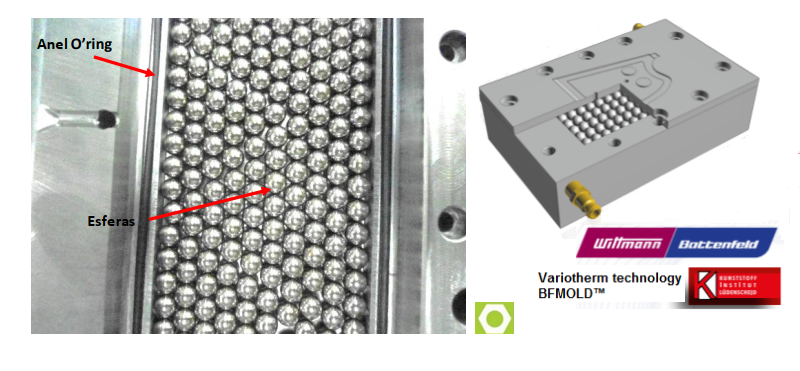
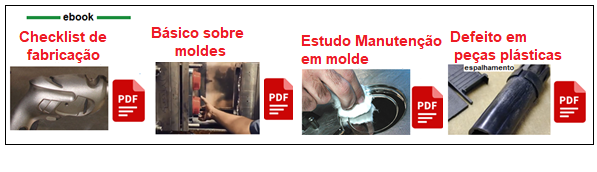
Análise comparativa entre sistema de refrigeração convencional x nova tecnologia BFMold
Levando se em conta a importância que a refrigeração do molde e o tempo de resfriamento tem dentro do processo de injeção, a busca pela redução do ciclo é um fator decisivo para a lucratividade, pois aumenta a produtividade do molde e diminui o custo de produção por peça.
Acompanhando o avanço de pesquisas, esse Estudo tem por finalidade comparar o sistema de refrigeração convencional de canais perfurados na cavidade com a Tecnologia de refrigeração BFMold desenvolvida pela empresa Wittmann-Battenfeld, com objetivo de avaliar assim a sua eficiência energética, influência e possíveis ganhos no ciclo de injeção, o que justificaria o investimento devido seu custo considerável.
Este resumo tem por objetivo levar conhecimento e caso deseje detalhes e mais informações acesse Tecnologia BFMold e ainda Análise Comparativa .
Desenvolvimento do trabalho proposto
O Método
Diante das considerações feitas, a proposta deste trabalho se resumiu ao
dimensionamento, projeto, fabricação e teste de um molde experimental que contenha o sistema de refrigeração convencional assim como o sistema de refrigeração BFMold. O método de análise será um comparativo entre esses dois sistemas de refrigeração, para comprovar a eficiência desse sistema e justificar um possível investimento na aquisição dessa tecnologia. Esse comparativo será realizado qualitativamente e quantitativamente sobre amostras injetadas no molde com os dois sistemas de refrigeração.
Fluxograma de trabalhoPara entender melhor os passos que foram realizados, a figura representa o fluxograma da proposta para esse trabalho.

O produto
O produto protótipo para o desenvolvimento desse trabalho foi definido como uma placa plana com 140 x 60 mm de área e 2 mm de espessura. Foi adotado o conceito de placa plana devido à facilidade e o custo de fabricação do molde protótipo, além de ser o tipo de produto mais indicado para a aplicação da tecnologia BFMold.
O tamanho assim definido para se adequar ao molde de testes já existente, não sendo necessária a fabricação de todo o molde. A espessura de 2 mm foi escolhida, pois é a mais utilizada nos produtos com este material. A Figura apresenta um esboço preliminar do produto objeto desse trabalho.
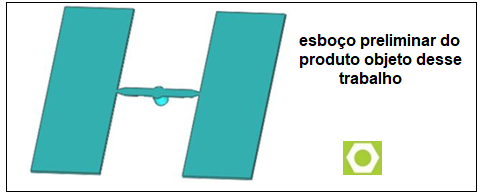
A Matéria-prima
O produto foi injetado em Polipropileno TC136 com 40% de carga de talco (PPT40), do fabricante Borealis, pois como pode ser visto na figura, é um dos polímeros mais consumidos pela empresa Sulbras, onde será desenvolvido o trabalho. Como observação, temos que os produtos injetados em polipropileno têm um tempo de resfriamento relativamente alto, devido aos “rechupes”, empenamentos e a baixa temperatura de desmoldagem provenientes desse tipo de material.
