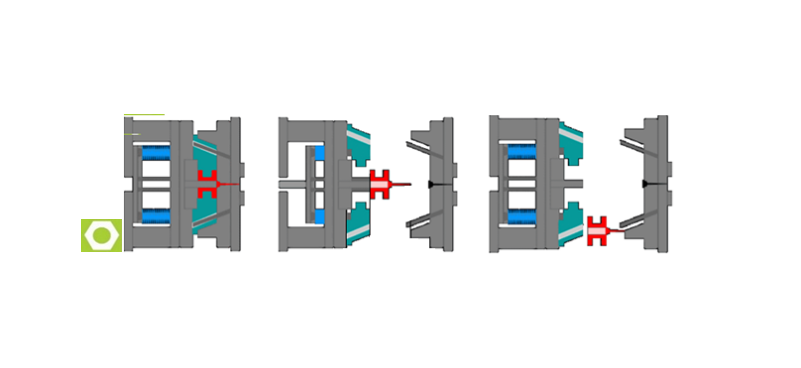

Ajuste da máquina injetora
– Ajustes inicias de fatores que interferem no processo
– Procedimentos básicos em ajustes iniciais
A Série Defeito Zero em peças plásticas procura abordarsobreas técnicas para a perfeita regulagem dos parâmetros na injeção de termoplásticos, buscando identificar e solucionar os principais defeitos oriundos de processo, matéria-prima, detalhes do produto ou ferramental. As soluções reduzem as perdas decorrentes de anomalias no processo de injeção de termoplásticos e visamos auxiliar os iniciantes da área.
Ajustes inicias de fatores que interferem no processo
Temperatura do fundido
Um dos mais importantes parâmetros no ajuste do processo; Valores muito baixos podem não permitir a completa fusão do material e valores muito altos podem levar o material à degradação.
A temperatura do fundido é ajustada através da temperatura de diferentes zonas de aquecimento ao longo do cilindro de plastificação (de 3 a 5 zonas).

A temperatura do bico de injeção deve ser igual a do polímero fundido e têm a função de manter uniforme este valor.
Temperaturas elevadas no bico de injeção podem facilmente degradar o material e
provocar mudança de cores, principalmente em resinas de PA (poliamida).
Usualmente, a temperatura do polímero fundido é sempre maior que a temperatura ajustada nas diferentes zonas do cilindro de plastificação. Este efeito é causado pelo aquecimento proveniente do atrito entre o parafuso injetor e o cilindro.
É possível medir a temperatura do polímero fundido com um termômetro e uma sonda de imersão ou um termômetro infravermelho, afastando o bico de injeção do molde e injetando o material fora do molde.
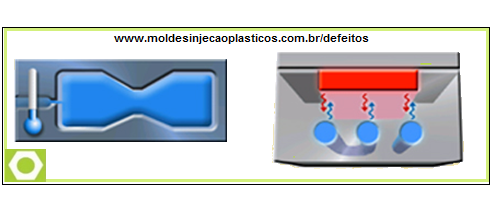
A temperatura do molde de injeção pode ser controlada com o ajuste da temperatura do fluido de refrigeração utilizado. Via de regra, procura-se ajustar a temperatura do fluido da refrigeração de 15 a 30° C abaixo da desejada na superfície do molde. A temperatura a se ajustar para o molde varia de acordo com a resina que será injetada e é indicada pelo fabricante.
É sempre desejável possuir temperaturas uniformes ao longo da superfície do molde, o que depende principalmente do projeto do sistema de refrigeração do mesmo. Variações de temperatura podem causar brilhos diferenciados e influenciar no preenchimento do produto
A temperatura ajustada a o fluido de refrigeração, associada ao tempo de resfriamento determina a temperatura da superfície do molde no momento da injeção. A dinâmica de ajuste destes parâmetros permite otimizar o tempo de ciclo na fabricação do produto.
Temperatura do molde
Machos profundos tendem a concentrar o calor.
Em moldes com machos profundos, sugere-se o uso de temperaturas diferenciadas para o fluido de refrigeração entre o lado móvel (dos machos) e fixo do molde. Isso permite reduzir a diferença de temperatura ao longo da espessura do produto e minimizar problemas de empenamento.
