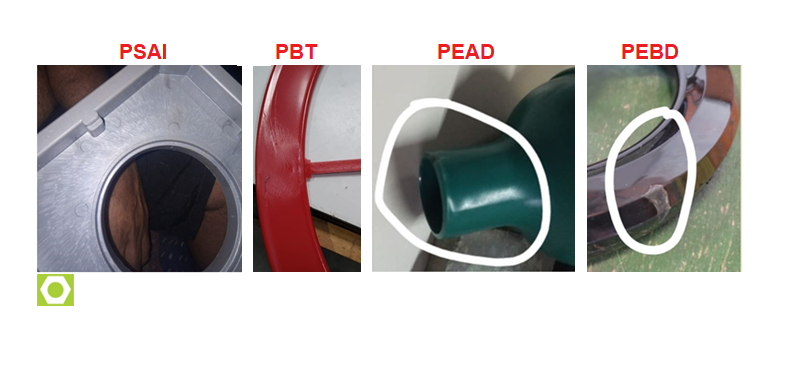
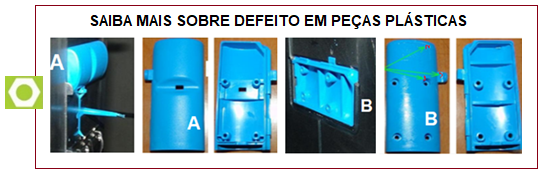
Problemas de injeção plástica com PEBD, PEAD, PBT, PSAI
Este conteúdo abrange diversos problemas que ocorrem durante a injeção de diversos produtos plásticos no dia à dia. São resumos de casos apresentados e que receberam comentários e sugestões de profissionais. A ideia é levar a informação na palma da mão, para um melhor direcionamento no momento da necessidade. Se lhe interessa saber mais sobre molde de injeção, manutenção em molde e sobre defeito em peças plásticas indicamos nossos Estudos livres. http://moldesinjecaoplasticos.com.br/loja/
Aqui temos espaço para quem sabe e para quem deseja aprender.
Qual a temperatura ideal para injetar PE?

Autor- Qual a temperatura ideal para injetar PE?
Comentários do grupo:
Trabalho com Temperatura de 200 ºC, 210 ºC, 190 ºC e 185 ºC, mas depende do produto que vai ser injetado e depende da máquina também.
Molde com canal, temperatura, faça escala, alimentação 185 ºC, plastificação 195 ºC, homogeneização 205 ºC, e fusão 210 ºC, a temperatura vai depender muito do tempo de residência do material no canhão, tipo se o canhão da máquina que está trabalhando não usa toda a capacidade de carga, ou falta pouco para carregar até o final, então aumenta uns 10 ºC a cada zona de aquecimento, agora se o canhão tem a capacidade de umas 3 ou 4 injetadas, pode trabalhar com essa temperatura passada acima.
Outro fator importante que tem que levar em conta é o ciclo da peça, acredito que para essa peça (se no caso for essa da imagem) esteja trabalhando com água gelada, deve estar com um ciclo de uns 70 / 80 tempo total.
Pois tudo é relativo e deve se levar em consideração, temperatura, tempo de residência, e tempo de resfriamento.
É um material parcialmente cristalino, então o ponto de fusão dele é baixo. Dependendo da peça (se no caso for essa da imagem) poderia trabalhar ela em 240 ºC, 240 ºC, 220 ºC, 220 ºC e 200 ºC. Levando em consideração a espessura da peça e se a máquina tem força para tal.
Também é bom verificar a temperatura para não aquecer demais a matéria prima e acabar degradando-a.
Depende muito da fluidez, injeto caixas temperatura câmara quente e canhão 270 ºC.
Depende muito da máquina.
180 ºC a 240ºC.
Mancha de queimado no final da injeção
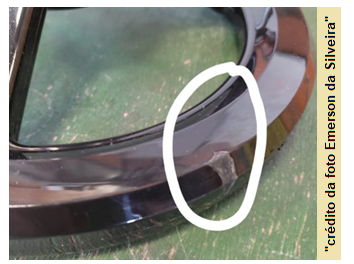
Problema: mancha de queima no final da injeção
Feito saída de gás no molde e bolsão de ar, mas nada resolve.
Tentei, uso PEBD – Polietileno Baixa Densidade – Canelinha, comecei em 240º e já fui até 175º, porém não mudou nada ou quase nada, já mudei de equipamento porém o problema permanece.
Estou utilizando PEBD – Canelinha + pigmento.
Comentários:
– Com certeza é uma queima devido ao aprisionamento de gás, o chamado efeito diesel. Isso acontece devido a uma propriedade geral dos gases que quando eles são comprimidos a certo ponto eles super aquecem, a temperatura se eleva tanto que acaba carbonizando o polímero na área de contato, no processo de injeção. Para que a cavidade seja completamente preenchida é necessário que o ar saia conforme o polímero vai entrando.
Eu faria assim:
– Trabalhar com o molde mais aquecido e com velocidade de injeção menor, aliviar o travamento, verificar a descompressão, principalmente a dianteira e diminuir ou zerar se possível, se possível diminuir a temperatura do material.
– Percurso do material muito longo até chegar ao final da injeção acumula muito gás
– Se tiver pino de extensão próximo desse ponto, faz a saída de gás no pino que resolve.
– Coloca para injetar mais lento, diminui um pouco o travamento do molde.
– Injetar com perfil talvez resolva, mas também se a velocidade de injeção estiver muito alta e a fluidez do material for alta, costuma dar essas queimas porque o ar não sai.
– Encontro de materiais com parede fina. Faça uma simulação de flow ou aumente a espessura, mas para facilitar a saída de ar deixa até sair uma mínima rebarba. Tem que ver a exigência da peça, vá injetando sem completar e verá o fluxo da matéria prima conforme for aumentando o material.
– Velocidade de injeção, fluidez do pigmento e homogênizacao do material e pigmento, experimente injetar com pouco ou sem pigmento.
– Já tentou reduzir temperatura da massa, quantidade da massa na cavidade, ou talvez seu equipamento não está bom, aí tem que contornar o problema, o chamado macete pode resolver.
– Está parecendo junta fria, pode ser que o material esteja esfriando antes de completar o produto.Experimente trabalhar com velocidade alta de injeção se caso não funcionar monta um perfil e vai trabalhando na velocidade (lembrando que perfil não é somente velocidade, você precisa saber em qual parte do produto determinada cota está atingindo, se é começo meio ou final do produto, nesse caso, precisa de velocidade na parte final do produto.
– Se as saídas de gás não resolveram a anomalia, recomendo mudar a posição da entrada da injeção na cavidade. Pela foto não está indicado, então não posso dar um conselho para a modificação.
– Muitas vezes o erro está em encontrar o ponto de comutação. Se você retirar o recalque a peça falha? Se já existe saída de gás no molde faz isso, zera o recalque e faz a peça falhar, depois acrescenta o recalque com velocidade mínima e uma pressão mais alta. Se não ficar bom a saída de gás deve ser aumentada ou até mesmo vai precisar de um poço frio nessa região.
– Desumidifica bem o material e muda o ponto de injecão para a peça acabar de encher na linha de junta e no escape de gazes. Alivia toda a linha de junta nessa zona em 0.03.
Peça está contraindo demais e não está dando encaixe.
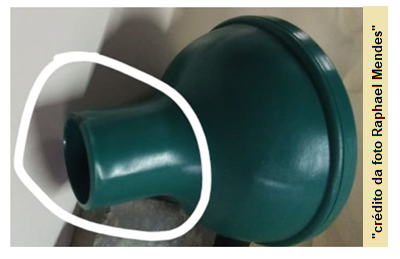
Problema: Peça está contraindo demais e não está dando encaixe.
A contração ocorre (em maior parte) no encaixe traseiro da peça. Injetando material PEAD- Polietileno Alta Densidade. Já tentei usar PP no lugar do PEAD, porém o material não atende.
Comentários:
– Algumas situações são: Aumentar tempo de resfriamento, diminuir tempo e pressão de compra pressão, trabalhar com água gelada nas duas partes, resumindo.
– Precisa de uma injeção mais rápida com menos massa calcada na cavidade, se com isso ocorrer acúmulo de gás, pode aliviar o travamento para ajudar na saída de gás, se mesmo assim não conseguir, terá que procurar outras alternativas, como troca de material e ajustes no ferramental.
– Refrigeração……Está baixa.
– Quantos milímetros tem a parede da peça?
– Como está a refrigeração? Tem algum condutor entupido?
– Já fez um teste para ela cair no recipiente com água gelada.
Autor – Já, sim.
– Faz um teste com tempo de refrigeração demorado, se não resolver o problema está no projeto do ferramental.
