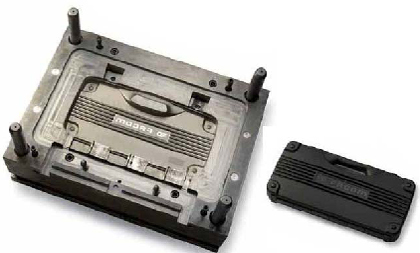
O processo de usinagem por descargas elétricas (EDM)
Da mesma forma que ocorre em muitas outras áreas técnicas, a aplicação tecnológica prática de descargas elétricas como processo de produção aconteceu devido à necessidade do ambiente industrial em solucionar alguns dos seus intrínsecos problemas de fabricação .Em 1943, dois russos, B.R. e N. I. Lazarenko, ao investigarem o desgaste de contatos de interruptores, deduziram que as descargas de centelhas poderiam ser utilizadas para usinar novos metais recém desenvolvidos que provaram ser difíceis de moldar pelos métodos convencionais .
A usinagem por descargas elétricas (EDM), um processo de usinagem não tradicional, tem substituído a furação, a fresagem, a retificação e outras operações de usinagem tradicionais e é agora uma opção de usinagem bem estabelecida em muitas indústrias em todo o mundo .A usinagem por descargas elétricas (EDM) é uma técnica amplamente usada para usinar metais duros e para executar tarefas específicas que não podem ser alcançadas usando técnicas convencionais.
A usinagem por descargas elétricas (EDM) é o processo de remoção de material por descargas elétricas de qualquer peça condutora. Isso é realizado aplicando corrente alternada ou contínua pulsada de alta freqüência à peça, através de um eletrodo ou fio, que funde e vaporiza o material da peça .
Neste processo, não há necessidade de o eletrodo-ferramenta possuir maior dureza do que a peça a ser usinada, como acontece nos processos de usinagem tradicionais. Isso pode reduzir os custos por um lado, mas a confecção da ferramenta geralmente possui custos elevados.
Nas figuras são mostrados alguns exemplos de ferramentas, peça e produto final utilizados em usinagens por descargas elétricas.
Matriz confeccionada por usinagem por descargas elétricas (EDM) com eletrodo-ferramenta de grafite (CATÁLOGO TÉCNICO CHARMILLES).
Peças com geometrias complexas obtidas através do processo usinagem por descargas elétricas (EDM) (CATÁLOGO TÉCNICO CHARMILLES).
Existem várias teorias sobre a usinagem por eletroerosão para explicar a natureza de tudo o que acontece durante a ocorrência das descargas elétricas. Amorim (2002) cita, em sua tese, que a teoria termoelétrica apresenta as melhores evidências explicativas do fenômeno de remoção de material por descargas elétricas. De acordo com esta teoria, o ciclo de uma descarga elétrica entre dois eletrodos submersos num meio líquido de trabalho ocorre em quatro fases consecutivas, a saber:
1. Fase de ignição da faísca:
– O eletrodo se aproxima da peça;
– As duas unidades são energizadas;
– Concentração do campo elétrico na fenda de trabalho (gap);
2. Formação do canal de plasma:
– Criação de um canal ionizado entre o eletrodo e a peça;
3. Fusão e evaporação de uma pequena quantidade de material nos eletrodos:
– Interrupção da centelha;
– Material da peça se funde localmente e se desintegra;
– O eletrodo se desgasta levemente;
4. Ejeção do material fundido:
– Evacuação das partículas metálicas pelo fluxo do dielétrico.
Compreenda a usinagem por descargas elétricas (EDM)
Na máquina de eletroerosão, a ferramenta é avançada em direção à peça, ambos mergulhados num líquido isolante, ou fluido dielétrico como é mais conhecido. A ferramenta é carregada positivamente e a mesa e a peça são negativas (ou vice-versa). Uma série de pulsos voltaicos é aplicada entre os dois eletrodos, que são separados pela fenda de trabalho (gap), numa distância em torno de 0,01 a 0,5 mm.
