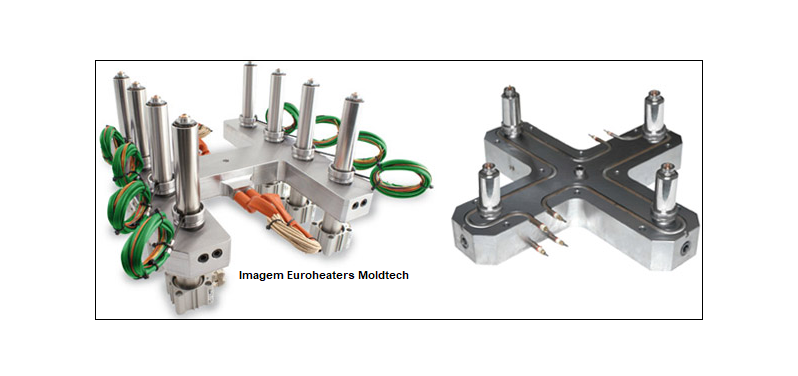
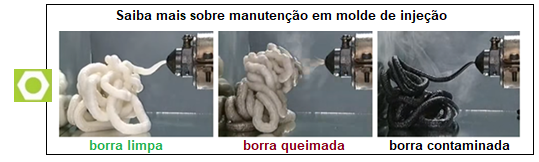
OBS: CUIDADO TEM LIVRARIA OFERECENDO LIVRO COM NOSSO CONTEÚDO
Câmara quente: conhecendo o sistema e ações para a manutenção
A divulgação e uso constante de sistemas de câmara quente oferece ao profissional através do conhecimento, condições de melhor utilizar o produto e melhorar o rendimento.
A dependência constante da assistência técnica pode não ser um bom negócio, sendo importante investir em treinamento para os funcionários.
A evolução tecnológica trouxe para a sociedade benefícios que às vezes não se enxergam claramente, mas que no dia à dia vem facilitando a vida como um todo. Na área industrial onde nos encarregamos de aplicar as inovações, vemos de perto as mudanças e vivenciamos as transformações com novos desafios .
Os sistemas de câmara quente de certa forma revolucionaram os processos produtivos no setor de plásticos e junto com eles aprendemos a fazer melhor e também solucionar novos problemas. Os sistemas permitem produzir com menos tensões internas comprometedoras, portanto, com melhor qualidade.
As tensões no produto final são reduzidas, pois o material já entra na cavidade do molde com a temperatura ideal para injeção. Na injeção por canal frio ( convencional), o plástico troca calor com o molde já nos galhos de distribuição causando congelamento na parede do canal. Este congelamento restringe a passagem do polímero até a peça, causando um maior cisalhamento das moléculas .
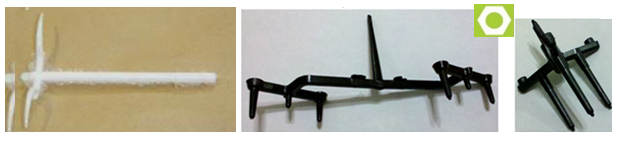
As inúmeras vantagens vindas com os sistemas trouxeram também novas soluções e medidas corretivas para os problemas de peças termoplásticas injetadas , já que os sistemas de câmara quente são os responsáveis pelo sucesso na injeção.
Problemas na injeção de peças plásticas em moldes com sistema de câmara quente, em geral são os mesmos da injeção convencional, porém acontecem com frequência menor e com maior facilidade corretiva, devido a eficiência e controle dos sistemas utilizados.
Os sistemas de câmara quente incorporam tecnologia avançada de mecânica dos fluidos, resistência dos materiais e transmissão do calor sendo que estão sujeitos a alta pressão de injeção e a altas temperaturas. Para preservar a vida útil dos componentes, vedações e do elemento de aquecimento é importante que a temperatura seja controlada e mantida dentro dos limites de segurança operacional, por isso é recomendável o controle individual de cada componente aquecido.
Em nosso país, recebemos pacotes prontos com importação de produtos de industrias que investem em novas tecnologias e processos e aí sim, vamos nos desenvolver , adaptar e depois criar similares. É repetitivo mas , importante sempre a lembrança de que a injeção de plásticos por sistema de câmara quente proporciona grandes vantagens em relação ao sistema convencional de injeção .