– Já tentou misturando 50% de PEBD com 50%PEAD, certamente irá reduzir a contração porque a contração do PEAD é muito elevada pode chegar até 2,5% já o PEBD a contração é bem menor, pode resolver seu problema.
– Tenta colocar + resfriamento no local.
– Tem peça que devido ao volume injetado o projetista tem que na área de encaixe deixar com dimensional acima do nominal, para no processo de fabricação essa área contraia mais e chega na medida ideal… (observe a medida de contração atual em condições normais de injeção e redimensione o macho para adequar a medida ideal de encaixe.
– As medidas alteram no recalque da máquina e no tempo de resfriamento.
– Para alimentar a produção, e legal fazer um gabarito externo para colocar.
– Isso mesmo, aqui fizemos assim. Criamos um dispositivo com ventilador para melhorar o processo.
– Já aumentou o tempo de recalque.
Autor – Deixei com 1,5 segundos não teve muita diferença, acha que deve aumentar?
– Pode colocar 3 segundos, aumente um pouquinho a pressão de recalque também para compactar bem.
– Em qual máquina está injetando?
Autor – Romi EN 170.
– Ela ainda contrai um pouco.
– Precisa ter um tempo de resfriamento e um tempo de recalque bem maior. Como está usando a refrigeração, gelada ou ambiente?
Autor – Refrigeração gelada, 12 graus com Chiller próprio para a máquina.
– Não deveria contrair tanto assim! Tente no tempo e pressão de recalque.
– A matéria prima é virgem ou reciclada?
Autor – Reciclada – Vou focar nisso.
– Muitas vezes, faltando refrigeração no processo a contração é certa, duas formas de melhorar, diminuir a velocidade da máquina ou melhorar a refrigeração.
– Trabalho com injeção de peças técnicas do seguimento automotivo, tenho esses tipos de problemas constantemente e consigo solucionar compactando com tempo de recalque alto.
Autor – Vou focar nessa parte de regulagem então.
– É possível dois testes, tempo alto de recalque e baixa pressão e depois pressão mais elevada e diminuir o tempo e testar o encaixe.
– Aumenta o tempo de recalque e pressão. Controlar que tem colchão no final da injeção. Se por acaso a rosca não consegue manter o colchão, vá até o fim, provavelmente válvula quebrada na ponta da rosca.
– Mistura um pouco de PP no PEAD, já tive um problema parecido, no meu caso deu certo.
Autor – Testei, não funcionou, mas valeu a dica.
– Coloca água gelada na parte móvel do molde, e vê como está o recalque pressão, velocidade e tempo.
– Temperatura e tempo de injeção.
– Alterar o ciclo e mudar a refrigeração do molde, pode ser que está refrigerando.
– Aumentar o tempo de recalque, tempo de resfriamento e refrigeração do molde, água gelada vai resolver.
– Está ficando maior ou menor?
Autor – Está ficando menor.
– Aumente então o tempo de recalque uns 2 segundos a mais, deixe esfriar e faça o teste.
– Tenta aumentar o tempo de resfriamento.
Autor – Já tentei, porém depois que esfria ainda abaixa.
– Já tentou deixar esfriar na água.
Autor – Ainda não, tentarei.
– Isso, tenta aí quem sabe dá certo.
– Parece estar rechupada…injeta mais material, e aumenta o tempo de recalque!
– Eu também faria um gabarito.
– Pode ser uma sujeira no molde, dá uma olhada para ver se não tem pedaços de materiais no molde.
– Vai ter que aumentar a refrigeração no postiço onde forma esse detalhe no produto.
– Aumentar o tempo de resfriamento e verificar se o resfriamento está tudo ok
– Em peças com problemas de contração no diâmetro (exemplo balde d’água) a melhor solução é o gabarito.
– Experimenta deixar cair na água, quando cai na água quebra a contração.
– Só com gabarito…
– Já tentou aumentando tempo de injeção e um pouquinho mais de resfriamento?
Autor – Aumentei o tempo de injeção até rebarbar, e resfriamento estou tirando com 30 segundos.
– Faz um gabarito com o diâmetro que precisa e encaixe após a injeção e deixe resfriar por algum tempo ou aumenta o diâmetro do macho para que atenda o dimensional que está precisando.
– Faz um gabarito de madeira ou cano de metal mesmo e deixa um tempo resfriando com ventilador.
– Refrigeração, aumenta um pouco o tempo de ciclo.
– Trabalho com bombonas em PEAD recuperado e ele também contrai.
– Vai ter que criar uma ferramenta para estancar essa contração que se chama pós cooling e colocar no produto logo que sair da máquina.
– Acredito que no molde está faltando uma saída de gás.
– Refrigeração.
– Talvez seja o caso de projetar com resfriador para retardar a contração.
– Trabalhar com água gelada e usar um retardo na dosagem já faz a diferença.
– Eu aumentaria com contra pressão e deixaria talvez resfriar dentro d’água se não houver melhor resfriamento.
– O molde não está com boa refrigeração.
– Experimenta deixar cair em água para esfriar mais rápido.
– Acho que só no recalque, ou trabalhar com água resfriada.
– Põe mais recalque, segura um pouco mais no resfriamento que já era.
– Olha como está a refrigeração do molde, pode estar passando pouca água. Trabalha com água gelada ou natural? Se for natural tenta colocar gelada para ver, assim não altera o tempo de resfriamento, quem sabe até abaixa.
– Fazer canal de saída de gás.
– Depois que extrair joga na água, deixa até o próximo ciclo. Vai resolver.
– Desenvolve um gabarito, que encaixe nos 2 furos, para ela esfriar no diâmetro desejado.
– Isso aí é ar preso dentro do molde.
– Faz um gabarito deixa o gabarito dentro da água e encaixe a peça nele.
– Como está a refrigeração.
– Se não tiver problema quando sai da máquina joga direto na água irá ajudar um pouco.
– Trabalho também com bastante.
– É verdade materiais de engenharia é um caso sério.
– Trabalho em fábrica de faróis e lanternas automotivas as peças tem que ter um bom dimensional caso contrário não encaixa na hora da montagem.
– Verifica a saída de gás, está pequena falha pode ser gás.
– Está usando água natural ou gelada?
– Aumenta o tempo de resfriamento.
– Que perca e essa bico de regador.
– Se aumentar o tempo de recalque consideravelmente, provavelmente resolverá seu problema.
Marca de queimado

Autor – Já foi baixado a temperatura, a injeção, aumentou o tempo de resfriamento e mesmo assim vira e mexe sai uma peça com marca de queimado no fechamento da peça e se baixar mais a injeção a peça não fecha.
Comentários:
Dá uma olhada na saída de gases do molde.
Autor – Esqueci de mencionar o molde trabalha com câmara quente.
O fato de ser câmara quente não altera o problema. O projeto do molde e desenho de produto devem colaborar para que os gases sejam empurrados para as extremidades do produto onde na linha de fechamento pode ser feita a abertura (de centésimos de milímetro) para o escape dos gases. A saída é procurar o ferramenteiro que fabricou o molde ou outro experiente para entender porque a emenda do material ocorre neste ponto.
Saida de gás deficiente. Na região que sai o defeito, pode colocar um pedaço de fita crepe para gerar uma saída de gás também.
Normalmente é saída de gás que causa esse problema coloca uma fita no final da junção do material para ver se resolve.
Limpa a saída de gás, também pode diminuir um pouco o travamento e diminuir a velocidade de injeção.
Tem que limpar as saídas de gás e diminui a velocidade da injeção.
Tire um pouco o travamento, caso de rebarba, trava novamente e diminui o recalque.
Se esse molde tiver câmara quente, confere todas as zonas e verifica se o termopar está lendo a temperatura correta ou está na posição correta.
Corrige primeiro as orientações já fornecidas. Caso não resolva aí provavelmente terá que fazer manutenção no molde.
Diminua as últimas velocidade de injeção.
Provavelmente o produto está com diferença na parede…este lado está mais fino.
Isso é falta de saída de gases, faça um perfil de velocidade o mais baixo possível no fim da injeção, ou tente compensar com a 2°pressão.
Limpe bem as fugas de gases, se conseguir baixe a força de fecho da máquina.
Vê-se a descompressão não está muito.
Da uma aliviada no travamento e limpa a saída de gás.
Se possível diminua velocidade de rotação da dosagem e velocidade de injeção.
Provavelmente é saída de gás, tenta dar uma aliviada no fechamento.
Como está a centralização macho / matriz.
Espessura, tente mudar velocidade de injeção, esta queima é sempre no mesmo lugar? é onde faz o final da injeção?
Faz uma ranhura com uma lima para sair o gás na direção do queimado.
