
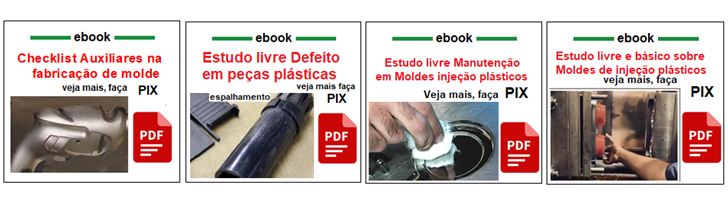
Este site é um Informativo. Precisamos de suporte para custear Atualizações e Melhorias. De apoio a nosso trabalho. Divulgaremos sua empresa como apoiadora.
Moldagem, Ciclo e Etapas de Moldagem
Conhecendo a injetora horizontal e ciclo
Fases do processo de moldagem
A palavra plástico significa capaz de ser moldado.
Os materiais plásticos são naturais ou artificiais, de origem orgânica, e podem ser moldados quando submetidos a determinadas condições. Seu componente básico é a resina, que pode ser classificada em termoplástica e termorrígida. Na moldagem das resinas termorrígidas, os componentes são misturados no molde ou na máquina e o endurecimento ocorre por meio de reações químicas, chamadas de reações de cura.
Na moldagem das resinas termoplásticas, a resina é plastificada (amolecida) no interior do cilindro pela rosca e injetada neste estado no molde. No interior do molde, ela é solidificada por meio de resfriamento e, portanto, não ocorrem reações químicas. As resinas termoplásticas tornam a moldagem simples e rápida por não sofrerem reações químicas durante a moldagem. Elas são utilizadas para produção de artigos de forma geométrica variada, suprindo, eficaz e economicamente, requisitos funcionais diversos. O método clássico de conformação das resinas termoplásticas é a chamada moldagem por injeção. Na moldagem por injeção, o material plastificado é forçado para o interior do molde onde, então, sofre solidificação.
Conhecendo a máquina injetora horizontal
A máquina injetora horizontal é composta de uma estrutura, onde estão fixados o sistema de injeção e o sistema de fixação, abertura e fechamento do molde. No interior desta estrutura se encontra o sistema de acionamento hidráulico e o sistema de controle. O sistema de injeção é o responsável pela alimentação, plastificação e injeção do polímero.
Nesta unidade o polímero é alimentado pela tremonha ou funil até o cilindro de plastificação. No interior do cilindro de plastificação encontra-se a rosca e no exterior as resistências de aquecimento, subdivididas em diferentes zonas. A plastificação do polímero ocorre no interior dos filetes da rosca. O movimento de rotação da rôsca faz com que os grãos de plástico se atritem com a mesma e sofram aquecimento e cizalhamento. Assim, à medida que o material é transportado ao longo da rôsca, ele vai sofrendo a plastificação e vai se homogeneizando.
A rosca é
subdividida em três zonas:
(1) zona de alimentação, em que a altura do filete é constante, devendo o
material ser apenas transportado, não podendo sofrer deformação;
(2) zona de compressão, em que a altura do filete diminui progressivamente e o
material sofre plastificação;
(3) zona de calibragem ou de homogeneização, onde o material já plastificado é
homogeneizado.
A outra função da rosca é avançar para injetar e compactar o plástico no molde.
As zonas de aquecimento do cilindro servem para controlar a temperatura, sendo compostas de resistências elétricas que fornecem calor para compensar as perdas de calor do cilindro para o ambiente, tanto por radiação como por convecção, e para a máquina (por condução). A temperatura de cada zona deve ser regulada de acordo com o material, as características da ferramenta e as características da peça.
O sistema de fixação, abertura e fechamento do molde é composto de uma placa fixa, uma placa móvel, guias das placas (normalmente colunas), pistão hidráulico para abertura e fechamento da placa móvel e pistão do sistema extrator. Neste sistema, a parte do molde que recebe o plástico do sistema de injeção é montada na placa fixa e a parte do molde, por onde normalmente a peça é extraída, é montada na placa móvel. Em cada ciclo, a placa móvel se desloca em direção à placa fixa para fechar o molde, acionada por um pistão hidráulico.
Durante a injeção, a força de fechamento ou travamento do molde precisa ser suficiente para manter as duas faces do molde encostadas. Caso contrário, o material entrará na fresta entre as partes do molde e formará rebarba na peça. O sistema de extração também é acionado por um pistão hidráulico e pode ser movimentado durante ou após a abertura da placa móvel, dependendo das características da peça a ser extraída.