O uso de temperaturas diferenciadas entre os lados do molde deve ser criterioso e levar em consideração a dilatação diferenciada das partes do molde. Este efeito pode chegar a travar o molde fechado, especialmente em moldes maiores.
Tabela com: temperatura de injeção / pressão de injeção / temperatura do molde para alguns materiais.
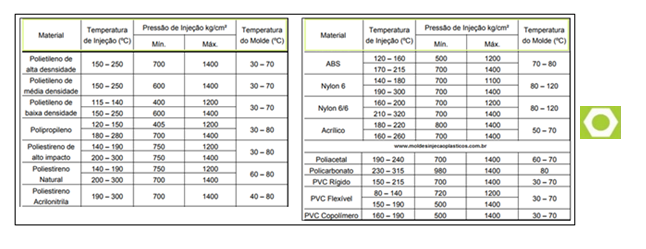
Veja tabelas http://moldesinjecaoplasticos.com.br/tabelas-com-valores-para-aplicacoes-de-termoplasticos/
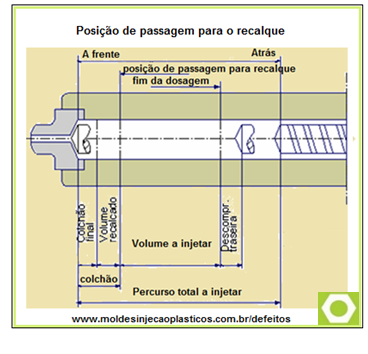
Ajuste da contrapressão de dosagem
A contrapressão é normalmente ajustada entre 5 e 10 bar de pressão hidráulica e tem grande contribuição no aumento do atrito e determinação da temperatura do polímero fundido.
Resinas misturadas a pigmentos no funil da máquina exigem maiores contrapressões para melhorar homogenização.
O volume dosado é maior com maior contrapressão. A contrapressão, para grandes comprimentos de dosagem pode comprometer o tempo de ciclo.
Maiores contrapressões permitem maior precisão na quantidade de material carregada a frente do parafuso ciclo a ciclo mas acelera o desgaste do parafuso plastificador.
Ajuste do limite de pressão de injeção
As máquinas injetoras permitem o ajuste do “limite” de pressão aplicado sobre o polímero fundido na etapa de preenchimento. Sugere-se ajustar esse limite ao máximo permitido pela máquina, para que não haja limitação, pela válvula de controle de pressão, às vazões possíveis de serem aplicadas e à velocidade de avanço do parafuso injetor.
Estando ajustada a posição de passagem para recalque para antes do completo preenchimento da cavidade, é possível prevenir excesso de pressão interna à cavidade, já que o limite de pressão é ajustado ao máximo.
As máquinas permitem ajustes de tempos de segurança onde, quando o parafuso injetor não alcança a posição de passagem até o tempo de segurança, o controle é comutado de velocidade para pressão automaticamente.
Ajuste inicial da pressão e tempo de recalque
Ao iniciar a máquina, deve-se ajustar tempo e pressão de recalque para ZERO para prevenir excessos de pressão ao molde e permitir definir o ponto ideal de passagem para recalque.
Dessa forma, ao atingir a posição de passagem para recalque, o movimento a frente do parafuso é interrompido e iniciada a rotação do mesmo para realizar a dosagem.
Ao iniciar a regulagem do processo procure ajustar uma posição de passagem maior de forma a garantir a injeção de 2/3 do volume da cavidade.
Reduza gradativamente a posição de passagem até ter a cavidade aproximadamente 95% preenchida. Normalmente, o colchão é ajustado para 10% do comprimento total de dosagem (fim da dosagem).
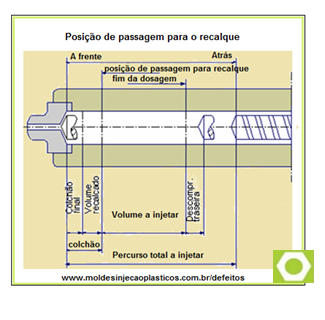
Ajuste da velocidade de injeção.