Diminuir força de fechamento, baixa a descompressão e rotação da rosca, também a velocidade e verificação a secagem da matéria prima. Se não resolver acionar ferramentaria para melhorar a saída de gás.
Diminua a velocidade de injeção, pode compensar no tempo de injeção. Verifique se as saídas de gases estão limpas próximo a essa região.
Fazer uma micro-saída de gases no molde.
Tem que fazer saída de gás no molde o máximo que você puder principalmente no caminho da queima.
Verifique a velocidade de injeção deixar mais lenta, pouco mais de pressão, mas talvez fazer uma saída de gás.
Faça secções do produto e verifique a espessura. Certamente onde da queimadura a espessura é menor, então é a última parte a preencher. Saídas de gás para o seu problema neste ponto da peça não são necessárias.
Marca estriadas na entrada de material
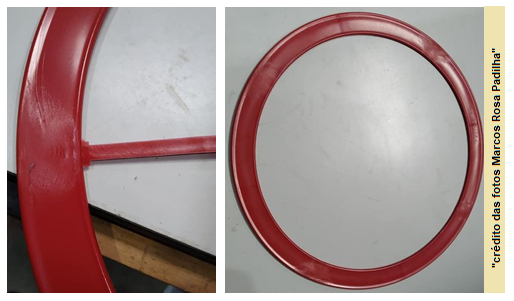
Problema: marca estriadas na entrada de material.
Material PEAD – Polietileno Alta Densidade. Molde com 04 pontos de injeção utilizando água normal, pois com água gelada costuma aparecer essas marcas.
Comentários:
– Turbulência, experimenta começar com velocidade baixa, faz um perfil.
– Reduza bem a velocidade de injeção justamente na entrada do material na cavidade e aumente pra poder concluir o preenchimento.
– Uma sugestão, aumente a pressão e velocidade até aparecer rebarbas, se melhorar o seu problema com certeza é saída de gás.
– Primeira coisa fazer um teste com baixa velocidade e depois em alta com a velocidade máxima de injeção e comparar se ouve alguma melhora. Caso não, usar uma matéria prima com uma fluidez maior pelo menos fluidez de 40. Se não resolver o jeito e aumentar a entrada do gate. Faça o teste e observe os resultados. A partir daí te dará uma noção do que esta influenciando no aparecimento dessas marcas.
– Pode ser a entrada obstruída, se tiver como aumentar com certeza ajuda.
– Experimente o seguinte processo entre com média pressão e baixíssima velocidade por 15 mande curso de injeção. E depois alta velocidade e pressão necessária para completar e baixo tempo de recalque e somente 0,8s de tempo de recalque.
– Qual a dimensão do canal em relação a espessura de parede ? Esse efeito de esguicho geralmente é gerado pela restrição do canal de injeção, ou/e velocidade de injeção muito alta – algumas vezes o material está entrando com muita fluidez (material muito quente), ou material com baixa fluidez(frio) que causa hesitação do fluxo no canal; Usar um escalonamento de velocidade pode ajudar; Começar com baixa velocidade, e ir subindo até um patamar estável.
– Teste prático: aumente o resfriamento e injete peças com a água desligada, escalone a injeção, início lento e depois um pouco mais rápido. Verifique as temperaturas de processo, pelo datasheet veja até quanto pode aumentar.
– Aumenta um pouco a tempo e faz um perfil de injeção, sendo mais lento no fim. Pode ter acumulação de gases na parte final da peça. Faz um estudo de enchimento da peça para ver qual o ponto de comutação. Se possível pede para aumentar ou fazer fugas de gases.
– Talvez aumentando a temperatura do cilindro e e principalmente do bico pode já começar a te ajudar. Pela foto da pra ver que antes de chegar na peça o material já está frio no canal.
– Da uma bela limpada no molde, aumenta a velocidade da rosca e aumenta a velocidade de injeção qualquer coisa abaixa um pouco a pressão se der rebarba, e da uma verificada nas temperatura.
– O conceito de canal meia cana influência diretamente nesta mancha o ideal seria passar para o conceito trapezoidal além disso é possível observar uma quebra de fluxo logo na entrada a mesma deve ocorrer de forma mais suave e com menor impacto, para isso o ideal seria escalonar o fluxo do canal até a entrada do produto.
Marcas de riscado na peça – Material PEAD

Autor – Injetamos peças em PEAD novo da Braskem e apresentou esse problema em média de 20 dias depois da injeção. Material da BRASKEM saco fechado sem contaminação por outro material.
Será que pode ter sido por causa do desmoldante?
Comentários:
O uso do desmoldante e em todas injeções? Ou não?
O uso do desmoldante é para facilitar a extração do produto.
autor – Isso, em todas as peças – Ultralub
Esse desmoldante é tudo: lubrificante, anticorrosivo, protetivo, use um desmoldante sem silicone em menor quantidade, esse bico aplicador encharca muito a peça.
Quase certo que sim, faça um trabalho no molde ou no processo para eliminar o desmoldante a base de silicone.
Desmoldante assim deve ser usado apenas quando você quer que o molde atinja uma certa temperatura ideal em que a peça já não fique presa mais, ou seja, o famoso até pegar ciclo, se precisa ser usado em toda peça, tem algo errado no projeto do molde, por exemplo ângulo de saída, e se não for possível corrigir, deve usar um desmoldante no próprio material.
Provavelmente é por causa do desmoldante. Depois de um tempo ele reage com material da peça.
Pode ser que sim, porque passei por esse problema aí tinha que passar o desmoldante meio de longe, ou passar e limpar com uma estopinha.
Certeza! Tem que procurar outro tipo de desmoldante sem base de silicone. Talvez procurar um deslizante para fazer blenda no material.
Você está usando que refrigeração nos machos
Coloca 0,5 porcento de estearato de zinco no material, já resolvi problema de desmoldagem assim, prepara pouco e faz um teste.
Pode ser matéria prima OFF, veja a possibilidade de outro lote de matéria prima.
Então….analisa o material se não é off grade…se for é possível estar aí o problema.
problemas com bolha
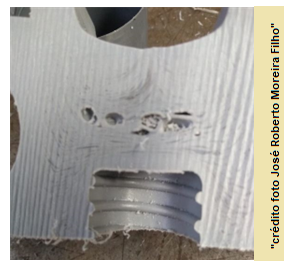
Problema: formação de bolhas
Material PEAD
Comentários:
Com essa matéria prima o mais indicado seria reduzir a temperatura da massa, reduzir a velocidade de preenchimento, aumentar o tempo de compactação, trabalhar com boa contrapressão e o mínimo de descompressão (se possível evitar) – evitar tudo que possa gerar gás na plastificação.
Checar saídas de gás do molde apesar destas bolhas também serem devido à espessura da peça e resfriamento no molde.
Problema chato de resolver, mas não impossível.
Autor – Já estou com a temperatura de 150 a 130.
– Está baixo até demais para PEAD; neste caso verificar a pressão de dosagem (pressão hidráulica no momento de giro da rosca) – caso esteja muito elevada é perigoso para o equipamento e a rosca pode “pular”, voltando sem girar completamente e carregando, nesse caso o ar, pois não ocorrerá plastificação.
Também verificar a viscosidade do material – caso a viscosidade seja baixa (alta fluidez) não seria o mais adequado para peça com espessura elevada.
PS.: a rosca + anel de bloqueio dessa máquina estão confiáveis? A malha de aquecimento é confiável?
Autor – O material que estou usando tem a fluidez muito baixa, tem que ser este para a peça.
– Correto, porém material com essa fluidez e com a temperatura que está usando deveria causar dano à unidade de injeção, por isso a dúvida.
– Ar preso. Provavelmente você tem um fluxo de material em duas frentes que se encontram neste ponto e o ar preso entre as frentes, não tem como sair. Tem de criar uma saída para estes gases. Ou mudar o ponto de injeção.
Autor – Quando eu corto a peça ainda quente não aparece a bolha.
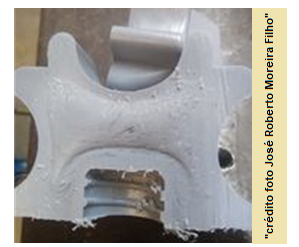
– É por que ela está ocasionando a degradação do material durante a solidificação, é necessário reduzir a temperatura do fundido e também aumentar o tempo de exposição do mesmo ao molde para que a solicitação aconteça o mais rápido possível com temperatura menor no Chiller.
– Tenta solidificar ela ainda nessa condição de cortada.
– Material está encapsulando o ar porque a velocidade de injeção está alta,
– Só para avisar, tempo de recalque não ajuda na compactação da peça, dependendo do gate, só vai desgastar equipamento.
– Verifique bem os escapes do molde, as velocidades de injeção (comece a injetar lentamente), contrapressão, temperatura do cilindro.
