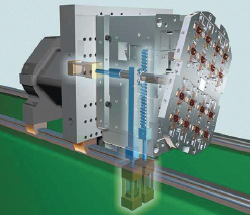
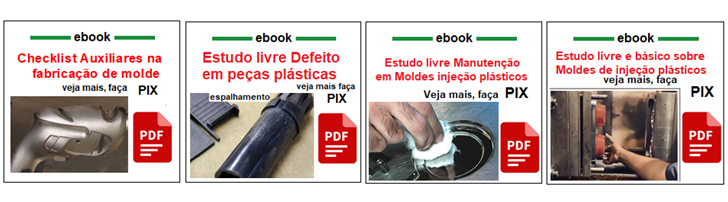
Evolução e processos de injeção multicomponentes
Considerações / Evolução
Por: PAULO DE OLIVEIRA BRASILEIRO
A evolução dos sistemas de canais quentes tem permitido a produção de peças complexas e de alto valor agregado. O projeto consistente do molde para injeção de produtos multicomponentes é a chave para o sucesso do processo.
O contínuo desenvolvimento do projeto de produtos plásticos, o aumento das exigências de mercado e da capacidade tecnológica disponível nas empresas brasileiras de projeto de produtos e de ferramentais, geraram uma atmosfera favorável ao desenvolvimento local de moldes para múltiplos materiais ou múltiplas cores.
O presente artigo tem a finalidade de introduzir particularidades dos moldes e dos processos de injeção com múltiplos materiais.
Processo já amplamente difundido na Europa e na América do Norte, não se trata de um assunto novo. A partir das técnicas de injeção sobre insertos plásticos ou metálicos, várias empresas brasileiras dos segmentos de embalagem, eletro- eletrônico, produtos de higiene pessoal e automotivo, têm aproveitado os benefícios da injeção de materiais múltiplos visando obter produtos com propriedades diferenciadas. Cabos de escovas de dente com detalhes em borracha, brinquedos, tampas com duas cores e lentes para lanternas de automóveis (Figura 3) são alguns dos exemplos mais comuns da utilização deste processo.
Muito já tem sido discutido sobre as vantagens econômicas e sobre os processos de fabricação. As empresas fabricantes de equipamento têm difundido o conhecimento tecnológico neste sentido, entretanto, ainda são poucas as ferramentarias no Brasil com experiência no projeto e na construção deste tipo de ferramenta.
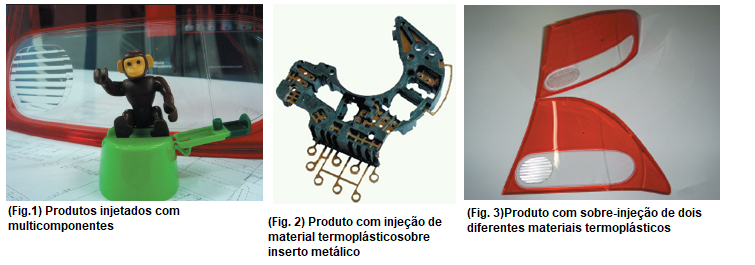
INJEÇÃO COM INSERTOS
Da necessidade de combinar propriedades, como por exemplo, a boa e má condutibilidade elétrica, se desenvolveu o processo de injeção sobre insertos, utilizado em diversos segmentos.
O mesmo princípio é empregado para obter peças plásticas de diferentes materiais ou diferentes cores.(Figura 1). A Figura 2 apresenta um componente elétrico desenvolvido com injeção de material termoplástico sobre inserto metálico. Já a Figura 3 mostra uma lanterna automotiva com sobre-injeção de materiais termoplásticos em cores diferentes.
Nos processos de injeção sobre insertos plásticos moldados previamente, a transferência da pré-forma, ou esqueleto, geralmente é manual. O sistema é quase sempre associado a pequenos lotes de produção e a um elevado índice de refugo de processo, causado por variações nas pré-formas e por diferenças dimensionais entre cavidades.