Características básicas:
- a) densidade de 1240 kg/m³;
b) índice de fluidez de 7 g/10min;
c) temperatura da massa de 200 a 240°C;
d) temperatura do molde de 20 a 40 ºC.
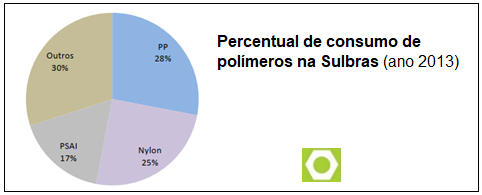
O moldeO conceito foi desenvolvido sobre um molde já existente na empresa, a fim de se reduzir os custos e o tempo de fabricação, e definido que seria composto por duas cavidades geometricamente iguais nas dimensões de acordo com o produto definido anteriormente. Uma das cavidades idealizada com os circuitos de refrigeração convencionais (em “U”) e a outra com a tecnologia de refrigeração com esferas, a BFMold.
O sistema de refrigeração convencional foi dimensionado de acordo com a metodologia padrão utilizada, já para o sistema BFMold, calculou-se pela teoria de trocador de placas paralelas, o qual se assemelha muito com o sistema construtivo e de troca de calor do BFMold.
O material para a construção do molde é o AISI 1045, devido a sua disponibilidade no mercado, custo baixo e de fácil usinagem, tendo em vista que o molde é protótipo de vida útil reduzida.
Preferiu-se utilizar os dois sistemas de refrigeração no molde a fim de eliminar variáveis do processo, como: temperatura da massa fundida, temperatura da água de refrigeração, temperatura da cavidade do molde, desgaste da máquina injetora, temperatura ambiente entre outras, assim pode-se avaliar somente a influência do sistema de refrigeração no processo de injeção. Na Figura pode-se observar um esboço preliminar do molde protótipo.
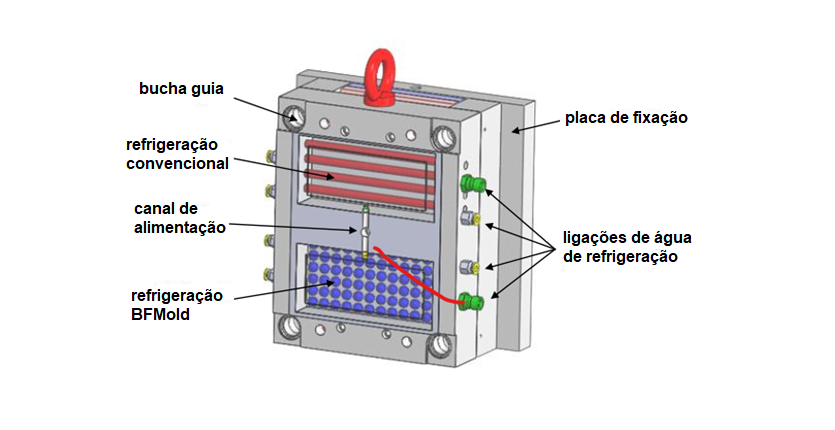
Dimensionamento projeto e execução
Circuito em U – informação auxiliarEsse tipo de circuito é comumente utilizado para refrigerar cavidades longas e estreitas, consiste em um par de furações passantes que são conectadas por uma mangueira ou por uma furação cruzada na sua extremidade, esse tipo de refrigeração é um dos mais simples e econômico, é muito utilizado em moldes de baixa complexidade, na Figura pode ser observado um exemplo desse sistema o qual tem a conexão entre os dutos feita por meio de uma mangueira
Circuito em Z – informação auxiliar
O circuito Z, por sua vez, é uma variação do circuito U com várias interligações, este é utilizado para refrigeração de grandes áreas e placas planas, sempre que for possível o número de canais de refrigeração deve ser par, do modo que a entrada e a saída da água estejam do mesmo lado do molde.
Segundo Brito et al. (2004) para evitar um aumento progressivo da temperatura do fluido de refrigeração ao longo do molde deve se evitar que o circuito tenha muitos canais (muito longo), caso isso aconteça, é possível fazer a divisão em dois circuitos em Z menores, sempre buscando a simetria entre os circuitos.