O sistema trata-se de um componente que devidamente instalado no molde, permite a injeção com a eliminação total ou parcial do canal, a menores pressões, em menor tempo, com menos mão-de-obra direta, menor consumo de energia, melhor utilização da máquina injetora e melhor qualidade.
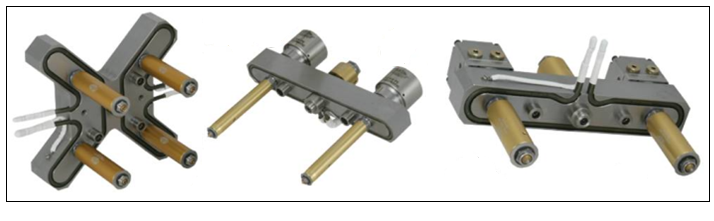
Os sistemas de canal quente, também conhecidos por câmara quente são sistemas de alimentação baseados no emprego de canais controlados termicamente para o processamento de materiais termoplásticos. Sua função é manter o material no estado fundido desde o bico do canhão da injetora até o canal de entrada na cavidade do molde.
Os moldes de canais quentes permitem a obtenção de peças sem extração do sistema de alimentação e já sabemos que o custo do molde é mais elevado, devido à sua maior complexidade e maior custo dos componentes. Utilizando um molde com câmara quente o executor devera apenas se preocupar com o sistema extrator . O que facilita o projeto e a fabricação do molde .
Vantagens em Relação ao Sistema Convencional
– Eliminação de perda de material (inclusive eliminação da moagem) gerando redução do custo de produção. Sensível economia de matéria-prima em especial nos casos em que o peso do galho, por aspectos técnicos, chega a superar o das peças. Conforme a peça a ser fabricada e matéria-prima utilizada os galhos não podem ser moídos, e o desperdício de resinas se torna ainda mais significativo.
– Os canais ou galhos produzidos durante o processo de injeção convencional podem representar muitas vezes , mais de 15% do material total utilizado por ciclo. Se êstes forem congelados, representam no mínimo, 15% do rejeito do processo, mais o rejeito de quando o processo estiver desregulado onde todo o conjunto deve ser desprezado (Manrich,p.365,2005).
– Redução do custo de produção graças à eliminação de sistemas de moagem e mistura, pois a ausência de galhos elimina a necessidade de reciclar materiais já transformados ( não precisará investir na compra de moinhos).
– Melhor Qualidade devido controle preciso do processo com utilização apenas de material virgem.
– Não ocorre a variação de cor, pois não há mistura de material virgem com moído.
– Redução do refugo por contaminação no material devido ao manuseio. (referente o retorno de material reciclado).
– Utilização de menores pressões de injeção e consequentemente menores pressões de travamento aumentando a vida útil dos equipamentos, o que significa peças menos tensionadas.
– Preenchimento de cavidades com espessuras reduzidas devido à menor perda de pressão causada pela bucha fria e canais de distribuição.
– Como o material entra na cavidade no estado fundido ocorre melhora no aspecto visual da peça e redução de contrações, chupagem e linhas de emenda (junta fria).
– Evita presença de metais junto com material plástico.
– Maior possibilidade de automação do processo de injeção.
– Vestígios de injeção podem ser controlados e em alguns casos tornam-se praticamente imperceptíveis.
– Os ciclos mais curtos resultam também, em menor uso das máquinas injetoras.
Utilização cria condições de melhorias.
A prática e o emprego constante desta nova tecnologia com certeza vai divulga lá e oferecer ao profissional condições de melhor utilizar o produto e com melhor rendimento, algo que só o conhecimento oferece. Digamos que o sistema de câmara quente consiste em um bloco de aquecimento ( metálico ) com resistências elétricas alojadas estrategicamente em canais devidamente distribuídos para que haja o aquecimento por igual em toda amassa do bloco. ( Esse bloco também é conhecido como “ manifold ”e bicos de injeção que podem , ou não conter resistência elétrica ).Termopares ficam em contato com os canais em vários pontos, mas principalmente próximo ao ponto de injeção (Manrich, 2005 ).
Como necessitam de controle ideal de temperatura e aquecimento do molde para um funcionamento perfeito as resistências elétricas tem sua temperatura controladas por zonas através de controladores específicos.
O manifold é responsável pelo aquecimento de toda a massa de material termoplástico que preenche as cavidades do molde .Os fornecedores de câmara quente adicionam um fator de segurança de 20% no dimensionamento do manifold , porém são comuns erros de dimensionamento devido informação errada do peso da peça a ser injetada.
