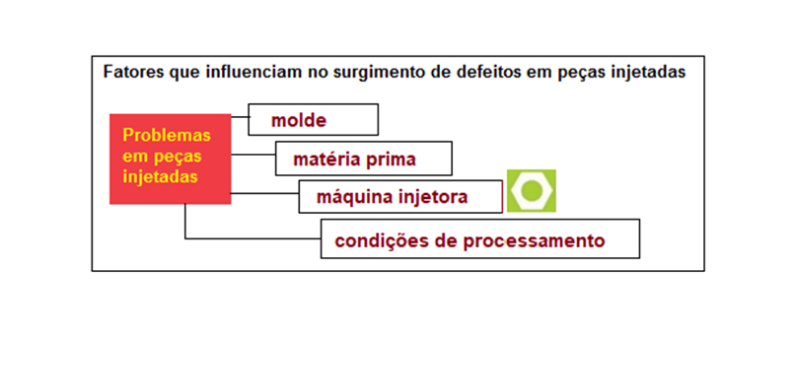

Fatores que influenciam na qualidade de peças plásticas
– Avaliação de defeitos e origem de problemas
– Origem e Resolução dos problemas de moldagem
– Possíveis erros do projeto do molde ou produto
– Geometria da peça injetada
– Variáveis sob o controle do operador
A Série Defeito Zero em peças plásticas procura abordarsobreas técnicas para a perfeita regulagem dos parâmetros na injeção de termoplásticos, buscando identificar e solucionar os principais defeitos oriundos de processo, matéria-prima, detalhes do produto ou ferramental. As soluções reduzem as perdas decorrentes de anomalias no processo de injeção de termoplásticos e visamos auxiliar os iniciantes da área.
Avaliação de defeitos em peças injetadas de termoplásticos
A obtenção de peças de boa qualidade está diretamente associada a dois importantes fatores técnicos na injeção de termoplásticos: o projeto / construção do molde e o processo de transformação, estando estes dois fatores sujeitos a variáveis de difícil controle.
No projeto / construção do molde, os cálculos relativos ao comportamento do plástico durante o processo de transformação são extremamente complexos. Também é praticamente impossível conseguir a repetição exata no aço das medidas especificadas no projeto devido ao desgaste das ferramentas de usinagem e das partes mecânicas das máquinas operatrizes.
No processo, a obtenção dos parâmetros de injeção especificados no projeto sofre variações, tanto em relação às características da resina injetada, quanto nas condições de controle de temperaturas, pressões, velocidades, tempos e todos os outros parâmetros de controle. Desse fato resulta que frequentemente nos primeiros testes de um molde existem correções que devem ser procedidas.
Após o teste inicial as cotas são controladas relativamente ao desenho de produto, e então são efetuadas as devidas alterações. Entretanto, todo teste de molde deve ser realizado com critério, seguindo uma sequência de ações que permitam obter o máximo de aproximação com os requisitos projetados.
Com o intuito de auxiliar na resolução de problemas durante os testes de injeção de materiais termoplásticos, apresentamos defeitos encontrados em peças injetadas, relacionando alternativas possíveis para ações que devem ser tomadas para minimizar ou eliminar tais defeitos, que podem ter origem no projeto, no processo ou em ambos.
Para procedimento correto, é importante uma ficha técnica acompanhar todos os testes até a aprovação final do molde.
Devido às variações que pode haver entre as resinas de diferentes fabricantes, é altamente recomendado que, ao definir a matéria-prima, seja solicitada a ficha de especificação do material ao fabricante.
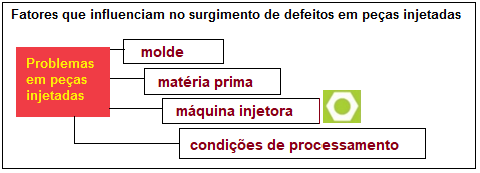
Existem ainda outros fatores que podem afetar o desempenho do processo e consequentemente a qualidade da peça injetada. O mais significativo é o sistema de refrigeração do molde.
Mesmo que apresentadas as possíveis ações para este fator, implicam em alterações significativas da ferramenta sendo, geralmente necessárias revisões completas no projeto original. Todos os tipos de problemas resultantes durante a moldagem por injeção, são gerados por fatores diversos que para a solução, acabam de certa forma exigindo também diversas ações que quando coordenadas, contribuem na eliminação e base para a solução dos problemas.
No projeto, o uso de software de simulação permite o acompanhamento das fases, sendo que os dados utilizados devem ser confiáveis. Para a eliminação de problemas típicos nas peças plásticas é importantíssimo que seja correta a maneira como se analise ou se faça a interpretação dos resultados encontrados na simulação.
