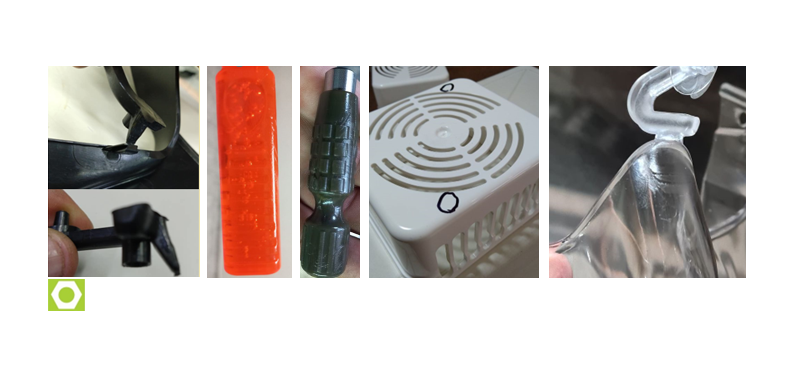
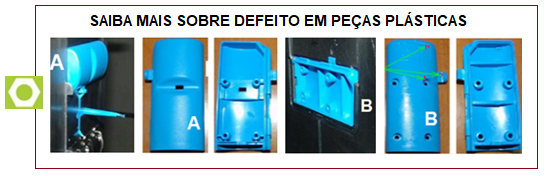
Problemas de injeção plástica em peças de PC
Este conteúdo abrange diversos problemas que ocorrem durante a injeção de diversos produtos plásticos no dia à dia. São resumos de casos apresentados e que receberam comentários e sugestões de profissionais. A ideia é levar a informação na palma da mão, para um melhor direcionamento no momento da necessidade. Se lhe interessa saber mais sobre molde de injeção, manutenção em molde e sobre defeito em peças plásticas indicamos nossos Estudos livres. http://moldesinjecaoplasticos.com.br/loja/
O que dizer da injeção de policarbonato?
Comentários:
– É chato de mais.
– Alta temperatura e muito ajuste.
– PC é um caos, pode estar tudo dentro do datasheet, mas o danado vai incomodar.
– Policarbonato e ruim de mais uma das piores injeção.
– Pior que o nylon e o noril?
– Pois eu gosto demais de injetar PC, principalmente cristal de extrema estética como lente de farol, porque além de quase todo dia aparecer um desafio, quando se pega material como PP, PBT, PA e outros não passa aperto.
– O segredo é uma boa desumidificação. Umidade em 0,1% no máximo. Tem que ser desumidificador com auto regeneração. Caso contrário, vai ter bolhas e linhas prateadas.
– O PC tem que ficar 6 horas estufando a 130 graus no granulo, se não tiver desumificador até dá para usar um secador normal. O diâmetro do furo do bico com 5 mm ajuda muito e tem que aquecer o molde acima de 80 graus.
– Tem que ser aquecedor próprio para óleo e mangueiras de alta temperatura.
– Trabalho muito com PC é muito melindroso, às vezes tá com o datasheet perfeito, estufagem temperatura do forno (unidade de injeção) temperatura do molde, etc. Mas as vezes tem que saber se a rosca tá boa, se não tem uma resistência queimada, nossa é uma diversidade que no PC influência muito, fora o molde verificando o galho, o gate e os poço frio primário e secundário.
– Tem graide de PC que aguenta até 315 graus e o mínimo 280 graus. Sobre a velocidade de injeção depende da peça.
– Primeiro o material bem estufado no mínimo 5 horas molde quente.
– As peças que faço são aquelas azuis (relé foto elétrico) fica em cima dos postes que liga as lâmpadas das ruas. O material aguenta chuva, sol calor, frio e impacto.
– Sempre que vou injetar eu esquento a ferramenta com o maçarico mesmo, chegando a 70 a 80 graus.
– É um material que se tiver tudo de acordo é muito bom de trabalhar, temperatura correta, saída de gás, material sem umidade, temperatura do molde e refrigeração ok o restante são detalhes.
Peça injetada de policarbonto trincando após 3 meses
Problema: peça injetadas de policarbonto trincando após 3 meses (André Paterno)
Comentários:
– Temperatura do molde pode estar gerando acúmulo de tensão interna quando combinada com água no material mal estufado. Gera trincas, recomendo olhar a temperatura do molde e depois o material.
Autor – O material é virgem e estou estufando por 4 horas a 120 graus. O molde tá aquecido a 60 graus.
– Temperatura de molde.
– Pode ter bolhas internas, o excesso de recalque.
Autor – Sim, fica com algumas bolhas na peça. Quando sai da máquina a peça sai sem bolha mais depois começa a aparecer as bolhas.
– Então pode ser umidade ou velocidade de injeção alta.
Autor – Quem vendeu o material disse para injetar com a velocidade alta.
– Realmente, agente trabalha com policarbonato e a injeção é rápida.
– Talvez aquecendo o molde pode ajudar.
– Contra pressão e a descompressão como está usando, elas?
– Alta ou baixa.
Autor – Estou aquecendo a 60 graus.
– Se for material recuperado deveria colocar 50% de material novo. Porque ele precisa de alta temperatura para ser injetado e as características dele muda. Sempre fiz com material novo e o moído eu misturo com novo.
– Que tipo de peça? É transparente? É utilizada em local que receba luz solar?
– Aumentar temperatura do molde.
– Verifica a procedência da matéria prima, tenta trocar por uma de fluidez menor. Utilize matéria prima virgem sem misturar com material moído.
– Se desse maiores informações da peça, talvez poderíamos ajudar.
