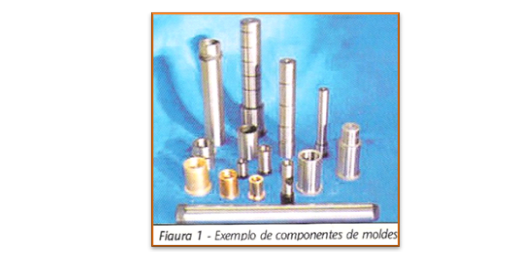
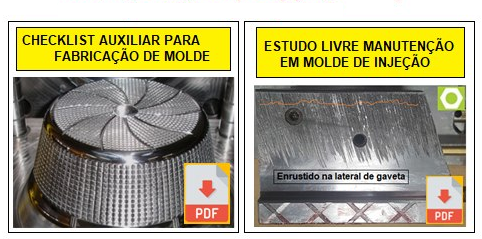
Por: Piter Alves de Sousa – Bruno Otávio de Castro Cardoso – Carlos Humberto Sartori – Lintha da Costa Battisti
Oxinitrocarbonetação aplicada a componentes de moldes e matrizes.
O processo de oxinitrocarbonetação apresenta resultados satisfatórios na prevenção de ataques químicos a superfície de componentes e ferramentas, através da associação de dois tratamentos: nitrocarbonetação seguida de oxidação.
Como alternativa ao processo corriqueiro realizado em banhos de sais fundidos, que exige uma série de cuidados quanto ao meio ambiente, é possível aplicar o processo realizado em sua totalidade em gás, uma vez que é estável, não poluente e economicamente viável para aplicação em componentes de moldes e matrizes, sendo possível obter elevada resistência ao ataque químico.
O desenvolvimento de novos materiais exige uma evolução nas características das ferramentas utilizadas em seu processamento, elevando sua performance e proporcionando sustentabilidade dos processos de fabricação. Dentro das possibilidades de melhoria na fabricação de um ferramental, as principais estão relacionadas com modificações de propriedades do aço a partir do qual o ferramental é obtido, sendo realização de tratamentos térmicos específicos ou ainda de processos associados à engenharia de superfície.
Entre os mecanismos de falha de ferramentas e seus componentes, a corrosão desponta como um dos fenômenos responsáveis por baixo rendimento, sendo retardada apenas pela aplicação de tratamentos superficiais. A oxinitrocarbonetação aparece como uma interessante alternativa, aliando as características da nitretação à oxidação, na prevenção da corrosão em componentes de moldes e de matrizes.
A aplicação da nitretação em buchas, colunas e pinos de extração (figura 1 ) como substituição a cementação, surgiu como uma interessante alternativa, refletindo em aumento de rendimento e economia com processos de usinagem. Enquanto a utilização da cementação envolve a necessidade de sobremetal para compensação das deformações resultantes do processo de têmpera, a nitretação é aplicada às peças já acabadas, sendo um processo a baixa temperatura, sem alteração da microestrutura do material e, conseqüentemente, sem deformação. O processo ainda implica na redução do lead time da fabricação dos componentes, assim como nos custos de logística, tendo a nitretação como a última operação.
A oxidação posterior à nitretação começou a ser empregada apenas com finalidade estética, em 1976. Entretanto, em 1982, estudos demonstraram que a camada oxidada composta por Fe3O4 aumentava a resistência à corrosão dos materiais tratados, sendo empregado em um primeiro momento na indústria automobilística.
A figura 2 apresenta uma análise do efeito da oxidação após a nitrocarbonetação na resistência à corrosão, em ensaio conforme norma ASTM B117. Observa-se que, para o mesmo tempo de exposição ao meio salino, a camada composta pela nitrocarbonetação seguida de oxidação apresenta um ganho considerável quanto ao surgimento de pontos de corrosão.
A nitrocarbonetação envolve a adição conjunta de nitrogênio (90-95%) e carbono (5-10%), tendo como objetivo a formação de uma camada branca com elevada resistência ao desgaste, composta por nitretos, carbonetos e carbonitretos, dependendo do material. Sua composição é função dos elementos de liga do aço e da composição do meio usado para transferência de carbono e nitrogênio.
As camadas produzidas por nitrocarbonetação e posterior oxidação geralmente consistem de três zonas:
– A transição para o substrato é constituída pela camada de difusão com espessura 0,1 a 1,0mm. A presença de (carbo)nitretos precipitados e nitrogênio intersticialmente dissolvido aumentam a dureza e resistência à fadiga do material nessa região;
– A camada de compostos geralmente com espessura entre 5 a 30 µm, consiste de (carbo)nitretos eε e γ;
– A camada mais externa é a camada de óxidos (0,5 a 3 µm) e a composição química é FeO4 (magnetita).