O sistema de câmara quente consiste de um manifold de distribuição e de bicos de injeção sendo que a necessidade de uma bucha quente fazendo o contato entre o manifold e o bico da máquina injetora depende do design da peça.
Este sistema é utilizado principalmente em moldes de alta produtividade com um grande número de cavidades ou em moldagens de grandes áreas com múltiplos pontos de injeção sobre a superfície do produto . A câmara quente é recomendada em componentes injetados de dimensões elevadas, onde em uma injeção utilizando o canal frio, o material polimérico demoraria muito para preencher completamente a cavidade do molde.
Em muitos casos como o canal frio do sistema de alimentação é muito extenso, há um risco do material polimérico se solidificar antes de adquirir a forma geométrica desejada.
Caso haja a necessidade da produção de um produto em vários tipos de côres o fornecedor da câmara quente deve ser informado para que o sistema seja dimensionado de forma a evitar cantos vivos ou outras restrições que comprometam a limpeza do sistema.
Há produtos nos quais as perdas com canais internos de injeção em um molde tradicional seriam inaceitáveis. Para essa situação, são utilizados moldes com câmaras quentes onde não há canais de injeção e sim, um volume aquecido por resistências que mantém a matéria-prima em estado pastoso para a injeção.
Nesse tipo de ferramenta, os ganhos estão na eliminação do galho, que implica na redução dos custos com as perdas de matéria-prima e na injeção por múltiplos pontos, que por sua vez implica na redução do tempo de ciclo do processo em função de um preenchimento mais rápido.
O controle individual de cada zona de aquecimento do sistema da câmara quente por meio de controladores de temperatura é realmente necessário para a garantia efetiva do processo .Deve-se evitar o sistema de “jampeamento”, pois problemas do processo não poderão ser identificados.
A temperatura do volume interno de matéria-prima no molde é controlada como se estivesse no cilindro pois, dependendo do tamanho da peça, esse volume permanece aquecido dentro do molde, por até duas vezes o tempo do ciclo de produção. Dependendo do tamanho do molde pode-se ter até sete pontos de sensores de temperatura na área de câmara quente do molde.
As regulagens dessas temperaturas podem gerar rejeitos dos mais variados tipos, tais como: mancha, rebarba, falhas de injeção e junção fria. Exemplo: caso o volume interno do molde não seja suficiente para preencher as cavidades, teremos uma parte da peça com material à temperatura da câmara quente e uma outra parte com material à temperatura do cilindro que, caso haja uma diferença de temperaturas, ocorrerão junções frias na peça, ponto no qual essa peça estará frágil e propensa à quebra.
Bico Valvulado
O sistema de câmara quente valvulada permite abertura controlada da entrada de fundido na cavidade. O sistema apresenta uma agulha que é acionada por meio hidráulico ou pneumático e que, quando recuada, permite a passagem do material plástico até a cavidade do molde e quando avançada evita a passagem do material.
A válvula de vedação tem como finalidade vedar o fluxo do material injetado, para que ele não escoe demasiadamente, dando melhor acabamento na peça e desperdiçando menos material.
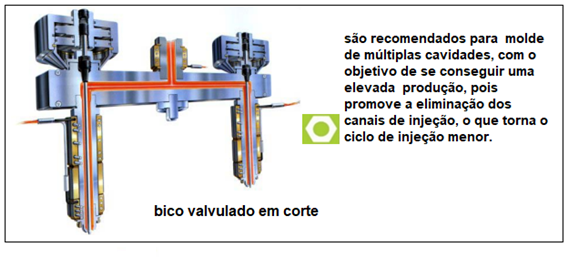
É utilizado para plásticos de engenharia que apresentam uma faixa muito estreita de temperatura de fusão, como o PBT e o náilon. É recomendado também para peças grandes onde o diâmetro do ponto de injeção é razoavelmente grande, evitando a formação de fios. Permite a injeção sequencial de peças grandes como pára-choque de carros.
Para moldes com mais de uma cavidade ou uma cavidade com mais de um ponto de injeção possibilita o controle da evolução da frente de fluxo na cavidade, direcionando linhas de emenda e reduzindo pressões de preenchimento.
Geralmente, é desaconselhada a utilização de bicos valvulados para o processamento de poliacetal . Se o uso de outros tipos de compostos torna necessária a utilização de bicos valvulados, devem ser usadas combinações com sistemas de agulha que garantam as menores perdas de pressão possíveis.