– Pode ser tensão no material, se a peça sai perfeita na hora da injeção experimenta estufar ela a 120° por 2 horas.
– Já tive muitos problemas assim. O que está acontecendo pode ser hidrólise. O PC necessita de um teor de umidade menor que 0.02% ou seja precisa estar muito seco. Há algumas maneiras de verificar este problema: o PC deve resistir facilmente a uma temperatura acima de 350°C na moldagem, se ele amarelar acima desta temperatura é sinal que há umidade no material. Outra modo é aquecer um granulo e colocar entre duas laminas de vidro e aperta-lo feito um sanduíche, se aparecer pequenas bolhas está com umidade. A umidade causa a hidrólise que é o rompimento da cadeia polimérica causando micro trincas que em pouco tempo progridem para grandes trincas. O ideal é usar um desumidificador e não um secador. Se tiver uma balança de verificação de umidade será melhor ainda. Também observe que o PC não resiste a compressão por muito tempo, se a peça fabricada por vc está presa a parafusos ou montada sob pressão também iniciará trincas. E por último se estiver montada junto a borrachas, pode haver migrações que ataquem o PC. Veja também o desmoldante, alguns atacam o PC. Espero que tenha ajudado.
– Pelas informações passodas do que está acontecendo nas peças, pode ser o caso de uma otimização do seu processo aí, estou trabalhando com policarbonato e apanhei bastante no começo, vou passar algumas situações que nos melhoraram o processo nosso.
– Tensão interna combinada com desumidificação ineficiente.
– Veja a quantidade de moído que está sendo utilizado na injeção, se tiver estufa, tenta estufar para ver se melhora, veja a refrigeração, tenta aumentar um pouco o tempo de recalque e diminua um pouco o tempo de refrigeração para ver se não ajuda.
Peça com marca do tipo jato livre
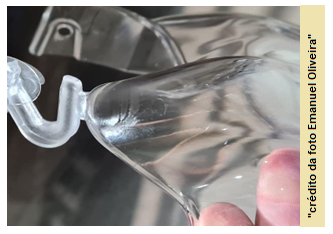
Problema: marcas do tipo jato livre.
Comentários:
– Reduz a velocidade de injeção. Velocidade de injeção por etapas.
– Começar lento e depois aumentar. Pelo que se consegue ver da peça se tiver a Velocidade baixa vai dar problemas no fim da injeção.
– Baixa a velocidade de injeção, caso perca ciclo ou não encha a peça, escalona, começando baixo e depois aumenta.
– E aumentar as velocidades e a última pressão.
– Deixa a primeira posição de injeção bem perto do tanto de carga que foi posto aí abaixa a primeira velocidade de injeção.
– Velocidade de injeção temperaturas elevadas e muita contrapressão na rosca pode causar isso.
– Escalonar a velocidade de injeção aumentar um pouco a temperatura do molde.
– Do jeito que estão os comentários acima estão corretos, deve trabalhar com velocidade e temperatura de molde para início de injeção lenta.
– Diminuir pressão de recalque e tempo e baixar contra pressão.
– Temperatura da unidade e aumentar temperatura do molde no arrefecimento.
– Este é um jato livre de material que entra na cavidade. Para eliminar o defeito é essencial modificar o ponto de entrada na cavidade ou modificar a forma do ponto de injeção. O defeito no jato livre é causado pela orientação do fluxo do material na cavidade. Se o fluxo que entra na cavidade for horizontal à cavidade, dá o jato livre, para evitar isso o fluxo que entra na cavidade deve encontrar uma parede recomendada de 90 ° (também pode ser menor) para garantir que o fluxo entre na cavidade em forma de leque, evitando a entrada do jato livre. Para verificar o quanto falo sobre o jato livre, faça prensas com o mínimo de injeções parciais para ver o jato e seu formato. O problema do jato livre é que o primeiro material que entra na cavidade para imediatamente próximo à entrada, resfriando, enquanto a continuação do fluxo quente continua em seu centro.
– O fluxo de material está direto na peça sem barreira para espalhar.
– A entrada de material deveria estar em um apêndice para ter quebra de fluxo, e o poço frio deveria ser maior.
– Pode ser desmoldante também.
Autor – Não tem desmoldante.
– Qual é a matéria prima?
Autor – PC.
– Ajuste a geometria do seu canal de injeção. O mesmo está aplicado de forma incorreta.
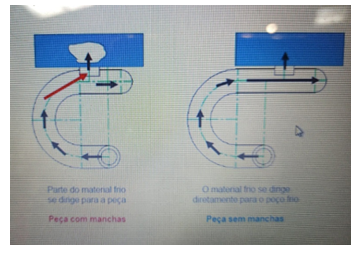
Autor – Obrigado pelo exemplo.
– Está parecendo que o recalque está demasiado e com isto acaba recalcando toda a região próxima ao canal….
– Esse modelo de canal tem que ser baixa a velocidade aí vai sair, apenas isso.
– Reduzir a descompressão, e começa a injeção lenta.
– Conforme dito, somente mudando o ponto de injeção. Parâmetros de processo não resolvem. Você pode insertar a região do canal com um tipo de gate “banana” ou “unha de gato”. Ou mudar a entrada do canal de forma que ele “encontre” uma parede perpendicular ao sentido do fluxo para que o mesmo se espalhe.
Solução:
Autor – Problema resolvido. Jogamos com a temperatura do molde a 135°C e velocidade. Aumentamos o ponto de injeção, pois o fluxo estava estrangulado. Obrigado pelos preciosos conselhos.
