
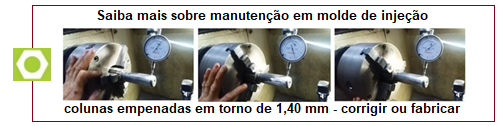
Tecnologia de moldagem do PVC por injeção
O processo de moldagem por injeção é uma técnica de moldagem do PVC que consiste basicamente em forçar, através de uma rosca pistão, a entrada do composto fundido para o interior da cavidade de um molde. Após o resfriamento da peça, a mesma é extraída e um novo ciclo de moldagem ocorre. Produtos típicos de PVC obtidos por meio de moldagem por injeção são conexões, alguns acabamentos de perfis, solados de calçados e peças técnicas diversas.
No caso do PVC dois aspectos são de especial importância: plastificação e preenchimento do molde. Isso porque o PVC apresenta tendência a se decompor quando exposto às temperaturas de fusão por períodos de tempo relativamente longos e também devido à alta viscosidade do fundido, o que exige equipamentos que permitam a aplicação de pressões de operação superiores às normalmente exigidas por outros termoplásticos.
Do ponto de vista tecnológico, o comportamento de fluxo de resinas puras apresenta pouco interesse, já que a resina de PVC só é processável quando composta com aditivos. A utilização de resinas de menor peso molecular, ou seja, menor valor K, tende a reduzir a viscosidade do fundido. Aumentos de temperatura também reduzem a viscosidade do fundido, porém são limitados em função da estabilidade térmica do composto e do tempo de residência do material fundido na máquina.
Aditivos que melhoram a processabilidade do composto tais como lubrificantes internos e plastificantes geralmente reduzem a viscosidade do fundido e diminuem a temperatura de fusão; auxiliares de processamento, por sua vez, trazem benefícios por aumentar a resistência do fundido. Lubrificantes externos podem proporcionar ganhos de fluxo, mas tendem a prejudicar a fusão do composto e, quando utilizados em excesso, podem gerar defeitos superficiais no moldado. Cargas, pigmentos, retardantes de chama e supressores de fumaça são na maioria sólidos que, quando utilizados em altas concentrações, sempre aumentam a viscosidade do fundido.
Compostos flexíveis de PVC apresentam sempre menores dificuldades de moldagem em relação aos compostos rígidos, em função da presença de plastificantes, os quais reduzem a temperatura de processamento e a viscosidade do fundido.
Peças técnicas com grande área de moldagem, tais como gabinetes de eletrodomésticos e aparelhos eletrônicos podem ser moldadas a partir de compostos de PVC rígido especialmente formulados para essas aplicações. Em geral esses compostos são formulados a partir da mistura de resinas de PVC de alta fluidez, com valor K da ordem de 50, em mistura com resinas de PVC convencionais. Para compensar a baixa resistência ao impacto inerente a essas formulações em função da resina de menor peso molecular, são necessárias grandes quantidades de modificadores de impacto e auxiliares de processamento. Ganhos em fluidez também são maximizados pela utilização de lubrificação interna adicional, sempre tomando as
devidas precauções para não reduzir excessivamente a temperatura de amolecimento diante do calor do composto.
Equipamentos e processo :
A injeção de produtos de PVC faz uso de equipamentos convencionais de moldagem do tipo rosca-pistão. Esses equipamentos possuem, dentro do cilindro de plastificação, uma rosca sem fim semelhante à descrita e utilizada no processo de extrusão com rosca única. A diferença básica entre os processos é que, no caso da injeção, a rosca possui em seu final um anel de bloqueio que permite a passagem do composto fundido no momento da dosagem e impede seu refluxo no momento da aplicação da pressão de injeção
A figura 01 mostra o esquema de um conjunto de injeção.
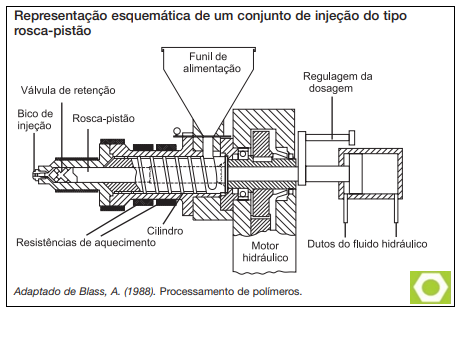
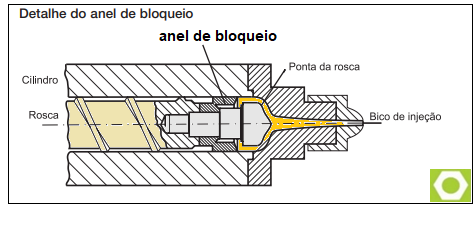
Figura 02 – Detalhe do anel de bloqueio
No passado era comum a utilização de injetoras a pistão que, devido à baixa eficiência de plastificação do composto, caíram progressivamente em desuso com o desenvolvimento das máquinas dotadas de sistema rosca-pistão. Esse sistema é extremamente eficiente para a plastificação do composto, uma vez que a rosca exerce forte ação cisalhante sobre o mesmo, permitindo eficiente plastificação e homogeneização da massa antes da injeção do composto fundido para o interior da cavidade do molde.
