosa.
Rotações da rosca: a regulagem do número de rotações da rosca é possível. A velocidade deve ser regulada de tal forma, porém, que o processo de plastificação termine durante o tempo de resfriamento.
Enchimento de material: 2 – 6 mm, de acordo com volume de dosagem.
Temperatura do molde: 0 – 50°C.
Secagem prévia: não é necessária.
Reaproveitamento: pode reaproveitar 100°/0 recuperado, como material moído.
Contração: 1,5 – 2°10, maior contração, maior torsão
Volume de Injeção: 5 – 95% do
volume do cilindro podem ser aproveitados.
Equipamentos do cilindro: Bico aberto, bico valvulado de agulha. Válvula de
bloqueio (RSP).
Parada da máquina: não é necessário passar nenhum material. Material térmico muito insensível.
Injeção das peças: canal de entrada de pontos, canal quente, canal isolado. câ¬mara prévia de pontos. São suficientes seções relativamente pequenas.
7 – Polipropileno PP
Densidade: 0,91 a 0,93 glcm3
Características do material: Este material é mais duro e resistente à temperatura que o PE (Polietileno), mas menos resistente ao frio. É apropriado especialmente para bisnagas. Duro, pesado, frágil, características dielétricas muito boas, esterilizável a 120°C, sem risco para a saúde, sem cheiro forte.
Resistente à: ácidos, bases, sais, álcoois, gasolina, óleos, sumo de frutas.
Não resistente à: hidrocarbonetos clorados, evite contato com cobre, pouca tendência à formação de ruptura por tensão. Reconhecimento do material: PP é facilmente inflamável, goteja e continua aceso. Tem chama clara com núcleo azulado, cheira a parafina (vela).
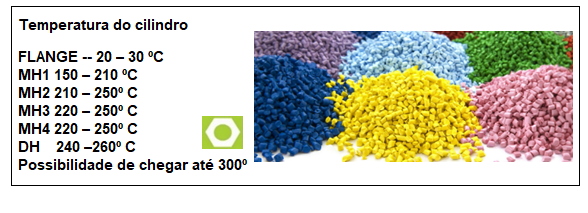
Pressão de injeção: maior pressão de injeção necessária: 1.200 – 1.800 bar.
Recalque: para evitar pontos de depressão é necessário um tempo prolongado de recalque (cerca de 500/0 do tempo do cicio).
Valor da pressão: aproximadamente 40 – 800/0 da pressão de injeção.
Contrapressão: 100 – 200 bar.
Velocidade de injeção: necessário uma elevada velocidade de injeção.
Rotações da rosca: a regulagem do número de rotações da rosca é possível. A velocidade deve ser regulada de tal forma, porém, que o processo de plastificação termine durante o resfriamento.
Enchimento de material: 2 – 6 mm, de acordo com o volume de dosagem.
Temperatura do molde: 20- 60oC. Quanto mais alta a temperatura do molde, melhor será a superfície das peças.
Secagem prévia: não é necessária.
Reaproveitamento: possível com até 1000/0 de material moído.
Contração: 1,2.2,2%.
Volume de injeção: podemos aproveitar de 10 .. 90%.
Equipamentos do cilindro: bico aberto com válvula de retenção (RSP), Bico valvulado agulhado condicionalmente aproveitável.
Parada da máquina: Não é necessário passar nenhum material posteriormente.
Injeção das peças: Canal de entrada de pontos, em série, canal quente, canal isolado, câmara prévia, canal de entrada nas zonas mais grossas da peça. Forma da peça: Leve em conta que não existem cantos vivos nas peças. Espessuras de parede irregulares provocam torsão. Para evitar chupado, os reforços da peça só podem ter 40 – 600/0 da espessura da parede. As inserções são possíveis, não se produzindo formação de fissuras. Peças rígidas e sem torsão são possíveis através de PP reforçado com talco.
Para evitar a fricção em peças deslizantes devemos adicionar, por exemplo, seringas .
REPRODUÇÃO PROIBIDA SEM AUTORIZAÇÃO
Hamilton Nunes da Costa – Editor de Revistas Independente
CFP VW SENAI / Matrizeiro especializado em molde
Projeto de moldes / Escola ART-MEC
Técnico mecânico CREA 126.785 / CFP VW SENAI