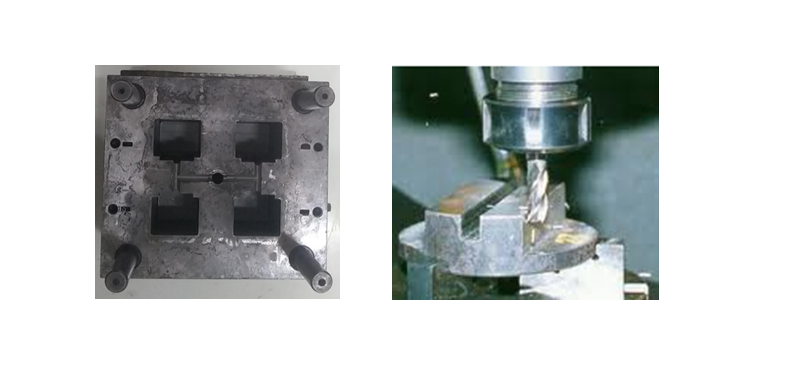
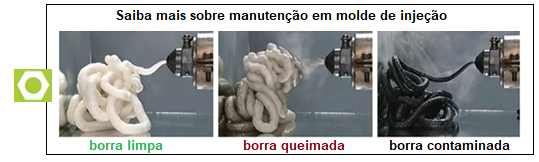
OBS: CUIDADO TEM LIVRARIA VENDENDO LIVRO COM NOSSO CONTEÚDO
Fatores que afetam a qualidade do molde
A ferramentaria fabricante é responsável pela qualidade do ferramental que está diretamente ligada às exigências do produto. Peças de boa qualidade em aparência (visual), peça de boa resistência mecânica e outros, depende muito para qual utilização o produto servirá. É importante sempre atender as exigências do cliente, ficando ciente da produção desejada para que se defina também o tipo de material a ser utilizado na sua fabricação. Em negociações com os clientes deve se conhecer quais as reais necessidades e exigências, para que a qualidade não seja comprometida.
Independente da construção do molde, a utilização em máquina adequada, as condições da máquina injetora e manutenção aplicada ao mesmo, darão ainda elementos para que a qualidade possa ser afetada.
A escolha do material para a fabricação do molde deve levar em consideração o tipo de matéria-prima a ser injetada e a quantidade de peças a serem produzidas, visto que para uma baixa produção, quanto maior o gasto, maior será o preço unitário das peças produzidas.
Do molde mais simples com entrada de material convencional, até o complexo com sistema de câmara quente, alguns itens devem ser observados para manter-se a qualidade necessária. Quanto maior o valor do ferramental, maior acabam sendo também as exigências e os cuidados com o mesmo, e considerar fatores como padronização faz parte deste processo.
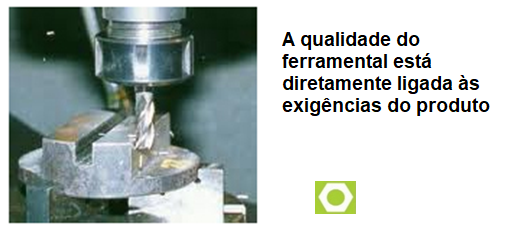
Desgaste nas cavidade.
A corrosão e ferrugem são itens que se tornam visíveis com o uso habitual do molde. O processo de fadiga ocasionado por fibras ou abrasivos da matéria-prima injetada com o processo contínuo de trabalho agridem as superfícies como faces e cantos das cavidades, e por isso, é importante a pré-avaliação para uso do aço correto no momento da fabricação . O uso do aço correto possibilita que receba a dureza apropriada e ainda há de se considerar que o uso de tratamento superficial em vários casos é apropriado para aumentar a vida útil dos componentes, principalmente aqueles que se movimentam e são carentes de lubrificação.