Peça com marcas de estrias
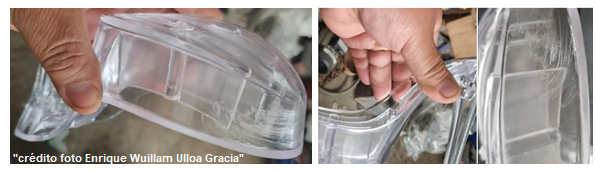
Problema: peça com marcas tipo estrias. Material policarbonato. Está bem seco.
Comentários:
1° Estufar a 120°C por 4horas.
– Se o material fornecido for pre estufado talvez 2 horas.
2° Ponto de injeção muito restrito, PC queima e causa mancha similar. (obs. Esse ponto restrito pode ser o bico da injetora, abra o furo o máximo possivel que a bucha do molde permita, gosto de no mínimo de 4mm no furo do bico para PC).
– Apesar que o seu material está bem seco, está mancha e de água, tem que estufa mais o seu material.
– Estufa mais material e melhora a velocidade de injeção, vê se ponto de fluxo não está pequeno para passagem do material correr melhor…
– Se tiver bem seco o material, tenta abrir mais a entrada do molde pra trabalhar com menos pressão
– Material frio!
– Pode colocar água quente para circular no molde e controlar na velocidade de injeção.
– A cada 20 kg de policarbonato em media de 1h para estufar, isso com desumidificador, se for sem em torno de 2 a 2 horas e meia, agora aconselho também diminuir a descompressão.
– Pelo jeito e perto do ponto de injeção tenta abaixar ou aumentar a velocidade de entrada so material ou tbm abaixa na câmara quente a temperatura correspondente a esse bico.
– Está parecendo contaminado com outro tipo de material, uma limpeza de rosca ,bico e porta bico ajudaria, mais se for espirrado,um pouco mais de contra-pressao ajudaria,pode também injetar por tempo pode resolver.
– Eu verificaria a temperatura do molde, depois temperatura do material no cilindro, em seguida velocidade de injeção, contra pressão levando em conta que o material tá bem estufado.
– Estufar a 120° e verificar furo do bico para não ter atrito na hora da injeção. Ideal para policarbonato furo de 5mm.
– Temperatura do molde em torno de 60 a 80 graus é o que pede o dataschit do PC.
– São inúmeros fatores que podem estar afetando seu processo. Aconselho ir por caráter eliminatório.
1° TEMPO E TEMPERATURA DE ESTUFA;
2° TEMPERATURA DO CILINDRO DE INJEÇÃO;
3° VELOCIDADE DE DOSAGEM;
4° CURSO DE DESCOMPRESSÃO;
– Material com umidade.
– Trabalhar com o molde mais quente tira descompressão e temperatura do bico.
– Provavel contaminação de material anterior.
– Temperatura.
Autor – mucha o poca temperatura
– Pode ser temperatura do cilindro baixa.
– Pode ser contaminação do bico e melhor queimar.
– Fazer saída de gás na linha de fechamento próximo a está região irá ajudar vc ter velocidade e pode resolver, analisar se o polimento tem ondulações, tbm influência.
– Diminui temperatura do bico.
– De mais tempo de secagem, no mínimo 6 horas. Qual a temperatura do molde ?
– Está úmido colar + contra pressão abaixa velocidade da rosca e usa o mínimo de descopressão.
– Só aumentar a contrapressão e prá resolver.
– O material não tem que ser aquecido. Tem que ser desumidificado. Pode ser temperatura do canal quente ou bico.
– Está parecendo gás, diminuir as velocidade de injeção,e também diminui a descompressão.
– Estufar por pelo menos umas 4 horas a 100 graus.
– Material úmido, mas tenta também zerar a descompressã
– Aumenta a contrapressão e diminui um pouco a descompressão.
– Já tirou a descompressão.
– Temperatura do bico elevada ! Está queimando a matéria prima.
– Não parece queima…mais voltado para gás de umidade.
– Acredito que seja queima ! Pelo que conheço de PC.
– Materia prima não estufada no tempo ideal.
– Saída de gás ou fazer uma bolsa fria.
– Se estiver usando descompressão, diminua o curso.
– Policarbonato, estufar mais.
– 12 horas de estufa entre 100 a 120 graus.
– Conta pressão, mais.
– Parece ter PMMA misturado.
– Colocar bico curto.
Peça com bolhas e riscos
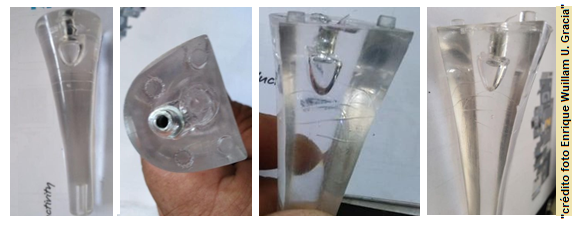
Problema: peça com bolhas e riscos. Material policarbonato.
Comentários:
– Conversei com profissionais que também trabalham com saltos sobre o problema. Indicaram trabalhar com pressão alta. Verificar bomba e motor hidráulico se estão ok. Os tubos que vão no salto ou porca de fixação precisam ser aquecidos e o operador da máquina trabalhar com luvas, pois a gordura das mãos influência para criar bolhas nas pontas dos tubos. Fazer o resfriamento da peça, após injetado com ventiladores, não usar ar gelado, mas sim ar do ambiente se posso ver um túnel de ar. O policarbonato por estar maciço em saltos não pode ser colocado em tanques de água gelada para resfriamento isso cria bolhas e trinca o produto com micro fissuras. Precisa ser resfriado com ventiladores industriais e não residenciais.
