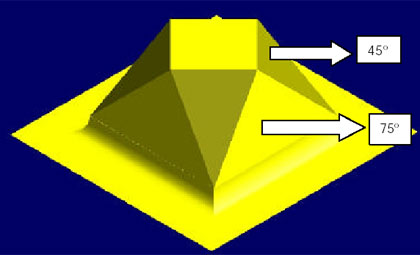

Análise do desgaste na ferramenta com a usinagem de grafita
Com a finalidade de interpretar e compreender melhor o fenômeno de desgaste sofrido pelo ferramental na usinagem de grafita foram realizados ensaios de fresamento para análise e determinação de vida da ferramenta. A definição quanto aos parâmetros de corte e ferramenta utilizada seguiu a linha do objetivo do trabalho em si, ou seja, o estudo do processo de fresamento de acabamento da grafita. Na indústria de ferramentas de injeção, a escolha pelo uso de processo de eletroerosão com eletrodos-ferramenta de grafita é determinada segundo características geométricas exigidas nos moldes e matrizes acabados, como também por conveniência e escolha na fabricação.
Algumas cavidades de dimensões reduzidas, onde não há possibilidade de corte com ferramentas de geometria definida, como por exemplo cavidades sem raio de arredondamento no fundo, rasgos com dimensões reduzidas e em locais de difícil acesso para uma ferramenta de corte, são casos onde há a necessidade do uso da eletroerosão.
Os eletrodos-ferramenta são mais exigidos quanto à sua forma e qualidade de superfície. Neste aspecto, as laterais do eletrodo desempenham papel fundamental no acabamento e qualidade final da cavidade. Por esta razão, os testes de vida de ferramenta foram realizados em condições de acabamento, para o fresamento periférico.
Foi utilizada uma ferramenta de metal-duro revestida por processo PVD com TiAlN, com diâmetro de 8 mm e 2 (dois) dentes. Os demais parâmetros de corte estão descritos juntamente com os gráficos de desempenho. Os testes tiveram por objetivo o acompanhamento da vida da ferramenta, observando o seu desempenho em direções e velocidades de corte diferentes.
Os resultados estão demonstrados em forma de gráficos de desempenho de vida de ferramenta, para as velocidades de corte utilizadas. Com velocidade de corte de 400 m/min observou-se um melhor desempenho, ou seja, rendimento de corte em torno de 20% maior para a condição em direção de corte discordante. Com o uso desta velocidade, no corte discordante há uma estabilização na evolução do desgaste, onde a ferramenta usina quase 10 m desgastando-se apenas 0,03 mm. Isto ocorre entre as marcas de desgaste de 0,06 e 0,09 mm (Figura 01). Já para o
corte concordante, com mesma velocidade de corte, este fenômeno não foi observado .
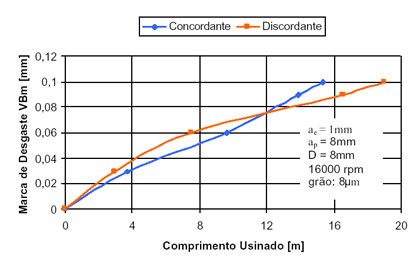
Figura 01- Evolução da marca de
desgaste de flanco, para vc = 400 m/min.
Em velocidade de corte mais baixa, 200 m/min, a marca de desgaste tem uma evolução semelhante para as diferentes direções de corte utilizadas, concordante e discordante, conforme Figura 02. Observa-se também que o corte em direção concordante tem rendimento levemente melhor que em direção discordante ao final do ensaio. Este comportamento foi também observado em testes feitos por König] e Pal et al,onde em baixas velocidades de corte a vida de ferramenta praticamente independe da direção de corte utilizada, porém à medida que as velocidades aumentam,melhora o desempenho das ferramentas para corte em direção discordante.