– Saída de gás no molde.
– Tem uma peça aqui de parede grossa que eu dou 120 segundo de recalque.
– Muita massa nesse ponto, precisa melhorar a refrigeração, vai melhorar o surgimento das bolhas após a desmoldagem.
– Se possível colocar alívios de massa no molde.
– Já tentou um tempo de recalque uns 5 segundos e uma pressão do recalque de 60 a 70 bar.
– Diminua a descompressão, aumente o tempo de recalque e para não perder tempo de ciclo diminua o tempo de resfriamento a mesma quantidade que aumentou de recalque, pois no recalque já está em resfriamento e aí verifique.
– O que talvez possa te ajudar é aumentar bem a contra pressão e injetar um pouco mais lento, ou pelo menos escalonar a injeção entrando mais lento, depois pode até abrir mais a velocidade.
– Faz um poço frio bem no centro onde estão saindo essas três bolhas, vai eliminar esse problema.
– Saída de gás no molde, no processo e retirar a descompressão e tentar alguma contra pressão na dosagem.
– Talvez resolva aumentar o canal de alimentação, daí consegue trabalhar com menos velocidade e menos pressão.
– Essa peça é um isolador polimérico (talvez de 15kv) de topo, injetado em PEAD.
– O ciclo de injeção para uma peça dessa de quatro cavidades seria ~ 4 minutos, com aquecimento de molde a 50°C e canal de entrada na bucha de injeção e bico em torno de 6 a 8mm. A contra pressão em ~ 30% e muito lenta, para misturar bem o material na dosagem, pois sua peça além de bolha tem material sem misturar, acredito que o PEAD mais o Master.
– A injeção bem lenta, e recalque com 90% da capacidade da máquina, se for uma Wittmann por exemplo. Temperatura de trabalho entre 150°C e 160°C, precisa ver caraterísticas de máquina para uma melhor dica. Molde com boa saída de gás no fechamento e se possível, aliviar o fechamento para uma melhor compactação, a linha de fechamento no começo está forte, mas vai fechando a cada ciclo.
“A dosagem mais lenta possível…”.
– Creio que deva ser ponto de injeção errado, como é PE de alta densidade, as saídas de gás devem estar no final da injeção, se o material passar pela saída de gás e fechar no centro não vai tirar, o ponto de injeção deve ser feito de um jeito que a peça seja preenchida no final do molde onde se coloca a saída de gás, nunca no meio, se não puder deve ser colocado uma saída de gás que é igual a uma válvula de ar.
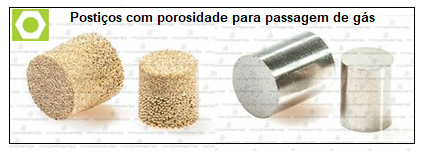
– Depende de várias coisas, se for aí onde fecha o material quando a peça acaba de encher, é bastante difícil de resolver.
– Se não for aí a zona de fecho, tenta baixar as temperaturas do fuso para 160, 140° aumenta o tempo de recalque assim como a pressão ao máximo, sem afetar a peça.
– Tenta trabalhar com o molde o mais frio possível, principalmente os machos roscados! Quando digo aumentar o tempo de recalque é bastante! Se o ciclo estiver em 65s metade disso seria de tempo de recalque, tirando no tempo de arrefecimento para tentar manter o ciclo.
– Todas acima devem ser verificadas! Usar bico valvulado se descompressão traseira ajuda.
– Diminua velocidade de injeção, diminua e velocidade de dosagem e aumenta a contra pressão.
– Conforme seja, vai regulando as válvulas de água que entram no molde para resfriamento.
– Diminua velocidade de injeção e aumenta tempo de recalque ajuda bastante, tira esses defeitos.
– Verificar saídas de gás, e mudar velocidade de injeção para baixa…
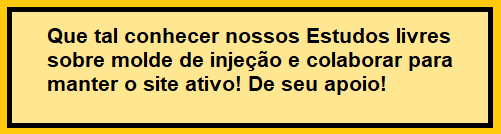
Peça com manchas espalhadas
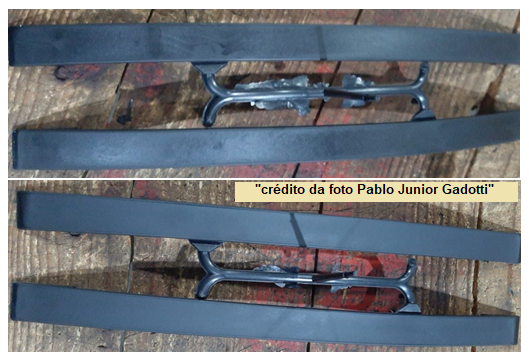
Problema: peças apresentando manchas espalhadas. Material PBT (Polibutileno Tereftalato)
Comentários:
– Secar e calor no molde.
– Mancha de água.
– Material úmido.
– Tenta aumentar a pressão de recalque no talo, as temperaturas do canhão e diminuir as velocidades de injeção, talvez ajude, verifica também se o desumidificador de material está funcionando corretamente.
– Não é mancha do polimento?
Pode ser:
– Umidade, contaminação, temperatura do molde inadequado, plastificação ruim.
– O ponto de injeção da forma como joga o material dentro da cavidade não tem o melhor design “esguichando-o” contra a parede fria do molde.
– Escalonar a velocidade nessa região da cavidade ajuda. Pelo preenchimento você consegue descobrir qual a faixa do percurso da rosca e ali você diminui bem a velocidade e depois acelera.
– Lembrando que poliéster precisa de desumidificador. Usar secador qualquer não costuma funcionar. Pior ainda se estiver usando aquelas estufas de bandeja e/ou material estiver exposto à umidade do ambiente porque algum saco está aberto ou as vedações do seu periférico não estão boas.
– Parece master degradando. Não utilize master “universal”, pois possuem veículo de PP.
– Umidade parece ser também uma causa, já que o PBT requer um tempo e temperatura maiores para desumidificar.
– Está parecendo que o material não foi desumidificado.
– Se tiver um controlador. Bota água quente no molde. Peças pretas são um saco independente do material.
– Temperatura do molde deve ser checada bem como as saídas de gazes verificadas a sua eficiência.
– Peças pretas utilizam negro de fumo que é muito higroscópico, verifique a desmistificação
– A secagem do PBT deve ser a 120ºC no mínimo 4horas…isto é seguramente umidade.
– Está bem estufado?
– Se o material em questão não estiver devidamente estufado, pode ser esguichamento, isso é ocasionado devido o posicionamento do ponto de injeção ou até mesmo sua proporção.
– Como tem mais de um ponto de injeção pode ser encontro de frente de fluxo.
– Temperatura é um grande facilitador de fluxo. Com o material devidamente estufado, isento de contaminação e na temperatura de processo ideal, uma sugestão seria o aquecimento da ferramenta (40°C a 50°C), uma injeção escalonada e a equalização dos gates…Gate tipo leque em todas as “entradas” da ferramenta.
– Caso esteja bem desumidificado o material e a mancha esteja no início do fluxo, verifique a descompressão e temperatura do bico. Da para ver que este molde já deu problema devido a estar modificado o canal de injeção.
– Caso o material esteja bem desumidificado, as temperaturas do molde e do canhão adequadas e o material não está contaminado, eu sugiro verificar a rotação da rosca, pode ser cisalhamento muito alto ou frente de fluxo.
– Coloca o molde a 120 graus.
– Como sempre o material é o vilão, o poço frio obrigatório antes da entrada do material não existe e um lado é leque, e outro direto? Verifica isso também.
– Verifica se o material está bem estufado. Diminui a velocidade de planificação, deixe o colchão o mínimo que poder e descompressão 0.4% da carga que está usando.
– Jato de areia no molde pode solucionar.
Pode estar compactando muito, temperatura muito alta, contra pressão alta, material úmido…tem que ir por eliminação.
– Uma excelente observação, falta “poço frio” no canal, pois minha impressão é material frio na entrada!
– Este material possui fibra de vidro ou e sem carga?
– Estás a referir a linha de fecho certo? Tenta aumentar a temperatura do molde e do fundido, e ajusta as velocidades que vai melhorar.
– Isso pode ser umidade, aumenta a temperatura da sua estufa, aumenta um pouco a temperatura, um pouco do canhão e cuidado com a temperatura do bico que pode estra queimando a matéria prima.
– Por foto é difícil avaliar, mas talvez uma polida no molde resolve, dá uma olhada para ver se tem material prima aderindo ao molde, já aconteceu aqaui. As vezes um pano com solvente resolve também.
– Parece fluxo de injeção, tenta injetar mais rápido ou colocar água aquecida na parte fixa.