MÁQUINA INJETORA
Os equipamentos de injeção, que há alguns anos limitavam as aplicações multicomponentes, receberam um impulso tecnológico intenso na década passada. Deste modo, consultando os fabricantes mundiais de equipamentos, encontramos hoje um amplo leque de opções. Com tantas possibilidades, a escolha do equipamento adequado pode se tornar complicada.
A regra básica, porém, sempre válida é, partir da necessidade do produto, definir a matéria-prima, o processo e só então o equipamento. Isso não significa que os fornecedores de equipamentos devam ser consultados por último. O envolvimento dos especialistas em máquinas em todas as fases do processo de desenvolvimento pode afetar, de maneira positiva, o próprio projeto do produto.
Em complemento aos equipamentos normais de uma unidade de injeção, dispõe-se atualmente de modelos com duas unidades de injeção, podendo apresentar as variações de alimentação frontal (Figura 4) e frontal e lateral (Figura 5).
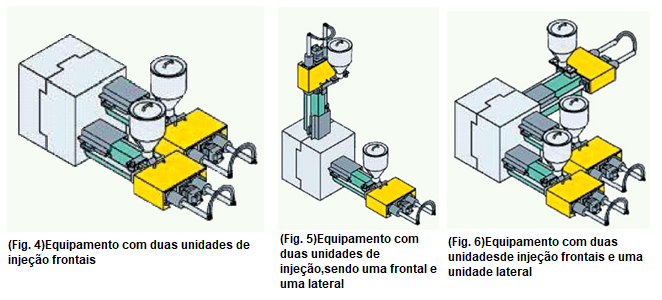
Também existem modelos com três unidades de injeção simultânea, com as variações de unidades frontais e laterais. A Figura 6 apresenta um modelo com duas unidades frontais e uma lateral.
O modelo da Figura 7 tem duas unidades frontais e uma unidade superior.
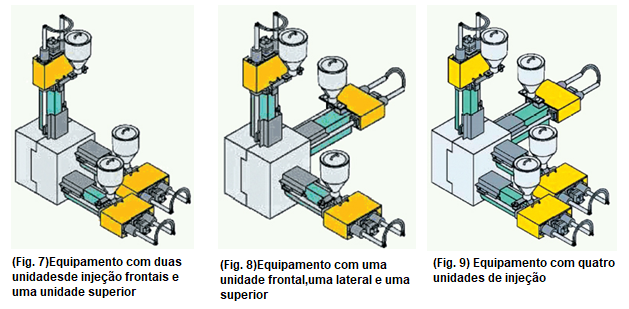
O modelo acomoda três unidades de injeção sendo uma frontal, uma lateral e uma superior.(Figura 8). É possível ainda obter outras combinações de configuração, dependendo da necessidade do processo de fabricação. A Figura 9 apresenta um equipamento com quatro unidades de injeção, caracterizando a complexidade de produto a ser produzido.
Cada unidade de injeção pode operar independentemente com materiais diferentes ou com o mesmo material e cores diferentes.
PROJETO DO MOLDE
Todos os transformadores consultados apontaram a tecnologia de projeto e construção do molde como fator preponderante para o sucesso de uma aplicação multicomponente.
Apesar de haver casos bem sucedidos de moldes construídos no Brasil, há ainda certo receio dos usuários finais quanto à qualidade e longevidade dos moldes aqui fabricados.
Além disso, nossos projetos nem sempre se equiparam em complexidade às opções que vêm da Europa e da América do Norte.
Algumas empresas internacionais do ramo automotivo projetam e fabricam moldes no Brasil valendo- se da credibilidade de suas matrizes na Europa. Em outras palavras, mesmo havendo a capacidade técnica local, ainda nos falta a tradição dos grandes fabricantes que já aplicam a tecnologia há vários anos.