Figura 02- Evolução da marca de desgaste
de flanco, para vc = 200 m/min.
Em ambos os testes, para velocidades de 400 e 200 m/min, e direções de corte concordante e discordante, o comportamento de desgaste foi semelhante. A partir das fotos realizadas no microscópio óptico (Figura03), classificou-se o desgaste de flanco da ferramenta segundo a norma ISO 8688-2 .Segundo esta, o desgaste é denominado “fenômeno de deterioração uniforme do flanco”. É a região com largura constante da marca de desgaste, e estende-se por toda a porção do flanco da ferramenta, adjacente ao inteiro comprimento ativo do gume
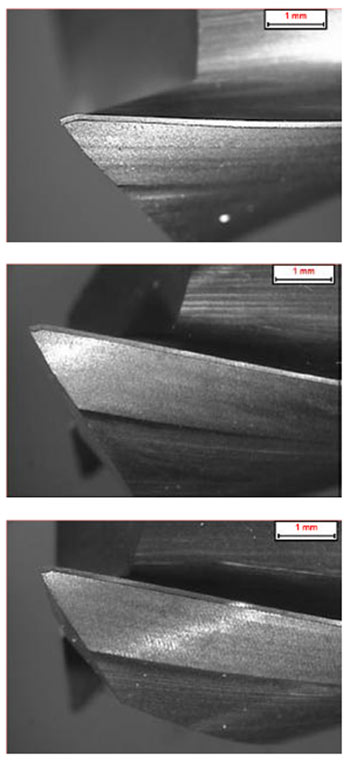
Figura 03- Desgaste de flanco uniforme para VB = 0,1 mm
Nas fotos realizadas no Microscópio Eletrônico de Varredura (Figura 4), fica evidenciado o desgaste abrasivo uniforme e constante, onde a camada de revestimento foi retirada, surgindo o substrato de metal-duro. Não se verifica nenhuma marca de achatamento do gume da ferramenta, nem de deformação plástica, lascamentos e recuo do mesmo. Pode-se também observar que o desgaste tem um comportamento uniforme em sua evolução, apresentando a mesma característica de forma tanto em meia-vida 95 como no final de vida de ferramenta. Também em toda a extensão da largura de corte, o desgaste mantém-se constante em sua evolução, não havendo marcas de desgaste máximo evidentes, como na usinagem de metais.
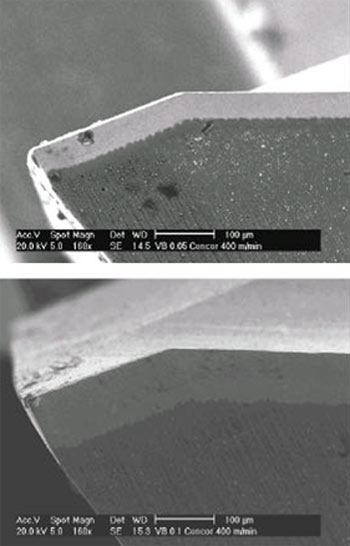
Figura 4 – Comparação entre os gumes da ferramenta
para marcas de desgaste de flanco de 0,05 mm e 0,1 mm.
Os testes ocorreram em condições secundárias idênticas, ou seja, as ferramentas (idênticas e de mesmo fabricante) tinham o mesmo comprimento em balanço (33,9 mm), fixadas em um mesmo mandril, na mesma máquina e o material da peça mantinha a mesma especificação e provinha do mesmo fabricante. Os ensaios denominados de meia-vida tiveram como critério de fim de vida uma marca de desgaste de flanco (VB) de 0,05 mm. Estes foram executados para que fosse possível averiguar melhor a evolução da marca de desgaste, através de uma análise em Microscópio Eletrônico de Varredura, após o ensaio. A partir da análise por microscópio das ferramentas, bem como citado por König ,a causa predominante de desgaste é de característica abrasiva, no flanco da ferramenta. Juntamente com a análise feita no MEV, foram realizadas amostragens químicas da parte desgastada da ferramenta e da parte ainda intacta desta (Tabela.1 e Figura 05). Na parte desgastada não são observados mecanismos de desgaste do tipo fissuras transversais e longitudinais, nem micro-quebras e deformações plásticas. Evidencia-se então a não-atuação de solicitações térmicas alternadas, nem de altas temperaturas geradas na região de corte

Tabela.1 – Análise quantitativa dos componentes existentes na parte desgastada da Ferramenta .

Figura 5- Análise qualitativa da composição química média da parte desgastada da ferramenta.
Como observado na análise quantitativa de composição química (Tabela.1), na parte desgastada da ferramenta existem somente componentes que formam o substrato da mesma, ou seja, tungstênio e cobalto, elementos que compõem o metal-duro. Com isto, pode-se supor que causas de desgaste como difusão química e adesão também não estão presentes, ou não têm conseqüências relevantes no desgaste da ferramenta de corte. Segundo König , existe um aumento no comprimento usinado a partir de uma redução do caminho de corte da ferramenta. Nos ensaios de vida realizados, esta redução no caminho de corte no material, para cada dente da ferramenta, deve-se ao aumento da velocidade de corte, pois o avanço por dente foi mantido constante em 0,05 mm. Assim, confirma-se a tendência de aumento no comprimento usinado a partir de redução do contato do gume com o material (atrito).
O aumento da velocidade de corte reduz o desgaste de face e de flanco da ferramenta, pois causa diminuição no tamanho das partículas de grafita, que tem relevante importância no mecanismo de desgaste abrasivo existente no processo, como detalhado no item sobre os mecanismos de desgaste na usinagem de grafita. Para este estudo, também foram realizados ensaios com velocidades de corte de 800 m/min, visando confirmar a influência inversamente proporcional da velocidade de corte sobre a vida da ferramenta, no corte da grafita. O avanço por dente manteve-se constante em 0,05 mm (vf = 3.200 mm/min), como nos ensaios com 400 m/min e 200 m/min.
Conforme a Figura 06, verifica-se um comprimento usinado em direção de corte discordante aproximadamente 15% maior que em direção de corte concordante, para uma marca de desgaste de flanco médio de 0,1 mm. Esta característica, de atingir-se um maior vida de ferramenta em direções de corte discordante, também ficou evidenciada no ensaio com 400 m/min. O aumento da vida de ferramenta para o fresamento em altas velocidades de corte também foi verificado por Pal el al e König .
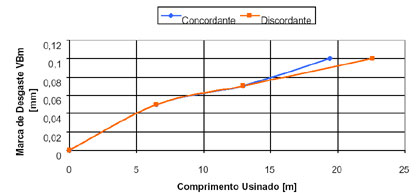
Figura 06- Evolução da marca de desgaste de flanco médio em função da direção de corte, para vc = 800 m/min
Com esta informação pode-se verificar que, ao contrário da usinagem de
materiais ferrosos, endurecidos ou não, o aumento da velocidade de corte não causa uma diminuição da vida da ferramenta. Assim, o uso da HSC na usinagem de grafita, entre todas as vantagens e benefícios existentes, também pode trazer a diminuição no custo do ferramental de corte como característica impulsionadora de desenvolvimento na área.Veja fig.07
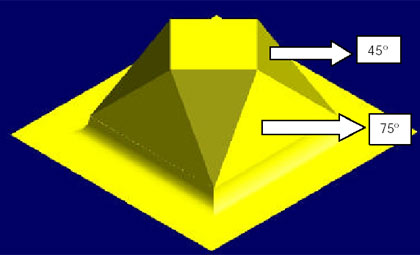
Fig.07 -Aspecto do corpo de prova com ângulos
de inclinação das superfícies.
Fonte :Dissertação Rafael Kratochvil