Inicialmente, ajuste a velocidade de injeção para a máxima disponível. Dessa forma pode-se alcançar a mínima resistência ao fluxo e maior qualidade na formação das linhas de emenda;
Para baixo tempo de preenchimento deve-se garantir a perfeita ventilação do molde com saídas de gases eficientes.
Perfis de injeção devem ser utilizados, para evitar defeitos superficiais causados por elevadas taxas de cisalhamento e marcas de queima por efeito diesel (ar aprisionado).
Os menores tempos de injeção são sempre desejáveis pois permitem os menores tempos de ciclo.
Ajuste dos tempos iniciais de recalque, resfriamento e molde aberto.
O tempo de recalque pode ser ajustado inicialmente para 10x o tempo de preenchimento da cavidade para em uma próxima etapa otimizá-lo;
O resfriamento do material termoplástico para completa solidificação da peça se inicia ao fim do preenchimento e início do recalque. O tempo de resfriamento pode inicialmente ser ajustado para 10x o tempo de preenchimento, e depois ser otimizado.
No ajuste do tempo de resfriamento, deve ser verificado o tempo de dosagem, para garantir que a carga do polímero possa ser realizada antes do termino do tempo de resfriamento e início da abertura do molde.
O tempo de molde aberto corresponde à soma dos tempos de abertura, extração e fechamento do molde e varia com a cinemática do molde, a presença ou não de gavetas entre outros fatores.
O tempo de molde aberto, como todo o ciclo tem influência direta no tempo de residência da resina dentro do cilindro de plastificação, devendo ser minimizado.
Ajuste da abertura do molde
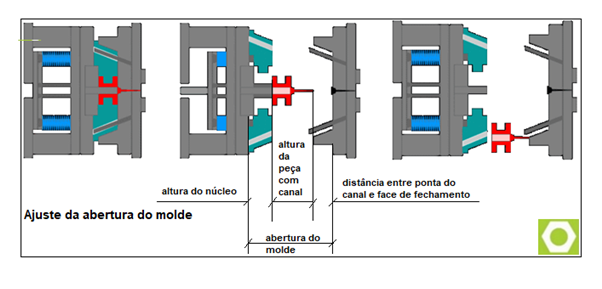
Ajuste a abertura do molde para mínima necessária, verificando espaço necessário para extração do produto. No caso do trabalho em semi-automático, onde a extração da peça é completada pelo operador, preveja espaço para o trabalho eficaz do mesmo.
O ajuste das velocidades de abertura deve ser feito observando a segurança do molde e inércia. Início lentos de abertura e fechamento podem evitar marcas no produto e permitem um funcionamento seguro da máquina.
Ajuste do início, curso e velocidade de extração.
As máquinas dotadas de cilindros hidráulicos de extração permitem o início do movimento dos extratores em uma posição ajustada da placa móvel da máquina. Estando liberadas as gavetas durante a abertura do molde, ajuste o início do movimento de avanço dos extratores procurando fazê-lo simultaneamente com a abertura.
O curso de avanço deve ser ajustado para um valor que garanta a extração do produto verificando o limite mecânico existente no molde. A velocidade de extração pode ser ajustada ao máximo e reduzida gradativamente caso verificam-se marcas indesejáveis no produto.
Cadência e otimização do processo.
Coloque a máquina em cadência para atingir um regime permanente de trabalho. Ajuste um valor mínimo de pressão de recalque e aumente-o gradativamente até que o resultado final no produto seja satisfatório, considerando o dimensional e aspecto visual (rechupes).
Deixe ajustado o mínimo valor possível de pressão de recalque, já que esta é causadora de tensões internas que podem contribuir para o empenamento do produto após a desmoldagem. Esteja certo de que o colchão a frente do parafuso injetor ao término do recalque é diferente de zero para garantir que a compensação de material na cavidade foi a desejada.
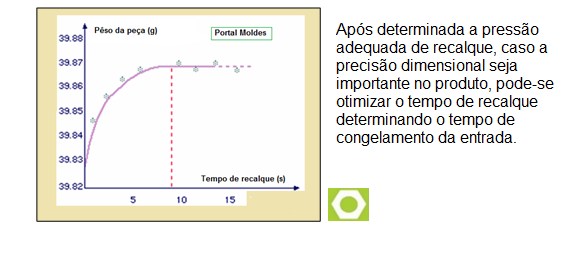
Após determinada a pressão adequada de recalque, caso a precisão dimensional seja importante no produto, pode-se otimizar o tempo de recalque determinando o tempo de congelamento da entrada.