À medida que o eletrodo-ferramenta, carregado com um potencial de alta voltagem, se aproxima da peça, forma-se um intenso fluxo eletromagnético e, finalmente, rompem-se as propriedades isolantes do fluido dielétrico. O fluido dielétrico é integrado ao processo. Ele fornece isolamento contra descargas prematuras, resfria a área isolada, e remove os detritos . O processo de quebra do dielétrico é um evento localizado: ele ocorre num canal de raio, aproximadamente, 10 µm .Quando os elétrons e os íons positivos alcançam o ânodo e o cátodo, eles liberam sua energia cinética na forma de calor.
Temperaturas de aproximadamente 8000 a 12000º C e fluxos de calor de até 1017 Wm-2 podem ser atingidos. Devido à evaporação do dielétrico, a pressão no canal de plasma sobe rapidamente a valores de até 200 atm. Porém, no final do pulso, quando a voltagem é removida, a pressão também cai repentinamente, e o metal superaquecido é evaporado explosivamente .
À medida que a ação procede, o canal do plasma aumenta de largura, e a densidade da corrente através da fenda de trabalho (gap) intereletrodo diminui. Com a fração da corrente em função da diminuição dos elétrons, as contribuições dos íons positivos aumentam, e proporcionalmente mais metal é então erodido do cátodo. A erosão de metal do cátodo pode ser de até 99,5%, sendo o desgaste do ânodo mantido a 0,5%. Em usinagem por descargas elétricas (EDM), portanto, o eletrodo-catodo é transformado na peça e o ânodo torna-se a ferramenta.
Esquema dos principais elementos construtivos de um equipamento de usinagem por descargas elétricas (EDM) (ARANTES, 2001).
Fluidos dielétricos e sua propriedades.
A conservação do meio ambiente representa para as empresas uma responsabilidade incontestável. Por outro lado, cada vez mais o mercado exige da empresa uma atuação transparente e concreta de preservação e conservação do meio ambiente, a qual se materializa pela realização de atividades que apresentem um mínimo impacto ambiental . Uma das principais fontes de poluição ambiental foi atribuída à indústria manufatureira e os processos de usinagem desempenham um papel importante uma vez que ele é o processo de fabricação mais usado.
A minimização do impacto ambiental tem sido um importante tópico para os fabricantes de todo o mundo, especialmente após a introdução das padronizações de sistemas de gerenciamento ambiental da ISO 14000. Além de maximizar a qualidade e custos, é imperativo para as indústrias de manufatura estarem preocupadas com a minimização do impacto ambiental de seus processos e produtos. A abordagem que tem sido usada para ter uma produção limpa que esteja de acordo com as exigências da ISSO 14000 é identificar e eliminar as origens da poluição
. A indicações de que uma das principais origens de poluição em usinagens por descargas elétricas de matrizes profundas é o fluido dielétrico, particularmente os óleos hidrocarbonetos. No momento, não há nenhum processo de manufatura totalmente limpo que possa substituir a EDM. O uso de gás (ar, oxigênio) em EDM poderia ser uma alternativa porque não produz nenhum resíduo e não causa nenhum efeito adverso à saúde. Porém, esta técnica não está desenvolvida o suficiente para ser empregada eficientemente.
De acordo com a norma NBR 1004 (1987), fluidos dielétricos são considerados resíduos da classe I (perigosos). Segundo esta mesma norma, um fluido será caracterizado como inflamável quando uma amostra for líquida e tiver ponto de fulgor inferior a 60º C. O contato com o fluido dielétrico (pelo ar ou diretamente) pode levar a reações alérgicas (principalmente de pele). Goh et al (1993) citam que os óleos hidrocarbonetos usados em EDM possuem componentes que irritam a pele causando dermatites. Leggat et al (2006) confirmam que os fluidos dielétricos contém agentes que irritam a pele dos operadores de EDM.