– Não resfriar os moldes de saltos com água gelada.
– Retire o recalque e tente sem ele.
– Os processos de aquecimento do tubo e resfriar com ventiladores ajuda muito.
1. Utilizar um PC com a maior viscosidade intrínseca (menor fluidez que encontrar), pois a peça é muito espessa e nesta área e haverá tendência de formar bolha durante o resfriamento no molde e/ou durante o resfriamento posterior à injeção.
2. Secar o material, se possível utilizando secador/desumidificador, a 120 graus por no mínimo 4 horas.
3. Manter temperatura de plastificação a mais baixa possível desde que não comprometa o equipamento.
4. Manter temperatura do molde em torno de 90 graus (ou mais se for aquecedor pressurizado ou a óleo).
5. Utilizar velocidade de injeção bem lenta e pressões de injeção e compactação altas.
6. Tempo de injeção + compactação alto.
7. Tempo de resfriamento deve ser controlado para não resfriar totalmente no molde pois poderá já sair com bolha – não deve ser muito longo.
– Quanto às manchas escuras e/ou estrias, o material está em processo de degradação térmica podendo ser no bico da injetora ou molde ou por muito tempo de residência devido a ciclo longo.
– Bolhas é por falta de compactação do material.
– Coloca aparelhos água quente entre 60 a 70 g.
Autor – os insertos eu pingo em água quente?
– Água do molde.
Autor – o molde deve estar com temperatura de 60 graus.
– Deve se trabalhar com velocidade de dosagem lenta, deixar o material no mínimo 5 horas a 120 graus. injeção: velocidade lenta, sempre em uma única unidade, sem escalonamento, se possível deixar sem descompressão.
– Primeiro estufar a 120 graus no mínimo 6 horas segundo carregar lento Tempo e pressões de recalque altos. Usar somente uma grade com somente uma pressão e 1 recalque.
– Sim temperatura 90g. E bastante contrapressão. E não esquecer. Que material tem que ser. Estufado.
– Não precisa trabalhar com segunda pressão. Basta injetar com pouca velocidade e pouca pressão. E com tempo de injeção. Trabalha só por tempo. Vai resolver.
– Interessante, a bolha se forma depois, provavelmente o material se contrai ao resfriar, criando como uma pressão negativa, que rompe o material cristalizado da superfície, permitindo a entrada de ar.
– Veja que a bolha que existe no interior desaparece.
– Faz uma saída de gás no molde e também um poço frio.
– Serra essa peça ao meio, no intuito de saber qual o tamanho da bolha, pra dimensionar o tamanho do poço. Detalhe o poço deve conter um extrator também e ser alinhado com a bolha.
– Velocidades de injeção baixas verificar temperatura refrigeração se está correta.
– Experimenta recalque bem baixinho.
– Velocidade e descompressão.
Autor – velocidade baixa e ativa ou desativa descompressão?
– Aumenta ela pra o material sair mais.
– Bolhas: dosagem lenta, aumento da pressão, velocidade de injeção lenta, temperatura baixa de cilindro, etc.
– Estrias: Acho que se trabalhar a temperatura de molde de 60 a 70° melhora.
Peça com marca de estrias localizadas
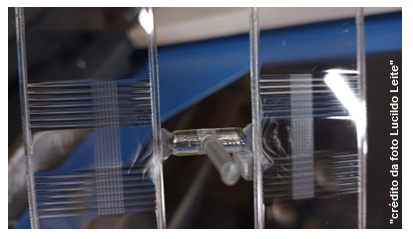
Problema: estrias localizadas.
Essas marcas não estão sumindo. Material PC. Molde está com óleo quente nas 2 partes. 75 graus de temperatura. Feito vários processos e persisti.
Comentários:
– Temperatura do molde está baixa.
– No mínimo 90 graus e se tem óleo coloca 120 a 130 graus.
– Injeta com perfil de injeção mais baixo na entrada e acelera a partir de 10mm de preenchimento. Monitora seu tempo de injeção antes e depois. Faz um embrião de injeção por posição ou tempo para determinar o exato ponto de comutação da velocidade.
– Baixa a primeira velocidade de entrada do material verificar a temperatura do molde que tem que estar em torno de 85 a 90 graus.
– O molde pode estar mais aquecido a temperatura do cilindro acima de 300 graus, e perfil de injeção, no início da injeção mais lento possível.
– Isto acontece porque o canal está muito restrito.
– Já tive esse problema a muito tempo atrás com o refletor do Fiat uno, problema solucionado diminuindo a velocidade da rosca (dosagem).
– Tenta preencher completamente a cavidade e no recalque apenas “segurar” sem muito deslocamento da rosca para a frente…. pressão de recalque, tem que perceber o deslocamento real. Não tem parâmetro fixo.
– Tenho esse problema com a lente do AGILE no acrílico e reduzo a velocidade de injeção e dosagem e soluciona.
– Pena que não tem espaço no canal, senão poderia tentar fazer um poço frio antes da entrada do leque, pode ser que seja material frio entrando primeiro.
– Aumente a temperatura do molde até por volta de 110°C se possível, coloque um perfil de injeção com a velocidade bem baixa no início (durante região de passagem pelo leque), reduza ou elimine a descompressão, verifique se é possível aumentar a temperatura do cilindro (faixa de temperatura do PC e de 280°C a 320°C).
– Pode ser que o material está úmido.
– Entrada de material muito grande.
– Deixa o molde com uns 90 de temperatura e abaixa a velocidade de injeção.
– Faça o processo com 2 ou 3 etapas de injeção, sendo na última antes da passagem para o recalque com velocidade bem baixa, e também diminui a velocidade de recalque.