– Balanceamento dos Gates (Ponto de injeção).
– Controlar temperatura do molde próximo a 80 graus.
– Trabalhar com pouco colchão.
– Mínimo possível de descompressão.
– Pode ser fibra, temperatura ou velocidade baixa.
Autor – Problema resolvido. Limpamos o canhão e aumentamos a temperatura.
Começando lenta para não dar turbulência na entrada e rápido no final para dar acabamento no produto.
Peça com manchas – Material PBT
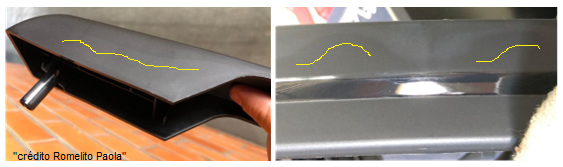
Autor – Testamos saída de gás, material está seco (testado no laboratório), testado com água quente e gelada. Sem master, material já vem na cor.
Conforme altero os parâmetros as manchas mudam um pouco de posição, então na textura não pode ser. As vezes mudo um pouco a pressão e velocidade as manchas mudam bem pouco de posição.
Mesmo zerando o recalque a mancha aparece.
É uma peça totalmente aparente do fogão, se eu aqueço acima de 60 ºC as peças ficas espelhadas e o cliente exige que sejam foscas. Trabalho com mais de 20 moldes dessa maneira e só esse que da mancha.
Posso trabalhar com 80 ºC ou com água gelada que as manchas aparecem. Em relação a compactação as peças chegam a falhar e mesmo assim mancha.
Comentários:
Tenta subir um pouco mais a temperatura, impressão é que o material está esfriando no caminho e deixando as marcas.
Subindo a temperatura já deve ajudar bastante.
Será que o sistema de refrigeração do molde está 100%? Nessa região pode estar frio o molde.
Pode ser marca de fluxo do material.
Se altera de posição quando altera a velocidade então trabalha em cima disso tenta achar a velocidade correta de injeção de dosagem, realmente me parece mancha do fluxo do material que pode estar correndo na hora da injeção ou na dosagem.
Alivia o fechamento ou travamento da máquina, se possível vai aliviando um pouco cada injetada para ver se melhora.
Com PBT essas manchas ocorrem devido a temperatura muito alta do molde e ou muita compactação (excesso de recalque).
Por exemplo, na mesma máquina com outro molde, não acontece isso?
Se isso acontecer, pode ser que o canhão trincou e está entrando água.
Imperceptível, mas aconteceu comigo, troquei o canhão, e não tive mais problemas.
Às vezes quando injeta peças falhadas, a matriz fica marcada provocando essas marcas, é só limpar a matriz, faz uma amostra com ABS de boa qualidade.
Já trabalhei com PBT, tive problemas com mancha era um molde novo só foi resolvido o problema quando fizemos um poço frio no molde na entrada da cavidade.
Injetei puxador de fogão em PBT, quando aparecia estas manchas o que resolvia era limpar o molde com massa de polir, depois voltava novamente, tinha que polir de novo.
Molde de 2 cavidades, o molde é novo?
Precisa verificar a cavidade se a textura não está manchada, precisa conferir a resina (temperatura) e se está usando master tudo isso influência.
Está aparecendo uma textura diferente no molde.
Tem saída de gás nesses pontos.
O molde é texturizado?
autor – Não polido.
Peça plana sofrendo empenamento
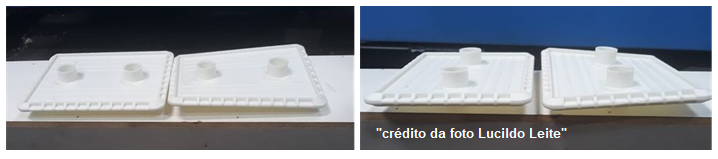
Problema: peça injetada sai plana, mas ao passar do tempo empena.
Material PBT – (Polibutileno Tereftalato) – Alguma sugestão?
Comentários:
– Tem que refrigerar o molde com água gelada.
– Verificar se o molde está centrado.
– Aumenta a comutação.
– Qual a temperatura do molde? Monitora a temperatura do molde? Tem como abaixar a velocidade de injeção? Tem como aumentar a temperatura da massa?
– Depende do ciclo.
– Se possível, há possibilidade de fazer um dispositivo, para resfriamento.
– Talvez aumentando o tempo de resfriamento, para que não saia muito quente e assim não entorta.
– Também vale verificar a água gelada.
– Acho que a associação de ambas as ideias deve praticamente solucionar o problema. Se a tensão for muito grande, mesmo com o uso de berço, pode ter a fragilização em algum ponto e eventualmente quebrar a peça.
– Pode fazer um dispositivo para resfriar a peça fora da máquina, na empresa onde trabalho casos assim nós colocamos em berço e deixamos resfriar um pouco, normalmente temos de 3 a 5 berços e vai fazendo o rodízio, sempre tirando a mais gelada.
– Faz um teste simples, coloca uma caixa com água com uma serpentina com circulação de água gelada e deixa as peças caírem na água após a extração, deve melhorar muito esse problema, ou até mesmo eliminar.
– Se quiser ajudar a eliminar de vez o problema, desenvolve um gabarito para encaixe das peças, para que elas conformem após a injeção das mesmas.
– Algumas peças precisam ser resfriadas em um gabarito na água dependendo do material utilizado, com formato da peça. Difícil resolver mudando parâmetros na injetora.
– No caso se colocou muito tempo e pressão de recalque acontece isso também.
– Pode ser o material e também pode ser que o molde estava com pouca refrigeração.
– Isso é contração do material. Pode tentar injetar com mais velocidade e menos tempo, a compactação em demasia ocasiona o empenamento. Molde deve ser aquecido em no mínimo 60⁰C. No seu lugar faria um berço para a peça resfriar pressionada, daí acabaria de vez com o problema.
– Se essa peça caísse na água também ajudaria.
– Uma solução relacionada a matéria prima é a utilização de carga, assim você ganha estabilidade dimensional.
– Em relação a processo, o aumento do tempo de resfriamento junto ao decalque pode ajudar.
Peça apresentando mancha bem no centro da peça
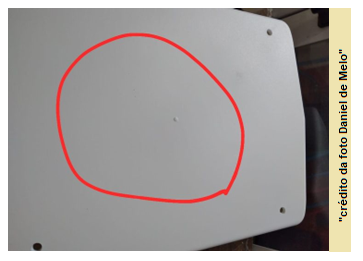
Problema: peça apresentando mancha bem no centro da peça.
Material PSAI – Poliestireno de Alto Impacto. Molde com câmera quente.
Comentários:
– Bico muito quente, provavelmente irá precisar melhorar a refrigeração nessa área, ou deixar todo o molde com a temperatura mais alta, esse é um dos problemas do bico quente em alguns materiais.
Autor – A temperatura do bico está em 170°C.
– Não era pra acontecer isso estando o molde na mesma temperatura.
Autor – Não estou usando recalque nessa peça.
– Usando água natural ou gelada?
– Vai diminuindo na câmera quente até sumir as manchas. Tenta abaixar a temperatura da câmera e do cilindro.
– Homogeneizar.
Autor – Também já fiz, não resolveu.
E a temperatura da câmara quente, diminui a temperatura que vai sumir a mancha
– Acredito que a temperatura da unidade móvel deva estar muito quente, esse material dependendo da espessura da sua peças uns 190 graus.
– Diminui a temperatura da câmara quente
– Talvez a temperatura no bico ainda muito quente, acabada transpassando pela parede da peça fazendo com que não dê tempo de resfriar a parada. Já tive o mesmo problema. As vezes seria melhor, fazer uma meia lua por traz da peça para que a injeção não vá direto na parede (macho) do produto.
– Ali é o ponto de injeção?
Autor – Isso mesmo, a mancha é em forma circular.
– Provável que esteja injetando no recalque, tenta diminuir a velocidade de recalque.
Autor – Não estou usando recalque.
– Tenta alterar descompressão traseiro ou recalque, me parece também que tem umas ondas, melhora com mais temperatura.
Autor – Se aumentar a temperatura do bico começa a queimar.
– Diminui temperatura, câmera quente.
– Verifique o resfriamento no molde. Os canais podem conter incrustações que estreitam a passagem de água.
– Provavelmente vai ter que mexer no dimensional do bico (bucha do molde).
– Faz um rebaixo mais ou menos no diâmetro de uma moeda na espessura de 0.50 na direção do bico de injeção morrendo a zero para direcionar o fluxo.
– Sugiro trabalhar com água quente no molde, principalmente lado fixo e injetar com perfil de injeção começando com velocidade bem baixa e aumentando gradativamente. Correto também seria injetar por posição e usar o recalque na peça.
