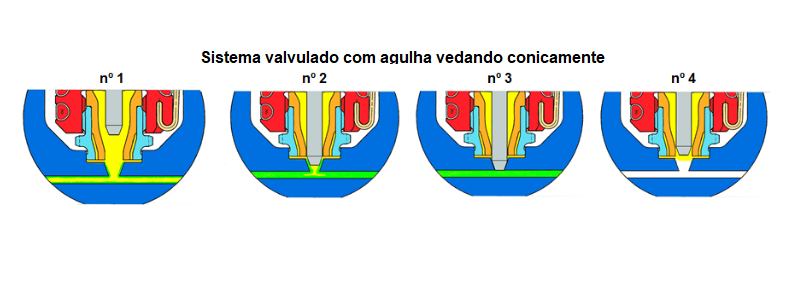
OBS: CUIDADO TEM LIVRARIA OFERECENDO LIVRO COM NOSSO CONTEÚDO
Como controlar o “vestígio” gerado no processo de injeção com câmara quente
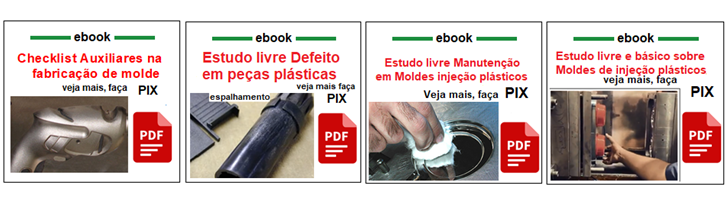
Há uma busca constante para a melhor solução no uso de molde com câmara quente, com objetivo de diminuir e controlar o “vestígio” gerado neste processo.
Sem dúvidas, a melhor alternativa para assegurar um bom controle de injeção em moldes de câmara quente é a utilização de bicos valvulados. Existem sim, algumas alternativas empregadas para abrir e fechar válvulas nos bicos valvulados.
Molde com canais de distribuição quentes : Câmara quente
É um molde mais sofisticado com custo inicial mais elevado, pois possui um sistema de canais de distribuição aquecidos, o que acarreta uma série de vantagens e controles, tais como:
Redução da mão-de-obra;
Redução de matéria-prima;
Redução no consumo de energia;
Utilização de menores pressões de injeção;
Menor tempo de resfriamento;
Menor curso de abertura;
Menor tempo de injeção.
Bicos de injeção convencionais abrem e fecham devido um balanceamento de pressão e temperatura. Alguns problemas no início da produção, como o congelamento ou o gotejamento do ponto de injeção, podem interromper o balanceamento e comprometer os resultados.
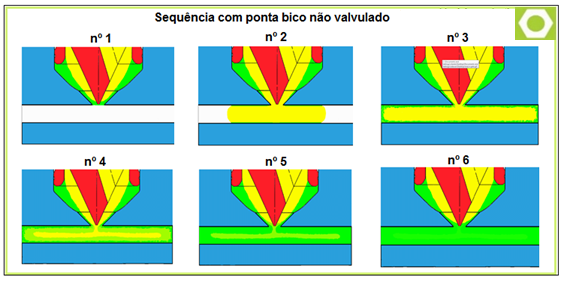
O uso de bicos de injeção valvulados nos sistemas de câmara quente resulta numa significativa melhoria da qualidade do vestígio na peça. Além disso, algumas técnicas de injeção de plástico só podem ser realizadas dessa forma. Sendo assim, o sistema de injeção e o vestígio são os principais responsáveis pelo bom funcionamento do molde e pela qualidade da peça final.
Os pontos de injeção valvulados com pino ou agulha abrindo e fechando, o controle da injeção e a repetibilidade do processo asseguram funcionalidade constante e melhoria da qualidade do injetado. A produtividade aumenta devido à redução de peças defeituosas e do tempo gasto para iniciar a produção.