A Figura mostra o impacto ambiental resultante do uso de usinagem por descargas elétricas (EDM) de matrizes profundas. Segundo Leão et al (2004), após a usinagem por descargas elétricas existem sedimentos (materiais removidos da peça e da ferramenta), resíduos dielétricos, cartuchos de filtros e resinas deionizadas que necessitam serem descartadas adequadamente para evitar a poluição do solo e rios.
Impacto ambiental resultante do uso da usinagem por descargas elétricas de matriz profunda (LEÃO et al, 2004).
Os fluidos dielétricos, especificamente desenvolvidos para o processo de usinagem por descargas elétricas (EDM) submersa, são produtos hidrocarbonetos altamente refinados (ou sintéticos). Há numerosas características químicas e físicas que podem ser usadas para definir e identificar o desempenho de cada fluido (INTECH EDM, 1996).
Os fluidos dielétricos cumprem uma função extremamente importante com respeito à produtividade, aos custos e à qualidade das peças usinadas. Saúde, segurança e meio ambiente são também aspectos importantes particularmente quando óleo hidrocarboneto é usado . EDM de matrizes profundas geralmente operam com óleo hidrocarboneto, enquanto a fio, micro EDM e furação rápida de furos geralmente trabalham com água deionizada .
As características básicas requeridas para um dielétrico usado em EDM são alta rigidez e rápida recuperação após a descarga, resfriamento rápido efetivo e habilidade de lavagem. McGeough et al (1997) afirmam que as principais qualidades exigidas do fluido dielétrico são: possuir rigidez dielétrica suficientemente alta para permanecer eletricamente não condutor até que a tensão de ruptura seja alcançada; ser capaz de se desionizar rapidamente após a descarga.,
Os fluidos devem remover as partículas erodidas; aumentar a densidade do canal de plasma e esfriar ferramenta e peça. A viscosidade do dielétrico age diretamente sobre os índices da taxa de remoção de material e do desgaste relativo, por causa de sua influência sobre as condições de lavagem e estrangulamento do canal de plasma, bem como sobre a refrigeração dos eletrodos.
Há muita informação na literatura sobre a influência da lavagem dos detritos de EDM na taxa de remoção de material, no desgaste do eletrodo-ferramenta e na precisão dos perfis produzidos, mas há pouca informação da influência na integridade dos componentes usinados por EDM.
Propriedades dos fluidos dielétricos
Para atender às exigências que o processo de usinagem por descargas elétricas (EDM) requer do dielétrico, as características principais destes fluidos são descritas a seguir:
Rigidez Dielétrica: capacidade de isolamento de um dado fluido para EDM. Maior rigidez dielétrica implica menor distância entre ferramenta-peça, com o conseqüente aumento da precisão da usinagem. Alta rigidez dielétrica ajuda a minimizar o arco e é freqüentemente tida c omo indicadora do desempenho do processo EDM.
Tempo de Deionização: este se refere ao tempo para íons e elétrons se recombinarem depois de uma descarga. Quanto menor é o tempo de deionização, menor é o tempo inativo de cada descarga (Toff) necessário entre os pulsos subseqüentes. Esta característica faz com que se evitem curtos-circuitos.
Viscosidade: Viscosidade é uma medida da resistência ao escoamento do fluido.
Menor viscosidade, melhores serão as características de escoamento, particularmente em cavidades profundas, pequenos detalhes, etc., apesar de alta viscosidade poderem proporcionar bom desempenho em alguns tipos de operações de desbaste. Alta viscosidade prejudica a expulsão dos produtos da erosão da interface ferramenta-peça. Para pulsos de pequena energia, é aconselhável uma baixa viscosidade do dielétrico para maior eficiência do processo.
Calor Específico: Quanto maior o calor específico, mais energia térmica pode ser acumulada sem grande aumento na temperatura, o que aumenta o rendimento do processo e a vida do fluido dielétrico. O elevado crescimento da temperatura aumenta a difusão de átomos da peça para o fluido e vice-versa, o que pode causar alterações significativas na estrutura do material usinado, além do aparecimento de uma maior quantidade de microtrincas causadas pelo calor excessivo .