Podemos aproveitar muito da experiência que nossos transformadores adquiriram utilizando e mantendo estes moldes importados, combinando esta experiência com nossa criatividade na busca de soluções que se adaptem perfeitamente aos nossos volumes de produção e às exigências do mercado.
Os conceitos de projeto para injeção de multicomponente são:
• Transferência manual
Normalmente a peça base (pré- forma) é injetada em um equipamento e transferida para outro manualmente, alojando-se na cavidade que será sobre- injetada. Algumas lentes automotivas são produzidas dessa forma.
Este processo é comumente aplicado também na sobre- injeção de insertos. O inserto é colocado manualmente no molde que, após fechado, recebe o material plástico sobre injetado.
• Transferência linear com robô
A transferência por robô se assemelha à transferência manual. Sendo a pré- forma e a sobre- injeção moldadas simultaneamente no mesmo molde, ocorre a automatização e uniformização do ciclo de moldagem, melhorando a qualidade do produto. Comparada com a transferência manual, permite maior complexidade ao processo e depende fortemente da geometria da peça. A pré-forma deve permitir a remoção por robô, se ajustar com facilidade à nova cavidade e possuir algum tipo de fixação que permita a permanência da peça em posição durante o movimento da máquina de fechamento horizontal.
A Figura 10 mostra o esquema de funcionamento deste conceito de molde.
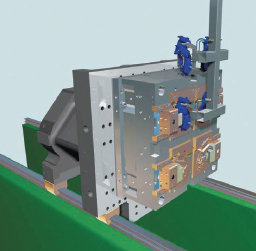
(Figura 10)Transferência linear com robô
• Transferência linear no molde
Moldes de transferência linear são bastante difundidos na indústria de higiene pessoal. O conceito de construção é relativamente simples, entretanto, sua fabricação requer dimensões extremamente precisas.
Este processo não exige recursos sofisticados da máquina injetora, sendo operado apenas com os recursos convencionais inerentes às unidades de injeção adicionais.
A transferência das pré-formas é feita por um mecanismo construído no molde. É comum haver também um mecanismo de retenção para garantir que as peças não caiam durante o fechamento da máquina.
Moldes deste tipo não são absolutamente simples de projetar ou de construir, porém garantem excelentes resultados para peças de produções mais elevadas.
No Brasil temos casos de moldes deste tipo para 16+16 e 24+24 cavidades.
A aplicação é também dependente da geometria da peça que pode ser sobre- injetada em ambos os lados.
O mecanismo de transferência deixa uma marca no produto que, em condições ideais de ajuste é imperceptível.
O molde da Figura 11 é construído com 16+16 cavidades para injeção de escova de dente.
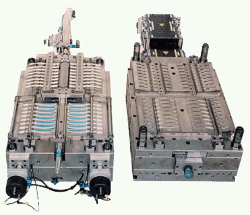
(Figura 11)Transferência linear no molde
• Molde com placa indexadora
Nestes moldes a transferência das pré-formas para a cavidade seguinte é feita pela rotação de uma placa instalada no molde. Durante a transferência, as peças permanecem alojadas no macho ou na cavidade, dependendo do produto.
Nos dois casos o sistema permite a injeção em ambos os lados da peça. Produtos de parede fina podem ser transferidos sobre o macho para evitar distorções quando da injeção do segundo e do terceiro material.
O tamanho e peso da peça são limitados pela capacidade de carga da placa indexadora.
O esquema da Figura 12 é de uma placa indexadora no molde
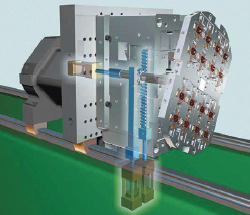
(Figura 12)Molde com placa indexadora
• Molde com macho retrátil (core back)
Neste caso não há transferência da peça e sim o movimento de um componente do molde. O molde é menos complexo e a máquina injetora menor, posto que a mesma cavidade injeta tanto a pré-forma quanto a sobre injeção.
