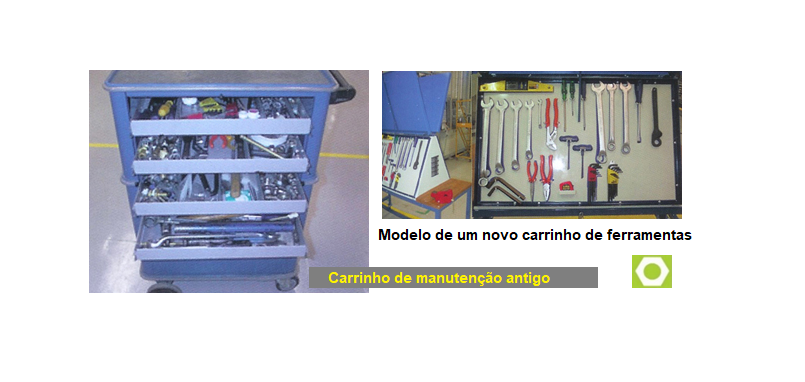
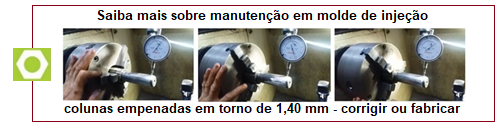
Troca rápida de moldes: Aumento de eficácia através da melhoria da etapa de preparação de máquina
Por: Gilsilei Bertoloti
A racionalização no uso dos termos é fundamental para eficácia do processo produtivo. Um dos fatores da baixa competitividade do setor de transformação de plásticos é o tempo excessivo despendido na preparação da injetora e na troca de moldes. Organizar esta etapa é garantia de melhoria do processo e, conseqüentemente, de retorno do investimento.
A troca rápida de ferramenta (TRF) tem por objetivo reduzir o tempo de setup, ou seja, o tempo em que a máquina fica parada para a troca de um ferramental. A TRF também é conhecida como SMED (Single Minute Exchange Of Die – Troca de ferramenta em um minuto).
A TRF é uma metodologia que auxilia na mudança rápida de uma linha de produção possibilitando, conseqüentemente, respostas rápidas diante das necessidades do mercado. Apresenta grande vantagem quando aplicada na produção de lotes pequenos de fabricação, pois permite reduzir os estoques intermediários e custos de inventários.
É importante lembrar que, apesar do estudo de caso estar voltado para a troca de um molde de injeção de termoplásticos, a TRF pode ser utilizada para qualquer processo, sendo originária da troca de um ferramental para estampagem de metais.
Em suma, a metodologia foca na redução dos custos totais de fabricação, diminuindo de maneira considerável os tempos improdutivos, que não agregam valor ao produto final.
Grande parte das empresas brasileiras não mensura esse tempo, desprezando-o na cotação do processo produtivo. As empresas trabalham com um tempo disponível de máquina que não é verdadeiro. O resultado é refletido na quantidade de horas extras adicionais necessárias para compensar a ineficiência das trocas de ferramental.
A redução do tempo de setup é condição necessária para diminuir o custo unitário de preparação. Tal redução é importante por três motivos:
1 . Quando o custo de setup é alto, os lotes de fabricação tendem a ser grandes, aumentando o investimento em estoques;
2. As técnicas mais rápidas e simples de troca de ferramentas diminuem a possibilidade de erros na regulagem dos equipamentos e;
3. A redução do tempo de setup resultará em aumento do tempo de operação do equipamento .
Definição de Setup
Aquelas tarefas necessárias e relativas às atividades de preparação de um equipamento, desde o momento em que se tenha completado a última peça boa do lote anterior até o momento em que se tenha feito a primeira peça boa do lote posterior.
Define-se dessa forma, como tempo total de setup o período transcorrido desde a produção da última peça boa do lote anterior até a produção da primeira peça boa do lote posterior.