O tempo de congelamento da entrada pode ser estimado pesando-se os produtos injetados sucessivamente, com aumentos graduais do tempo de recalque. Quando os aumentos feitos no tempo de recalque não mais impactam no peso do produto injetado, tem-se determinado o tempo ideal de recalque.
Por último, reduza gradativamente o tempo de resfriamento e temperaturas do fluido de refrigeração, observando para que as temperaturas do produto extraído sejam maiores que a temperatura de deflexão para a resina injetada.
Temperaturas de deflexão para diferentes resinas podem ser obtidas com os respectivos fabricantes.
Procedimentos básicos em ajustes iniciais do processo de injeção
Diminuir as pressões e velocidade de fechamento, abertura, extração injeção e recalque. Movimentar a máquina em manual lembrando‐se de utilizar as regulagens da ficha de processo e otimizar a pressão e velocidade.
Deve‐ se tomar o cuidado de não colocar a pressão de travamento em excesso e colocar proteção de molde a mais baixa possível, para garantir que caso fiquem peças presas, não danificar o molde e ainda obter redução no consumo de energia.
Tabela com fases de regulagem de injeção.
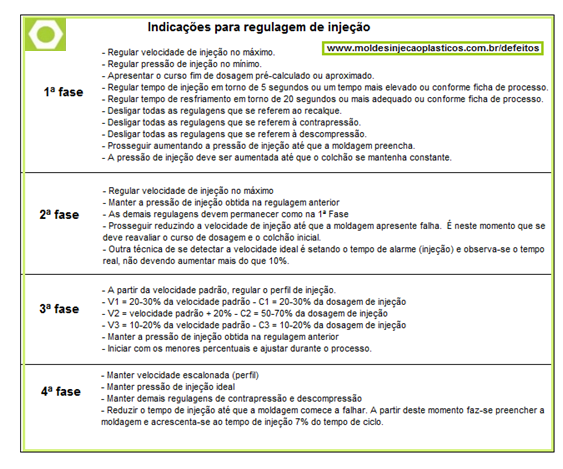
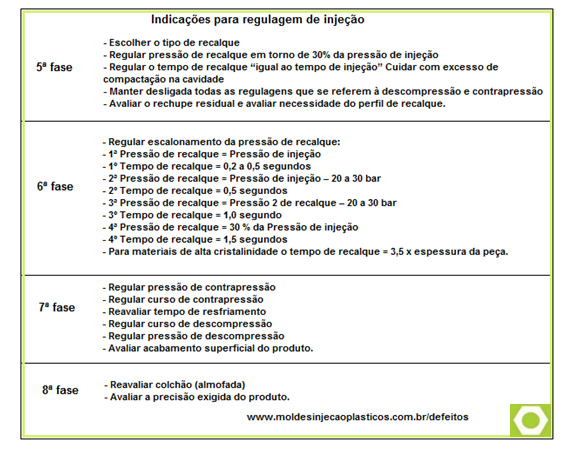
O que é comutação?
A Comutação é a passagem da injeção para o recalque, podemos ter esta passagem controlada por tempo de injeção, por posição de injeção, por pressão de injeção ou por todas elas, para na sequência atuar o recalque.
Tempo e Pressão de Recalque
O Recalque tem a função de eliminar ou minimizar os rechupes e garantir a estabilidade dimensional do produto a ser injetado. Como durante o resfriamento a peça sofre uma contração volumétrica, a finalidade do recalque é compensar essa contração, evitando que a peça apresente “rechupes”. O recalque é o responsável em garantir a precisão do preenchimento do molde.
O ponto ideal para comutar da injeção para o recalque se dá após o preenchimento da cavidade podendo ser feita por tempo, curso, pressão hidráulica ou pressão interna na cavidade do molde. No final do curso de injeção, a quantidade de material que fica à frente da ponta de rosca para o recalque atuar é chamada de almofada.
