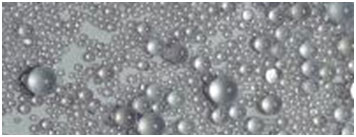
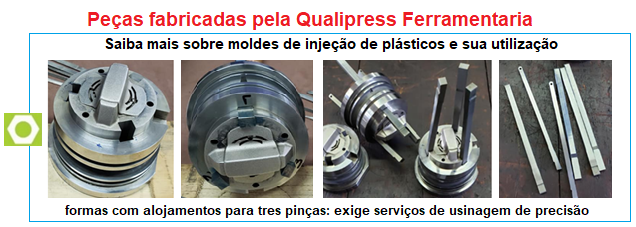
A influência de cargas na composição da matéria prima
As cargas são substâncias que são misturadas a um material base de forma a não se solubilizar ou reagir, e sim permanecer difundidas uniformemente no mesmo. No caso da borracha, uma pequena porcentagem de carga (até 3%) favorece a vulcanização, porém normalmente as cargas são utilizadas em proporções muito maiores que esta, com o objetivo básico de reduzir o custo do material.
Já com respeito aos termofixos e aos termoplásticos, as cargas são utilizadas para conseguir ou aumentar algumas propriedade definidas dos mesmos, mesmo que, quase sempre, às custas da diminuição indesejável de outras propriedades. Não é incomum um termoplástico com cargas custar mais caro que o mesmo material sem carga.
Nos termofixos, as cargas incluem uma vasta gama de materiais, incluindo asbestos, serragem de madeira e pós metálicos. Na borracha, é mais freqüente o uso de minerais, como caulim, e pós de diversas rochas.
As cargas utilizadas com maior freqüência no termoplástico são a fibra de vidro (FV), micro-esferas de vidro (MEV), o talco e o caulim. Com menor freqüência, e visando conferir ao termoplástico características bastante especiais, são usados grafite em pó, bissulfeto de molibdênio em pó e com maior raridade, em casos muito especiais, pós metálicos.
É muito comum o uso de cargas em praticamente todos os termoplásticos, porém para alguns deles, a porcentagem de carga deve ser limitada para evitar perder a qualidade típica do material, responsável pela sua indicação.
É o caso do acetato, cuja característica mais atraente é o “efeito mola” aliado à alta resistência à flexão, propriedades estas que podem ser bastante prejudicadas pela adição de cargas. Respeitadas as limitações de cada tipo de carga, contudo, as mesmas são largamente utilizadas.
As fibras de carbono são utilizadas para dar leveza e resistência.
São fibras formadas por longas cadeias de átomos de carbono. Estas fibras são longas, de cor preta e aspecto sedoso, muito mais resistentes e muito mais caras que as fibras de vidro. A resistência à tração das fibras de carbono chega a 70.000 kg/cm², quase o dobro dos 45.000 kg/cm² que podem ser alcançados pela FV.
Na maioria das aplicações são usadas na forma de mantas tecidas com as fibras, dispostas em camadas sobrepostas e em ângulos adequados, cuidadosamente estudados para conferir às peças a maior resistência possível; estas camadas sobrepostas de mantas são embebidas em resinas do tipo epóxi, poliéster, fenólica ou polyimida, nas mesmas técnicas usadas na fabricação de peças de fiber glass.
Peças feitas com estas técnicas são usadas quando o fator custo tem prioridade secundária e se quer obter peças leves e muito resistentes, como aplicações da indústria aeronáutica e aeroespacial, que as utiliza em peças estruturais de mísseis, satélites e aeronaves. Também são usadas em carros de Formula 1 e em equipamentos esportivos caros como esquis, raquetes e varas de pesca.
Embora menos usadas como reforço em termoplástico para injeção do que a fibra de vidro, quando o são, apresentam-se como fibras de seção circular, com diâmetro aproximado de 0,01 mm, cortadas em comprimentos de 2 a 3 mm.
As vantagens obtidas com o uso de fibras de carbono como reforço em termoplásticos são o aumento da resistência mecânica e da rigidez, bem como da resistência ao desgaste, à fluência e à fadiga. Aumentam também a estabilidade dimensional das peças.