– Já tive esse problema algumas vezes em peças para eletrodomésticos (linha branca).
– Tenta diminuir a velocidade e pressão de dosagem (deixa carregar quase próximo do final do tempo de resfriamento).
– Isso é saída de gás colocar água só na parte móvel do molde.
– Material parece que não foi estufado, outra coisa PSAI a temperatura e de 230ºC para cima.
Autor – Se eu usar esta temperatura de 230ºC não tiro uma peça boa, porque amarela tudo e a mancha que eu me refiro parece ser diferença de temperatura.
– Abaixa temperatura do bico, está muito quente.
– Segura no recalque somente com um tempo maior, depois de abaixa a temperatura do bico e se não resolver dá uma olhada se o direcionador do bico parece que não está funcionando ou está pequeno dá uma descompressão no final da dosagem também ajuda só não pode ser muito, pois pode causa outro problema então vai aos poucos.
– Analise o master, as vezes ele está degradando e veja se não está com muita sobra de colchão.
Falta de brilho – Material PSAI
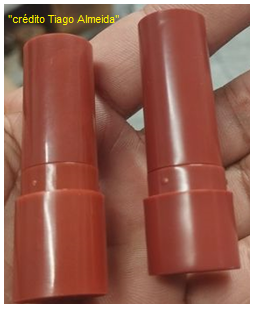
Autor – Peça injetada em PSAI com 2% de pigmento marrom. Mandamos fazer polimento para obter brilho mais não conseguimos um bom resultado. A peça da direita é a nossa e a da esquerda do concorrente, dá para ver a diferença do brilho.
Comentários:
O material está bem estufado e livre de umidade? Tem que ver o molde se está bem polido e espelhado.
Já tive casos em que acrescentei P.S cristal, em torno de 15 a 30%, isso vai depender do seu tipo de produto, porque tem casos que a peça fica quebradiça, acho que vale a pena testar.
Adicionar uma porcentagem de PS Cristal.
Se o molde está espelhado, deve estar injetando devagar ou o molde está muito frio.
PSAI normalmente não tem alto brilho.
Caso não possa adicionar PS Std (cristal) para melhorar o brilho as opções seriam:
1. Polir (espelhar) o molde.
2. Aquecer o molde no limite da transição vítrea do PSAI (em torno de 70 ºC).
3. Procurar por um “grade” de PS médio impacto com menor teor de borracha e com maior brilho.
4. Se possível substituir o PSAI pelo ABS.
A primeira opção vai ser a mais eficaz, mesmo o material não tendo muito brilho com o molde espelhado vai resolver o problema.
Polimento no molde ou PSAI cristal.
Os pigmentos que está utilizando, são óxidos ou anilinas?
Tem que ser anilinas, e pede para seu fornecedor qual a temperatura que resiste a anilina dele, sem manchar e informa a temperatura que está utilizando, para que forneça uma anilina para temperatura maior do que estiver utilizando no molde.
Adicione Stirolux que ajuda no brilho e no problema da quebra.
Como que está o espelhamento do molde, todo o material por si só solta uma micro partículas de resina e interfere na qualidade da peça, experimenta fazer uma limpeza no brilho do molde com a pasta de polir blend não é caro, passe com alguma flanela de algodão.
Já trabalhei com ps rc600 em peça branca. E onde o molde era polido dava brilho.
Tente aumentar a temperatura da resina e do molde fechando a circulação da água ou adicionando um controlador de temperatura, até o ponto que assegure à qualidade e não comprometa a produtividade. Acho válido verificar a questão do polimento da cavidade, tem que estar bem polida para dar brilho, injeta com uma velocidade decrescente. Acho que todos os comentários acima podem agregar em algum ponto para melhorar.
Você pode fazer um teste com PSAI alto brilho, pois a peça padrão pode ter sido injetada com grade. O custo dele é maior do que o PSAI convencional.
Um bom polimento ou espelhar, e aumentar a velocidade de injeção. Essa peça me parece ser a base do Baton já trabalhei com essa peça em uma empresa chamada IPEL. Os moldes eram todos espelhados.
Fazer uma blenda, 70% ABS 30% San, aumentar a temperatura do molde, outra possibilidade é verificar com o fornecedor de masterbatch se tem alguma carga mineral, geralmente o carbonato de cálcio entre outras cargas tendem a deixar uma certa opacidade no masterbatch, isso também irá impactar no brilho da sua peça.
Verificar o espelhamento das cavidades e vai aumentando a temperatura da massa, do bico para trás, decrescente, a velocidade também tem que ir aumentando!
Se poder injeta em ABS com molde aquecido que vai conseguir bastante brilho na peça.
Usar PS cristal Stander depois adicionar pigmento.
O PSAI devido a presença de elastômero tende a ser mais opaco.
O que pode ser feito é acrescentar PS cristal em mistura com o PSAI.
Verificar sempre a resistência ao impacto, pois com o aumento do PS cristal a resistência ao impacto diminui.
Faça aos poucos, começando com 10% de cristal.
Aumente a temperatura da refrigeração do molde
O produto é o reflexo da cavidade do molde, portanto o mesmo precisa estar espelhado para mostrar esse brilho que espera.
Mas para ajudar na situação atual, experimente colocar / aumentar a contrapressão, compactando a massa e melhorando assim a plastificação. O molde quente também irá ajudar no resultado (70 ºC a 80 ºC), porém isso elevará um pouco o ciclo.
Lembre-se também que, quanto mais pressão de injeção e de recalque, mais o produto mostrará as imperfeições e detalhes da cavidade. Portanto, se o molde não estiver espelhado, procure trabalhar com o mínimo de pressão e recalque… Comece apenas com o suficiente para encher a cavidade.
Peça com linha de junção – Material PSAI
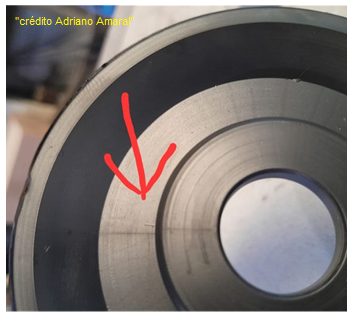
Autor: Começamos a injetar essa roldana em PSAI e está saindo com essa trinca.
Comentários:
Para mim isso é flow lines, o material precisa ser injetado mais rápido para fazer uma melhor união quando as duas frentes de unem.
Autor – Linha de fluxo, junção. Temperatura 270 ºC.
Efetuar saída de ar, nesse ponto da linha de emenda ajudaria a minimizar esse defeito.
Emenda fria, faça saída de gás no molde ou injeta mais lento.
Esse tipo de emenda fria é possível suavizar, com as ações acima, mas eliminar não, você só conseguirá eliminar essa junta fria de uma forma!
Fazendo um posso frio no sentido dá junta para o processo eliminar o material mal emendado.
Observe se o defeito aparece antes de extrair a peça, pode estar trincando por conta da extração
Autor – Pessoal, sai de 270 ºC para 300 ºC e melhorou bastante, porém continua um capilar bem fininho em meia a peça…vou continuar insistindo.
Isso acontece antes de extrair ou quando extrai veja isso abre o molde e não deixa extrai.
Autor – Antes de extrair.
Autor – Injetava em Nylon e PP, não tinha esse problema.
Isso é emenda fria, saiu da temperatura de 270 ºC para 300 ºC, é muito alto, não vai adiantar muito, pois para esse material é ideal trabalhar com ciclo rápido, para que o molde aqueça, se estiver trabalhando com água gelada na parte móvel é melhor mudar para industrial, fazer um poço no final dessa emenda. Terá uma pequena mão de obra, terá que fazer acabamento com rebarbador, a temperatura para esse material 250 ºC é o suficiente, dependendo do tamanho e peso da peça e máquina.
Deixa o molde mais quente, PSAI pede molde com aquecimento em torno de 40 ºC a 50 ºC, tenta água industrial sem o chiller.
Junta fria, tem que trabalhar com o molde mais aquecido.
Acabamento da peça opaco e borra com brilho – Material PSAI

Autor – Testando uma peça em PSAI, mas está saindo opaca e a borra com brilho. Que fazer, o molde é espelhado.
Comentários do grupo:
Umidade no material, tenta colocar em uma estufa mais ou menos 4 horas a 100 °C.
Já tentou aquecer o molde para ver.
Tenta injetar ABS preto com SAN, molde aquecido 60 ºC vai dar um brilho top.
Autor – San preto também ou incolor, qual a porcentagem de mistura?
SAN virgem começa com uma porção menor na receita 70% ABS preto e 30 de SAN virgem.
Autor – E qual temperatura de processo que recomenda.
Faz uma rampa crescente, começa com 230 ºC e vai até 270 ºC e injeta rápido para não marca o fluxo na injeção.