A camada de compostos apresenta elevada dureza e garante boa resistência ao desgaste, especialmente se constituída de nitretos ε. A camada de óxido pode funcionar como uma camada passiva sobre a camada de compostos desde que não existam micro-trincas, penetração do meio corrosivo pela camada ou dissolução da mesma no meio de atuação.
Para obtenção de boa adesão da camada de óxidos é importante que na mesma não existam tensões de tração (para evitar micro-trincas), mas que as tensões compressivas da mesma sejam limitadas (para evitar flambagem). Um bom controle dessas tensões pode ser obtido através do parâmetro Pilling-Bedworth (PB) que avalia a relação entre os volumes específicos por átomo metálico de óxido e substrato no caso do crescimento por difusão de ânion no oxigênio. Para valores de PB menores que 1 temos tensões de tração na camada de óxido e para valores de PB maiores que 1 temos tensões compressivas na camada de óxido.
A tabela 1 mostra valores do coeficiente PB para diversos sistemas “óxido-substrato”, mostrando inclusive que maiores teores de nitrogênio na camada ε reduzem o coeficiente PB, garantindo maior resistência à flambagem da camada de óxidos.
A concentração suficiente de nitrogênio (com adições carbono) na camada é a chave para uma boa sustentação da camada de óxido proporcionando uma elevada resistência à corrosão.
Como essas concentrações são diretamente influenciadas pelos parâmetros de processo, grandes discrepâncias entre tratamentos de oxinitrocarbonetação podem ocorrer, principalmente em processos instáveis e/ou mal controlados. processo Corr-I-Dur obedece a certas regras ligadas a equipamento, controle supervisório, controle de atmosfera e parâmetros de processo para garantir repetibilidade de resultados de resistência à corrosão. Na figura 4 pode ser visto um forno utilizado no processo de oxinitrocarbonetação. A figura 5 apresenta uma análise da resistência à corrosão em salt-spray para amostras de aço SAE 4140 e 5140 com diferentes processos de oxinitrocarbonetação.
Processos convencionais de oxinitrocarbonetação, sejam eles realizados em plasma, banho de sal ou gás atendem exigências de 96 horas de salt-spray, mas possuem limitações para atender a crescente demanda de 240 horas ou mais.
PROCEDIMENTO EXPERIMENTAL
Para o desenvolvimento deste trabalho foram utilizados corpos de prova em aço SAE 1045 polidos (Rz = 2 µm), com dimensões de Ø25mm x 50 mm. O procedimento de preparo da superfície dos corpos de prova objetivou a padronização da rugosidade, já que esta influencia diretamente nos resultados da resistência a corrosão.
Destinaram-se dois corpos de prova para cada processo, sendo estes tratados conforme abaixo:
– Nitrocarbonetação em sal + oxidação em banho de sal (processo 1);
– Nitrocarbonetação em gás + oxidação em banho de sal (processo 2) e;
– Nitrocarbonetação e oxidação em gás pelo pro-cesso Corr-I-Dur (processo 3).
Não foram realizadas amostras de oxinitrocarbonetação em processos a plasma devido ao histórico prático e teórico de baixos resultados de resistência a corrosão em salt-spray.
Os parâmetros de processo seguem apresentados na tabela 2.
As análises realizadas para avaliação da resistência à corrosão e propriedades das camadas obtidas envolveram análises metalográfica, ensaios de microdureza e ensaio de resistência à corrosão em atmosfera salina salt-spray conforme DIN 50021-SS (ASTM B117-73). O perfil de penetração de nitrogênio foi obtido através de técnicas e espectroscopia GD-OES.
Figura 5 – resultados de ensaio de salt-spray em amostras oxinitrocarbonetadas por diversos processos .
A análise metalográfica foi realizada por microscopia óptica convencional, sendo adotada para avaliação da morfologia e da espessura da camada oxinitrocarbonetada. O ensaio de dureza foi realizado em escala Vickers (microdureza), avaliando em paralelo a resistência ao desgaste das camadas nitrocarbonetadas obtidas.
O ensaio em salt-spray foi adotado com o objetivo de avaliar através de uma correlação, a resistência dos processos ao fenômeno de corrosão, já eu muitos ferramentais estão suscetíveis ao ataque por soluções corrosivas.