METODOLOGIA SMED
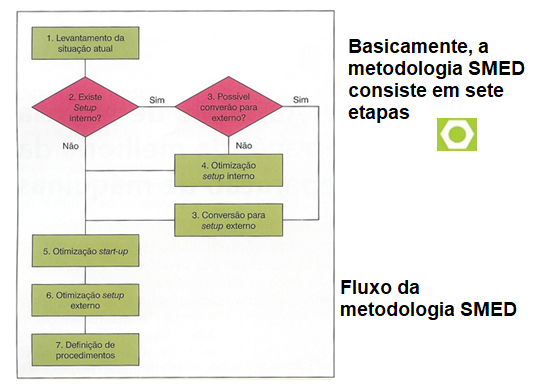
1- Caracterização da situação atual: Observar o processo atual da comutação, fazer um vídeo da troca, estudar os tempos, entrevistar os operadores;
2 – Identificação de setup interno e externo: São separados as atividades executadas com a máquina parada (interna ou setup interno) das atividades executadas longe da máquina com a mesma em funcionamento (externas ou setup externo). Deve ser preparada uma lista de verificação para o setup externo (check -list);
3 – Migração para setup externo: Etapa de transformação de atividades internas para externas;
4 – Otimização de setup interno: Aumentar a eficiência das atividades internas restantes;
5 – Otimização de início de operação: Aperfeiçoar o processo de colocação da máquina em operação com o intuito de reduzir o tempo de início de produção (start-up);
6 – Otimização de setup externo: Aumentar a eficiência das atividades externas e;
7 – Definição de procedimentos: Formalizar a seqüência de ações que devem ser adotadas para a redução dos tempos de setup.
ESTUDO DE CASO
O exemplo a seguir é resultado de uma consultoria realizada em empresa de injeção de plásticos do interior de São Paulo. A empresa produz peças plásticas para a linha branca, linha automobilística e embalagens para cosméticos.
A adoção da metodologia SMED contemplou as sete etapas descritas anteriormente.
Levantamento da situação atual
A fim de investigar os tempos de preparação foi realizado o vídeo de uma troca de molde de injeção para o caso determinado, conforme demonstrado na Tabela abaixo:
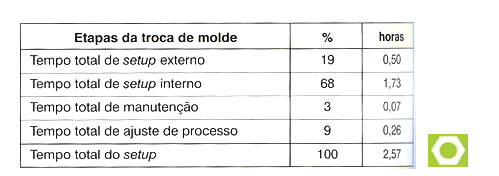
Identificação de setup interno e externo
Em sala de aula o vídeo foi apresentado para as equipes de trocadores de moldes, supervisores e preparadores de matéria-prima. Foram identificados os tempos da troca e separados em atividades internas (interno) e externas (setup externo).
Convém salientar que nesta troca foram verificados “, problemas de manutenção relativos a mau funciona. mento do mouse’ do painel de comando da máquina.A, máquina foi desligada e ligada para que o dispositivo, pudesse entrar em funcionamento.
Migração para setup externo
Nesta etapa foram identificadas as atividades internas que poderiam ser realizadas com a máquina ainda em funcionamento. A Figura 2 mostra a análise da troca. Nela estão contidos apenas os itens que não deveriam ser realizados com a máquina parada, exceto retirada e colocação de mangueiras.
A etapa de retirada dos conectores de água na parte inferior do molde representou algo em torno de 9,5% do setup interno. Este tempo poderia ser evitado se o molde possuísse pés.
A operação de colocação das mangueiras de refrigeração representou 11,7% do setup interno. Um dos motivos para este tempo elevado foi a falta de identificação nas entradas e saídas dos canais de refrigeração e a falta de um esquema de montagem das mangueiras.
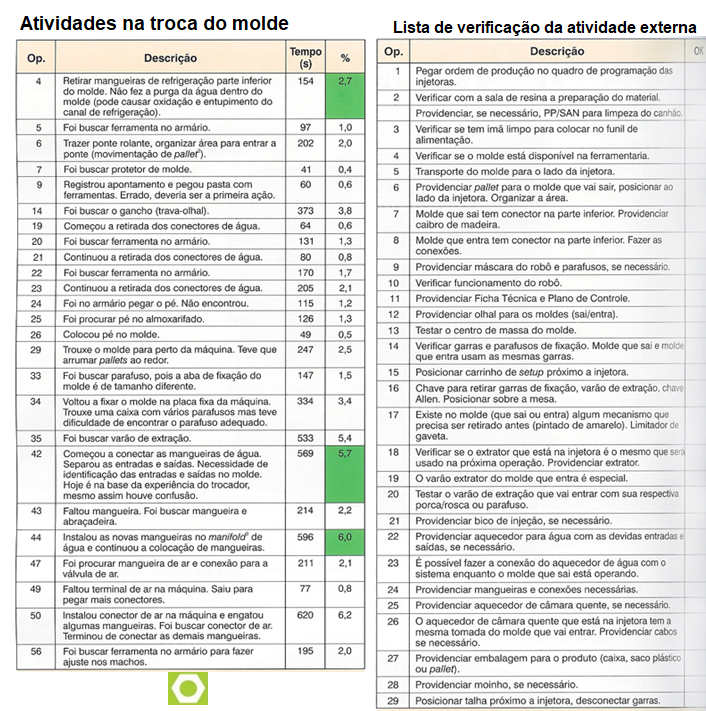
Muitos gerentes podem olhar para este cenário (14,4% do tempo gasto com retirada e colocação de mangueira) e acreditar que devem partir para a compra de um sistema de engate rápido. Isto não é necessariamente correto. Uma das idéias do SMED é reduzir a troca de molde sem fazer investimentos, ou no máximo fazer um investimento pequeno. Somente após todas as etapas serem otimizadas é que se deve pensar em investimentos.