Autor – Vou fazer isso vou e ver como fica.
Já tive o mesmo problema e com esse mesmo material e não consegui fazer sair com brilho, me disseram para fazer micro texturização, mas como não era necessário o brilho trabalhamos assim mesmo.
Acho que termorregulador resolve.
Qual temperatura está usando?
Autor – Comecei com 230 ºC no bico e 10 ºC a menos por zona na quinta zona com 200 ºC.
Aquecer o molde na parte fixa onde provavelmente seja sua parte espelhada, ajudará muito, 70 °C é o suficiente para adquirir o brilho.
Seca bem o material, e coloca água aquecida.
Sabe que o PSAI é opaco, ele não vai dar brilho na peça, já o PS cristal esse sim tem brilho.
Isso é falta de temperatura.
Tem que aquecer o molde a mais de 60 ºC no lado espelhado, provavelmente o fixo, o PSAI é difícil para abrir brilho, tenta colocar na mistura uns 15% de PS cristal, vai ajudar.
Aumentar a temperatura do lado fixo, mínimo 60 °C.
Marcas de fluxo em diversos pontos – Material PSAI

Autor: Injetando peça em PSAI virgem. Como eliminar estas marcas de fluxo, na entrada dos submersos e na junção do fluxo.
Comentários do grupo:
Na junção do material pode ser gás, tenta fazer a saída que vai ajudar.
Pode ser velocidade de injeção ou tente aumentar a temperatura para o material ficar mais fluido.
Baixa a pressão.
Temperatura do molde pode estar baixa dificultando a fluidez e esfriar o material, temperatura do material injetado aumentar um pouco, velocidade de injeção alta (lenta) deverá ser o máximo possível. Diâmetro do ponto de injeção muito pequeno. (aumentar).
Experimente usar bico de 3 furos, ajustar velocidade de injeção, temperatura do cilindro.
Limpeza de escapes interiores e exteriores. Antes de efetuar abertura dos escapes pode experimentar colocando uma fita de cola entre janelas de escape para ver se ajuda na resolução.
Peça saindo com manchas do tipo rajados

Problema: peças estão saindo com rajados.
Já estufei o material, já abaixei temperatura, pressão, tirei descompressão, nada adiantou, aumentei a temperatura e nada de subir. Já testei outros 3 materiais e deu o mesmo problema. Material PSAI – Poliestireno de Alto Impacto.
Comentários:
– Quantas horas esse material ficou na estufa e a que temperatura? Essas manchas são de umidade, ou talvez velocidade muito alta.
Autor – O material é PSAI e foi estufado durante 4 horas a 60 graus. Está saindo rajados no galho, descarga do canhão está saindo igual EVA cheio de furo, matéria prima moída, já fiz até um bico de injeção novo, e o mesmo acontece em outros moldes.
– Estufa a 80ºC vai melhorar. Só dá uma cuidada para não embolar o material.
– Pode aumentar a temperatura do material.
– O moído pode estar com pó. Tem que peneirar. A temperatura não é 60º C é 90ºC. Quando injetar manda o mais rápido que poder.
– Esse material necessita 6 horas de secagem e tem que trabalhar com ele quente, ideal um funil térmico.
– Material deve estar contaminado. Ou a máquina está com vazamento de a água no pé da rosca. Faça uma correção porque já aconteceu comigo!! Se estive usando refrigeração no pé da rosca retire e observe se vai melhorar o aspecto das peças.
– Pode ser que o grão do material está com umidade da extrusão, muito difícil solucionar o problema, só com outro.
– Umidade, quantas hora está deixando esse material na secagem.
– Tem que ver se não há vazamento de água na garganta. Já tive esse problema de vazamento de água na garganta. Basta pingar.
– Esse tipo de rajado é chamado de metalização e ocorre com ponto de injeção muito estreito, velocidade de injeção muito alta e temperatura da câmara quente muito baixa. Faz um estudo para adicionar mais um ponto de injeção, para auxiliar no preenchimento da peça. Diminui a velocidade de injeção e aumenta a temperatura da câmara quente.
– Se for Material industrial moído é complicado pode ter contaminação com itens que tenham carga mineral ou já sofreu degradação térmica, até excesso de pigmentos faz isso.
– Dependendo a matéria prima tem que secar corretamente se for ABS no mínimo 4 horas.
– É uma característica de material com umidade. Está deixando o tempo correto do material utilizado?
– Veja as saídas de ar no molde também.
– Difícil, embora tenha bastante informação, ainda é pouco. Matéria prima e a primeira coisa que tem que analisar, bico obstruído, velocidade de injeção, compactação, mas me parece umidade ou bico obstruído.
– Todos os comentários são importantes, no entanto, se já estufou o material tentaria no processo usando um perfil temperatura, averiguar o diâmetro do bico da máquina, perfil de dosagem e contra pressão baixo aumentando gradativamente para expulsar os gases do material. Se é PSAI, não usa muito contra pressão, perfil de injeção baixo aumenta gradativamente, porém tenha muito cuidado na hora de escalonar as posições de injeção, outro ponto muito importante não usa descompressão muito alta nem pressão e velocidade.
– Primeiro a secagem de material depois, aumenta o canal de injeção deve ser muito pequeno. Diminuir a velocidade de injeção. Acredito que já vai resolver.
– O gate pode estar obstruído ou estrangulado. Porém se trocar o bico de injeção por um com furo um pouco maior, também pode resolver.
– Parece umidade no material ou bico obstruído. ABS e PSAI são clássicos.
– Verificar o bico, pode estar com alguma sujeira. Tipo pedaço de latão.
– O que pode ocasionar também é a refrigeração, tem que ser natural não gelada, isso aí no pé da rosca, também.
– Já verificou as resistências da máquina, o diâmetro do bico também pode causar esse tipo de defeito.
– Depende, é necessário avaliar o conjunto molde x máquina x matéria prima. Tempo de estufagem do material, aquecimento/refrigeração do molde, se a estufa está realmente absorvendo a umidade do material, polimento do molde, diâmetro dos gates.
– Umidade no material, velocidade de injeção, molde muito frio.
– Pode ser velocidade muito alta, poder ser umidade também, pode ser saída de gás, pode ser temperatura muito alta. A bucha do molde está correta com o bico do canhão?
– Material sem estufar, molde frio, muito recalque essas são algumas opções.
– Provavelmente a velocidade de injeção está muito alta, já ajustou esse parâmetro?
– O problema deve estar no molde (frio ou quente demais)
– Abre mais a entrada de injeção.
– Parece ser material com umidade, essa resina está sendo estufada em silos ou desumidificador?
– Isso está com cara de umidade.
– Trocou 3 vezes o material e não resolveu, complicado isso é umidade, ou estufagem do material com temperatura baixa.
– E como está o furo do bico, grande pequeno ou tem ferro.
– Pode ser molde isso. Tem saída de gás?
– Parece umidade de uma checagem.
– Temperatura ambiente.
– Colocar absorvedor de umidade tá resolvido o problema.
– Coloca uns 4% de dessecante.
– Material com umidade.
– Se já trocou o material 3 vezes, já estufou e mexeu no processo, agora seria legal dar uma olhada na refrigeração da garganta do canhão. Se tiver vazando, mesmo que pouco nada mais vai resolver a não ser fazer o reparo. Não tá normal isso aí. A marca de material úmido é muito grande para ser problema de estufagem ou processo.
– Contudo verifique, se o material moído tiver muito pó, também não vai adiantar fazer outras coisas.
– Tente aumentar o diâmetro do bico e consequentemente aumenta a fluidez.
– Velocidade de injeção e tempo de injeção, já olhou também.
– No PSAI aumentamos a contrapressão e o bico com um furo maior, quando pega ciclo também melhora um pouco.
Marcas de rechupe – Material TPU
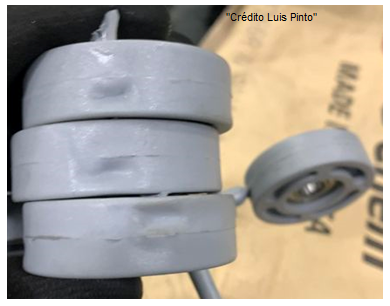
Autor – Peças saindo com rechupes demais. Material TPU shore
Comentários:
TPU é um elastômero, portanto, requer um tempo de recalque elevado, preencha o produto sem recalque até encontrar o volume da injeção, depois disso, entre com e recalque a 70% da injeção por um tempo maior, pode até diminuir o tempo de resfriamento para compensar o ciclo. Quanto mais tempo de recalque, maior o ganho no dimensional do produto.
Compacta mais, velocidade baixa, + recalque, pode ser pouco resfriamento, caso ele vá rechupando conforme esfrie.