Um exemplo típico deste ataque ocorre ao processamento do PVC (policloreto de vinila), onde há a liberação do ácido clorídrico (HCl), agente com forte poder corrosivo.
Para as matrizes, há a possibilidade de utilização de aços inoxidáveis ou aplicação de revestimentos PVD, o que não se aplica em buchas e colunas, em função do alto valor agregado. Sendo assim, a utilização da oxinitrocarbonetação para os demais componentes de um ferramental se lança como alternativa na prevenção de fenômenos de corrosão.
RESULTADOS E DISCUSSÕES
Metalografia e avaliação da curva de dureza
As figuras 6 – 7 – 8 demonstram os resultados obtidos para os processos 1,2 e 3 respectivamente.
Os parâmetros para ensaio salt-spray, conforme norma DIN 50021-SS (ASTMO B117-73), usados para o ensaio, estão apresentados na tabela 3.
Após 80 horas, as amostras oxinitrocarbonetadas pelo processo 2 (nitrocarbonetação em gás e posterior oxidação em banho de sal) apresentaram distinta corrosão comparadas às amostras do processo 1 e 3 que não apresentaram nenhum indício de formação.
Após 120 horas de salt-spray as amostras oxinitrocarbonetadas pelo processo 1 (nitrocarbonetação em sal e posterior oxidação em banho de sal) apresentaram os primeiros indícios de corrosão e após 160 horas apresentavam severa corrosão.
As amostras oxinitrocarbonetadas pelo processo Corr-I-Dur não apresentaram nenhum sinal de corrosão, mesmo Após 320 horas de salt-spray, quando o ensaio foi interrompido (figura 9).
Figura 10 – Perfil de nitrogênio na camada nitrocarbonetada
obtida pelo processo 3 ( Corr-I-Dur ), Apresentando profundidade de 20 microns e 96N em massa =10
Figura 11 – Perfil de nitrogênio na camada nitrocarbonetada
obtida pelo processo 2 (nitrocarbonetação em gás com posterior oxidação em sal).Apresentando profundidade de 14 microns e 98N em massa = 7,5
CONCLUSÕES
O processo de oxinitrocarbonetação é uma excelente escolha para elevar a resistência ao desgaste e corrosão de componentes de moldes e matrizes como colunas, buchas e águas. A resistência à corrosão obtida pelo processo Corr-I-Dur é superior aos processos convencionais de oxinitrocarbonetação envolvendo banhos de sais (ou mesmo plasma), além de ser uma tecnologia ecologicamente correta.
Os melhores resultados obtidos pelo Corr-I-Dur podem ser explicados pelo maior controle do processo, através da avaliação constante do potencial de nitrogênio, podendo desenvolver camadas com maior ou menor concentração de nitrogênio, proporcionando formações de camadas de óxido mais estáveis.
REFERÊNCIAS BIBLIOGRÁFICAS
[1] www.wikipedia.org.br
[2] Silva, André Luiz V. da Costa e; Mei, Paulo Roberto; Aços e ligas especiais. Edgard Blücher, 2006.
[3] ASM Handbook: Volume 4 – Heat Treating; ASM International, 1991.
[4] Totten, George E.; Howes, Maurice A. H.; Steel heat treating handboo. Marcel Dekker, 1997.
[5] Walkowiak G.; Wägner M.; Corr-I-Dur Nitrocarburizing and Oxidizing: Correlation between Layer Constituition and Corrosion Resistence, Proceedings of 8th Seminar of the IFHTSE 2001, 12-14 September, Dubrovnik Cavtat, Croatia, 201-207.
[6] Warmebehanglung GMBH. Bodycote Research. Process Corr-I-Dur, 2005.
[7] www.brasimet.com.br/durotin
Piter Alves de Sousa – Graduado em Tecnologia de Processos Metalúrgicos. É responsável pela Engenharia de Processos na unidade de São Leopoldo da Bodycote Brasimet.
Bruno Otávio de Castro Cardoso – Engenheiro Mecânico. É responsável pela Engenharia dos Processos de Nitretação da Bodycote Brasimet.
Carlos Humberto Sartori – Engenheiro Metalurgista e Mestre em Engenharia de Metalúrgica e
Materiais. Atua como Coordenador da Célula Ferramentas da Bodycote Brasimet Processamento Térmico Unidade São Paulo.
Lintha da Costa Battisti – Estudante do curso de Engenharia Industrial e Química. É estagiária de Engenharia da Bodycote Brasimet na unidade de São Leopoldo – RS.
Fonte: Revista Ferramental edição nº 30 fev 2016
Conheça nossos info-produtos