Os sistemas são recomendados em moldes em que há múltiplas cavidades, com o objetivo de se conseguir uma elevada produção, pois promove a eliminação dos canais de injeção, que torna o tempo do ciclo de injeção menor. Para que haja o rendimento esperado e previsto o sistema deve ser fabricado de modo a garantir um balanceamento mecânico que permita um fluxo livre do material sem interrupções sendo que para isso, deve haver comprimentos de fluxo idênticos, mesma quantidade de curvas e mesmo diâmetro de passagem. O dimensionamento tem que ser otimizado para minimizar o tempo de residência e a queda de pressão.
Para evitar a dilatação muito acentuada entre o bloco da câmara quente e o restante do molde é necessário fazer a refrigeração desta parte do molde. Além de evitar a dilatação, o que pode causar problemas no fechamento do molde, a refrigeração serve para corrigir eventuais problemas de aspecto visual da peça, principalmente no ponto de injeção.

É importante para o iniciante entender que o termo refrigeração se aplica ao sistema que gera as condições de se regular para mais ou menos a temperatura dos equipamentos em uso. Essa condição deve ser verificada à parte e envolve fluido refrigerante composto de “água ou óleo”. . Água ou fluidos hidráulicos do molde podem estar muito próximos aos equipamentos e às conexões elétricas. O vazamento de água pode causar um curto circuito elétrico. O vazamento de fluido hidráulico pode causar incêndios. Sempre mantenha as mangueiras de água ou fluidos hidráulicos em boas condições para evitar vazamentos.
Com o sistema de refrigeração bem trabalhado consegue se dar o equilíbrio e normalmente com o fechamento da válvula um bom desprendimento do produto com um mínimo de vestígio. A fim de minimizar as percas de calor com a placa da máquina ,as placa do molde ou do bloco do sistema de câmara quente também conhecido como hot half, geralmente recebe isolação através de placas isolantes tipo Celeron. São chapas de materiais compósitos, com espessura variando de 5 a 10 mm, que minimizam a troca de calor entre molde e placa da máquina.
ACESSE O GUIA DE EMPRESAS PARA SISTEMA DE CÃMARA QUENTE E ACESSÓRIOS
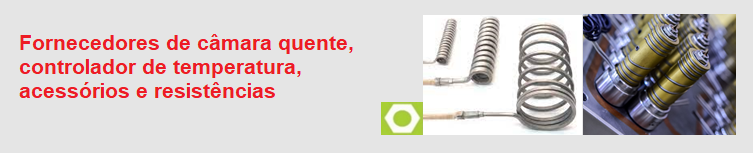
Projetos de acordo com necessidade do cliente.
Acompanhando o desenvolvimento contínuo, as opções para uso de bico quente ou sistemas de câmara quente completos são várias , podendo ser projetado até certo limite, de acordo com as necessidades do projeto do molde .
Em matéria de bico quente” finos e longos”, há grande variedade inclusive bicos especialmente fabricados para processar peças pequenas ou com restrições de perfil em “ hot halfes” ou sistemas de câmara quente, satisfazendo os moldes com multicavidades , como por exemplo os usados nas indústrias de embalagens.
Alguns conjuntos de bicos quente, ditos como família compartilham entre si os mesmos torpedos e configurações de gate, resultando em multiplas opções de gate térmico para ajustarem se ao seu uso.
Para o processamento de plásticos de engenharia há bicos com duas resistências independentes que formam um excelente controle de aquecimento da cabeça do bico ao gate e proporcionam um controle eficaz para este tipo de matéria prima .
Os manifolds tem que possuir um balanceamento correto e natural dos canais de fluidez, fornecendo um preenchimento uniforme das cavidades individuais. Em casos especiais alguns tipos de manifolds conforme exigências são reológicamente balanceadas, possibilitando preenchimento 100% uniforme.
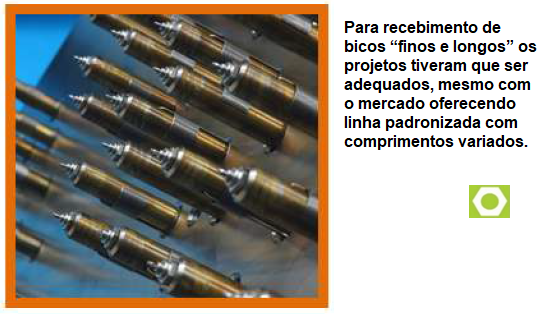
O mercado oferece inúmeras possibilidades em fornecimento de soluções tanto para aplicação com multimateriais e multicores. Os sistemas atendem desde aplicação em simples embalagem plásticas de multicavidades a também componentes avançados como peças estruturais e de engenharia para a indústria automotiva.