Itens como preenchimento da cavidade, refrigeração e empenamento devem ser analisados de forma a validar a geometria da peça à injetabilidade, definição de número de pontos de injeção, lay-out das cavidades, minimizar diferenças de temperatura e determinar formato inicial da peça e magnetude das deflexões a fim de inibir o empenamento.
Desde que se trabalhe com dados e parâmetros reais à matéria-prima em estudo, o resultado trará por si só a eliminação de muitos problemas nas peças plásticas já que, a análise final estará o mais próximo da correta. Alguns materiais necessitam de critérios técnicos para utilização e portanto, as condições de injeção devem ser também analisadas.
A resolução de quaisquer problemas no processo ou defeitos nas peças moldadas requer um bom conhecimento sobre polímeros, equipamentos de processamento e um entendimento claro do processo de injeção.
Não somente conhecimento e experiência são requeridos para a resolução de problemas de moldagem, mas também tempo e paciência. Para eliminar um defeito numa peça moldada, um plano deve ser traçado e executado passo-a-passo, um passo de cada vez. A abordagem deve ser sistemática, lógica e organizada, Uma abordagem desorganizada pode levar a um gasto de tempo bem maior, para resolver o mesmo problema.
Todos os passos devem ser registrados pois, não se sabe depois de quanto tempo (meses ou anos) o mesmo problema pode aparecer novamente. Todo transformador de plásticos deve guardar registros dos problemas que ele encontrou e como ele os resolveu. Se ele compilar esta informação, ele não vai depender de adivinhação ou de experimentações, para tentar resolver os problemas.
Origem e Resolução dos problemas de moldagem
O sucesso na moldagem por injeção acontece quando se produzem peças plásticas de boa qualidade, em uma produção de ritmo contínuo. Mas, podem ser encontrados problemas ao se trabalhar, mesmo de modo contínuo com qualquer termoplástico. Isto ocorre principalmente quando se inicia o trabalho com um novo molde.
Mas os problemas também podem ocorrer quando se muda um molde de uma máquina para outra, ou quando se passa a utilizar um material plástico diferente.
Os defeitos que aparecem em peças injetadas podem ser originados por condições de máquina não adequada, de um molde não satisfatório ou de um material plástico impróprio.
Os três fatores máquina, molde e material tem que ser considerados quando se trata de eliminar defeitos e se obter ótimas condições de moldagem. Normalmente tende-se a responsabilizar os problemas ao material ou às condições de moldagem, quando, na realidade, a origem do inconveniente é a própria máquina não adequada ou o desenho do molde.
Relacionamos os dez defeitos mais comuns na moldagem por injeção: dentro de nossas possibilidades incluímos na segunda parte causas e procedimentos de ajuste.
- Injetadas curtas
- Falta de brilho
- Zonas queimadas
- Depressões superficiais ou bolhas
- Linhas de união fracas
- Aderências no galho ou cavidades
- Manchas pretas, prateadas, poros
- Rebarbas
- Frestas negras ou cor degradada
- Torção ou contração excessiva
Por exemplo, para injetada curta como defeito
Injetadas curtas: se as cavidades não são preenchidas por completo, as possíveis causas podem ser:
— condições do equipamento: Pressão de injeção demasiadamente baixa,
temperatura da massa do material demasiadamente baixa, alimentação insuficiente.
— Molde: Temperatura demasiado baixa, entradas e canais demasiado pequenos, ventilação inadequada, etc.
— Material: A viscosidade do material é muito elevada, os grânulos do material no cone estão demasiado frios ou não são de tamanho uniforme. Geralmente, a solução para cada possível causa é evidente.
No exemplo dado, o primeiro passo é controlar as temperaturas do cilindro para verificar que elas são as corretas para o material empregado. No possível, há que medir a temperatura de massa do material; a mesma se controla através de pirômetro em sucessivas purgas, para se assegurar que o cilindro esteja com o sistema de calefação adequado.
Como segundo passo, deve-se verificar se a pressão de injeção é a correta e também se deve efetuar um ajuste do controle mecânico de alimentação de forma tal que o pistão ou pistão rosca não fique sem material no seu avanço para frente.
Da mesma forma é importante se verificar as outras causas estabelecidas no quesito “A Máquina“. Se ela está operando satisfatoriamente, as condições referentes ao “Molde” e por último, as de “Material“.
O emprego da técnica “passo a passo” para definir a causa de um problema pode ser tarefa fácil, no entanto, a sua correção pode levar muito tempo, em especial se devemos ajustar a temperatura do cilindro. Isto deve ser feito diminuindo ou aumentando de 5ºC a 1OºC de cada vez fazendo uns 10 ou 12 ciclos entre cada
modificação para ir permitindo que a temperatura da massa se equilibre com a do cilindro.