Como forma de evitar que atividades externas (setup externo) sejam realizadas como atividades internas (setup interno) foi elaborada uma lista de verificação (check-list) de setup externo, como mostra parcialmente a Figura. Todos os itens devem ser verificados antes de se iniciar uma troca de molde. A lista completa tem mais de 40 itens de verificação.
A recomendação dada aos trocadores de moldes foi para que somente iniciassem a troca de um molde se todos os itens do check-list tivessem sido verificados.:1 Um dos pontos mais importantes deste check-list se refere à matéria-prima. Em empresas que utilizam matéria-prima que precisa ser estufada por 4 horas ou até mesmo 6 horas, é comum terminar a troca do molde e verificar que ainda não há matéria-prima disponível ( estufada).
Otimização do setup interno
Aumentar a eficiência das atividades internas restantes é um dos passos mais importantes para a meIhoria do resultado da eficácia do processo. Serão mostrados aqui exemplos de como melhorar o tempo da atividade interna.
Exemplo 1 – Padronização de bicos de injeção
Nesta empresa existiam vários tipos de bico de injeção. Alguns em raio com várias dimensões diferentes, outros com chanfros em ângulos variados.
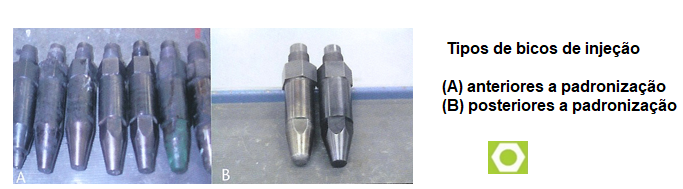
Foram padronizadas todas as buchas e bicos de injeção para apenas dois modelos. O trocador de molde passou a ter em seu carrinho de ferramentas os dois tipos de bico. Além disso, foi acrescida no check-/ist de setup interno a verificação do tipo de bucha do molde que iria ser colocado em máquina e a disponibilidade do bico no carrinho.
Exemplo 2 – Padronização de refrigeração
Foram eliminadas, para alguns moldes, várias entradas e saídas de água e substituídas por um distribuidor único (manifold). Este manifo/d foi confeccionado na fermentaria da empresa. É um sistema simples, barato e eficiente. Consiste em um tubo de alumínio que distribui a água para as entradas do molde. No outro lado, outro tubo coleta a água de saída. Ao invés do trocador ter que conectar várias entradas e saídas no molde, ele conecta um menor número de mangueiras. Em alguns casos apenas uma entrada e uma saída por lado do molde. A Figura 5 mostra o exemplo desta ação.
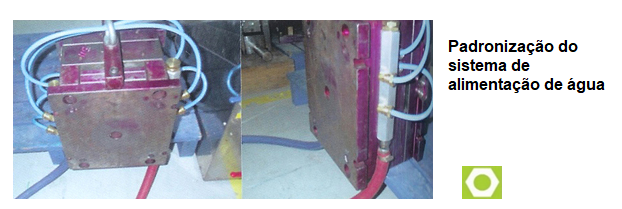
Há uma prática comum na utilização de moldes que é a colocação de pontes entre as várias entradas e saída
De água. Uma boa solução é deixar estas pontes fixas no molde evitando perda de tempo com a colocação das mesmas durante o setup interno. A figura 6 mostra um exemplo desta prática juntamente com a adição de Um! manifold de distribuição de água. É uma solução interna sem os investimentos em sistemas de conexão rápida.
Otimização do início de operação
Melhorar o tempo início de operação (start-up) ou início de produção consiste em diminuir os tempos de ajuste de processo, o que significa minimizar ou eliminá-los.