Condutividade Térmica: Quanto maior a condutividade térmica do fluido dielétrico, menor é o tempo necessário para solidificar e refrigerar as gotas de metal expelidas da zona de erosão. Isso reduz a possibilidade de partículas se aderirem ao eletrodo ou se redepositarem na superfície da peça .
Ponto de Ebulição: Quanto maior o ponto de ebulição do dielétrico, este se mantém mais estável em temperaturas elevadas sem perder suas propriedades originais, perdendo frações menores de componentes pela evaporação seletiva das frações mais voláteis.
Ponto de Fulgor: é a menor temperatura na qual um líquido libera vapor ou gás em quantidade suficiente para formar uma mistura inflamável. Por mistura inflamável, para fins de apuração do ponto de fulgor, entenda-se a quantidade de gás ou vapor misturada com o ar atmosférico suficiente para iniciar uma inflamação em contato com uma chama (isto é, a queima abrupta do gás ou vapor), sem que haja a combustão do líquido emitente .
Limite de Fluidez: é um indicador da capacidade que o fluido tem de escoar livremente a baixas temperaturas. A temperatura indicada é a mais baixa na qual o fluido pode escoar.
Odor: Um “odor” pode indicar, muitas vezes, evaporação excessiva do dielétrico, mas pode também indicar a qualidade do local de trabalho para o operador. A maioria dos fluidos de alta qualidade do mercado são desodorizados ou com odor pequeno, mas tolerável .
Cor (Saybolt): A escala de Cor Saybolt é usada para descrever a cor de fluidos
dielétricos para eletroerosão, usando valores numéricos de +30 até –30; com +30, indicando incolor, ou cor de água, e –30, uma cor de limão, um amarelo pálido. (INTECH EDM, 1996).
Estabilidade à Oxidação: A oxidação ocorre quando o oxigênio ataca e degrada o fluido dielétrico. O processo é acelerado pelo calor, luz e reações com metais; e na presença de água, ácidos e contaminantes sólidos. Quanto maior a estabilidade à oxidação do fluido dielétrico, maior será a duração no sistema EDM
Custo: custo é um fator importante em qualquer produto usado por uma empresa. Entretanto, é uma falsa economia tentar economizar dinheiro usando produtos que não foram formulados para serem usados no processo EDM como fluido dielétrico. O risco de baixa expectativa de vida, potencial dano à saúde e baixo desempenho dielétrico são grandes. Por outro lado, alto custo não necessariamente corresponde a um melhor desempenho, ou melhor, qualidade das superfícies usinadas
Perigo à saúde: Um fator muito importante, nos dias atuais, é o perigo à saúde causado por produtos químicos durante seu uso na indústria. Muitos esforços têm sido feitos para minimizar os riscos à saúde, graças à legislação trabalhista mais rigorosa, no Brasil e no mundo, visando proteger sempre a integridade física do operador. Fluidos sintéticos com menores adições de aromáticos e até soluções aquosas são hoje usados para evitar problemas tais como dermatites, problemas respiratórios e até mesmo sérias intoxicações.
Os efeitos à saúde causados por materiais manipulados têm se tornado um assunto de grande importância nos últimos anos. Apesar de todos os fornecedores de fluido EDM recomendarem um grande cuidado no armazenamento e que se evite prolongada exposição aos fluidos, na realidade, muitos operadores de EDM não usam proteções tais como luvas, máscaras e semelhantes .
Fonte: UTILIZAÇÃO DE FLUIDOS DIELÉTRICOS À BASE DE ÓLEOS VEGETAIS NA USINAGEM POR DESCARGAS ELÉTRICAS POR PENETRAÇÃO
Autor :RENATO MONTANDON DE LIMA
Dissertação apresentada ao Programa de Pós-graduação em Engenharia Mecânica da Universidade Federal de Uberlândia, como parte dos requisitos para a obtenção do título de MESTRE EM ENGENHARIA MECÂNICA