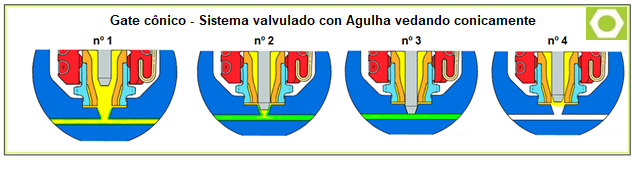
Além disso, o vestígio numa peça injetada deve ser o menos visível possível. Na injeção convencional, dependendo do material e volume injetado, ocorrem alta fricção e tensão no ponto de injeção e a consequente degradação do material. Além disso, o processo pode resultar numa queda alta de pressão. Nos bicos valvulados, o pino fecha o ponto de injeção. Mesmo com um grande diâmetro, o vestígio na peça é quase imperceptível. A fricção e tensão reduzidas no ponto de injeção garantem peças de alta qualidade e livre de tensionamento.
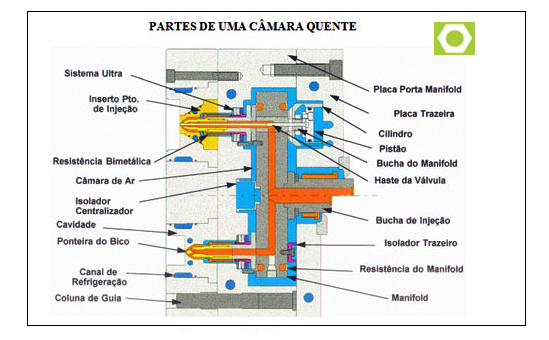
Ciclo menor – Após o preenchimento da cavidade, a peça esta sujeita a uma contração volumétrica, compensada pela pressão de recalque, responsável também por prevenir o retorno do plástico pelo ponto de injeção. Dependendo da peça, o tempo de recalque pode durar dez segundos ou mais. Após essa etapa, a injetora inicia a dosagem para recomeçar a operação. Dessa forma, o tempo de recalque tem grande importância para o ciclo de injeção.
No caso de bicos valvulados, o ponto de injeção pode ser fechado no momento de máxima pressão, permitindo, de acordo com o injetado, redução do tempo de recalque ou até a sua eliminação total. Dessa forma, a dosagem para o próximo ciclo ocorre antes. O sistema também favorece a redução quando o ciclo é definido pelo tempo de dosagem e não de recalque, em virtude da maior vazão de material no gate, com consequente aumento da velocidade de injeção.
Dimensionamento do gate
Depende basicamente dos seguintes fatores:
Fluidez do material (pressão, Taxa e tensão de Cisalhamento)
Espessura do produto (pressão de injeção)
Volume a ser injetado (quantidade de gate)
Temperatura do material fundido (recalque)
Temperatura do molde
Dimensionamento ideal é por Experiência ou Estudo de CAE
Localização do gate
Em local pouco ou nada visível
Mais próximo possível do centro da peça (comprimento de fluxo)
Localizar na parte de maior espessura da peça (recalque)
Evitar localizar nas áreas mais tensionadas ou solicitadas mecanicamente
Existem algumas alternativas empregadas para abrir e fechar válvulas nos bicos valvulados.
Novos processos – Cilindros hidráulicos ou pneumáticos são empregados para abrir e fechar pinos da válvula. A pressão pode derivar diretamente da máquina ou de uma estação de pressão separada. É importante manter a pressão estável, a fim de garantir o funcionamento consistente do pino valvulado, em ambos os casos. A atuação do cilindro é controlada por sensores que monitoram o avanço da rosca da injetora.
Os sistemas de canal ou câmara quente convencionais não controlam individualmente os pontos de injeção. Caso necessitem de maior pressão ou fluxo de volume num dos pontos, o balanceamento é feito por meio de cálculos baseados em parâmetros e geometrias. Durante o try-out, muitas vezes, os valores calculados precisam ser alterados em virtude de mudanças na geometria ou espessura da peça, no material ou nos parâmetros do processo. Nesses casos, a eventual correção do balanceamento do sistema convencional é onerosa e demorada. Com sistemas valvulados, o fluxo por ponto de injeção pode ser controlado com tempos de abertura individuais, facilitando a correção do balanceamento.
Além disso, com o controle individual do fluxo em cada ponto de injeção é possível injetar famílias de peças com pesos diferentes. Os pinos ou agulhas valvulados abrem primeiro nas peças maiores. Em seguida, os pontos das menores são acionados. No final da injeção, todas as pontas estão abertas, e a máquina aplica a pressão de recalque.