O sistema hidráulico é composto de bomba hidráulica, válvulas, pistões, motor hidráulico e outros. A bomba hidráulica fornece a pressão necessária ao óleo para mover os pistões e o motor. As válvulas recebem sinais do sistema de controle e permitem ou não a passagem de óleo, conforme a necessidade.
A máquina injetora será mais eficiente quanto mais tarefas ela conseguir executar ao mesmo tempo. Ela em essência já representa uma solução única em múltiplas funções, já que não apenas recebe os moldes e a matéria-prima, mas controla todas as variáveis necessárias para o sucesso de cada produção. Essas ferramentas potentes, apesar de versáteis são produzidas para trabalhar com moldes de injeção específicos, personalizados para cada produto que deverá sair do estágio final de produção. É essa especificidade que garante a execução precisa da atividade programada para a produção, com o material e produto que a máquina foi destinada. Essa destinação singular confere desempenho e confiabilidade em toda a sua vida útil.
O controle da temperatura para a fusão do material envolvido na produção é realizado por sensores e controladores existentes dentro da própria estrutura de cada máquina, que enviam às resistências de alto desempenho a quantidade ideal de energia, que finalmente é transformada em calor. É esse processo de superaquecimento das resistências elétricas para máquinas injetoras especiais que torna possível uma injeção precisa e de qualidade.
Fica evidente que durante todo o processo, desde o recebimento da matéria líquida que se transformará através da máquina, até a expulsão do produto final, a máquina injetora é responsável por controlar as variáveis e automaticamente corrigir os erros de produção, inclusive os erros de forma final, que devem ser observados e ajustados. Por isso a escolha dessa máquina não deve apenas levar em consideração as dimensões necessárias para a produção, e sim a procedência do fornecedor a qualidade final do produto.
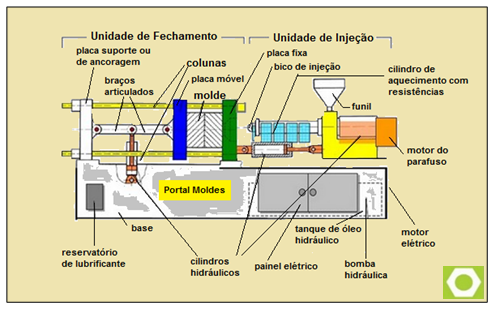
Unidade de Fechamento
A unidade de fechamento é composta por uma prensa, que tem a função de manter o molde fechado durante a transferência da resina para a cavidade do molde, e fazer os movimentos de abertura e fechamento possibilitando a extração da peça. O tamanho da unidade de fechamento será definido de acordo com o tamanho do molde, e a de força de fechamento exigida pela peça. As máquinas mais utilizadas no mercado podem variar de 50 até 3000 toneladas de força de fechamento.
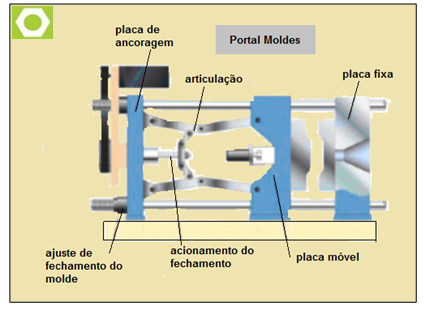
Dependendo da tecnologia, a máquina poderá ter em sua unidade de fechamento agregados outros dispositivos auxiliares como: extrator hidráulico, extrator pneumático, acionamentos de machos, etc. A figura mostra uma unidade de fechamento com suas principais partes.
Unidade de Injeção
A unidade de injeção é responsável pela fase de dosagem ou plastificação da resina, tem como seu principal componente o conjunto de plastificação, composto pelo cilindro de plastificação e o fuso de plastificação, que são envolvidos por uma série de resistências que aquecem o conjunto para possibilitar o amolecimento da resina.
O fuso de plastificação, ou rosca, quando acionado faz o transporte da resina do funil, até a ponta do cilindro, é nesta fase que acontece o amolecimento e a homogeneização da resina termoplástica. O material que foi armazenado na ponta do cilindro será transferido para dentro da cavidade do molde na fase de injeção, quando o fuso avança, movimentado pelo pistão de injeção ou, em máquinas elétricas, pelo motor elétrico, conforme a figura.