Devido o sistema de injeção ser seqüencial, os ciclos se tornam mais longos.
O processo é extremamente dependente da geometria do produto sendo especialmente indicado para pré-formas que não podem ser removidas da cavidade para a injeção do novo componente.
Um exemplo típico são as tampas onde a primeira parte injetada requer extração forçada.
A Figura 13 apresenta um detalhe de funcionamento do macho retrátil e a Figura 14 o esquema da parte móvel de um molde com macho retrátil.
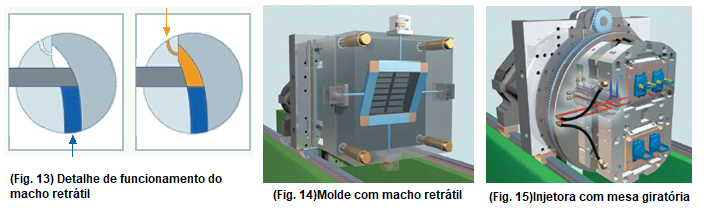
• Máquina com mesa giratória
Este sistema utiliza máquina injetora equipada com mesa giratória na placa móvel. A mesa possui as conexões elétricas, pneumáticas e hidráulicas requeridas para o acionamento do molde, o que simplifica muito o projeto da ferramenta quando comparado aos demais sistemas de transferência.
É o método empregado na fabricação de lentes automotivas, especialmente para veículos com maior volume de produção.
Um esquema de máquina injetora com mesa giratória é apresentado na Figura 15.
COMPATIBILIDADE ENTRE MATERIAIS
Além da geometria das peças, da qualidade do molde e dos cuidados no processo, a escolha da matéria prima é de fundamental importância quando se deseja a adesão entre os componentes.
Por outro lado, podemos escolher materiais incompatíveis para obter peças articuladas.
Um exemplo, demonstrado na Figura 16, é um boneco injetado com POM (cabeça) e PA (corpo). Possibilidade esta já empregada em vários componentes automotivos, formando uniões articuladas que não podem ser desmontadas.
A Tabela 1 identifica a compatibilidade entre os diversos materiais termoplásticos e elastômeros comerciais.

(Figura 16)Exemplo de injeção com materiais incompatíveis
SISTEMA DE INJEÇÃO
Apesar do avanço na tecnologia de câmaras quentes, que presenciamos nos últimos anos com a chegada ao Brasil de grandes fornecedores internacionais, ainda existem limitações tecnológicas quando se trata de injeção multicomponente.
O projeto do molde continua apresentando desafios quanto à configuração (layout) das cavidades, à linha de fechamento, à separação dos múltiplos materiais e ao mecanismo de transferência.
Cabe ao fornecedor de câmara quente oferecer soluções que se adaptem a essas necessidades sem agregar outras limitações ao projeto.
Um projeto de distribuidor (manifold) bi-partido permite obter flexibilidade no desenho do molde sem abrir mão do balanceamento de fluxo.
A capacidade de operar com 2, 3, 4 ou mais materiais em um mesmo manifold também simplifica o projeto do molde multicomponente, além de oferecer opções de design de produto sem agregar operações adicionais.
Barras de injeção (sprue bars) valvuladas para moldes de dois níveis (stack molds) garantem a operação sem perdas de resina e eliminam o obstáculo causado pelas barras de injeção convencionais.
A Figura 17 mostra o esquema de um sistema de câmara quente para injeção multicomponente.
Com isso, o projetista do molde tem a liberdade de empregar, por exemplo, um mecanismo de transferência linear que passe pelo centro de injeção.
Controles precisos de bicos valvulados para processamento de elastômeros, padronização e longevidade dos componentes são essenciais quando se trata da injeção de produtos diferenciados.