Na figura pode-se observar uma aplicação do circuito Z na refrigeração de uma placa plana, onde o mesmo foi dividido em dois circuitos menores para reduzir o efeito do aumento da temperatura do fluido ao longo do sistema de refrigeração.
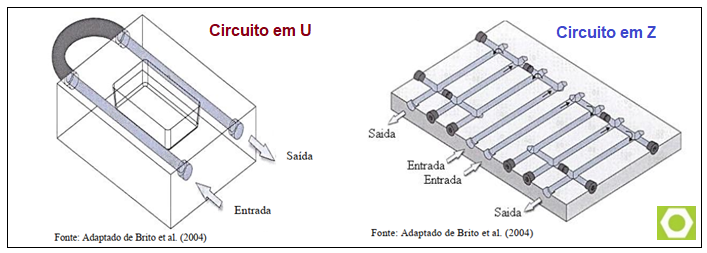
O sistema de refrigeração de moldes de injeção por dutos em “U” e “Z” é amplamente utilizado na fabricação dos moldes, devido à facilidade de sua aplicação e fabricação. Outros aspectos positivos desses sistemas são o baixo custo de construção, e a rapidez com que são fabricados.
Em contrapartida, esse sistema de refrigeração tem uma eficiência menor, pois ele tem uma reduzida área de troca térmica com o fluido refrigerante. Essas áreas de trocas são localizadas em pontos específicos, o que ocasiona uma refrigeração não uniforme e com um tempo maior. Para peças de menor complexidade e de baixo volume de produção esses aspectos negativos não são impactantes para o processo, e por esse motivo esses sistemas “convencionais” ainda são os mais utilizados nos moldes de injeção.
No entanto, para moldes de maior complexidade, alto volume de produção, dentro de um mercado cada vez mais competitivo, onde uma redução de segundos no ciclo de injeção significa a lucratividade ou não do negócio, é necessário investir em tecnologias, que muitas vezes tem um custo elevado, sem a garantia do retorno desejado para a aplicação em um caso específico. Assim, surge a necessidade de se comprovar experimentalmente a eficiência ou não de uma dada tecnologia, para depois aplicá-la em maior escala dentro da necessidade da empresa. Baseado nisso, esse trabalho executou um teste experimental para comparar o sistema de refrigeração convencional com a tecnologia de refrigeração BFMold, e para isso foram definidos a seguir os parâmetros preliminares.
Com o produto já definido nas características mostradas anteriormente, foi dimensionado o sistema de refrigeração convencional baseado na literatura apresentada e com os valores calculados foi possível projetar a refrigeração para uma cavidade do molde do produto definido, onde foram projetados seis canais de refrigeração para a cavidade com sistema convencional, sendo três no lado fixo do molde e três no lado móvel, chegando a um comprimento total de 1,2 m de canais de refrigeração muito próximo dos 1,02 m calculados. Posteriormente esse sistema de refrigeração passou por uma análise moldflow® para verificar se foi corretamente dimensionado e atenderá a necessidade do produto protótipo.

Para o projeto do sistema de refrigeração BFMold utilizou-se o conceito de convecção forçada sobre uma placa plana, onde se tem uma grande área de contato entre o líquido refrigerante e o molde, assim promovendo uma melhor dissipação de calor. Após foi realizada uma verificação dos valores encontrados usando a teoria de escoamento em meios porosos, situação construtiva que se assemelha com a cavidade de refrigeração cheia de esferas proposta.
Para fins comparativos foi definido que o fluxo de refrigerante será o mesmo que o do sistema de refrigeração convencional (4,61 l/min) e a espessura entre a refrigeração e produto também será 21,5 mm para avaliar se com a mesma configuração de molde e disponibilidade de água o sistema BFMold é mais eficiente.
O tamanho da cavidade de refrigeração que contém as esferas é ligeiramente maior que a peça, tendo um tamanho de 152 x 72 mm e uma espessura de 8 mm; conforme foi verificado através das teorias de transferência de calor sobre placa plana e escoamento em meios porosos, além de ser um tamanho de esfera comercial de fácil acesso. Na teoria de convecção forçada em um escoamento sobre placas planas, de acordo com Incropera et al. (2008), tem-se uma grande área de contato entre o líquido refrigerante e o molde, assim promovendo uma melhor dissipação de calor.
