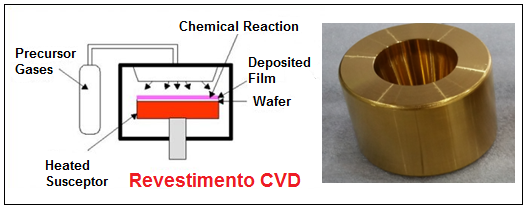
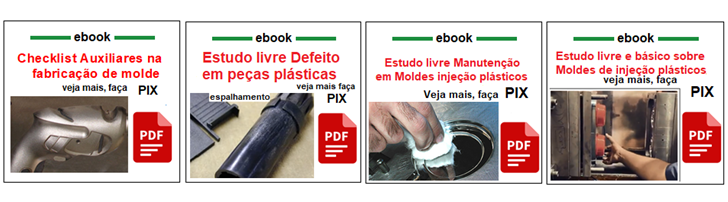
REVESTIMENTOS CVD (Chemical Vapor Deposition) E PVD (Physical Vapor Deposition)
A vida de uma matriz é determinada principalmente por sua resistência aos processos de desgaste no qual podem ser de diferentes naturezas dependendo de sua aplicação. Matrizes para trabalho a quente sofre desgaste abrasivo e fadiga térmica. Matriz de estampagem e de forjamento a frio deverá resistir ao desgaste abrasivo e alta tensão. Desta forma, o material é geralmente tratado termicamente. Eventualmente em adição a este tratamento, a nitretação, os revestimentos por PVD e CVD são exemplos de tratamento superficial que protegem a superfície da matriz e prolonga sua vida. O tratamento térmico usual é realizado antes do semi-acabamento, acabamento, ou polimento. O fabricante de matriz tenta evitar a usinagem de desbaste em materiais endurecidos embora isto possa economizar tempo .
Tratamento Térmico determina dureza final
Os aços ferramenta possuem ampla aplicação no setor metal-mecânico em operações relacionadas ao corte, conformação e injeção de metais e polímeros. As solicitações a que são submetidas as ferramentas nestes diversos processos são extremamente complexas e exigem dos materiais uma otimização de propriedades, principalmente relacionada à resistência mecânica, tenacidade e resistência ao desgaste. A resistência mecânica e tenacidade estão relacionadas primeiramente ao processo de tratamento térmico de têmpera e revenimento, que confere a dureza final ao material e controla a microestrutura. Entretanto, a otimização das propriedades tribológicas, na superfície de contato, pode ser substancialmente elevada pelo uso de diferentes tratamentos superficiais.
No uso de tratamentos superficiais, o aumento no desempenho de ferramentas tem sido buscado pelo uso da nitretação ou de revestimentos tribológicos . Atualmente, a nitretação sob plasma pulsado já encontra aplicação industrial no Brasil para o tratamento de diversos tipos de aços ferramenta. Os revestimentos tribológicos, principalmente o TiN, também é utilizado industrialmente desde meados da década de 80, do século 20, por fabricantes de ferramenta e prestadores de serviço.
Uma combinação ótima entre estes tratamentos superficiais vem sendo buscada principalmente por universidades e institutos de pesquisa. O tratamento dúplex, consiste na nitretação sob plasma seguida de
revestimento por TiN. O revestimento de materiais pré-nitretados pode ser realizado no mesmo reator utilizado para a nitretação, denominado processo híbrido ou em reatores diferentes, denominado processo dúplex. A combinação do tratamento termoquímico de nitretação com a deposição de TiN-PVD permite obter camadas com diferentes propriedades, gerando uma superfície onde o material apresenta uma combinação funcional de ambas para uma otimização de desempenho .
Várias pesquisas sobre o uso de revestimentos em aços nitretados têm demonstrado o potencial do processo dúplex .Com a nitretação sob plasma prévia, o aumento na dureza do substrato se traduz por uma elevação na capacidade de suportar carregamento do sistema, melhorando a resistência ao desgaste de superfícies dúplex .