As particularidades, descritas acima, devem ser consideradas pelo projetista do molde quando da escolha do parceiro para o desenvolvimento de câmaras quentes multicomponentes.
Tabela 1- Compatibilidade de materiais
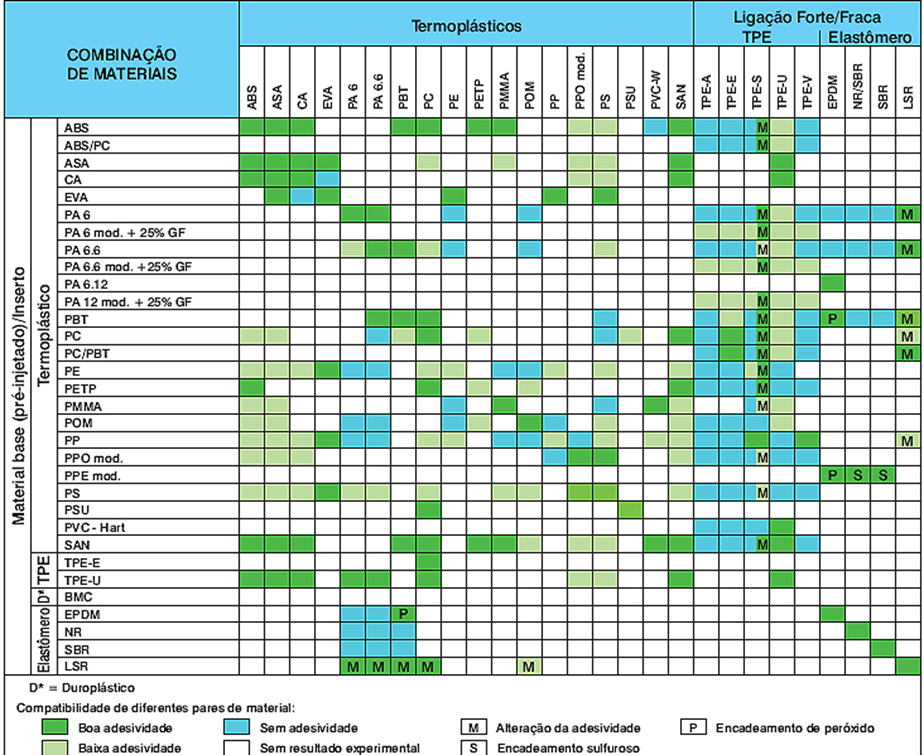
(Figura 17)Exemplo de câmara quente para injeção de multicomponente
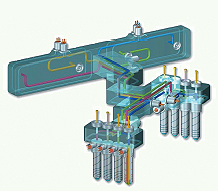
LIMITAÇÕES DO PROCESSO
São comuns hoje, moldes produzindo escovas de dente ou lentes automotivas com até quatro materiais ou cores utilizando máquinas com quatro unidades de injeção.
Uma máquina injetora hipotética poderia oferecer outras quatro unidades de injeção sem maiores dificuldades, entretanto a complexidade do molde certamente seria a restrição mais importante para um número maior de componentes.
Quanto às limitações no projeto do produto, há que se considerar seriamente a geometria da peça, o material e o processo de fabricação já no desenvolvimento do produto.
FONTES DE CONSULTA
Empresas colaboradoras do artigo: Belga Indústria de Matrizes, Elite Indústria de Matrizes, Indústria de Plásticos Cária, Johnson & Johnson, Jplast Indústria de Moldes, Plastek do Brasil Indústria e Comércio, Seaquist Closures Embalagens, TechTools Ferramentaria, Valeo Iluminação e Visteon do Brasil.
Foram consultados os sites das empresas: Arburg GmbH, Battenfeld do Brasil, Engel Áustria GmbH, Foboha Formenbau, Krauss Maffei do Brasil, Machines Boucherie NV, Mold Masters do Brasil e Zahoransky Formenbau GmBh.
Fonte: Revista Ferramental