Para recebimento de bicos “finos e longos” os projetos tiveram que ser adequados, mesmo com o mercado oferecendo linha padronizada com comprimentos variados. O perfil destes bicos são projetados para que se permita a instalação de cavidades próximas com alojamento eficientemente projetados para melhorar a performance de refrigeração e força do gate.
Normalmente são dotados de características de fluidez que habilitam a moldagem de peças com facilidade.
Para obtenção de uma eficiência máxima é possível se projetar e construir um sistema de câmara quente com stack molde adequando se à aplicação desejada .Quanto aos hot half, são inúmeras as vantagens .Os sistemas são fornecidos prontos para uso sem necessidade de instalação elétrica , montagem ou usinagem adicional e existe a possibilidade de manutenção nos bicos e áreas do gate com o molde montado em máquina .
Algumas precauções devem ser tomadas no uso do bico quente:
• Tipo de material que será injetado.
• Dilatação térmica do bico e do material metálico em contato com o bico.
• Tipo da ponteira.
• Montagem do bico no molde, ajuste sem interferências, pois pode haver vazamento para dentro do bico.
Escolha do sistema:
Vários fatores influenciam na decisão de escolha de um sistema com base em detalhes de projeto do produto e do molde. Várias são as limitações de projeto do molde como , tipo de vestígio ,tipo de resina e ainda os requisitos de qualidade do produto como tolerância, estabilidade dimensional e aparência são decisivos . A utilização de um sistema inadequado de câmara quente causa grandes perdas de pressão. Para ser utilizado nestas condições, este sistema necessitará de altas temperaturas, o que poderá provocar a degradação do polímero,gerando outros problemas.
Para a escolha de um sistema algumas características são importantes como canais com uma seção transversal completa e com elementos de aquecimento simetricamente incorporados são a melhor solução. Sistemas aquecidos internamente, que permitem a circulação do polímero apenas por uma seção anular, causam uma excessiva perda de pressão e devem ser evitados sempre que possível.
No caso de materiais sensíveis termicamente e de compostos com retardantes de chama, deve-se evitar ao máximo quaisquer restrições ao fluxo.A divisão do material fundido em várias frentes de fluxo assim como os canais, com deve ser evitada na região do ponto de injeção.
No caso do processamento de materiais abrasivos, tem se provado vantajoso utilizar pontas de bico intercambiáveis. Além disto, poderão ser alcançados resultados razoáveis com o uso de pequenos torpedos.
A utilização da câmara quente sempre ira aumentar o custo do molde pois, visando a redução no custo de produção com menor tempo de ciclo há uma maior complexidade no projeto , mais gastos com a compra do sistema e equipamento auxiliar e ainda assistência técnica especializada .
O molde deve ser preparado para receber a câmara quente com fixação adequada do mesmo, lembrando se que a adição do sistema de câmara quente necessita de máquinas com maior curso de abertura devido ao maior tamanho de molde. As câmaras sem dúvidas proporcionam um melhor desempenho dos moldes e retorno compensador para os transformadores sendo que a multiplicação de fornecedores tem ajudado na expansão do mercado . Os dados tornam possível calcular o retorno que elas proporcionam na produção dos mais diferentes tipos de produtos.
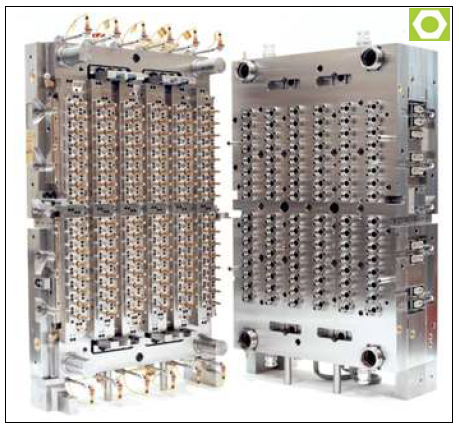
Considerações importantes para a escolha:
Quando se injeta polímeros de engenharia semi-cristalinos em moldes de câmara quente, o sistema utilizado tem grande impacto sobre a funcionalidade do molde e sobre a qualidade da peça. Com estes materiais, o controle da temperatura deve ser mais estreito que com os materiais amorfos. Este artigo aborda os pontos mais importantes que devem ser considerados na escolha da câmara quente mais adequada para POM (poliacetal), PA (poliamida), PBT e PET (poliésteres).
