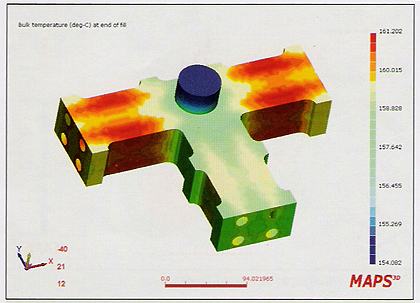
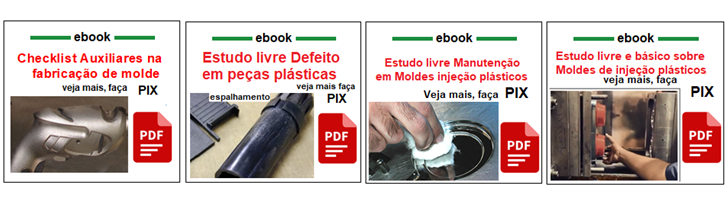
Por: Manuel Casa Branca
As diversas ferramentas de projeto e engenharia assistidas por um computador permitem extrair o máximo de rendimento das ferramentas de injeção. Um dos grandes destaques são os sistemas para a simulação do processo de injeção antes mesmo do início da construção dos ferramentais.
A moldagem por injeção é uma das operações de processamento de polímeros mais importantes da indústria plástica na atualidade. Durante anos a experiência e empirismo de projeto anteriores, a intuição e o método de tentativa e erro foram fatores chave no desenho e na otimização do processo das operações cada vez mais ineficientes quando aplicadas na injeção de peças complexas e dispendiosas, assim como no processamento de novos materiais.
Para racionalizar os tempos de criação e garantir melhor qualidade técnica dos produtos, foram desenvolvidos sistemas computacionais com o intuito de simular as operações reais e, dessa forma, reduzir os altos custos inerentes a metodologia antiga.
Ao utilizar um software eu permita fazer a simulação real a 3D, é possível testar o produto no computador e prever potenciais problemas no desenho atual antes de o molde ser fabricado.
TENDÊNCIAS DA ANÁLISE DA MOLDAGEM POR INJEÇÃO
A simulação a meio-plano ou 2,5D é o método preferido para as simulações de enchimento ou estudos reológicos, ainda que de uma forma pouco precisa. É um método que tem por base a simplificação do modelo 3D da peça, pela sua conversão em uma casca. Para tanto se procede à criação de uma meia espessura na parede da peça, assumindo-se que o escoamento no interior do molde é laminar. Até alguns anos atrás de 85 a 90% das peças injetadas eram de geometria simples o que não comprometia, por este fato, o rigor da análise.
Recentemente, a simulação 3D está ganhando terreno devido sua maior precisão, facilidade e rapidez na criação de malhas. Além disso, os avanços tanto em computadores como em programas estão fazendo da simulação 3D uma realidade cada vez mais acessível em qualidade e preço. As principais razoes por optar pela simulação 3D são:
• Ambiguidades e impossibilidade de escolher o meio plano da peça em muitas situações;
• Elevado tempo para a criação do meio-plano;
• Falha em capturar aspectos importantes de fenômenos inerentes ao processo de moldagem por injeção, como quebras de fluxo e fluxos secundários;
• Possibilidade de criar toda a malha automaticamente e;
• Desempenho dos computadores cada vez melhor com preços de aquisição em queda.
SISTEMAS CAE DISPONÍVEIS NO MERCADO
Existem no mercado vários softwares de simulação CAE. Os sistemas são compostos de módulos, que atendem as diversas demandas dos usuários finais. Na generalidade dos módulos existentes são:
Enchimento – Flow Module
Módulo para simulação do comportamento do polímero fundido durante a fase de enchimento do processo de injeção. Oferece soluções para todas as fases de desenho e fabricação, a fim de melhorar tanto a produtividade como a qualidade da peça. Potenciais problemas como enchimentos incompletos, localização indesejável da linha de soldagem (ou junta fria) e bolhas de ar são possíveis de detectar antes de o molde ser fabricado. Além disso, as variáveis de processamento tais como tempo de enchimento, temperatura de processamento e força de fechamento também podem ser otimizadas usando este módulo.