Uma análise sistemática das possíveis causas e a aplicação das correções necessárias proverá as referências ou bases para produzir peças de alta qualidade.
Detecção de defeitos internos como porosidades e trincas.
A Metrotomografia trouxe inovação no controle de qualidade de peças de alta complexidade técnica. Uma das aplicações mais frequentes na área de Metrotomografia®, e que deu origem a esta tecnologia, é a detecção de defeitos internos como porosidades e trincas. Na figura é possível verificar a ocorrência de porosidades nas extremidades de um componente fundido, o que, possivelmente, poderia implicar em fratura do material.
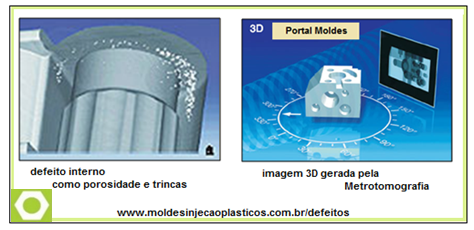
A utilização da tomografia computadorizada em 3D na metrologia industrial possibilita a caracterização de defeitos internos em peças como a existência de porosidades e micro trincas, além da medição interna de componentes que somente seriam avaliados por sistemas ópticos ou apalpadores após a destruição (corte em seção transversal) da peça.
Possíveis erros do projeto do molde ou produto
A – Entrada
de material na peça em lugar errado
Possíveis efeitos: linhas de emenda, linhas de fluidez, jateamento, ar preso no
molde, tensões internas na peça, peça torta, incompleta, espaços vazios dentro
da peça.
B – Entradas
e/ou canais finos demais
Possíveis efeitos: peça incompleta, material muito quente, canal se resfria
antes do tempo, rechupe e espaços vazios dentro da peça, peça torta.
C – Posição
desequilibrada das cavidades em molde de várias cavidades
Possíveis efeitos: pressão desequilibrada no molde, contorção do molde,
diferença dimensional entre peças, peças com rebarba e outras incompletas,
dificuldade na extração e tensões na peça.
D – Sistema
de refrigeração no molde desequilibrado
Possíveis efeitos: ciclo mais longo, contorção e tensões nas peças, contração
maior após injeção, problemas de extração, defeitos na superfície.
E – Falta de
saídas de ar ou saídas de ar insuficientes
Possíveis efeitos: é necessária pressão de injeção mais alta com baixa
velocidade de injeção, material queimado, linhas de fluidez, problemas de
extração, peça incompleta, pequenas bolhas na peça.
F – Sistema
de extração mal projetado e/ou colocação incorreta dos extratores
Possíveis efeitos: problemas de extração, contorção e defeito na peça,
problemas no tempo de ciclo de injeção.
G – Ângulo
interno da bucha de injeção insuficiente
Possíveis efeitos: problemas de extração do canal de injeção, alto desgaste do
molde.
H – Canal da
bucha de injeção muito comprido
Possíveis efeitos: problema de extração, perda de pressão, ciclo mais longo, o
canal se resfria prematuramente.
I – Quina do
canal não arredondada
Possíveis efeitos: sensibilidade a quebras (bolhas e trincas), tensões
internas.
J – Mal
fechamento de machos e outras partes do molde
Possíveis efeitos: problemas de extração, contorção no molde, diferença do
dimensional nas peças, forças desequilibradas no molde, ar preso na cavidade ou
na peça, rebarba nas peças.
K –
Movimentação do molde em função da falta de áreas de travamento
Possíveis efeitos: rebarba nas peças, mudanças dimensionais, problemas de
extração e perda de pressão.
L – Galho
muito fino
Possíveis efeitos: Problemas de extração, perda de pressão, peças incompletas.
M –
Desencontro entre o bico da máquina e a bucha de injeção
Possíveis efeitos: problemas de extração do canal de injeção, vazamento de
material para fora do molde e perda de pressão.
N – Ângulo de
saída das cavidades muito pequeno
Possíveis efeitos: dificuldade de extração das peças, contorção das peças,
mudanças dimensionais.
O – Mudanças drásticas na espessura da parede da peça e cantos vivos
Possíveis efeitos: preenchimento desequilibrado da peça, mudanças dimensionais, ar preso no molde, desgaste do molde e fragilidade das peças.
– Geometria da peça injetada
Na fase inicial do projeto do molde, deve-se realizar uma análise cuidadosa do modelo da peça. O objetivo consiste em antever problemas que podem ocorrer no molde, fazendo uma modificação à peça de forma a eliminar esses problemas. Esta análise permite, também, verificar os mecanismos necessários para a moldagem e extração.