Ciclo da Máquina Injetora
O ciclo de operação, durante a moldagem por injeção, compreende as seguintes etapas, ilustradas na figura:
1. Fechamento do molde;
2. Avanço da unidade de injeção (ou encoste);
3. Injeção, período em que a unidade de injeção permanece na posição avançada
durante um tempo determinado em função da natureza do material, do tamanho e da
forma do produto a ser moldado;
4. Recalque, onde é feita a compactação do material plástico para compensação
da contração do mesmo no interior da cavidade do molde;
5. Recuo do canhão;
6. Dosagem do material a ser injetado;
7. Abertura do molde e extração da peça, após o produto moldado ter resfriado.
O processo de injeção de uma peça ocorre de forma cíclica, onde tempos e fases dependem da complexidade dos equipamentos utilizados e do formato do produto. As fases de ciclo básico de moldagem estão ilustradas na figura.
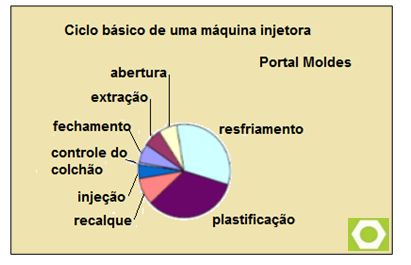
Etapas
de moldagem da máquina injetora.
As etapas de moldagem da máquina injetora são descritas a seguir. Para iniciar
o processo, o molde deve estar aberto, o canhão recuado e a tremonha
abastecida, conforme ilustrado a figura. O primeiro passo é encher a unidade de
injeção com resina plástica da tremonha (dosagem).
Imagem 1-
O fechamento do molde é realizado pelo sistema hidráulico, que movimenta a placa móvel na direção da fixa. A “velocidade de fechamento” é referente ao avanço da placa móvel da injetora no momento do fechamento do molde e deve ser ajustada de forma que o fechamento ocorra sem choques e para isto, há o recurso do “amortecimento de fechamento” que permite o avanço da placa rapidamente até atingir o micro que aciona o amortecimento quando então a velocidade será reduzida até o “limite de fechamento”, evitando assim, o choque, considerando que a velocidade de avanço baixa, pode gerar aumento no tempo de ciclo total.
O recurso do limite de fechamento informa para o comando da máquina o momento de aplicar a força de fechamento sobre o molde. No instante do fechamento entra em ação a “proteção de molde”, que é um recurso que possibilita o travamento da máquina, apenas se as superfícies de fechamento estiverem livres de peças injetadas ou partes metálicas, sendo que em máquinas com ciclos automáticos sem operador, pode ocorrer que uma peça fique presa na cavidade ou entre as placas do molde e, se o fechamento ocorrer pode acontecer danos ao molde.
A proteção de molde garante que a aproximação final entre as placas do molde seja realizada com baixa pressão e, é importante que na preparação de máquina seja observada a regulagem.
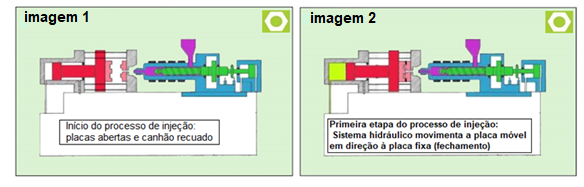
Imagem 2 –
Com o molde fechado, ocorre o “avanço da unidade de alimentação” sendo que a velocidade de avanço do bico deve ser ajustada de forma a reduzir ao máximo o tempo de ciclo, sem, contudo, gerar problemas. Para o momento do encosto, o recurso do “amortecimento de avanço do bico” deve ser ajustado de modo a evitar um impacto entre o bico e a bucha de injeção evitando possíveis danos.
“A pressão de avanço do bico”, exercida sobre a bucha de injeção, deve ser regulada pois, se a mesma for elevada poderá empenar as placas do conjunto e ainda, se a pressão de avanço do bico for baixa, poderá ocorrer o recuo da unidade de alimentação no momento da injeção provocando vazamento do material injetado (dificultando até extração do canal).
Imagem 3 –
Nesta fase dá-se o avanço da unidade de injeção (canhão), ocorrendo o encoste, conforme mostrado na figura. O “tempo de avanço do bico” deve ser sempre ajustado para a realização da operação de encosto do bico observando-se que se o tempo for elevado sem necessidade, aumentará o tempo de ciclo.
Em máquinas modernas o comando de injeção, impede que a unidade de alimentação injete material sem que o bico esteja devidamente encostado e ainda, dependendo das características do material que será processado, existe a opção de se produzir com o bico continuamente encostado sobre a bucha de injeção ou com a mesma recuando a cada ciclo.
Para a injeção de material plástico consideremos que o tempo de injeção, velocidade de injeção, e pressão de injeção são controlados independentes mas, relacionados entre si na busca de boas propriedades e visual para as peças. Com o bico já pronto em termos de regulagem, iniciamos o ajuste da “velocidade de injeção”, que procede ao avanço na rosca no momento da injeção.