Tipos de agulhas
— Agulha para material amorfo
Material amorfo é mais viscoso e menos fluído
Agulha veda por cisalhamento
Vedação não pode ser por esmagamento (empenamento da agulha)
Diâmetro da agulha é o mesmo da saída do material
Material mais amorfo exige mais pressão para ser empurrad
— Agulha para material semicristalino
Material semicristalina é pouco viscoso mais fluído
Agulha veda por esmagamento
Agulha veda conicamente
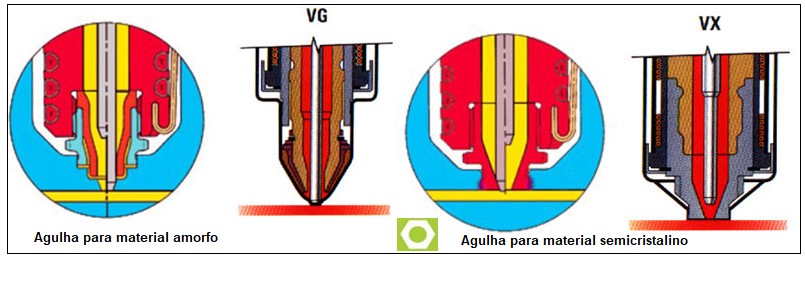
Menos linhas – Na produção de peças com mais de um ponto de injeção, o encontro de frentes de fluxo de material na cavidade formam uma linha de emenda na peça. Dependendo do composto de material, do acabamento superficial ou da cor, a linha de solda fica visível e necessita de tratamento secundário, como pintura, por exemplo. Como, em geral, o encontro das frentes de fluxo do material acontece no final do enchimento da cavidade, quando a pressão de injeção e a temperatura do material já estão reduzidas, não é possível garantir a união homogênea. Sendo assim, a peça injetada pode quebrar com facilidade na linha de solda. Diferentes pressão e distribuição de temperatura podem aumentar as tensões e resultar num maior empenamento da peça na região da linha de união. Usando pontos de injeção valvulados, uma peça longa pode ser preenchida de um lado para outro ou do centro da cavidade para as extremidades abrindo os pontos sucessivamente.
No início da injeção, somente um ponto fica aberto. Os outros pontos se abrem quando o material passa por eles. Com a abertura sequencial dos pontos de injeção, frentes de fluxo de material nunca se encontram, eliminando linhas de solda visíveis. Esse processo também é chamado de injeção sequencial ou em cascata. A peça final tem estrutura uniforme e tensões reduzidas.
Conclusões e recomendações
Recomenda-se, portanto, a utilização de bicos valvulados como alternativa de melhoria do processo de injeção através de moldes com canais de distribuição quentes (moldes de câmara quente). Estes bicos valvulados podem minimizar a presença de vestígio nas peças ou até mesmo eliminar este problema, além de outras vantagens como, por exemplo, produtividade, pois o processo fica mais dinâmico.
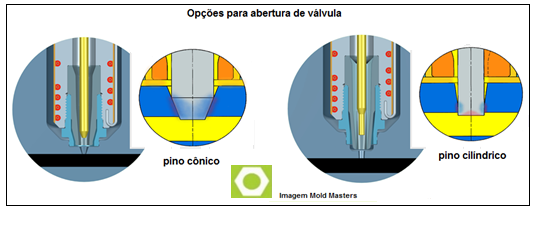
Nossa divulgação:
ACESSE O GUIA DE EMPRESAS PARA SISTEMA DE CÂMARA QUENTE E ACESSÓRIOS
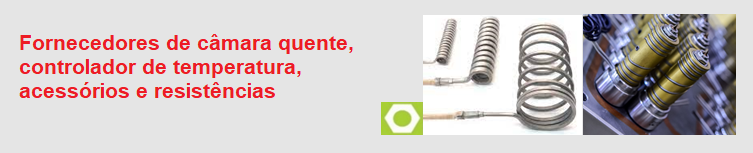
Fontes : SBRT / SOCIESC
—- Como eliminar o ponto de injeção nas peças com câmara quente ?
Publicação Autorizada ao Moldes Injeção Plásticos.
Hamilton Nunes da Costa – Editor independente
CFP VW SENAI / Matrizeiro especializado em molde
Escola ART-MEC / Projeto de molde
CFP VW SENAI / Técnico mecânico – CREA 126.785