Os polímeros mencionados demonstram uma certa diferença entre a temperatura recomendada do fundido e a sua temperatura de solidificação. Portanto, é necessário isolar termicamente a câmara quente dos canais e dos bicos. O lay-out dos bicos deve ser feito de modo que canais de injeção naturalmente balanceados possam ser usados.
Esta é a única maneira de garantir perdas de pressão uniformes e tempos de residência similares em todas as cavidades. No caso de peças pequenas, recomenda se a utilização de entradas indiretas, especialmente quando se utiliza materiais reforçados com fibras de vidro.
A quantidade de material que passa por cada bico aumenta, facilitando o controle da quantidade de calor transmitida ao composto. As dimensões dos bicos podem ser maiores, permanecendo pequenos os pontos de injeção. Poços frios devem, de qualquer forma, ser arranjados faceando o bico de injeção da câmara quente. Este é o único modo de prevenir que entre material frio na peça.
Controles separados devem ser providos para a entrada da câmara quente, para os canais quentes e para cada bico. Deste modo, se torna possível equilibrar a temperatura de cada cavidade independentemente, no caso da utilização de materiais sensíveis termicamente. Deve se, sempre, utilizar equipamentos de controle que garantam uma temperatura constante (ex.: PID). Os sistemas de câmara quente devem ser suportados mecanicamente, assim como é feito com o sistema de extração.
O molde se torna menos resistente próximo aos canais e, portanto, deve ser reforçado ao máximo. Circuitos de aquecimento separados, dispostos em torno dos bicos da câmara quente permitem um controle mais preciso das temperaturas das cavidades.
A questão de padronização é importante, pois tem influência nos custos. Casos especiais em alguns tipos de sistemas devem ser planejados devido a dificuldade na reposição. A utilização de mais fornecedores de sistemas deve ocorrer, pois gera mais opções na fabricação.
Fonte : Pesquisas: C.Técnico Campinas – Plástico Moderno/ Petropol
Hamilton Nunes da Costa – Editor de Revistas Independente
CFP VW SENAI / Matrizeiro especializado em molde
Escola ART-MEC / Projeto de molde
CFP VW SENAI / Técnico mecânico – CREA 126.785
Manutenção Preventiva de Sistemas de Câmara Quente
Um dos fatores mais importantes para manter um sistema de câmara quente em bom funcionamento é evitar a entrada de impurezas no canal do manifold e nos bicos. A contaminação da matéria prima obstrui os canais e pode entupir os gates, dificultando assim a injeção da peça. Para limitar ao máximo a entrada de impureza na câmara quente recomendamos:
- manter o material de plástico o mais puro possível; e
- utilizar um filtro homogenizador entre cilindro e bico da maquina injetora para filtrar o material fundido antes de entrar na câmara quente.
O objetivo é evitar obstruções no processo de injeção e quando a pressão de injeção começa a subir é chegada a hora de limpar o filtro homogenizador. O filtro deve ser construído para facilitar a limpeza do seu elemento filtrante. Mas em principio a limpeza de um filtro é sempre muito mais eficiente do que desobstruir um gate de um sistema de câmara quente.
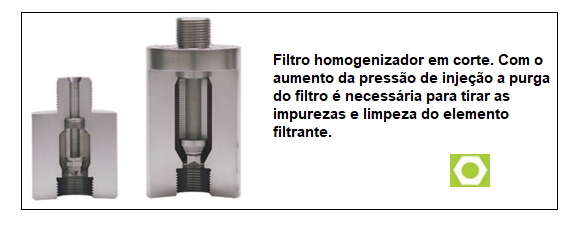
Com o aumento da pressão de injeção a purga do filtro é necessária para tirar as impurezas e limpeza do elemento filtrante. Em caso de processar plástico reforçado com fibra longa, naturalmente a fibra obstrui o filtro mais rápido. Neste caso recomendamos purgar o conjunto cilindro – filtro – câmera quente com material sem fibra antes da parada do molde. Este procedimento deixará cilindro, filtro e câmara quente limpos e facilitará a rotina de iniciar novamente a próxima produção de peças. Caso haja preocupação com a
possibilidade de misturar material com ou sem fibra, recomendamos o uso de uma cor diferente para o material da purga.