A camada nitretada influi na resistência ao desagaste
A resistência ao desgaste do aço ferramenta AISI H13 é otimizada após tratamento superficial de revestimento PVD-TiN. A superfície dúplex, “TiN/Nitretação sob Plasma”, possuem maior resistência ao desgaste microabrasivo quando comparada com o aço na condição sem tratamento superficial, apenas temperado e revenido, ou revestido com TiN sem a pré-nitretação.
O estudo dos coeficientes de desgaste mostraram que a resistência ao desgaste das superfícies dúplex é otimizada fundamentalmente pela presença da camada nitretada sob plasma. A maior resistência ao desgaste das superfícies dúplex depende não só da dureza máxima atingida na camada nitretada, mas também de sua profundidade. Camadas nitretadas sob plasma mais profundas possuem maior resistência ao desgaste microabrasivo, por um aumento na sua capacidade de suportar carregamento. Portanto, o aumento no tempo de nitretação é necessário para aprofundar a camada nitretada e, conseqüentemente, aumentar a resistência ao desgaste microabrasivo nas superfícies dúplex
Processos de deposição em constante estudos para evolução
A deposição de filmes cerâmicos sobre aços ferramentas é uma prática muito comum em tratamentos superfíciais. Estas camadas podem ser produzidas por diferentes processos, que se dividem basicamente em dois grandes grupos:
processos químicos a vapor (CVD) ou processos físicos a vapor (PVD), podendo ambos ainda ser assistidos por plasma. Cada processo tem suas caracteristicas, vantagens e desvantagens que dependem principalmente da aplicação final do filmes. Um grande esforço de muitos grupos de pesquisas da área de ciência e engenharia de superfície tem sido melhorar e controlar a adência entre a camada depositada e o substrato. Muitos resultados satisfatórios têm sido alcançados nos últimos anos, tais como a deposição, por exemplo, de uma camada intermediária de Ti entre o substrato e a camada de TiN .
O tratamento duplex de nitretação iônica seguida por um tratamento PVD também tem sido utilizado e mostra-se como um processo com um futuro promissor .Estudos mostram que o tratamento duplex quando feito em reator híbrido melhora a aderência entre o aço ferramenta nitretado e a camada de TiN, devido ao aumento da capacidade do substrato de suportar carregamento. Em pesquisas, diferentes filmes com propriedades mecânicas, microestruturas e composição química diferentes foram depositados sobre o aço ferramenta AISI H13 sem tratamento de nitretação. O processo híbrido foi utilizado para a obtenção da camada nitretada e do revestimento. A aderência entre filme e substrato foi avaliada em termos da razão entre a dureza e o modulo de elásticidade (H/E). Os resultados mostram que quando a razão H/E do filme e do substrato se aproximam ocorre uma significativa melhora da aderência do conjunto.
O tratamento superficial aplicado antes do processo de PVD.
O tratamento superficial aplicado antes do processo de PVD tem grande importância para a retirada da camada de sujeira e partículas metálicas depositadas na ferramenta. Antes do processo a ferramenta/molde deve estar isenta de qualquer sujidade e partículas, a limpeza por ultra-som hoje é o método mais eficiente para limpeza de peças, conhecida como limpeza de precisão é capaz de chegar em locais de difícil acesso e tem capacidade de remover 100% da sujeira a partículas metálicas preparando a superfície para receber a cobertura.O tratamento de superfície está à nossa volta, bastando olhar para o lado para identificarmos objetos que necessitam dele, tais como utensílios domésticos, objetos de uso diário no escritório (clipes, tesouras e grampos), na arquitetura e construção, nos veículos de todas as espécies e na vida social (adornos, jóias e bijuterias), tornando nossa vida mais agradável em muitos sentidos.O setor de tratamentos de superfície é muito vasto e tem papel fundamental na prevenção da corrosão e na manutenção, fatores esses cruciais na preservação ambiental, aumentando a durabilidade e a vida útil dos materiais.