A fixação ou acúmulo de resíduos na face e cantos onde ocorram fechamento, propícia ou facilita a deformação no aço, danificando o ajuste, sendo importante que as saídas de ar (ou gases) sejam rotineiramente escovadas para que a sua função de escape sempre ocorra naturalmente.
Oxidação dos porta-moldes
No caso dos porta moldes, o empenamento nas placas de extração não devem ocorrer mas, às vezes acontecem e tornam- se visíveis, e portanto devem ser avaliados para saber até que ponto está interferindo na qualidade do trabalho. A oxidação aplicada elimina o problema de ferrugem precoce que acontece com os aços de pouca qualidade e o uso de óleo protetivo previne a ferrugem.
Imantação das Peças
O processo de desimantação ou desmagnetização deve ser observado durante a fabricação. Já na fase de acabamento ou durante a manutenção da ferramenta, é importante observar que em muitas máquinas de usinagem o tipo de fixação do componente para usinagem é feito por meio de equipamentos magnéticos auxiliares ou sistemas eletromagnéticos como as mesas de retíficas e se faz necessário desmagnetizar o componente usinado antes da montagem no molde. Esta ação vai eliminar as possibilidades de fixação de elementos ferrosos estranhos, ao processo (cavacos minúsculos ou pós metálicos).
Estes elementos ferrosos estranhos quando fixados no molde, podem vir a danificar áreas de fechamento ou superfícies de acabamento externo do produto injetado. Estas observações são importantes, pois, em alguns equipamentos mais antigos, o processo de desmagnetizar não é automático (mesa de seno, blocos magnéticos permanentes e outros).
Para o operador do equipamento de usinagem essa operação de desmagnetizar já é parte do processo, porém, cabe ao ferramenteiro certificar-se de que o mesmo foi efetuado pois, a responsabilidade é de todos.
O processo de retificação é o de maior influência no sentido de magnetizar as peças. Caso a peça não seja desmagnetizada e entre em processo de eletroerosão, o pó gerado no processo acaba sendo absorvido e interferindo no rendimento da usinagem.
Peças com excesso de imantação podem gerar erros, no momento do zeramento para início de usinagem e ainda, no caso de medições, a imantação pode gerar conflitos nos equipamentos de medição que possuem cabeçote com sistema magnético.
Em casos de peças metálicas e que estejam imantadas, durante a usinagem por máquinas de retíficas coordenadas, caso não se utilize a refrigeração por ar comprimido forçado, as partículas arrancadas tendem a se manter fixadas no interior do furo ou nos detalhes executados.
Necessidade de Ventilação
Em todo molde equipado com sistema de câmara quente a temperatura é controlada para a eficiência do sistema e do processo produtivo. Nesse processamento ocorre a dilatação dos componentes e a transformação da matéria plástica aquecida, sendo a formação de gases inevitável.
A ventilação ajuda a liberar os gases, eventuais sinais de fumaça proveniente de queima, e odores que podem se formar durante a atividade, além de que, o espaço livre em torno do sistema da câmara quente, permite acesso aos componentes, como fiação e outros, facilitando a manutenção.
Pelo tipo de equipamento e montagem do sistema de câmara quente, dificilmente deve ocorrer vazamento de matéria-prima. Caso o sistema esteja trabalhando com excesso de pressão, é então necessário uma revisão do mesmo para que não haja alteração no processo e por consequência alteração no dimensional do produto, tornando o mesmo às vezes sem utilidade.
No uso de sistemas de câmara quente, caso haja necessidade de se trabalhar com a matéria – prima de outra côr, é necessário que o sistema seja desmontado para limpeza. Esta é uma desvantagem em relação aos canais de injeção convencional. Este processo de limpeza deve ser feito por profissional habilitado para a função.
Injeção convencional
Para o sistema de injeção convencional, na maioria dos casos não se faz necessário o polimento da superfície dos canais, pelo contrário, as superfícies não polidas têm a vantagem de reter a película do material frio adjacente às paredes e prevenir a sua liberação para o interior da cavidade.