A regulagem da velocidade de injeção é realizada por válvula hidráulica que controla o fluxo de óleo, fechando-se a válvula, ocorrerá uma diminuição e abrindo-se ocorrerá um aumento da velocidade de injeção.
A velocidade de injeção é de grande influência no processo podendo definir parâmetros dimensionais e visuais do produto e, é inversamente proporcional ao tempo de preenchimento da cavidade, pois, quanto maior a velocidade, menor o tempo de preenchimento da cavidade, sendo que o tempo de injeção programado no comando da máquina tem controle independente da velocidade de injeção.
Para a maior velocidade de injeção, mais rápido será o preenchimento da cavidade, maior o atrito entre a massa fundida e as paredes dos canais e das cavidades, aumentando, portanto, a orientação das cadeias. Pode haver influência no tempo para eliminação de gases dentro da cavidade, na formação de rebarbas e marcas de fluxo devido a turbulência.
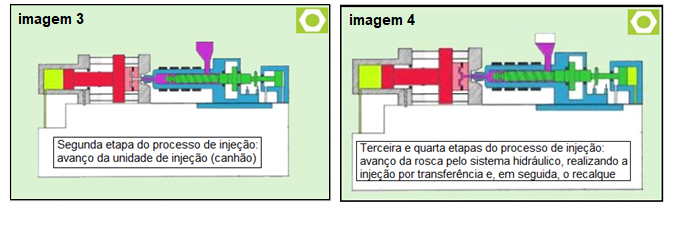
Imagem 4 –
A pressão de injeção é utilizada quando o material plástico é injetado na cavidade do molde e tem uma influência direta nas características do produto. Esta pressão é obtida no manômetro da máquina no instante em que ocorre a injeção sendo que, consideremos ainda a pressão real de injeção que é a pressão na câmara de dosagem, além das perdas de pressão no bico e nos canais de distribuição do molde.
A pressão de injeção vai depender do tipo de material a ser processado, tipo de máquina injetora, temperaturas de plastificação, diâmetro do oficio do bico e características do molde (dimensões do sistema de alimentação). Sendo que uma pressão de injeção alta poderá compactar demais o material dentro da cavidade, dificultando a extração, originando rebarbas e ainda provocando um alto nível de tensões internas, ocasionando quebras e trincas. A pressão de injeção baixa poderá acarretar o não preenchimento da cavidade, peças com rechupe e provocar um acabamento irregular. É correto iniciar o processo com baixa pressão de injeção e aumentá-la progressivamente até atingir as características desejadas do produto.
No tempo de injeção, o fluído hidráulico provoca o avanço da rosca da injetora sob pressão controlada e se este tempo for curto, poderemos ter o não preenchimento da cavidade, pois não existe tempo suficiente par ao avanço da rosca ou pistão. Caso o tempo seja longo, a injeção é completada com o restante do tempo, para compactação da peça na cavidade. Equipamentos modernos oferecem a possibilidade de regulagem independente para o tempo de injeção e tempo de compactação.
“A pressão de recalque” também conhecido como 2º estágio de injeção, atua sobre o moldado dentro do tempo de recalque, visando a compactação do material e a compensar o encolhimento por contração. Em equipamentos que possuem controle independente para regulagem da pressão de recalque, e a peça necessitada, deverá ser da ordem de ½ a 1/3 da pressão de injeção regulada e caso o equipamento não possua este recurso e a peça necessite do recalque, devemos então realizá-lo, através da pressão de injeção.
“O tempo de recalque “ é aquele programado para que a rosca continue mantendo a pressão sobre a peça injetada, a fim de evitar defeitos visuais e dimensionais na peça e normalmente é expresso em segundas e em equipamentos modernos pode ser regulado com aproximação de décimos de segundos. Se o equipamento não oferecer regulagem para o tempo de recalque, devemos recalcar a peça dentro do tempo de recalque.
Peças com paredes finas e com entradas capilares muito pequenas necessitam de pouco tempo de recalque, pois, logo após o preenchimento da cavidade, a entrada já se solidifica impedindo a ação do recalque sobre, o moldado e também, o recalque atuaria somente sobre os canais de distribuição.
Conforme o produto e suas características dimensionais ocorrem uma variação do tempo de recalque e da pressão de recalque. Há peças em que já se efetua o recalque na própria operação de injeção sem que haja necessidade de fazê-lo separadamente.
A “velocidade de dosagem” é a mesma com que a rosca retorna em rotação após o tempo de recalque, efetuando a dosagem. Algumas injetoras permitem uma regulagem específica dessa velocidade e em outras ela é uma consequência da regulagem da RPM da rosca e da contra pressão de dosagem. Esta “contra pressão de dosagem” é hidráulica e aplicada na parte traseira do atuador de injeção, que a rosca tem que vencer para poder retornar e ainda, tem influência diretamente na plastificação do material e deve ser regulada observando-se a temperatura da massa fundida.