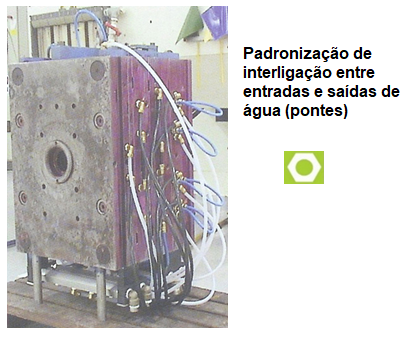
O uso de fichas de processo, sejam em papel ou no programa da máquina na injetara deve ser aplicada de forma mensurável e repetitiva. A maioria dos casos em que se perde tempo no ajuste de uma injetora é porque aquela máquina não tinha ficha de processo para aquele molde ou produto.
É de elevada importância o treinamento sobre a operação e programação dos robôs para os trocadores. Nas empresas que utilizam robôs para a retirada de peças o início de produção fica sujeito à chegada do técnico especialista neste equipamento para colocar a máquina em marcha.
Como curiosidade, em uma determinada empresa o processo consiste em:
. Trocador de molde coloca o molde em máquina;
. Trocador de molde preenche uma ordem de serviço1 . para a manutenção elétrica da fábrica solicitando instalação dos conectores da câmara quente e ligação da mesma e;
. Após instalação e aquecimento da câmara quente trocador de molde libera a máquina para produção.
O tempo perdido nesta etapa representa 26,8%do tempo total da troca do molde. O problema foi resolvido com um treinamento para a equipe de troca de molde, educando sobre as técnicas de conexão correta dos cabos elétricos e sobre a ligação do sistema de câmara quente.
Otimização do setup externo
As primeiras atividades para ganho de eficácia são :executadas nos processos internos, como visto ante’ífiormente. Todavia, também os processos externos ‘podem ser significativamente melhorados.
Como mostra a Figura 7, o carrinho dos trocadores de moldes era de difícil manuseio e visualização das ferramentas, pois elas estavam armazenadas em gavetas. Foi substituído por outro que apresenta melhor organização e visualização das ferramentas (Figura 8). É possível verificar a falta de alguma ferramenta sendo mais fácil encontrar determinada chave, além de esse carrinho ser mais baratos que os tradicionais.
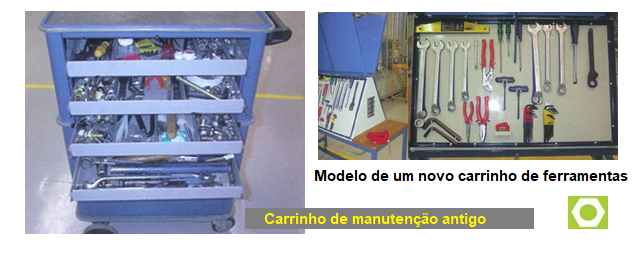
Definição de procedimentos
Por fim, é importante formalizar a metodologia de!envolvida de maneira que sua aplicação seja independente da equipe que a desenvolveu.
A instituição de procedimentos claros e precisos facilita a execução dos processos de preparação das máquinas, regulamentando o seu cumprimento para racionalização dos tempos.
CONCLUSÃO
Nota-se pela Figura 9 que a sistemática de TRF começou a dar resultados e os tempos das trocas começaram a ser reduzidos.
Nas melhorias implementadas em três máquinas, no período de janeiro a março, tivemos uma redução para 32% do tempo inicial na primeira máquina (TA), para 90% na segunda (TB) e para 26% na terceira (TC). Entretanto, a partir do mês de abril foram feitas mudanças no quadro de pessoal, inclusive com o desligamento do gerente da área. Essas alterações causaram descompasso no processo e falta de acompanhamento dos índices de troca de molde, resultando em aumento destes indicadores. A média, que já registrava uma redução de 62% do tempo original, foi desloca da para um ganho de apenas 30%. É de responsabilidade da gerência de produção acompanhar o tempo da troca. Um simples formulário Gestão à Vista deixa o preparador mais atento. Os índices de troca de molde devem ter a mesma atenção que os índices de produtividade, qualidade, refugo, eficiência entre outros.
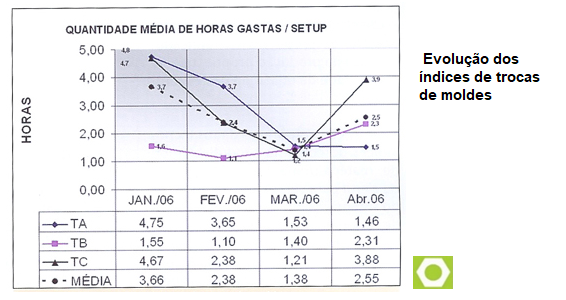
Publicado em 12/06/2017
Por: Gilsilei Bertoloti
Fonte: Revista Ferramental