A espessura da parede tem grande influência nas principais características da peça, incluindo o seu desempenho mecânico, aparência estética, plasticidade e economia. A espessura ideal, por vezes, consiste num equilíbrio entre orientações opostas como a resistência vs redução de peso ou a durabilidade vs custo. Devem-se considerar possíveis problemas de moldagem e alterações caras no molde, quando se incrementa a espessura numa peça. Também é importante considerar que quanto maior a espessura da peça, maior o seu volume e o tempo de arrefecimento, conduzindo a maiores tempos de produção, aumento dos custos finais, assim como o aparecimento de defeitos nas peças. No caso de espessuras demasiado finas, a peça possui uma resistência inferior, além de se correr o risco de não haver um preenchimento completo da cavidade.
Uma geometria complexa da peça, por si só, é indicativa de que, se não houver um olhar crítico dos inúmeros pormenores na fase de projeto, poderão ser sentidos fortes problemas de qualidade, tais como defeitos de preenchimento do molde e deformação da peça durante a solidificação, entre outros. A própria geometria implica desde logo o uso de diversas metodologias de abordagem ao projeto, permitindo assim que a forma exigida pelo cliente possa ser efetivamente cumprida.
Uso de desmoldantes: entre os aditivos que podem acumular mais resultados prejudiciais, devemos destacar os desmoldantes, pois seu uso abusivo pode criar sérios problemas de adesão (impressão, pintado, hot stamping).
O estearato de zinco é um dos desmoldantes mais comuns e, se não for utilizado em proporções excessivas pode ser eliminado com facilidade. Pelo contrário, a utilização de silicones deveria minimizar-se ao máximo, pois a sua eliminação é muito difícil e é suficiente a simples presença de traçados insignificantes para criar graves complicações, não tão somente desde ponto de vista da adesão, senão também dos defeitos superficiais que podem gerar.
– Variáveis sob o controle do operador
Muitas variáveis podem ser controladas, a depender das habilidades e conhecimentos que os operadores e supervisores possuam sobre o processo de injeção. Estas variáveis são as temperaturas, pressões, tempos e velocidades. As variáveis devem ser verificadas e corrigidas uma de cada vez, até que a solução ideal seja encontrada.
Manutenção da máquina, conservação das instalações e manutenção do molde também podem ser considerados desde que haja preparo do funcionário.
A Velocidade de Injeção corresponde à velocidade de avanço do parafuso injetor a frente, no momento da injeção do material para dentro da cavidade do molde (fase de preenchimento). Máquinas modernas permitem ajuste diferente de velocidade ao longo do trajeto do parafuso;
A velocidade deve ser ajustada para a máxima possível, consideradas a qualidade do produto e o menor tempo de ciclo. O uso de perfis de injeção deve ser considerado para manter constante a velocidade da frente de fluxo na cavidade e constante as características finais do produto.
Velocidades baixas no início da injeção evitam o jateamento do polímero logo após a entrada e manchas em torno da mesma.
Velocidades baixas ao
final do preenchimento podem evitar excesso de pressão na cavidade e
marcas de queima por gases aprisionados.
Posição de passagem para recalque.
Corresponde à posição
ao longo do trajeto do parafuso injetor em que a máquina injetora passa do
controle de velocidade de avanço do parafuso injetor para o controle da pressão
aplicada pelo mesmo sobre o polímero fundido.
Tem influência direta sobre a eficácia da aplicação do recalque.
Associada ao ajuste da pressão de recalque pode evitar excesso de pressão
interna à cavidade;
Deve ser ajustada um pouco antes do completo preenchimento das cavidades para levar em consideração a inércia do parafuso injetor.
Pressão e tempo de recalque.
Corresponde aos valores de pressão aplicados ao polímero fundido por um tempo determinado, contado após o alcance da posição de passagem para recalque.
Máquinas modernas permitem ajuste de diferentes pressões ao longo do tempo de aplicação de recalque. A aplicação do recalque é justificada até o completo congelamento das entradas das cavidades. Manter a aplicação de pressão após este momento só recalcaria o sistema de alimentação (canais). O uso de perfis de recalque deve ser considerado para procurar compactar de forma uniforme toda a extensão do produto e minimizar problemas de empenamento.
Publicado em 16/10/2021
Fonte: Moldes Injeção Plásticos
REPRODUÇÃO PROIBIDA EM AUTORIZAÇÃO
Hamilton Nunes da Costa – Editor de Revistas Independente
CFP VW SENAI / Matrizeiro especializado em molde
Projeto de moldes / Escola ART-MEC
Técnico mecânico CREA 126.785 / CFP VW SENAI
Este site é um Informativo. Precisamos de suporte para custear Atualizações e Melhorias, assim, divulgaremos sua empresa como apoiadora. Faça cadastro no Guia de empresas ou utilize banners.