A contra pressão possibilita homogeneizar a massa de material em estado fundido, homogeneizar também a massa de dosagem e a incorporação de pigmentos. Em peças técnicas de muita precisão, poderá ocorrer problemas com massas heterogêneas de dosagem, que podem ser resolvidos aumentando-se a contra-pressão.
Imagem 5 –
Para conhecer o valor da contra-pressão, devemos acionar o nanômetro no instante da dosagem. O ponto de retorno da rosca é determinado pelo “limite de dosagem” ajustado.
Ao retornar, fica na extremidade da rosca a quantidade determinada de material que será utilizado na próxima injeção. A regulagem inadequada do limite de dosagem, poderá influir na aparência e nas propriedades do produto, observando-se que uma dosagem excessiva ocasionará peças com rebarbas, ao passo que, uma dosagem insuficiente provocará peças incompletas ou “chupadas”.
Nas injetoras o curso de dosagem possui uma escala, graduada, para referencias em próximas injeções.
Quanto maior o retorno, maior será a quantidade de material dosado e, é claro que quanto menor o retorno, menor será a quantidade de material dosado. Importante considerar que a rotação na rosca e a contra-pressão de dosagem devem ser reguladas em conjunto, objetivando o término da dosagem instantes antes do término do resfriamento.
Alguns materiais plásticos no estado fundido possuem a viscosidade muito baixa (principalmente as poliamidas e o PVC) e podem ocasionar problemas de processamento em função desta característica.
O recurso da descompressão nas máquinas injetoras surgiu para minimizar estes problemas, possibilitando um retorno rápido da rosca, sem rotação, no final do curso de dosagem. Desta maneira, a rosca descomprime o material fundido, acumulado na câmara de dosagem, aliviando a pressão interna e evitando o escorrimento do material pelo bico de injeção.
A “descompressão” ou também chamada “função Z” em alguns equipamentos possibilita por ação hidráulica, um retorno em rotação da rosca, independente de haver ou não material no cilindro de aquecimento. É também, a descompressão, uma etapa individual do ciclo de moldagem, podendo ocorrer o seu acionamento independente de qualquer outro comando. Considerando que este retorno no final do curso de dosagem sendo muito longo, pode causar um acúmulo grande de ar na câmera de dosagem, facilitando a oxidação da peça, devido aprisionamento de ar quente na cavidade.
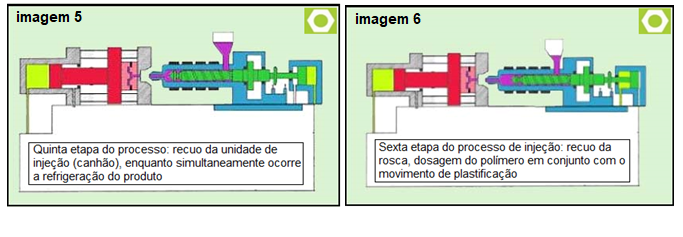
Imagem 6 –
O recurso do “recuo da unidade injeção” a cada ciclo, pode ser utilizado em alguns casos especiais de processamento como por exemplo, quando o material plástico fundido tende a escorrer pelo bico, obstruindo o canal da bucha de injeção e também nos casos onde a troca de calor entre o bico e o molde é prejudicial aos processos de moldagem. Para estes casos o limite de recuo do bico e a velocidade com que este recuo ocorrerá deve ser observada, objetivando-se reduzir ao máximo o tempo total de ciclo.
O “tempo de resfriamento” da peça inicia-se em paralelo à dosagem e ao recuo do bico, e neste período, a máquina fica totalmente parada, travada e na cavidade do molde ocorre a solidificação do produto. O tempo é ajustado em segundos e conforme equipamento até em décimos de segundo.
Consideremos
que o tempo gasto com o resfriamento da peça, é o de maior influência no tempo
total de ciclo, daí a necessidade para os transformadores procurar reduzi-lo ao
mínimo possível e com este objetivo, vários recursos podem ser utilizados na
redução deste tempo. A circulação de água gelada no sistema de refrigeração do
molde é um exemplo.
Se houver uma redução em excesso do tempo de resfriamento, poderão ocorrer
peças com problemas dimensionais, geométricos ou com elevados níveis de tensões
internas.