TPU 45 shore? Se for isso mesmo, só conseguirá resolver com expansor média de 1% e tempo de resfriamento em torno de 70 segundos e recalque também longo, procurar expansor na empresa (Aditive Plásticos Ltda SP).
Coloca 2% de agente expansor no material para cada quilo que ajuda tirar a chupagem.
Sugiro baixar a temperatura de canhão, alta só no bico e se puder colocar um pouquinho de expansor vai ajudar no teu processo. Compactação e velocidades de injeção também são fundamentais no TPU.
Isso só vai melhorar com agente de expansão, azodicarbonamida ou talvez um agente nucleante. Adicionar agente expansivo.
Para resolver problema de chupagem primeiro passo é regular a máquina como pressão, recalque, temperatura e tempo de saída ar que fica o ar preso no molde. Se por acaso não resolver, existe ó expansor que coloca no material. O material pode ser PP. PE. ABS. NAYLON. Qualquer tipo ele resolve.
Primeiro uma boa desmistificação, manter quente e seco no funil, alta pressão no recalque e tempo depende do teu resfriamento do molde, velocidade de injeção de média para baixa, temperatura de injeção que não degrade o material, pois o tempo é um pouco alto e o material fica parado no canhão. E com todas as dicas, não coloque expansor, se não resolver chame um técnico que fornece o TPU.
Atenção que os expansores deixam o material poroso no interior.
Velocidade baixa, velocidade de contrapressão baixa, temperatura baixa, a água não pode estar muito gelada no molde, depois que a peça completou entra com recalque, velocidade do recalque baixa também para não dar queima.
Se não for possível, tem de tentar melhorar as saídas de gases, podes experimentar tirar força de fecho ao molde e injetar com velocidade média alta, logo depois de encher as cavidades entras com a segunda pressão (recalque) bem alta até que apareça rebarba e tenha desaparecido os chupados.
TPU é para sobre injeção, a roda pode ser de pp h503.
E só verificar o curso que está sobrando de colchão, se não está zerado ou com pouca carga de dosagem. Se tiver entre 0 a 5 dá para aumentar o curso.
Depois vai aumentando a força de fecho aos pouquinhos até a peça ficar sem rebarba e chupado.
O tempo e segunda pressão (recalque) devem ser altos, temperatura do molde o mais baixa possível.
Abaixar a velocidade da rosca, pois a velocidade alta aumenta a temperatura interna do cilindro, não correspondendo com a temperatura programada.
É bom conferir se o material não está retornando pelo anel de bloqueio também.
Primeiro verificar a capacidade da sua injetora e depois verificar se não está usando muito material moído próxima etapa ver bico de injeção se não está obstruído se tiver tudo ok aumentar tempo de injeção.
Injeta com velocidade de injeção mais baixa o possível para que saia o ar da cavidade, também verificar se a saída de ar no molde está correta.
Você já cortou uma peça para ver como está a interna dela?
O molde pode estar muito gelado, isso ajuda a dar chupagem.
Aconselho a que aumentem o funil do jito ou galho que me parece de 6 mm, para pelo menos 8mm, e aumentar o ataque a peça em 0,5mm por banda.
Gate muito pequeno também pode ser problema.
Aumentar pressão e velocidade de injeção…fazer pegar posição de recalque aumenta tempo de recalque e resfriamento dosagem contrapressão.
Recalque diminui a velocidade de injeção.
Tenta segurando tempo de injeção ou recalque tempo mais alto.
Diminua a velocidade de injeção e aumente o tempo de injeção e recalque.
Aumentar o tempo de recalque, e pressão de recalque, se não conseguir vai ter que aumentar o canal de injeção, para o material fluir melhor.
Se o recalque e a velocidade baixa não resolver, tira um pouco do travamento.
Tempo de injeção e recalque baixos ou até falta de carga. Pode ser tempo de resfriamento também.
Primeiro zerar pressão de recalque e tempo aí injetar até completar a peças, aí então dar uns 20 bar de recalque e 3 segundos de tempo, aí se precisar alimentar um pouco mais até ficar boas as peças.
Talvez tenha que aumentar a dosagem, pode estar com pouco colchão, pode estar com tempo de injeção muito baixo é só aumentar um pouco, tempo injeção e recalque.
Esse tipo de material e peças se deve completar com recalque para retirar o rechupe.
O TPU exige bastante tempo de recalque em paredes grossas.
Diminua a velocidade de injeção e aumente o tempo de injeção e recalque.
Autor – O recalque ajudou.
Peças aderindo ao molde – Material TPU
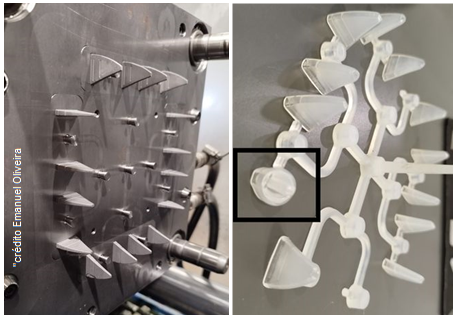
No teste de um molde com material TPU por vezes algumas ficavam presas no macho.
Comentários:
Verifique polimento, saída de ar e depois refrigeração do molde.
Polimento ajuda e um pouco mais de tempo de refrigeração também, mas percebi que tem um desenho em baixo relevo no extrator, verifica isso também
Verifique primeiro o polimento da cavidade, depois ângulos de extração do molde e tempo de resfriamento.
Tenta polir, se não dar certo manda por teflon em todos machos, vai melhorar a produção.
Tenta fazer um bom polimento de saída.
As peças não preencheram todas de um tempinho e mais de resfriamento.
Autor – Aumentando a refrigeração ficam presas na cavidade.
Nada complicado passa um WD.
Se caso não resolver com as dicas de melhoramento no molde, existe desmoldante próprio para TPU.
Muita pressão ou recalque ou pouco resfriamento.
Já tem garra suficiente no macho pode ser isto.
Primeiro de tudo é verificar se os postiços a qual a peça está ficando agarrado no molde, tem alguma carga negativa ou positiva. Depois caso esteja tudo normal, procure ajustar o tempo de resfriamento e a velocidade de extração da peça.
Mancha junto ao ponto de entrada – Material ASA
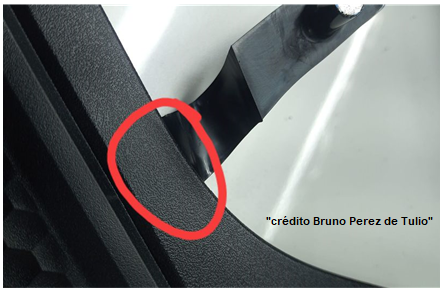
Autor – Mancha peça próximo a entrada de material. Alguém já trabalhou com material ASA?
Comentários:
Já tive este problema com várias peças. Isso não é gás é turbulência do material na entrada da cavidade.
Tenta diminuir a velocidade de injeção neste ponto aí, entra com o material mais devagar e depois que passar deste ponto coloque a velocidade de injeção normal para preenchimento da peça.
Temperatura na parte da textura mais ou menos 80 ºC.
Autor – Está peça está saindo com está mancha na entrada do galho.
Injeta em perfil com início da injeção mais lenta.
Autor – Mudei a refrigeração do canal também nada.
Isso é falta de saída de gás (fica preso por causa do encontro de massa,)…nada mais que isso .molde com Textura o material dificulta a saída dos gases….isso acontece , falta escape.
A princípio a textura é para disfarçar qualquer anomalia na peça que não possa ser corrigida, por alguma nervura de massa maior, esse ponto da injeção pode ser excesso de recalque, velocidade alta no início da injeção, verifica se não pode ser saída de gás.
Vejo que o molde é de uma textura mais grossa, verifica as saídas de gás e baixa a primeira velocidade de injeção.
Qual é o seu problema? Específica melhor.
Autor – Esse ponto escuro na entrada do galho para a peça.
Este ponto fosco ou escuro da peça pode ser muito recalque, diminui um pouco da pressão de recalque se estiver usando, porque pode estar compactando muito, depois da peça já preenchida vai ficar está mancha.
Tem que ter mais tempo
Autor – Coloquei mais tempo, porém a mancha persisti.
Autor – Tentei com início de injeção devagar depois mais rápido.
Autor – Melhorou a mancha colocando ar comprimido direto no ponto resfriando enquanto a peça fica na esteira aguardando.
Atualizado em 17/01/25
Fonte: Grupos Técnico em Plásticos e Injeção Plástica do Facebook
Apenas Resumo: Moldes Injeção Plásticos
Esperamos ter colaborado com os profissionais!
ACESSE: Isso também irá facilitar o trabalho do profissional