As principais informações fornecidas por este módulo são:
• Visualização da frente de fluxo do escoamento do material no interior da cavidade (Figura 1);
• Determinação da espessura adequada para a peça;
• Fornecimento da localização das linhas de soldagem;
• Previsão de bolhas de ar e enchimentos incompletos;
• Visualização das variações de fluxo;
• Determinação do número de entradas e sua respectiva localização;
• Otimização do canal de entrada (gate) e tamanho da entrada;
• Otimização do tempo de enchimento e da temperatura do fundido/molde;
• Visualização da distribuição de pressões (Figura 2);
• Facilitação do fluxo por introdução de artifícios como facilitadores ou dificultadores de fluxo por introdução de artifícios como facilitadores ou dificultadores de fluxo;
• Impedimento do enchimento em excesso ou insuficiente e;
• Previsão da força de fechamento
Figura 1 – Visualização da frente de fluxo do material
Refrigeração – Cool Module
Este módulo permite a simulação real a 3D da transferência de calor no molde durante a fase de resfriamento no processo de injeção. E essencial para dimensionamento dos canais e previsão do desempenho da refrigeração/aquecimento de forma a obter um processo rápido e uniforme em todo o molde. Deste modo, os engenheiros podem reduzir o tempo de ciclo e melhorar a qualidade da peça obtida.
Com este módulo é possível determinar o tempo de arrefecimento ideal. Além disso, potenciais problemas tais como refrigeração não balanceada, arrefecimentos desiguais e zonas demasiado quentes podem ser detectados e solucionados. As principais informações e resultados obtidos com este módulo são:
• Previsão do melhor tempo de arrefecimento e disposição/tamanho dos canais, para obtenção de processo rápido e uniforme;
Figura 2 – Visualização da distribuição de pressão
• Redução do tempo do ciclo e melhora da qualidade do produto;
• Simulação da eficiência do circuito de refrigeração, de acordo com a disposição e o tamanho dos canais (Figura 3);
• Redução das tensões residuais e térmicas através de arrefecimento uniforme;
• Melhoria da estabilidade dimensional através da redução do arrefecimento desigual e;
• Melhoria da qualidade da superfície.
Figura 3 – Distribuição da temperatura nas paredes do molde
Recalque – Pack Module
Depois da fase de preenchimento total da massa fundida do molde, é injetado ainda mais plástico na cavidade de modo a compensar a contração resultante de uma maior densidade, o que é feito desde o inicio da fase de resfriamento da peça até a sua temperatura de extração.
Este módulo simula o comportamento da solidificação do polímero e a transferência de calor durante a fase de compatação (ou recalque) do processo de injeção.
As principais informações e resultados obtidos com este módulo são:
• Previsão da contração volumétrica;
• Visualização de potenciais pontos de rebarbas e rechupes;
• Redução de empenamentos resultantes de contração volumétrica não uniforme;
• Estimativa do peso da peça;
• Previsão do tempo de resfriamento da entrada e o tempo de espera necessário;
• Seleção da máquina de injeção pela força de fechamento exercida;
• Consistência da peça devido ao controle preciso da velocidade do fuso da máquina injetora;
• Previsão da pressão, da temperatura da densidade, da contração volumétrica (figura 4) e da distribuição da razão de solidificação e;
• Otimização do tempo do ciclo.
Empenamento – Warpage Module
Durante a fase de enchimento, compactação e arrefecimento, o material passa por uma serie de processos complexos que levam a alterações no volume especifico local. Enquanto a peça está no molde, é pressionada contra as paredes deste, originando tensões durante o processo de solidificação. Na extração, a diminuição da tensão no produto causa uma contração imediata – normalmente, anisotrópica e não uniforme – por toda a peça, acarretando em nova contração durante a fase de resfriamento após a extração. Este comportamento poderá provocar empenamento da peça. As principais informações e resultados obtidos com este módulo são:
• Previsão do empenamento da peça (figura 5);
• Previsão da contração adequada para o molde;
• Determinação da espessura mais adequada da peça para redução do grau de empenamento;
• Redução do empenamento por introdução de artifícios como reforços e nervuras;
• Melhoria da estabilidade dimensional através de alteração do desenho de produto;
• Otimização da contração da peça e;
• Melhoria do processo de montagem por inserção de nervuras e encaixes.
RECURSOS ADICIONAIS EM SISTEMAS CAE
Figura 4 – Distribuição da contração volumétrica
Figura 5 – Resultado total do empenamento
Existem ainda no mercado sistemas como recursos mais avançados que permitem uma serie de outras análises e verificações para otimização do processo.