Para a abertura do molde é necessário o ajuste da velocidade ou vazão de abertura que é responsável pelo recuo da placa móvel da injetora, combinando-se a abertura do molde com o fim do tempo de resfriamento. Há de ser considerado o ajuste para se obter ciclos mais rápidos, porém, se gerar problemas de balanço na máquina de injeção.
Imagem 7 –
O “amortecimento de abertura” é um recurso que possibilita um deslocamento à baixa velocidade da placa móvel da injetora, no início e no final do curso de abertura.
Este recurso possibilita que a abertura se inicie lentamente, até que as colunas do molde sejam extraídas das buchas do lado oposto, ou até que as gavetas existentes no molde possam recuar suavemente. A finalidade principal do amortecimento é a de evitar paradas bruscas da placa móvel no final do curso de abertura, que poderiam gerar balanço por inércia no equipamento, sendo o limite de abertura controlado por um sensor de final de curso para estabelecer o limite do retorno.
Tendo equipamento deve possuir
este recurso. Com o molde aberto, deve ser observado se o espaço entre as duas
metades é suficiente para a extração do produto, de forma automática ou
manualmente.
O curso de abertura deve ser o necessário pois , um deslocamento muito grande
da placa móvel provocará aumento no tempo de ciclo.
Para a “extração do produto” a regulagem da “velocidade de extração” só é possível para extratores com acionamento hidráulico sendo o mesmo, responsável pelo deslocamento da barra extratora da máquina, que faz o acionamento do sistema de extração do molde. O ajuste da velocidade de extração não deve permitir que a peça seja arremessada contra a outra metade do molde e que ocasionem marcas de extração no produto.
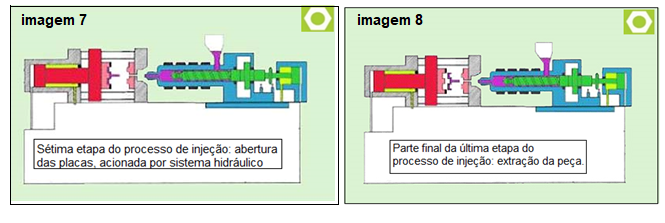
Imagem 8 –
A “pressão de extração” também só é possível ser ajustada em equipamentos com extrator hidráulico e trata-se de força de atuação da barra extratora (da máquina sobre a placa impulsora do molde. A pressão ajustada, deve ser suficiente para deslocar a placa impulsora da extração até seu limite sem provocar trancos na placa impulsora do molde danificando-a. pelo curso de extração definido, ocorre o deslocamento dos extratores e também o produto injetado.
Este curso deve ser regulado cuidadosamente, pois, se for muito pequeno pode acontecer a não extração por completo da peça, e se for excessivamente longo, haverá perda de tempo e indicando falha no projeto do molde. Nem todos equipamentos permitem, mas existe a possibilidade de se realizar no momento da extração um, dois ou mais golpes da barra extratora sobre a placa impulsora do molde. Todo molde possui um curso de avanço do sistema de extração pré-definido, para possibilitar a extração total do produto injetado. A “extração repetitiva” é um recurso que permite uma maior segurança na operação de extração principalmente em moldes com muitas cavidades, onde devemos garantir que todas as peças sejam extraídas antes do início de um novo ciclo. A cada avanço da barra extratora, o sistema de extração do molde deve recuar novamente, auxiliado por molas ou por retorno mecânico.
Fases do processo de moldagem m
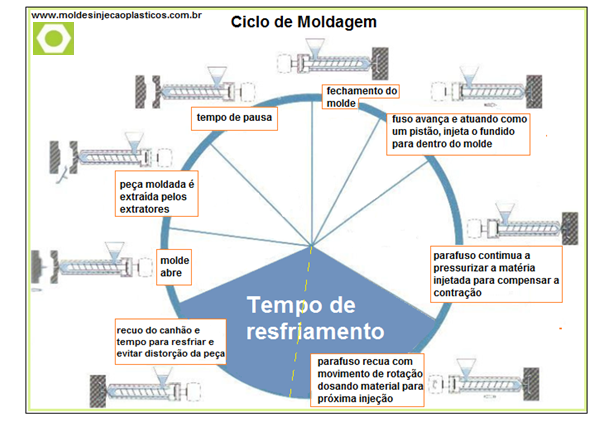
Condições de Moldagem
A moldagem será satisfatória se houver um controle das seguintes variáveis que tem influência sobre a moldagem por injeção:
Pressão de injeção: Varia de maneira ampla conforme o tipo de molde ou de máquina. Em geral, deve-se procurar o uso do mínimo de pressão, para a obtenção de artigos moldados, livres de defeitos internos e superficiais. Um excesso de pressão provoca, em geral, escape de material pelas juntas.