A tecnologia de limpeza por ultra-som fornece a qualidade necessária de limpeza que exige uma superfície onde é aplicado um revestimento de PVD, abaixo explanamos um pouco mais sobre a tecnologia. O ultra-som fornece elevada energia mecânica mediante a geração de ondas sonoras de alta freqüência através de um dispositivo, constituído essencialmente de um gerador de corrente elétrica à alta freqüência e de um ou mais transdutores que convertem esta energia elétrica em energia mecânica por meio de ondas acústicas. A capacidade percentual de conversão desta energia elétrica em energia mecânica mais ou menos elevada é o que dá sua eficiência.São utilizadas ondas ultra-sônicas justamente porque sua elevada freqüência provoca um efeito físico chamado cavitação de particular interesse e aplicação nos processos de limpeza superficial.
PVD – Deposição física de vapor
PVD (Physical Vapor Deposition): vaporiza o material sólido por calor e recondensa o vapor sobre a superfície do substrato para formar o filme fino sólido.
PVD, em inglês, é o termo que designa o processo de Physical Vapour Deposition. No português poderíamos traduzir para deposição física de vapor. Trata-se de um processo descoberto acidentalmente por Michael Faraday (22/09/1791-25/08/1867), que observou a deposição de partículas na superfície interna de bulbos de lâmpadas incandescentes oriundas da explosão do filamento.
Você já notou que em uma lâmpada queimada o vidro fica escurecido no interior? A partir disso pesquisadores desenvolveram um processo de deposição em vácuo onde, primeiramente, um material é transformado em vapor, então é transportado nessa fase e por último é depositado na superfície de um substrato. Este processo permite depositar uma infinidade de metais puros e ligas (como ouro, cromo, etc.) bem como uma série de nitretos e outros compostos. Com o avanço da pesquisa, foi desenvolvido o chamado “íon plating”, técnica inicialmente utilizada na Europa, introduzindo diversos benefícios ao processo de PVD: melhor adesão, controle da estrutura do filme, deposição em temperaturas baixas, assim como deposição de ligas, multicamadas, nanocamadas e camadas com gradiente de composição.
A técnica consiste basicamente na aplicação de uma voltagem negativa nos substratos. A forma através da qual o material é transformado para a fase vapor é o principal ponto de distinção dos processos. Os processos de PVD (Evaporação por feixe de elétrons, arco catódico e “magnetron sputtering”) podem ser oferecidos em duas diferentes temperaturas, selecionados de acordo com o tipo de material a ser revestido.
O processo padrão é realizado a 500ºC, enquanto o chamado processo de “baixa temperatura” realiza-se em torno de 200ºC.
Uma seqüência normal de processo consiste primeiramente na preparação do produto fora da câmara de deposição inciando com um sofisticado equipamento de limpeza por ultra-som, seguido da montagem do produto nos dispositivos e carregamento na câmara, já com o produto no interior da câmara de deposição, esta é evacuada, as peças são aquecidas, ocorre uma limpeza por bombeamento com gases inertes, uma limpeza com íons metálicos e por fim o revestimento.
No diagrama abaixo é possível identificar as etapas do processo de PVD.
O processo paar PVD Ocorre dentro de uma câmara sob vácuo, onde o material a ser depositado é inicialmente vaporizado e ionizado formando um plasma. Por diferença de potencial, os íons, de forma pura ou combinados com átomos de nitrogênio e/ou carbono, são atraídos para a superfície das peças a serem revestidas.
Existem três tecnologias básicas para a vaporização do elemento principal da camada, que se encontra no estado sólido na forma de um catodo: arco elétrico, desintegração por bombardeamento com átomos de argônio (sputtering), ou por feixe de elétrons.
Neste processo, para o revestimento ocorrer de forma adequada em termos de espessura, estrutura atômica e aderência, é importante que as superfícies úteis das peças a serem revestidas estejam “na linha de visão” do catodo. Isto torna importante a montagem de carga e a criação de dispositivos específicos que garantam a exposição correta das peças.
“Existem três tecnologias básicas para a vaporização do elemento principal da camada, que se encontra no estado sólido na forma de um catodo: arco elétrico, desintegração por bombardeamento com átomos de argônio (sputtering), ou por feixe de elétrons”
O PVD geralmente ocorre a temperaturas entre 180 e 500°C, o que faz com que uma grande gama de ligas metálicas possa ser revestida sem afetar suas propriedades estruturais, notadamente a dureza obtida em um tratamento térmico anterior.