Alguns módulos adicionais que podem ser encontrados são:
Orientação das Fibras – Fiber Module
Na maioria dos materiais, é sabido que as propriedades são anisotrópicas devido à orientação das fibras ser relacionada com o processo de enchimento e ter uma estrutura de camadas idêntica à orientação das fibras.
A estrutura basicamente consiste em 3 camadas: camada superficial, camada nuclear próxima do centro e camada intermédia entre as camadas superficial e nuclear.
Na camada superficial as fibras tendem a alinhar na direção do fluxo. Por outro lado, na camada intermédia o fluxo de corte faz com que as fibras se orientem na direção perpendicular à direção de fluxo.
Figura 6 – Simulação de orientação das fibras e propriedades térmicas e mecânicas
Este módulo simula a orientação das fibras (figura 6) e as propriedades térmicas e mecânicas resultantes da compactação/enchimento para injeção com termoplásticos reforçados com fibra de vidro/carbono. A previsão da orientação das fibras é crucial em peças e projeto de moldes para a obtenção de peças bem moldadas.
Elastômeros – Rubber Module
O processo de injeção de elastômeros é definido como um processo cíclico automático em que a faixa ou forma granular dos compostos de borracha são derretidos e aquecidos a uma temperatura abaixo da temperatura de vulcanização. Então o material derretido é injetado através de um bico, canal ou ponto de entrada em um molde quente que está a uma temperatura suficiente para iniciar a vulcanização. Subconsequentemente ocorre a vulcanização da borracha na cavidade e a extração da peça moldada.
Atualmente o processo de injeção de borracha está crescendo rapidamente. Existe uma troca gradual da compressão pela injeção de produtos de borracha. Os setores automobilísticos, de máquinas, calçados e de indústrias farmacêuticas são exemplos típicos do negócio de injeção de borracha.
Este módulo simula em 3D o enchimento, transferência de calor e vulcanização de produtos de borracha durante o processo de moldagem por injeção, demonstrando vários fenômenos físicos como o padrão de escoamento da borracha, peças incompletas, linhas de soldagem, localização de saídas de ar, pressão e distribuição de temperatura, força de fechamento e grau da cura (figuras 7 e 8).
Figura 7
Figura 8
Balanceamento de Canais – Hot Runner Balancing Module
Nos últimos anos a construção de moldes com muitas cavidades e a exigência de peças com qualidade elevada vieram trazer maior ênfase ao balanceamento dos canais de injeção. Como a maioria desses moldes, incorporam sistemas de canais quentes, por vezes estes sistemas foram acusados de ser a causa direta para o enchimento desigual das cavidades.
Um sistema de canais quente mal fabricado pode causar enchimentos desiguais. É muito importante de terminar qual o sistema de canais mais apropriado logo no inicio da orçamentação do molde assim como no projeto inicial de modo a evitar custos indesejáveis mais tarde.
Os pontos ideais para injetar uma peça são calculados através do sistema de canais quentes (figura 9) pode ser alcançado com este módulo.
Figura 9
Injeção a Gás – Gás Module
Este módulo permite simular os padrões de enchimento para o processo de injeção a gás, auxiliando no desenho da peça, no posicionamento da entrada de material e na otimização das condições de moldagem, fornecendo a localização adequada para os canais de gás a fim de obter um perfeito enchimento e uma boa penetração do gás. Possibilita ainda prever as descargar súbitas e os defeitos raiados, problemas comuns neste processo de injeção.
Otimização da Entrada de Material – Gate Module
Permitindo prever a localização ideal para a entrada de material (ou as entradas), o módulo reduz a possibilidade de enchimento incompleto da cavidade, avalia as taxas e tensões de cisalhamento, facilita a simulação de várias configurações possíveis para a entrada, de forma a assegurar que a espessura da peça, a temperatura do molde e a temperatura do fundido estarão dentro dos valores aceitáveis.
CONCLUSÃO
Os diversos recursos que a tecnologia oferece para a resolução de problemas têm facilitado o desenvolvimento de produtos cada vez mais complexos.
Em função da grande variedade de soluções disponíveis, é importante definir o tipo de sistema mais adequado através da realização de avaliações criteriosas (benchmarking) e concentrar esforços no treinamento e formação de uma equipe técnica competente.
FONTE: REVISTA FERRAMENTAL