– Tira a descompressão da dosagem.
– Estufar bem material a 80/90 graus por no mínimo 6/8 horas
– Não trabalhar com recuo de bico do canhão.
– Tirar a baba do bico quando canhão avançar.
– Verificar saídas de gás no molde.
– Injeto várias peças para lanterna e não trabalho com molde aquecido, não há necessidade (água torre) no meu caso não tenho problema nenhum em processo.
– Temperatura 90 graus e velocidade de dosagem menor, aumenta um pouquinho a contrapressão.
– Aumenta temperatura de processo.
– Acrílico é difícil para injeção plástica mesmo, mas pela foto me parece saída de gás.
– Rosca com baixa velocidade, sem descompressão, velocidade de injeção média pra baixa. E molde acima de 110 graus.
– Tem uma outra saída que é fazer um poço frio no molde.
– Tire a água da zona de alimentação.
– Velocidade de injeção deve estar muito alta. Diminua no início e faça um escalonamento. Temperatura do molde pode colocar 90 graus.
– Aumenta a temperatura do bico do canhão.
– Velocidade de injeção.
– Manda abrir o canal da entrada do material.
– É velocidade, aumenta.
– Estufou (c/ar circulante) o material antes de injetar?
– Aumenta mais a temperatura do cilindro e diminui a velocidade de injeção.
– Pesquisar sobre efeito esguicho!
– O canal de injeção está errado, para PC sempre deve ter uma configuração em M ou S, mas nunca direto no produto.
– Velocidade também resolve.
– Aumenta a fluidez do PC, qual está usando?
– Canal do jito não tem diâmetro ideal, corpo do jito ou canal de distribuição não tem polimento (crucial para este tipo de matérias polímeros), injeção em leque tem de aumentar espessura em mais 30% ao que está no momento, molde entre 90 a 110c°, perfil de injeção deverá ser rápido de princípio e descer gradualmente antes de comutar… (atenção à desumidificação tempo e temperatura e temperatura do cilindro) (siga especificações da ficha técnica).
– Aumentar descompressão e baixa velocidade de injeção e dosagem.
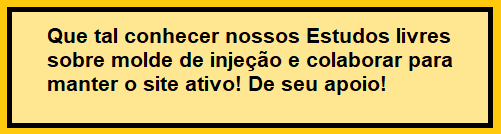
Peça com linha de emenda visível
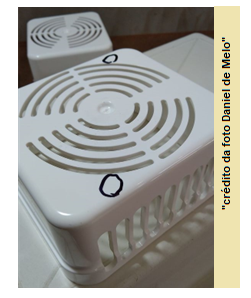
Problema: linha de emenda visível. Material policarbonato.
Comentários:
– Conseguiu resolver o problema da solda fria?
– Quais os planos agora? Vai tentar com um PC de alta fluidez?
Autor – câmera quente trabalhei já com 370°c. Amarela ainda mais a peça.
– O aquecimento do molde pelo menos a 90 graus porque a injeção em policarbonato requer o molde nessa faixa de temperatura trabalhar com a velocidade controlada evitando o embalsamento de ar no local, jogando a linha de junção para as aletas laterais.
– Tem muitas dicas boas aqui, as iniciais muito importantes para tentar remover a linha, normalmente as linhas de emenda ou junção aparecem quando há muita diferença de temperatura entre o início da injeção e final da injeção,
– Faz saída de gás e polimento na matriz, talvez melhore.
– A configuração do produto propicia esses problemas de injeção.
– Como não se consegue enxergar o defeito para ver se é linha de junção, marcas de fluxo ou outro, a princípio pode ser feito.
– Água quente, mas não dá nem para ver na foto.
Autor – mas o cliente vê e olhando na luz é bem nítida, estou usando água quente a 100°.
– Não poder ser 100graus, só aquecedor a óleo chega a essa temperatura, tem medidor de temperatura? Peça para o eletricista checar seu aquecedor de molde.
– Coloca só na fixa e diminui a velocidade de injeção e a pressão alta.
– Já existem termorreguladores a água que chegam a 130 graus. Água pressurizada… Trabalho com alguns.
– Pelo que percebo pela foto, o problema que refere parece ser a linha de união. Experimente afinar o ponto de comutação, e na zona onde o material une baixa drasticamente a velocidade de injeção e depois volta a subir.
Autor – ok.
Água industrial no molde e velocidade rápida e temperatura 275 a 300 graus.
Autor – tudo isso eu já fiz.
Se já tentou de tudo, o jeito é um PC de alta fluidez. É a 1ª vez que injeta o produto?
Autor – O produto não, mas o molde sim. Foi feito modificações para eliminar processos. No outro molde a solda fria era em outro lugar e a entrada de material também, neste molde foi colocado câmara quente.
– Se fazer a simulação de injeção no software ele vai mostra a junta fria no lugar exato, se não resolver texturização vai esconder pelo menos.
Autor – 270°. Não posso fazer textura a peça tem que ser brilhosa.
– Vai aumentando a temperatura até o limite até começar dar sinal de queima degradação.
Autor – Ok.
– Nas duas regiões marcadas coloque dois pinos extratores, faça saída de gases facetando os pinos e se o produto permitir deixe-os um pouco abaixo do nível para servirem de “poço frio” o material frio vai se alojar permitindo que o material mais quente faça a perfeita soldagem. Essa seria ações corretivas na ferramenta depois que todas as possibilidades de processo se esgotarem.
– Pode ser falta de saída de gás, veja também a temperatura da ferramenta, mas por repetir sempre o mesmo ponto, pode ser gás mesmo.