Do ponto de vista eletro-eletrônico, os termoplásticos reforçados com fibras de carbono apresentam um atrativo especial: como as fibras são condutora, apresentam efeito de blindagem elétrica, protegendo os circuitos eletrônicos contra interferência eletromagnética.
As Micro-Esferas de Vidro dão maior resistência ao calor e tração.
São esferas microscópicas e maciças com diâmetro médio aproximado de 0,025 mm, muito usadas principalmente como carga para as poliamidas, às quais conferem maior resistência ao calor e melhor resistência à tração e à compressão, melhorando inclusive o módulo de elasticidade à flexão.
Uma variação deste material são as micro-esferas ocas que são esferas com diâmetro externo médio de aproximadamente 0,075 mm com espessura de parede de 0,001 a 0,002 mm, e que são usadas em casos especiais onde além de se procurar as vantagens oferecidas pelo emprego das micro-esferas de vidro, é também de grande importância manter a densidade do material tão baixa quanto possível.
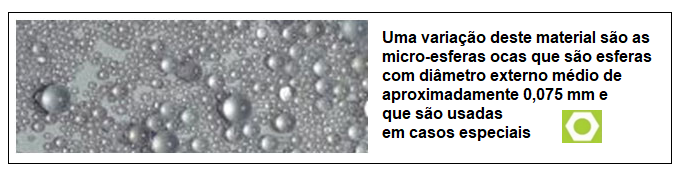
As micro-esferas de vidro, tanto as sólidas quanto as ocas, além dos motivos mencionados acima, são usadas como carga nas poliamidas e poliésteres em porcentagem de 5 a 30%, para melhorar a fluidez e conferir a estes termoplásticos um comportamento mais isotrópico.
O talco aumenta a rigidez.
O talco, silicato de magnésio hidratado, em partículas com tamanho médio de 2 a 20 microns, dureza mohs de 1,0 é usado principalmente como carga para o polipropileno. Neste termoplástico, o talco, em porcentagem de 10 a 40%, aumenta a rigidez e eleva a temperatura de deflexão ao calor, mantendo boas as propriedades de resistência à tração, compressão e impacto.
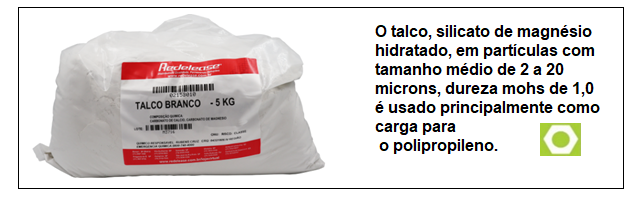
As fibras de vidro reforçam as peças moldadas.
As fibras de vidro são usadas para reforças peças moldadas de resinas plásticas, laminados, e peças injetadas de termoplásticos.
O tipo de material mais utilizado é o vidro “E” (vidro “elétrico”) por apresentar boas características elétricas, boas propriedades mecânicas, resistência ao calor, à água e aos ácidos. É utilizado na forma de fibras longas, com diâmetro de 0,01 a 0,02 mm, e é apresentado como feixes de fibras ou em forma de tecido ou manta.
Quando usado em termoplásticos para injeção, estas fibras são cortadas com comprimentos de aproximadamente 2 mm. Usada em porcentagens de 5 a 30% é de grande utilidade para melhorar as propriedades mecânicas dos termoplásticos, bem como sua resistência ao calor, porém prejudica o aspecto superficial das peças, tornando-as opacas, e por vezes “malhadas”, ou seja, com aspecto desigual entre uma região e outra da mesma peça.
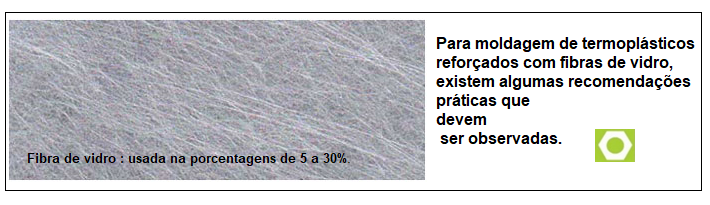
Para moldagem de termoplásticos reforçados com fibras de vidro, existem algumas recomendações práticas que devem ser observadas.