Em resumo, verificou se que a vazão mínima necessária foi de 0,02 litros por minuto, muito menor que a disponibilizada em máquina, logo está garantida e eficiência do sistema utilizando uma esfera de 8 mm.
Como não existe uma teoria para o escoamento e transferência de calor que represente fielmente o sistema de refrigeração proposto, o seu correto funcionamento foi garantido de acordo com as duas teorias que mais se aproximam do seu sistema construtivo. Verificado que o diâmetro de esferas escolhido de 8 mm atende perfeitamente, e com certa folga, foi então projetado o sistema de refrigeração BFMold.
Analise de moldflow
Dimensionado o sistema de refrigeração, foi então modelado o molde por completo, baseado em um molde de testes já existente na empresa e submetido esse modelamento a uma análise em moldflow para obter os parâmetros teóricos para o processo de injeção, assim como obter um resultado preliminar no que diz respeito ao sistema de refrigeração.

Esses resultados demonstram que o sistema de refrigeração convencional se mostrou eficiente para o produto, comprovando a técnica de dimensionamento apresentada para o sistema de refrigeração convencional. Com os resultados da simulação iniciou-se o processo de fabricação do molde, que foi feito internamente na Sulbras, com máquinas e recursos próprios, desde o dimensionamento, projeto, simulações, execução e teste.
Fabricação do moldeA partir da finalização do projeto foi iniciada a fabricação do molde, que se constituiu na usinagem dos componentes, montagem, ajustes e periféricos. As peças usinadas foram feitas internamente na Sulbras, foi utilizado um centro de usinagem CNC para garantir a precisão dos componentes, onde foram necessárias aproximadamente 20 horas de usinagem.
Na figura pode-se observar o resultado final da usinagem da placa plana no lado móvel.

A partir disso foi iniciada a montagem do molde o que solicitou a aquisição de 350 esferas (de rolamento) no diâmetro de 8 mm as quais foram montadas dentro da cavidade de refrigeração, que por sua vez foi vedada com a ajuda de um o’ring como se pode ver na figura.
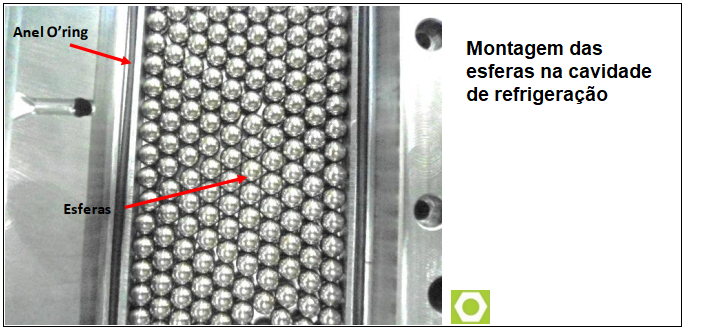
Após foi feito o ajuste das placas do macho e cavidade que ficam acima do sistema BFmold, para melhor compreender essa montagem, visualiza-se a figura

Com as placas ajustadas e montadas foi feita a montagem com o restante do molde protótipo já utilizado pela empresa.
Montagem do molde em máquina e Avaliação do testeNa primeira etapa do teste, os parâmetros de injeção foram definidos de acordo com os dados obtidos por meio de simulação computacional, os demais parâmetros foram estabelecidos de acordo com a necessidade do processo e ajustes pertinentes no ato da injeção.
Com a máquina já em “produção” após vários ciclos de injeção e com o processo estável, foram injetados 60 ciclos, onde foram retiradas cinco coletas sempre na injetada de final 0, ou seja, a cada 10 peças.
Nessas amostras foram feitas a medições da temperatura da peça de cada cavidade assim que foi extraída do molde. Dessa forma, foi possível estipular um valor médio de temperatura. Essa medição foi feita com o auxílio de câmera termográfica FLIR modelo E40.
A diferença de temperatura entre as cavidades, assim como a distribuição da temperatura na superfície das peças já são suficientes para uma avaliação inicial. Na Figura pode-se observar um exemplo de medição de temperatura e a câmera termográfica utilizada.