– Recalque por comutação ou tempo.
– Limpeza nas saídas de gás, temperatura do molde 70graus no aquecedor lado fêmea e velocidade de injeção em modo perfil ou início da velocidade rápido e meio para o fim lento.
– Pela foto não é possível ver se a junção é uma junção fria ou uma junção de gás. Por isso é difícil dar conselhos. Se for uma junção fria, aumente as temperaturas do molde em até 90 ° C. Mas, da posição, eu diria que é uma junção de gás.
-Todo mundo aconselha aumentar a velocidade e a pressão, digo para fazer o contrário, e verificar a força de fechamento do molde…. Se já aumentou e não deu certo agora tenta abaixar.
– É apenas regulagem.
– Com este tipo de geometria de produto, você sempre irá ter a linha de emenda nesta região.
– Só resta amenizar ou suavizar a linha, trabalhando com o molde mais quente, cerca de 80C.
– Talvez jogando com temperatura, lado matriz 90C e macho 60C, consiga provocar um deslocamento favorável, mas ele sempre existirá.
– Linhas de emenda são sempre um dilema, precisa pensar no projeto, bicos sequências, etc. E ainda assim estarão em algum lugar.
– Tenta suavizar, eliminar não será possível.
– Pode ser o curso no descanso de dosagem, que causa os gases na injeção e acumula naquele ponto, ou experimenta diminuir velocidade de injeção, provavelmente irá falhar justo naquele ponto, aí terá uma ideia que o material não está fluindo, aí aumente a temperatura nas primeiras e segunda zona de aquecimento.
– Olhando o produto e o ponto de injeção central, pode estar com um desbalanceamento de fluxo do material, a superfície por onde seu material deve fazer o preenchimento está em condição assimétrica. Se reparar as duas linhas de solda fria se localizam no mesmo posicionamento da peça. Tudo leva a crer um desbalanceamento de fluxo, na região onde se tem menor massa a percorrer a solda fica imperceptível e o lado oposto visível.
– Faça uma simulação do balanceamento de fluxo através do software moldflow ou altere o desenho do seu produto balanceando o fluxo de preenchimento.
– Começa a injeção devagar e termina rápido em 2 posição.
– Aumenta mais a temperatura do cilindro para melhorar o fluxo de injeção.
– Aumenta a pressão e velocidade de injeção.
– Fuga de gás em uma das costelas exteriores.
Peça com formação de bolhas
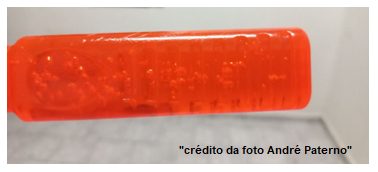
Problema: Aparecimento de bolhas.
Saindo da injetora sem bolha, jogo na água gelada aí dá bolha. Material policarbonato e a peça tem 20 de espessura. Se não jogar na água dá rechupe.
Comentários:
– Policarbonato para não gerar bolhas no processo de injeção tem duas coisas no processo que é crucial para tirar um produto sem bolhas, secagem do material de 5 a 6h a 120 graus e o aquecimento do molde acima de 90 graus, é coisa mais comum quando não estiver bem seco umidade e molde frio são os maiores causadores de bolhas.
– Bolha por esta eu não passei ainda. Eu compactaria mais a peça, no recalque e contra pressão, depois criaria uma forma de deixa lá pelo menos uns 5 minutos em um berço para não deformar, é após colocaria na água. Assim o choque térmico não será tão intenso. Mas isso chutando mesmo.
– Não use contrapressão, irá cisalhar o material e podem aparecer estrias (espirrados) na peça. O recalque é fundamental.
Autor – sim, com certeza, se utilizar de forma errada a contra pressão irá prejudicar o processo, porém a contra pressão é fundamental para estabilizar colchão, não gerar bolhas e principalmente pra garantir a homogeneização do material, principalmente policarbonato.
– Os dois sinais que a peças apresentam são da mesma causa, falta de material no produto, pouca compactação. Tem que colocar mais material dentro do molde.
– Rechupe, quando resfria devagar as moléculas estão conseguindo se movimentar mais que o aceitável para o produto. Bolhas quando coloca na água. Como você coloca na água as paredes da peça refrigeram rápido e o centro da espessura fica sem material gerando as bolhas, a falta de material ocorre pela baixa compactação do material. Policarbonato é um material de baixa fluidez é difícil acertar o diâmetro correto do ponto de injeção para evitar o congelamento antes do total preenchimento da cavidade.
– Os comentários da contra pressão são importantes para o melhorar o processamento. Existem tabelas que indicam a melhor forma de programar os parâmetros para cada material na injetora.
– Pelo pouco que se vê na foto (turbulência interna devido ao fluxo que entra na cavidade). Parece que a causa se deve ao tipo de entrada do material na cavidade do molde. Parece que vejo um jato livre devido ao tipo de entrada do material. O fluxo de entrada deve encontrar uma parede, o mais próximo possível de 90° para abrir o fluxo da frente em um Leque comum, evitando o jato livre, que cria bolhas de ar no interior. Nesse caso 20 mm é muito alto. é a condição mais natural para acionar o jato livre e as bolhas. Repito, além de uma boa plastificação do material. (Policarbonato que também exigiria um parafuso plastificante com perfil e taxas de compressão específicos para o PC) e determinação do tipo de injeção na cavidade. Tudo isso não exclui parâmetros de plastificação e injeção, velocidade de pressão, pressão / tempo de compressão final adequado para o PC.
– Outra coisa que na primeira observação não citei um produto com essa espessura fazer entrada em leque 12,0 largura x 1,5mm. Fazer injeção com perfil com baixa velocidade.