Temperatura do cilindro: A temperatura é responsável pela plastificação correta ou não do material, e a temperatura do material depende não só da temperatura do cilindro, como também da velocidade com que o material passa através dele. Um aquecimento uniforme do material depende, em suma, de um correto controle da temperatura do cilindro de aquecimento e do controle rigoroso do tempo e duração do ciclo.
Tempo do ciclo: É o intervalo de tempo entre o início da injeção de plástico no molde na peça atual até o início da injeção na peça seguinte. O ciclo total é a soma do tempo do ciclo da máquina mais o tempo que o operador leva para abrir a porta, retirar a peça, e fechar a porta (em moldes não automáticos). Deve ser o mínimo do ponto de vista econômico, porém deve estar também nos limites estabelecidos para a boa qualidade do objeto moldado. A velocidade de injeção é governada fundamentalmente pela viscosidade do material (logo, pela temperatura interna), pela pressão e pelo mínimo de restrições oferecidas ao fluxo de material ao longo de seu caminho. Na figura temos todas as etapas de tempo compreendidas no ciclo de injeção plástica.
Temperatura do molde: Uma temperatura constante do molde, abaixo do ponto de amolecimento do material, é o objetivo do produtor, e isto, em geral é obtido por circulação de um fluido em temperatura constante através dos canais do molde
— Fase de plastificação
O inicio do ciclo de injeção, mostrado na figura inicia com a plastificação do termoplástico por cisalhamento devido ao atrito gerado pela rotação da rosca.
O material plastificado é então acumulado na parte frontal do fuso, sendo que as cintas de aquecimento são responsáveis por mantê-lo na temperatura ideal até o momento da injeção. Em seguida, a unidade injetora avança até a bucha de injeção, o molde é fechado e a cavidade está pronta para ser preenchida.
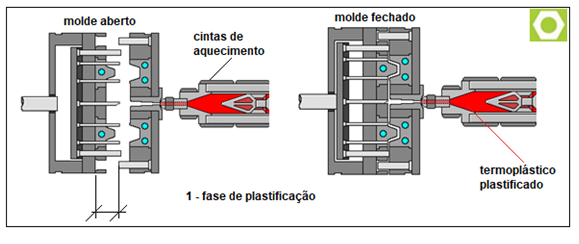
Veja animação:http://moldesinjecaoplasticos.com.br/wp-content/uploads/2020/03/video2.gif
— Fase de injeção
Após o completo fechamento, a máquina libera a execução do ciclo seguinte que é o preenchimento da cavidade do molde, onde pressões e velocidades podem ser ajustadas de forma escalonada, compactando o material na melhor condição técnica possível. Após o preenchimento da cavidade a pressão de injeção é reduzida iniciando se o recalque, esta etapa da injeção evita que o material sob pressão dentro da cavidade, ainda na forma viscosa, retorne para o cilindro. A fase de injeção (preenchimento e recalque) é a mais importante para a qualidade estrutural do produto, pois pressões, velocidades e temperaturas irão influenciar diretamente na qualidade física do produto.
A figura mostra a fase em que o material é rapidamente injetado dentro da cavidade do molde, após o material ter sido dosado e plastificado. O tempo de injeção depende do volume da peça e do sistema de alimentação, mas geralmente em peças de tamanho pequeno a média é de um a três segundos. Na medida em que o termoplástico preenche a cavidade o ar presente neste local é forçado a sair através da folga existente entre a cavidade e os pinos extratores e pela linha de fechamento do molde por detalhes denominados saída de gases, especialmente projetados para essa função.
— Fase de dosagem
Esta fase se caracteriza pela plastificação (aquecimento, amolecimento e Homogeneização) da resina, que ocorre durante o transporte da matéria-prima, do funil até a ponta do cilindro, onde já deverá estar na forma viscosa, pronta para ser transferida para a cavidade. Na fase de plastificação também é definido o volume de material a ser transferido para o molde, sendo que este volume é estipulado pela própria condição da peça. Para que ocorra o amolecimento do material, o cilindro é aquecido por meio de resistências elétricas a uma temperatura que pode ser ajustada conforme a necessidade de processo adequado para cada tipo de resina (por exemplo, a temperatura para o Polietileno é igual a 220º C, enquanto que para a Poliamida 6 é igual a 280º C).