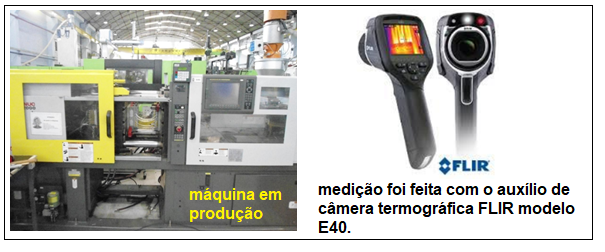
Após foi reduzido o tempo de resfriamento até que a temperatura da cavidade com o ciclo de refrigeração convencional fosse igual à temperatura de desmoldagem característica desse material (55°C para peças técnicas), o mesmo foi feito com a cavidade sistema de refrigeração BFmold e com esses valores de tempo de ciclo foi possível estimar o ganho percentual em produtividade desse tipo de tecnologia de refrigeração.
As peças provenientes desses testes passaram por avaliações posteriores, tanto dimensionais, que foi feita com paquímetro a fim de avaliar a influência no percentual de contração, como avaliações geométricas com a medição da planicidade das peças através de máquina de medição tridimensional Mitutoyo. Foi também avaliado o grau de cristalinidade das peças provenientes do teste através do ensaio DSC disponibilizado pela Universidade de Caxias do Sul.
Com base nesses dados e avaliações foi então possível concluir qual a eficiência da tecnologia de refrigeração BFmold quando comparada a refrigeração convencional por circuitos perfurados na cavidade. Foi possível também identificar a sua influência no produto final e os ganhos com esse processo.
Resultados e discussão
Serão apresentados os detalhes do teste dos equipamentos e recursos utilizados, o processo de obtenção de amostras, resultados obtidos, assim como sua análise e posterior conclusão.
Preparação para coletas de amostras
Com base nos dados preliminares acima descritos, foi então realizado o teste prático a fim de se obter amostras que comprovem o que foi dimensionado anteriormente. O molde e seus periféricos foram instalados na injetora selecionada e apresentada anteriormente, e o ajuste dos parâmetros de injeção foi iniciado. Os parâmetros iniciais de processo foram determinados a partir da simulação moldflow® e replicados na máquina injetora.

A temperatura da água de refrigeração foi programada do termorregulador Piovan com a temperatura pré-estabelecida de 40°C.
A vazão de líquido refrigerante de 4,61 l/min foi regulada e garantida a partir de rotâmetros instalados na própria injetora conforme demonstra a figura, onde a escala máxima do rotâmetro é 200 e corresponde a 10 l/min. Sendo assim, com uma escala de 92 tem-se aproximadamente 4,6 l/min.

Com esses parâmetros garantidos foram então ajustados os demais parâmetros de injeção a fim de se obter um processo estável onde seja possível obter peças perfeitas livres de falhas e imperfeições, possibilitando o processo de comparação entre elas. Na figura observa-se a peça na sua condição ideal de processo de injeção.
Este processo adequado ao produto pode ser observado através da curva de injeção (laranja) mostradas na figura. Assim, com peças na condição ideal foram coletados os demais dados de saída do processo o qual se pode observar a seguir:
a) pico de pressão de injeção 270 bar;
b) tempo de injeção 1,208 seg.;
c) pressão de recalque 215 bar;
d) tempo de recalque 6 seg.;
e) tempo de dosagem 5 seg.;
f) tempo de ciclo 19 seg.,

Resultados
Feito isso, foi então iniciado a contagem para a coleta das amostras como foi explicado no capítulo três, e logo após a retirada da máquina, foram feitas as medições de temperatura das amostras com a câmera termográfica. Para tal, foram definidos dois pontos estratégicos para essa medição que pode ser observado na figura.
Feitas as medições com a câmera termográfica os dados foram montados na Tabela 7, onde foi possível então verificar o comparativo entre as amostras.

Observou-se, preliminarmente, que o sistema BFmold propiciava um resfriamento maior (em média 2°C) em relação ao sistema convencional. A partir desses dados foi então montado o gráfico de temperaturas ao longo do tempo conforme a figura.
Pode-se concluir que os dois sistemas não apresentaram aumento de temperatura no produto ao longo do tempo, o que comprova que o sistema de refrigeração foi corretamente dimensionado.
O tempo entre a extração do produto e a medição da temperatura foi de aprox. 2 segs. E sendo esse processo manual, pode ter causado uma pequena flutuação na curva na amostra 20 como pode ser observado na figura.