– De fato, é o choque térmico que está fazendo as bolhas. As paredes externas resfriam mais rápido que o interior do produto acontecendo um rechupe ao contrário pelo fato de ocorrer tipo um descolamento que gera essas fissuras em forma de bolha. Tenta baixar o fluxo, recalcar ou ainda aumentar um pouco a contra pressão e baixar a velocidade da dosagem e atrasar a dosagem em uns 3s de começo.
– Além da secagem do material, tenta usar o recalque como o tempo de resfriamento.
– Resfriamento.
– Material úmido preencha mais com recalque e coloca na água da rede para dar choque térmico.
– PC só roda com molde aquecido água quente. No máximo água industrial
– Com relação à falta de compactação. Caso esteja usando master, necessário avaliar o veículo dele, que deve ser de PC.
– O tempo de resfriamento tem que ser mexido.
Diminui a temperatura e aumenta o tempo de resfriamento, diminui também a velocidade de dosagem da rosca. Pode também tentar aumentar a compactação, parece que falta material aí.
– Aumentar o resfriamento, tentar um ventilador por mais um tempo e depois mergulhar na água.
– Além das observações acima, mais tempo de recalque.
– Resfriamento dá o tempo dela.
– Tenta com água aquecida.
– Tenta aumentar o tempo de resfriamento.
– Além das opções já citadas, vale a pena você estufar esse PC antes de usar.
– O erro aí está ligado a escolha do material para injeção da peça, pode perguntar a qualquer empresa fabricante de policarbonato, as bolhas vão aparecer por conta da espessura de parede. Acima de 10 mm é inevitável o aparecimento dela. Para remover será necessário recalcar…. muito… As vezes com pressões maiores que a de injeção. As bolhas ocorrem por causa da rigidez do PC ao resfriar… Visto que se não coloca na água gelada, ela deforma. Neste caso eu sugiro que vá aumentando o tempo devagar até o peso estabilizar…. Use pressões de recalque inicialmente iguais a de injeção e cuidado com a força de fechamento. Mantenha alta para que o molde não abra.
– Já tentou deixar a peça em água quente para “diminuir a temperatura” antes de deixar ao ar livre?
– Algumas peças para cabos de alta tensão são imersas em água quente após a extração.
– Tem que dar uma pressão maior e aumentar o tempo de injeção para compactar melhor.
– Aumenta o tempo de compactação, deve ajudar.
– Tem que ser bem estufado mínimo 5 horas a 120 graus PC.
– Sempre que injetamos policarbonato resfriamos as peças com ventiladores, peças que apresentam rechupe é porque ainda não foi acertada a carga ideal de material, falta material, todas as peças quanto maior a espessura maior se faz necessário o tempo de ciclo, em policarbonato sempre transfiro parte do tempo de resfriamento no tempo de recalque, por ex. se o resfriamento seria 15 segundos transfiro 3 ou 4 segundos adicionando ao tempo já programado de recalque, melhora a estabilidade estrutural da peça.
– Uma dica que me ajuda muito é usar uma velocidade menor de carga e uma contrapressão da rosca menor ajuda a diminuir os gases produzidos pelo próprio material na hora deste processo ajudando a eliminar bolhas internas.
– Aumentar o volume de material na cavidade compactar mais (recalque) aumentar o resfriamento e aumentar a contra pressão. Avaliar diâmetro do furo do bico da máquina e também da bucha e cavidade do molde.
– São bolhas de vácuo, tem a haver com a contração. Como mete na água a arrefecer, as paredes exteriores ficam frias e o núcleo quente. Ao contrair faz bolhas de vácuo. Injetar com matéria prima o mais baixo possível e aplicar muita contra pressão, tempo e pressão. Se tiver uma balança, pese a peça. Quanto mais pesada melhor vai ficar quando arrefecer.
– Policarbonato, material amorfo = menor movimentação por unidade de molécula, maior tempo de arranjo molecular devido ao espaçamento microscópico entre elas. Olha, entendo a necessidade do mergulho do produto para ganhar tempo de ciclo, mas como nos comentários anteriores, a parede espessa apresenta necessidade de mais tempo de resfriamento dentro da cavidade, sendo assim, se o produto não tiver especificações de isenção em FMEA como emendas frias (frente de fluxo), frisamento (aparência rugosa), pequenos pontos de rechupe. Tente ajustar as temperaturas do termo regulador e resistências do canhão para o mínimo possível, vai alterar a fluidez e colocar a necessidade de mais vazão e pressão da máquina para o preenchimento do produto. Com maior velocidade de preenchimento, ocorre a redução do tempo de injeção e aí se tem maior capacidade de recalque antes do congelamento do ponto de injeção (segurando a pós pressão no retorno da massa). Aumente o diâmetro da bucha e ponteira do bico para 5 mm no mínimo, se possível. Caso seja necessário um visual uniforme no produto o tempo de refrigeração terá que ser elevado e vai ter que agregar isso a sua hora máquina.
– Só vejo aumentar tempo de resfriamento. Se jogar na água vai dar bolha.
– Todas respostas acima e mais tempo de recalque, pois estas bolhas são geradas pela contração do material. Molde aquecido a 80 graus e o canal bastante generoso para durante o recalque possa ir compensando a contração.
– Injeção de policarbonato tem que ser bem lenta no início.
– Outra coisa que influência bastante é o canal, que tem que ser em leque a entrada na peça.
– Injeta com escalonamento de injeção.