O encolhimento das peças moldadas em termoplásticos reforçados é significativamente inferior ao correspondente aos termoplásticos não-reforçados. O encolhimento depende da espessura da peça, número de cavidades do molde e do desenho do ponto de injeção.
Ponto de injeção com diâmetros de até 0,8 mm podem ser empregados mas geralmente não se recomenda entradas com diâmetros inferior a 1 mm. Pode ser observado um aumento marcante na resistência ao impacto e tração das peças moldadas com pontos de injeção de maior abertura.
A localização inadequada dos pontos de injeção pode dar origem a empenamentos nas peças moldadas. É conveniente que as entradas dos molde sejam posicionadas de forma tal a permitir um arranjo aleatório ( não orientado) das fibras dentro da cavidade.
Os canais de injeção devem ser bem polidos, cônicos e os mais curtos possíveis. Os moldes devem ser projetados com vista a permitir rápido enchimento das cavidades. Respiros com maior abertura, ou em maior número, devem ser considerados. As rebarbas serão menores que com termoplásticos não reforçados.
O fluxo de materiais no molde deve ser mais rápido, para compensar a rápida solidificação dos termoplásticos reforçados.
O controle de temperatura da superfície do molde tem importante influência no enchimento e acabamento das peças moldadas. Quanto mais frio o molde, mais curto o ciclo de moldagem e pior o acabamento superficial das peças.
Linhas de solda (onde os fluxos se encontram dentro da cavidade) devem ser evitadas através do projeto adequado dos moldes e pontos de injeção. Isto é recomendado porque ocorre um alinhamento (orientação) acentuado das fibras nas linhas de solda.
Como regra geral a espessura das paredes de peças moldadas em termoplásticos reforçados não deve ser inferior a 1 mm.
Variações bruscas na espessura da peça deve ser evitadas para impedir concentrações de tensões e afloramento superficial das fibras.
O caulim é utilizado como carga de reforço.
Este material, que é componente principal da fabricação da porcelana chinesa, na forma de pequenas partículas hexagonais de 0,3 e 5,0 microns e com largura de 8 a 12 vezes a espessura, na sua forma calcinada (o caulim existem em 3 tipos: lavado em água, calcinado e separado por ar) é uniforme, de alto brilho e baixa abrasividade.
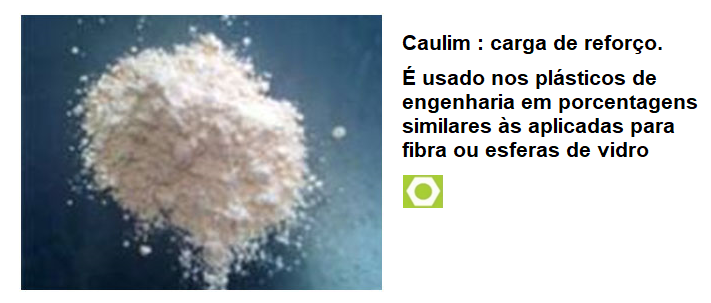
Nesta forma, é usado como carga de reforço em poliamidas e outros plásticos de engenharia devido à melhoria que proporciona na resistência mecânica dos mesmos. É usado nos plásticos de engenharia em porcentagens similares às aplicadas para fibra ou esferas de vidro. É também muito usado em compostos de vinil para revestimento de fios, para melhorar as propriedades relacionadas com a isolação elétrica.
Publicado em 12/06/2017
PROIBIDA REPRODUÇÃO SEM AUTORIZAÇÃO
Hamilton Nunes da Costa – Editor de Revistas Independente
CFP VW SENAI / Matrizeiro especializado em molde
Projeto de moldes / Escola ART-MEC
Técnico mecânico CREA 126.785 / CFP VW SENAI