Foi possível observar pela Tabela 7 que o sistema BFmold tem uma distribuição mais uniforme de temperatura onde a diferença de temperatura entre a região do canal de injeção e a extremidade do produto é menor se comparado ao sistema de refrigeração convencional, o que comprova a bibliografia.
Enquanto na refrigeração convencional existe uma dificuldade em remover o calor próximo ao ponto de injeção, a peça com o sistema BFmold tem uma temperatura distribuída de maneira mais uniforme ao longo da peça, isso pode ser comprovado pela Figura, onde é possível observar essa diferença de temperatura.

Essa diferença reflete diretamente no empenamento do produto, o que pode ser observado logo após a injeção, onde o sistema convencional teve um empenamento alto e o sistema por cavidade de esferas teve peças bem mais planas. A região próxima ao canal de injeção com maior temperatura tende a contrair de forma diferente que o restante do produto causando assim o empenamento do mesmo.
Para comprovar esse ganho em qualidade do produto, as peças foram encaminhadas para medição de planicidade em uma máquina tridimensional, que gerou um plano formado por 21 pontos sobre a superfície da peça. Na Figura pode-se observar o relatório de medição de uma das injetadas contendo os dois sistemas de refrigeração:

As demais amostras também foram dimensionadas usando a mesma metodologia, os resultados podem ser observados na Tabela 8.
Assim foi possível comprovar o ganho em qualidade do produto devido à tecnologia de refrigeração BFmold. Este parâmetro por si só já justifica um possível investimento em tal tecnologia, pois a característica de planicidade é difícil de se obter em peças moldadas por injeção. Posteriormente foi feita uma avaliação dimensional do percentual de contração, feita através de paquímetro convencional, tomando como medida base o comprimento máximo do produto de 140 mm.
Devido à peça sair mais fria do molde no sistema de refrigeração BFmold a contração posterior é reduzida, em termos de processo, este também é um resultado positivo, pois a contração posterior (que acontece fora do molde) ocorre de forma livre sendo passível de deformações e tensões no produto enquanto a contração dentro do molde ocorre de forma mais controlada.
Isso pode ser comprovado observando a Tabela 9, que mostra a medida lida e o percentual de contração calculado.
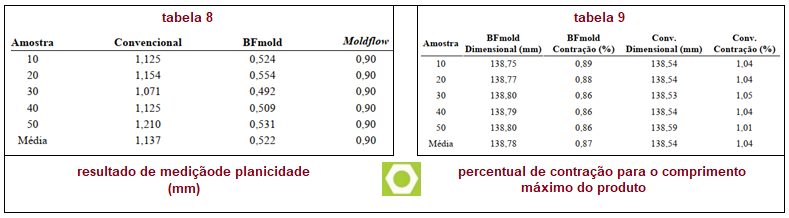
Como forma de dimensionar o ganho em termos de ciclo, foi variado o tempo de resfriamento, partindo do ponto em que a cavidade convencional estivesse na temperatura de desmoldagem, enquanto a temperatura da cavidade com sistema de refrigeração BFmold estava mais fria. Assim foi reduzido o tempo de resfriamento para que esta cavidade chegasse à temperatura de extração, podendo dimensionar o ganho em segundos que é mostrado na Tabela 10.
Foi identificado um ganho no tempo de resfriamento de 3 segundos, que equivale a 20% do tempo de resfriamento total. No ciclo total esse ganho foi de 15,8% o que é um ganho considerável, pois em um dia de produção tem-se um ganho de aproximadamente 850 peças.

Na Figura a seguir observa-se o comportamento da temperatura da peça com a variação do tempo de resfriamento.
ANÁLISE DSC
Foi selecionada a injetada de número 30 para a análise DSC, a qual foi retirada uma amostra de 10 mg, na região próxima ao ponto de injeção, ponto em que houve maior diferença de temperatura conforme as medições realizadas. A seguir na Figura é apontado o local de retirada da amostra no produto injetado.

A seguir serão apresentadas as imagens correspondentes aos termogramas DSC realizados com o material injetado nesse trabalho, sendo que para a comparação será considerada somente a primeira corrida térmica para determinação do grau de cristalinidade. A seguir na Figura pode-se observar o termograma da amostra injetada com sistema de refrigeração convencional.