A manutenção preventiva deve ser diferenciada da desmontagem completa do sistema. Como regra geral, quanto menos ocorrer a desmontagem de uma câmara quente melhor, já que alguns itens, como, por exemplo, anéis de vedação, necessitam obrigatoriamente ser trocados a cada procedimento de desmontagem. Antes de iniciar uma manutenção preventiva na câmara quente é muito importante ter conhecimento técnico adequado do tipo e da marca em uso. Assim, recomendamos solicitar um treinamento técnico do fabricante do sistema em uso e
aprender o procedimento correto de sua manutenção preventiva.
Os sistemas de câmara quente de alta tecnologia oferecem resistências blindadas com dois filamentos separados em cada resistência de bico. Esta redundância permite uma produção ininterrupta no caso de rompimento de um dos filamentos, possibilitando a troca da resistência somente durante a manutenção programada. A troca periódica de resistências funcionando por resistências novas como parte típica da manutenção preventiva não é necessária por que estas resistências normalmente não falham por idade.
Hoje a maior causa de queima de resistências da câmara quente e o vazamento de plástico, são a infiltração de água da refrigeração no molde e curto-circuito nos cabos da ligação elétrica. A fixação da resistência de sistemas de alta tecnologia atualmente é feita por um anel elástico e a ponta não precisa ser mais desmontada para trocar uma resistência
do bico de injeção. Assim a troca da resistência ficou significativamente mais fácil e rápida e a possibilidade de vazamentos devido a eventuais erros na montagem da
ponta foi eliminada.
A queima de termopares, entretanto é imprevisível e por isso sistemas de alta tecnologia prevêem um segundo termopar na resistência, aumentando assim a redundância da câmara quente. Recomenda-se a troca de termopares em cada manutenção preventiva. Por isso é importante que os termopares sejam montados em separado da resistência, facilitando o acesso e a troca.
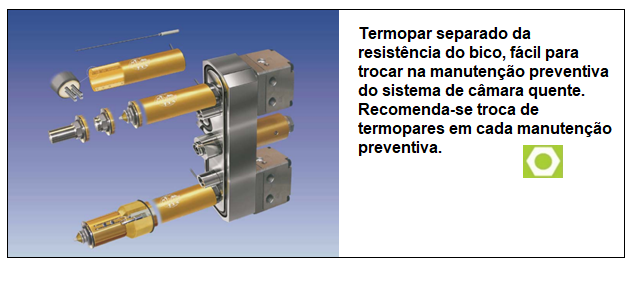
Durante a manutenção preventiva do molde (normalmente duas vezes por ano) recomendamos inspecionar a conexão entre cabos e resistências e cabos e conectores para garantir que a conexão esteja justa e a passagem elétrica esteja isolada, não existindo contato com o molde. Estes são as maiores causas de falhas Além disso o uso de controladores de temperatura com soft-start é altamente recomendado para reduzir a possibilidade de queima das resistências da câmara quente no inicio da produção.
Uma manutenção preventiva das ponteiras e gates da câmara quente é necessária quanto se injeta materiais reforçados com carga. Estes tipos de material são altamente abrasivos e estes componentes da câmara quente sofrem um constante desgaste. Para reduzir este problema novos tipos de ponteiras foram desenvolvidos com uma cobertura para elevar a resistência ao desgaste aumentando a flexibilidade das aplicações. Alem disso os fabricantes de câmara quente normalmente oferecem insertos em aço para a região do gate. Estes insertos podem ser trocados facilmente durante a manutenção do molde no caso de um desgaste excessivo pelo material de injeção abrasivo.
Fonte: Sistemas de câmara quente, manutenção preventiva e recomendações para instalação dos Sistemas
Artigo do Moldes ABM – 10º Encontro da Cadeia de Ferramentas, Moldes e Matrizes. Autores: William dos Santos e Michael Rollmann (www.incoe.com)
Publicado em 05/06/2017 Atualizado em 07/05/2023
REPRODUÇÃO PROIBIDA SEM AUTORIZAÇÃO
Hamilton Nunes da Costa – Editor de Revistas Independente
CFP VW SENAI / Matrizeiro especializado em molde
Escola ART-MEC / Projeto de molde
CFP VW SENAI / Técnico mecânico – CREA 126.785