Exemplos de camadas típicas obtidas pelo processo PVD: TiN, CrN, AlTiN, AlCrN, TiBN, TiCN.
Algumas das principais características destas camadas são: elevada dureza, que pode ir de 1800 a 3500HV, a temperatura de utilização que vai de 400 a 900°C, além de propriedades antiaderentes.
As camadas PVD podem fazer ferramentas durar até 10x mais quando comparado à vida de uma ferramenta apenas com tratamento térmico, além de permitir a utilização de ferramentas em condições de maior produtividade.
CVD – Deposição de vapor químico
CVD (Chemical Vapor Deposition): usa gases ou precursores em estado vapor e o filme depositado a partir de reações
químicas sobre superfície do substrato.
Também ocorre dentro de uma câmara sob vácuo, neste processo, o elemento a ser depositado vem da decomposição de um gás a partir de uma reação química. O material da camada condensa na superfície das peças que são revestidas.
Comparativamente ao PVD, o processo CVD não tem a limitação da “linha de visão” das peças com relação à fonte das material a ser revestido, o que torna a montagem de cargas bem mais simples. Neste caso, basta que se consiga um fluxo laminar e uniforme dos gases gerados por toda a carga.
Já em termos de temperatura, o processo ocorre normalmente entre 600 e 1000°C, o que limita significativamente os tipos de materiais que podem ser revestidos. Tipicamente os substratos são de metal duro.
Exemplos de camadas obtidas pelo processo CVD: TiN, TiC, TiCN, TiBN, Al2O3.
As características destas camadas são similares às das camadas PVD, mas o CVD proporciona em alguns casos uma temperatura de trabalho superior, podendo chegar a 1200°C. Os benefícios do revestimento CVD aplicado sobre ferramentas são semelhantes aos conseguidos com o PVD.
Processo combinado PVD / PACVD
Os processos PVD e CVD podem ser combinados de forma sequencial em uma mesma câmara. Nesta configuração, o processo CVD é modificado para ocorrer a temperaturas entre 180 e 350°C. Para que isto seja possível, a decomposição dos gases que geram a camada a ser depositada é ativada por plasma, daí o nome PACVD, Plasma Activated CVD.
Com a técnica do PACVD, uma importante família de revestimentos pode ser produzida, que é a das camadas DLC (Diamond Like Carbon). Estas camadas, geralmente depositadas sobre um filme prévio de PVD, são à base de carbono e combinam características de deslizamento do grafite e resistência a riscamento do diamante.
Assim sendo, as principais características das camadas DLC são: baixos coeficientes de atrito, abaixo de 0,20, e altas durezas, que podem ir até 3000HV e em condições especiais a valores ainda maiores.
As vantagens principais destas camadas estão na minimização de por atrito, maximização de resistência a desgaste e aumento de confiabilidade de componentes mecânicos de precisão.
Fontes :
Influência da Razão Entre a Dureza e o Módulo de Elasticidade (H/E) na Aderência de Revestimentos de TIN e TIC depositados sobre Aço AISI H13
A.C. Recco, A. P. Tschiptschin, I. C. Oliveira M. Massi, H. S. Maciel.
Influência do Tratamento de Nitretação sob Plasma no
Desempenho de Superfícies Dúplex Revestidas com TiN .
Adonias Ribeiro Franco Junior; Carlos Eduardo Pinedo ; André Paulo T.
Revista Industrial Heating junho 2016- Paulo Vencovsky
REVISTA FERRAMENTAL .—Enge Solutions
Imagens peças: www.ticoating.com
REPRODUÇÃO PROIBIDA SEM AUTORIZAÇÃO
Hamilton Nunes da Costa – Editor de Revistas Independente
CFP VW SENAI / Matrizeiro especializado em molde
Escola ART-MEC / Projeto de molde
CFP VW SENAI / Técnico mecânico – CREA 126.785