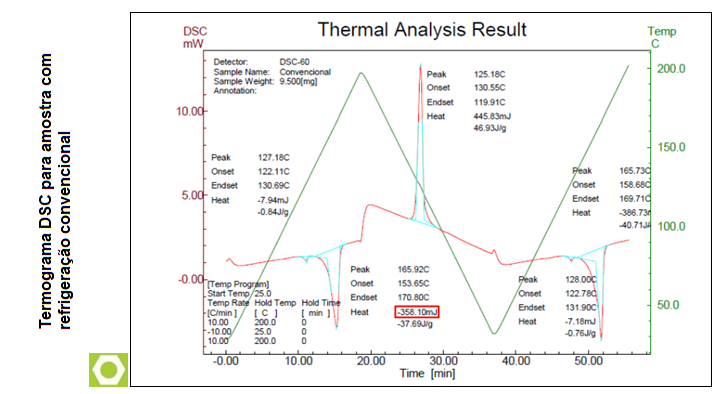
Observando a figura acima se observa um calor de fusão de 358,1 mJ para o pico referente a primeira corrida de fusão do amostra, dividindo este valor por 6 mg (quantidade de polipropileno puro em uma amostra de 10 mg de PPT40) temos um valor de calor de fusão corrigido de 59,68 J/g. Quando comparado este valor aos 209 J/g de um polipropileno hipoteticamente 100% cristalino nos dá um grau de cristalinidade de 28,55%.
A mesma avaliação pode ser feita na Figura que mostra o termograma DSC para a amostra injetada com o sistema de refrigeração BFmold.
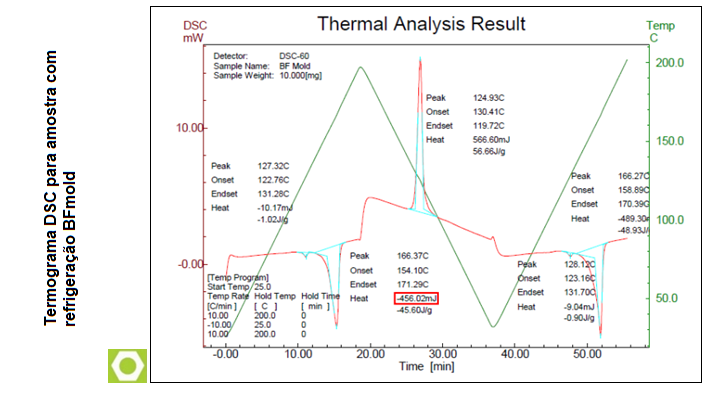
Para essa amostra o calor de fusão foi 456,2 mJ, fazendo a mesma correlação
utilizada para amostra com refrigeração convencional chegamos a um calor de fusão corrigido de 76,0 J/g que comparado ao valor padrão citado acima nos retorna um grau de cristalinidade de 36,4%, que é 7,85% maior do que as amostras injetadas com o sistema de refrigeração convencional.
Através desses dados apresentados pode-se observar que o sistema de refrigeração por cavidade de esferas promoveu um aumento na cristalinidade do polímero injetado. Esse aumento se deve ao resfriamento mais uniforme promovido por esse sistema de refrigeração, que reduz a diferença de temperatura entre diferentes regiões do produto.
Esse aumento da cristalinidade reflete diretamente sobre as propriedades mecânicas do polímero, assim como na geometria, pois o polímero com suas cadeias mais organizadas reduz a deformação pós processamento, isso pode ser verificado com a medição de planicidade apresentada anteriormente, onde as peças injetadas com o sistema de refrigeração BFmold apresentaram melhor planicidade.
CONCLUSÃOBaseado nos resultados apresentados, conclui-se que o sistema de refrigeração de molde de injeção por cavidade de esferas traz muitos benefícios ao processo. O ganho em temperatura de extração foi considerável, e garantiu um tempo de ciclo de aproximadamente 15% menor, o que é um grande avanço levando em conta que para esse estudo foi feito correto dimensionamento do ciclo de refrigeração convencional, que se mostrou eficiente dentro dos parâmetros calculados.