Para que serve o colchão em injeção de plásticos?
O colchão ou almofada é o material que sobra na ponta da rosca, ele é necessário para que o recalque possa ser eficiente na sua função. A almofada deve conter material suficiente para compactar bem a peça. Peças mal compactadas pode ser resultado de almofada muito baixa. Se na injeção o importante é controlar a velocidade, no recalque é controlar a pressão e o tempo de atuação.
A pressão do recalque deve ser o suficiente para compensar a contração da peça, e valores altos podem provocar tensões na peça, dificultar a desmoldagem e até danificar o molde. O ideal é que se regule no início do processo, com valores ligeiramente mais baixos, aumentando gradativamente até o valor ideal.
Deve-se ter cuidado na regulagem dos parâmetros nesta fase, pois se muito altos forem os parâmetros nesta fase, poderão surgir problemas como: rebarbas no produto, dificuldade de extração, tensões e outros; por outro lado se baixos demais forem os parâmetros, poderá surgir rechupes e variações no dimensional do produto. Aqui como na fase de injeção, esta depende da complexidade do produto a ser injetado, por isso não se pode calcular diretamente, e sim estimar. Sendo que é aconselhável que seja de 40% a 80% da pressão de injeção, e se possível escalonado.
Nas injetoras modernas é possível escalonar os valores de pressão de recalque de tal modo que, conforme a peça solidifica no interior do molde, a pressão de recalque vai diminuindo. Este escalonamento evita que haja uma compactação excessiva e também diminui os efeitos de tensão na peça. O tempo de recalque está diretamente relacionado com a espessura da parede da peça, e deve ser suficiente para o canal de injeção ou a peça solidificar (depende do que ocorrer primeiro). Um modo de encontrar o tempo ideal de recalque é através da pesagem de peças acabadas: quando não houver alteração no peso significa que o canal ou a peça solidificou. Um erro bastante comum é continuar recalcando quando o canal de injeção já está solidificado. Neste caso o recalque não está mais atuando e a injetora, desperdiçando energia e prolongando o ciclo.
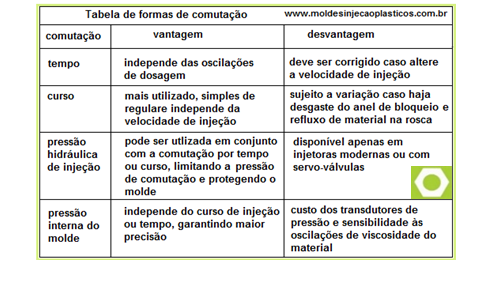
Publicado em 16/10/2021
REPRODUÇÃO PROIBIDA SEM AUTORIZAÇÃO
Hamilton Nunes da Costa – Editor de Revistas Independente
CFP VW SENAI / Matrizeiro especializado em molde
Projeto de moldes / Escola ART-MEC
Técnico mecânico CREA 126.785 / CFP VW SENAI
Este site é um Informativo. Precisamos de suporte para custear Atualizações e Melhorias. Faça cadastro no Guia de empresas ou utilize banners. De apoio a nosso trabalho e divulgaremos sua empresa como apoiadora.
This site is a newsletter. We are in Brazil and we need support to pay for Updates and Improvements.
We will announce your company as a supporter here, contact us by email to provide financial support for our work.
contato@moldesinjecaoplasticos.com.br
Injection machine adjustment
- Initial adjustments of factors that interfere in the process
- Basic procedures in initial adjustments
The Zero Defect Series in plastic parts seeks to address the techniques for the perfect adjustment of parameters in the injection of thermoplastics, seeking to identify and solve the main defects arising from process, raw material, product details or tooling. The solutions reduce losses resulting from anomalies in the thermoplastic injection process and we aim to help beginners in the area.
Initial adjustments of factors that interfere with the process
Melt temperature
One of the most important parameters in the process adjustment; Too low values may not allow complete melting of the material and too high values may lead to material degradation.
The melt temperature is adjusted through the temperature of different heating zones along the plastification cylinder (3 to 5 zones).
We wish you good reading (text can be translated by Google Translate)