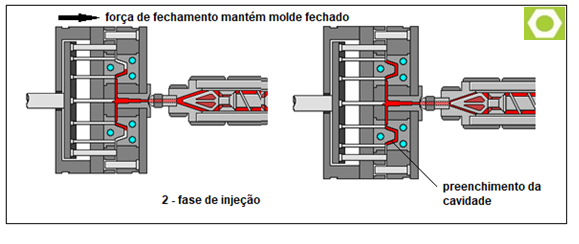
Veja link:http://moldesinjecaoplasticos.com.br/wp-content/uploads/2020/03/video3.gif
— Fase de refrigeração
A figura mostra a fase de resfriamento que é a mais longa do ciclo de injeção convencional. Depois que a cavidade foi preenchida, compactada e recalcada, a peça precisa ser resfriada até a sua temperatura de extração. Paralelo à fase de resfriamento ocorre também o retrocesso da unidade de injeção, e a dosagem e plastificação de uma nova quantidade de material para o próximo ciclo.
O resfriamento, ou cristalização, da resina inicia-se logo após o final da injeção.
Para que o material se cristalize o mais rápido possível, os moldes são providos de sistemas de refrigeração onde, normalmente, é utilizada água resfriada, para permitir a troca de temperatura entre molde e o material que está sendo moldado. Em tecnologias mais avançadas os moldes são construídos com ligas de metais que permitem uma rápida absorção do calor da resina, dispensando sistemas de refrigeração acessórios.
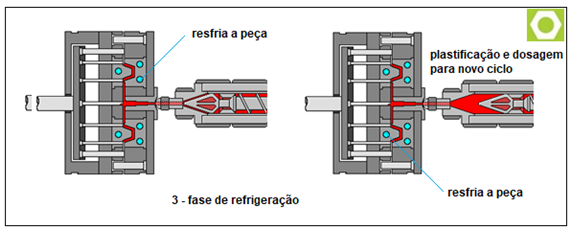
Veja link:
http://moldesinjecaoplasticos.com.br/wp-content/uploads/2020/03/video4.gif
— Fase de extração
Uma vez que a peça atingiu a sua temperatura de extração (temperatura abaixo da qual ela não sofre mais variação dimensional tanto por contração, diferença de temperatura ou deformação pela ação dos pinos extratores), o molde pode ser aberto. A imagem mostra o momento em que a abertura do molde aciona os pinos extratores que são os responsáveis pela retirada da peça do interior da cavidade.
A abertura do molde acontece para que a peça possa ser extraída, sendo o
movimento controlado por ajustes de velocidade e pressão, os quais permitem manter uma baixa velocidade no início da abertura, passando-se para uma velocidade maior na posição intermediária e, novamente, reduzindo-se a velocidade para a parada completa da placa e a retirada da peça.
A fase de extração se caracteriza pela expulsão ou retirada da peça do molde. O modo de extração irá mudar conforme o tipo de peça e a tecnologia do molde ou da máquina. A extração da peça pode ser feita em modo manual, onde o operador abre a porta e retira a peça do interior do molde, sendo que este modo de operar a máquina é conhecido como semi-automático. No modo automático, a peça é retirada do molde sem a interrupção do ciclo, fazendo-se uso de dispositivos mecânicos, pneumáticos, hidráulicos ou mesmo de robôs. Geralmente o ciclo automático é o mais recomendado, devido a menor variância induzida no processo.
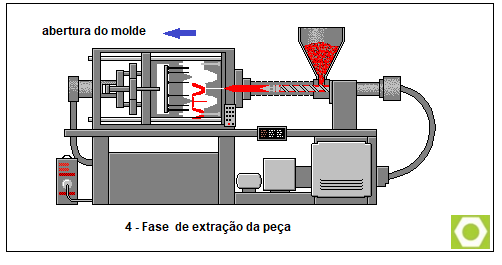
Veja animação:http://moldesinjecaoplasticos.com.br/wp-content/uploads/2020/03/video1.gif
Exemplo de molde e produto:
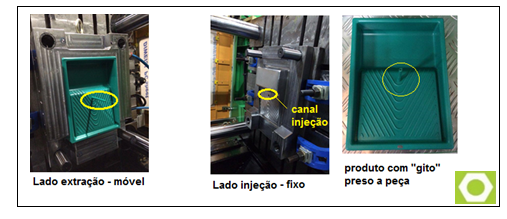
Publicado em 11/06/2017 atualizado em 02/11/2021
Fonte: Moldes Injeção Plásticos
REPRODUÇÃO PROIBIDA SEM AUTORIZAÇÃO
Hamilton Nunes da Costa – Editor de Revistas Independente
CFP VW SENAI / Matrizeiro especializado em molde
Projeto de moldes / Escola ART-MEC
Técnico mecânico CREA 126.785 / CFP VW SENAI
Este site é um Informativo. Precisamos de suporte para custear Atualizações e Melhorias. De apoio a nosso trabalho. Divulgaremos sua empresa como apoiadora.