Quando se utilizar injeção direta ou convencional com buchas, o furo que fecha o canal de injeção deve ser polido, sem marcas para não correr o risco de retenção do canal principal. A conicidade varia de 2º a 5º .
No caso de uma única cavidade, o diâmetro do bico na entrada da cavidade deverá ser aproximadamente o dobro da espessura da peça nesse ponto. Caso o diâmetro seja estreito, pode causar delaminação do material ou calor excessivo na região.
Os canais de alimentação com secção grande apresentam várias vantagens . Êles proporcionam um melhor acabamento da superfície moldada, menor proporção de peças chupadas e redução substancial do ciclo de moldagem.
Quanto mais curto forem os canais, menores serão as chances de solidificação da matéria injetada em seu interior. Em moldes com injeção em várias cavidades, por meio de canal, a distribuição das cavidades dentro do molde deve levar em consideração os diferentes percursos que a matéria-prima pode percorrer, para que todas sejam preenchidas em um mesmo instante
Sistema de Extração
O sistema de extração deve receber tantos pinos quanto possível, sem interferir no sistema da refrigeração devendo extrair de maneira uniforme a peça injetada, de forma suave e sem distorções.
Fatores como os ângulos de saída, polimentos laterais e ainda tempo de recalque e resfriamento, são importantes para o momento da extração possibilitando eliminar o uso de desmoldantes.
Sistema de refrigeração adequada
A eficiência do sistema de refrigeração no molde recebe influência da fase de fabricação pois, as definições de diâmetros dos furos com as distâncias apropriadas para a superfície da cavidade, durante a fabricação devem ser executados corretamente conforme projeto para evitar distorções.
Independente do tipo de circuito e considerando que o projeto esteja de modo adequado quanto à fabricação, é importante observar-se a montagem de jampers pois,” o uso mal posicionado quanto às entradas e saÍdas pode gerar distorções no controle da temperatura”, influenciando na qualidade do processo.
Na montagem do sistema de refrigeração do molde durante a fabricação, a fase de limpeza que antecede a vedação deve merecer especial atenção pois, mesmo com a retirada de cavacos, a fuligem suja de óleo se fixa no interior das furações e caso não haja equipamentos para operação de limpeza e teste, antes do try-out, essa fuligem e o óleo irão contaminar o sistema anexo da injetora.
É importante que esta operação de teste seja feita de maneira que seja possível além da verificação de vazam
Fabricação das Cavidades
Na fabricação das cavidades, o tratamento térmico feito de acordo com especificações do fabricante , já garante o tempo de vida dos componentes que suportarão os esforços e assimilarão o processo de fadiga com maior preparo. A utilização de postiços em pontos críticos como locais ineficientes de refrigeração e saída de gases nos mesmos facilitam o processo.
Durante a fase de projeto, o conjunto de medidas que são importantes e até sem possibilidades alguma de alteração, merecem atenção especial, podendo receber reserva de material para que o acerto dimensional seja feito na fase de try-out.
Para considerar estas reservas é interessante que o profissional técnico de Prova Prática acompanhe, para que elas não sejam exageradas e principalmente para que não faltem. Essa observação é importante pois, o fato de as cavidades não receberem postiços adicionais ou retoques de solda na fabricação para acerto de dimensional, mantém a qualidade do ferramental. A superfície soldada com aquecimento necessário para injeção pode provocar manchas na peça moldada.
No caso de peças injetadas que recebam inserto metálico, a contração do plástico pode chegar até cinco vezes à do metal, sendo necessário prever as folgas que assimilem esta deformação para procurar manter o dimensional do produto.
Equipe Moldes Injeção Plásticos
Não temos patrocinadores. Compre seu Estudo completo que permite cópia se assim desejar, e colabore para que o site continue passando informações, pois muitos necessitam como você. Continuando como está e sem apoio encerraremos nosso trabalho em maio de 2022. Obrigado.