Esse ganho por si só pode definir o desempenho econômico do molde de injeção, pois reduz o custo operacional por peça, podendo ser um fator decisivo em um mercado cada vez mais competitivo. Outro ponto a ser observado é a diferença no percentual de contração, onde a peça que possuía o sistema de refrigeração posterior teve um percentual de contração menor
(aproximadamente 0,9%) em relação à peça com refrigeração convencional
(aproximadamente 1,05%), isso pode ser atribuído ao fato de a peça com refrigeração por cavidade de esferas sair mais fria do molde, reduzindo sua contração posterior.
Na avaliação DSC foi observado um aumento no grau de cristalinidade de 7,88% sendo de 28,55% para a amostra injetada com sistema de refrigeração convencional contra 36,4% para a amostra injetada com o sistema de refrigeração de cavidade de esferas, esse aumento na cristalinidade refletiu em um ganho na característica geométrica do produto. E este foi o ganho mais importante encontrado nas análises feitas, a qualidade geométrica da peça.
O sistema de refrigeração apresentado possui um sistema construtivo que propicia uma refrigeração mais homogênea, enquanto a peça com sistema de refrigeração convencional apresentava uma região mais quente próximo ao canal de injeção. Essa diferença de temperatura na peça causa uma contração diferente em determinadas regiões do produto causando uma deformação por empenamento.
Essa deformação foi determinada através da medição de planicidade da peça, onde os resultados encontrados foram de aproximadamente 0,52 mm para a peça com refrigeração BFmold contra aproximadamente 1,12 mm da peça com refrigeração convencional. Essa melhoria é de grande importância, pois é difícil reduzir empenamentos no processo de injeção.
Comparando os resultados obtidos com a simulação no moldflow®, foi observado que os valores encontrados no teste prático refletem com uma boa precisão o que o simulado, tendo em vista a comparação de deflexão máxima e temperatura de extração.
Com tudo isso se pode concluir que o sistema de refrigeração BFmold é uma ótima alternativa para produtos específicos de geometria plana, pois os investimentos nessa tecnologia podem trazer benefícios em ganho de produtividade e qualidade. Esse investimento inicial é de aproximadamente EUR 12.000,00 (referência ano 2013)que em um molde comercial de grande volume de produção, justifica seu investimento pela série de benefícios apresentados anteriormente.
É importante salientar que a utilização dessa tecnologia depende muito do
sistema construtivo do molde.
Outro ponto importante foi o da vazão de água utilizada, pois foi verificado que o sistema BFmold possui menos restrição ao escoamento, sendo possível escoar mais água por dentro da cavidade de refrigeração, essa vazão foi controlada via rotâmetro e mantida igual para os dois sistemas para garantir o comparativo.
O mesmo ocorre com a distância entre a cavidade de refrigeração e a peça, que foi mantida a mesma que para a refrigeração convencional, assim foi possível comparar somente o ganho em tipo de transferência de calor.
Os resultados obtidos refletem o que foi dito no capítulo 2 (link anexo), onde foi ressaltado que uma etapa muito importante no projeto de um molde de injeção é a arquitetura e dimensionamento dos dutos de refrigeração, é onde se pode apresentar o sistema de refrigeração BFmold como uma alternativa para ganhos em produtividade e qualidade comprovada para determinados produtos produzidos pelo processo de moldagem por injeção.
Sugestões de melhorias
Como sequência desse trabalho, para fim de aumentar o ganho em produtividade do sistema de refrigeração por cavidade de esferas, pode ser feita uma avaliação da distância da cavidade de refrigeração até a peça, reduzindo-a até uma condição ótima, visto que o suporte mecânico da placa que contém a cavidade está garantido pelas esferas; assim aumentando a taxa de transferência de calor neste sistema.
Outro ponto a ser melhorado é explorar a vazão máxima de água no sistema, que se mostrou maior do que a com dutos perfurados. Esse aumento de vazão aumenta a turbulência do sistema e consequentemente a taxa de transferência de calor por convecção do sistema de refrigeração.
Para tornar o estudo mais aprofundado também sugere se a medição da temperatura da cavidade do molde com auxílio de termopares.
Resumo e Publicação exclusiva Moldes Injeção Plásticos
Méritos a Sulbras e Wittmann-Battenfeld
Autor EVAIR JOSÉ BASSO Agradecemos Autorização
REPRODUÇÃO PROIBIDA SEM AUTORIZAÇÃO
Editado por: Moldes Injeção Plásticos