O acionamento da rotação da rosca é feito por meio de motores elétricos ou hidráulicos. Já o movimento linear necessário para a injeção do composto fundido para a cavidade do molde é conseguido normalmente por meio de atuadores hidráulicos, porém existem no mercado injetoras de acionamento totalmente elétrico, sendo essas últimas normalmente utilizadas em ambientes assépticos para injeção de peças técnicas ou hospitalares, nos quais não se pode tolerar a presença do fluido hidráulico por se tratar de um contaminante eventual.
Produtos como conexões e uma série de peças técnicas rígidas e flexíveis são moldados em injetoras convencionais, dotadas de uma unidade de fechamento do molde (prensa), com acionamento hidráulico ou elétrico, na qual faz-se a montagem do molde, e de uma unidade de injeção. Parâmetros importantes para a seleção de uma máquina injetora são a força de fechamento do molde, que pode variar na faixa de 30 a mais de 1.000 toneladas, a área útil entre placas (correspondente ao máximo tamanho de molde que pode ser montado na máquina), a capacidade de injeção em volume de composto e a capacidade de plastificação do conjunto injetor.
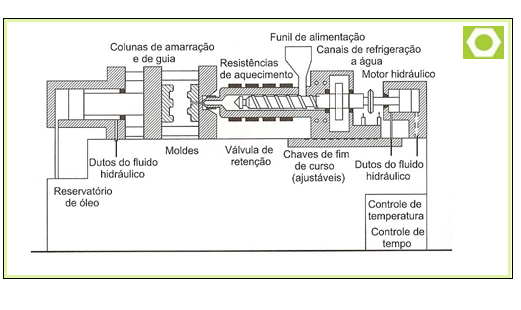
Figura 03 Representação esquemática de uma injetora convencional .
O processo de moldagem por injeção pode ser descrito implificadamente em seis etapas, que constituem o chamado ciclo de injeção:
Fechamento do molde: O ciclo de moldagem é iniciado pelo fechamento e travamento do molde, necessário para suportar a altíssima pressão no interior da cavidade no momento da injeção.
Dosagem: Plastificação e homogeneização do composto no cilindro de injeção, conseguidas por meio do movimento de rotação da rosca recíproca e de aquecimento do cilindro por resistências elétricas.
Parâmetros importantes na etapa de dosagem são a temperatura do cilindro, a velocidade de rotação da rosca e a contrapressão da rosca. Maiores velocidades de rotação da rosca promovem maior cisalhamento e homogeneização do composto, porém com maior solicitação térmica, o que pode comprometer a estabilidade do mesmo. O mesmo vale para a contrapressão da rosca, que nada mais é do que a pressão exercida na traseira da rosca de modo a dificultar seu recuo no momento da dosagem. Quanto maior a contrapressão, maior o cisalhamento e homogeneização do composto, bem como maior a solicitação térmica do mesmo.
Injeção: Como o próprio nome indica, trata-se da injeção do composto fundido para o interior da cavidade (ou cavidades) do molde por meio do movimento linear de avanço da rosca recíproca e bloqueio do contrafluxo pela ação do anel de bloqueio.
Parâmetros importantes nessa etapa são a pressão e a velocidade de injeção, sendo que ambas podem ser escalonadas para promover o preenchimento uniforme das cavidades.
Outro aspecto importante diretamente relacionado à etapa de injeção refere-se aos canais de injeção e aos pontos de injeção das cavidades do molde. É através dos canais de injeção que o composto fundido chega às cavidades do molde, sendo que o ponto de entrada do composto é conhecido como ponto de injeção. Os canais de injeção devem ser dimensionados de forma a permitir o fluxo do composto fundido com a mínima perda de pressão. Os pontos de injeção, por sua vez, devem ser dimensionados e posicionados de modo a permitir o preenchimento uniforme da cavidade, com a menor incidência possível
de defeitos superficiais. Pontos de injeção extremamente restritos podem provocar excessivo cisalhamento do composto, podendo acarretar até mesmo degradação térmica por causa do aquecimento induzido pelo atrito.
A figura 04 mostra diversos tipos de pontos de injeção utilizados na moldagem do PVC.
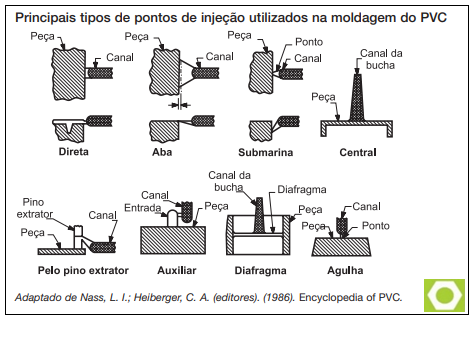
(d) recalque: finalizado o preenchimento das cavidades, a pressão nas mesmas é mantida até a solidificação completa dos pontos de injeção. Essa manutenção da pressão nas cavidades é conhecida como recalque, e se destina a compensar a contração da peça moldada durante seu resfriamento, evitando a ocorrência de defeitos de moldagem como os chamados “rechupes” e outras imperfeições, bem como perda de parâmetros dimensionais. Uma regra básica define que a dosagem
deve incluir um volume entre 5 e 10% maior que o necessário para o completo preenchimento do molde, de modo a permitir a aplicação de pressão pela rosca sobre a massa uma vez preenchida a cavidade, sendo essa pressão normalmente cerca de 75% do valor da pressão de injeção.
(e) resfriamento: finalizada a etapa de recalque, a peça é mantida no molde fechado para complementação de sua solidificação.
Paralelamente à etapa de resfriamento sem aplicação de pressão na cavidade, o processo inicia um novo ciclo de dosagem de composto para a próxima injeção. O resfriamento prossegue até que a peça moldada apresente resistência mecânica suficiente para poder ser retirada do molde sem sofrer deformações ou perda de parâmetros dimensionais.
(f) extração: encerrada a etapa de resfriamento o molde é aberto e a peça extraída por ação de extratores mecânicos ou, mais comumente, hidráulicos ou elétricos. Alguns produtos podem ser extraídos com o auxílio de ar comprimido ou pela simples interferência do operador da máquina injetora.
O ciclo de moldagem é então reiniciado por um novo fechamento do molde e etapas posteriores.
Com relação ao molde de injeção vale comentar que cada peça a ser moldada requer características específicas de projeto das cavidades, canais e pontos de injeção, posicionamento de pinos extratores, utilização de placas adicionais, machos e gavetas (principalmente no caso de conexões). Normalmente os moldes são resfriados pela passagem de água por serpentinas usinadas nas placas. Com relação ao material de confecção dos moldes, dá-se preferência pela utilização de aço nas placas de montagem e aços-liga nas placas das cavidades, muitas vezes cromadas para maior durabilidade. Para produtos de baixa escala de produção utiliza-se eventualmente o alumínio e suas ligas para a confecção dos moldes pelo menor custo do metal e de sua usinagem.
Calçados moldados em composto de PVC flexível expandido normalmente são injetados em máquinas rotativas, nas quais um ou mais conjuntos de injeção injetam continuamente material em moldes dispostos em um carrossel. Esse processo de injeção demanda tempos de resfriamento normalmente demorados em função do grande volume das peças moldadas que, para não limitar a capacidade de injeção do processo e conseqüentemente sua produtividade, fazem da rotação dos moldes uma alternativa para melhor aproveitamento da capacidade da máquina. O carrossel possui normalmente entre quatro e dezesseis porta-moldes que alternadamente são posicionados em frente ao conjunto de injeção para preenchimento da cavidade. Uma vez preenchido o molde, o carrossel substitui a estação em frente ao conjunto de injeção e o molde preenchido passa por todo seu ciclo de resfriamento e extração da peça moldada, até o posicionamento para um novo ciclo de injeção. Equipamentos desse tipo podem ainda incluir mais de um conjunto de injeção em outras posições do carrossel,
permitindo a injeção de peças formadas por mais de um tipo de composto ou até mesmo de material, ou seja, peças de múltiplas cores e durezas.
A figura 05 mostra esquematicamente uma máquina injetora rotativa.
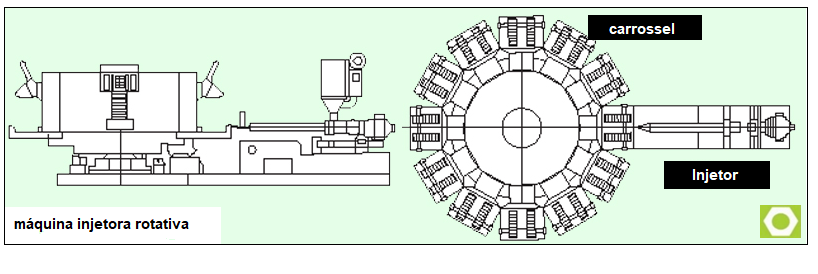
Figura 05 Representação esquemática de uma injetora rotativa
Publicado em 11/06/2017
Fonte: Tecnologia do PVC – 2ª Edição nov. 2006 Braskem
Veja mais em: INDICAÇÕES PARA O PROCESSAMENTO DE DIFERENTES MATERIAIS PLÁSTICOS – 2