– Primeira com baixa velocidade, a segunda vai aumentando e daí por diante. Diminui a velocidade de contrapressão. Se a peça não estiver muito pesada aumente o tempo de. Recalque. corrija a temperatura da ferramenta. se não resolver analisar a entrada de material. Se não for de câmera quente.
– Se for de câmera quente pode elevar mais um pouco da temperatura da câmara OK…
– A causa da bolha é a velocidade da contra pressão, diminui. Velocidade da descompressão pode estar muito auto.
Autor – quando eu injeto manual a borra já sai com bolha por que seria?
Autor – Estou estufando a 120 graus por 6 horas na estufa funil.
– Muito tempo no aquecedor queima o material.
Autor – Quanto tempo teria q deixar no aquecedor?
Autor – Molde com canal frio.
– Descompressão baixa com velocidade baixa.
Autor – Descompressão, tem sim.
– Ajuste de canais. Aquecimento de molde pode ser com resistência. Desumidificador para retirar melhor a umidade.
– Está aquecendo o molde? Tem que trabalhar com velocidade baixa, tempo de injeção alto e pressão, assim como o recalque pressão 80% da injeção e tempo alto.
– Tenta trabalhar com aquecedor de óleo quente no molde.
– Aumentar a contra pressão e o tempo de resfriamento e o recalque.
– Consulte o fabricante ou representante pra ver se está usando o PC correto. Fluidez e dureza também podem influenciar.
– Pode ser a descompressão. Tenta trabalhar com ela zerada
– Velocidade de injeção no mínimo possível.
– Tem que diminuir o tempo de injeção e a pressão de injeção, vai resolver.
Peça com mancha junto ao ponto de entrada
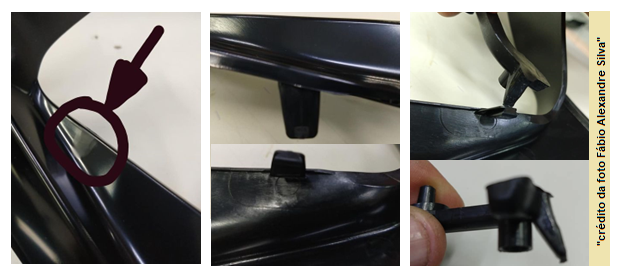
Problema: Manchas no ponto de entrada
Material PC/ABS, trabalhando com a matriz a 70°C, câmara quente a 240°C, cilindro com média de 250°C, velocidade de injeção escalonada começando com a velocidade muito baixa e aumentando para efetuar o preenchimento do produto.
Acredito que teria que mudar a entrada de material, porém não sei qual método adotar.
Comentários:
– Fazer um perfil de injeção com a velocidade inicial muito lenta e depois acelerar
Autor – já fiz, sem resultado.
– 7mm/s?
– A imagem não está muito nítida, mas para mim está parecendo umidade de material.
Autor: material está bem estufado.
– Se for mexer em parâmetro pode aumentar a velocidade inicial também trabalhar com a velocidade bem alta mesmo.
– A questão do galho, pode aumentar a espessura da parte que está no extrator, ele pode estar estrangulando a entrada de material.
– Experimenta mudar o perfil, escalonamento de injeção, inicia rápido e vai abaixando a velocidade.
Aumenta o canal de entrada do material “gate”.
– Eu aumentaria a temperatura do molde, finalizava a injeção com velocidade baixa, se o problema for falta do brilho na peça, pela foto tá difícil visualizar.
Autor – Não se trata de falta de brilho, o problema é mancha na entrada do material.
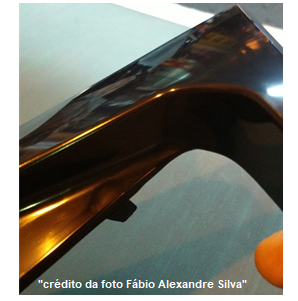
– Já tirou uma peça sem recalque pra ver se a mancha aparece? Sugiro injetar a peça parcialmente para identificar em qual momento ocorre a mancha.
Autor – mesmo sem recalque aparece sim.
– Pode ser o estrangulamento do detalhe do produto onde o canal ataca. Porém se vc aumentar pode causar chupagem na classe A.
– Isso é jato livre,tem que fazer perfil no processo, sendo que deve-se iniciar a injeção com velocidade muito lenta.
– Está parecendo material frio. Faz um teste. Aumenta um pouco a câmara quente e verifica o comportamento. Apesar da imagem não tá muito nítida tá parecendo q e vc isso.
– Isso acontece também quando se usa uma contrapressão muito alta. Por ser bico quente vai um pouco de material. Faz também esse teste.
– Umidade, ABS, PC não tem segredo para injetar desde que o material esteja desumidificado.
Autor – não é umidade não, injetamos diversos itens com a mesma a mesma temperatura e tempo de desumidificação e não temos esse problema.
– Isso ocorre muito no PVC rígido e com redução da velocípede injeção na entrada da cavidade resolve. Se não resolver tenta Scott bright nesse ponto.
Autor – o problema é que a peça é pintada, fazíamos retrabalho com lixamento e é exatamente o que estamos tentando eliminar.
– Vai sumir aumentando. Temperatura do material. Geralmente se trabalha com PC em torno de 280 à 300 graus. Aumenta também a temperatura da Câmara quente 300 graus.
– Verdade, injetamos nessa temperatura também.
– Chama o mecânico que ele resolve, com certeza, problema de controle de velocidade da máquina.
Autor – É máquina zero km e de qualidade.
– Não confia nestas máquinas novas.
– Pelo tipo de gate mostrado na foto você pode minimizar o problema com o escalonamento da injeção, deve encontrar o ponto exato da transição do fluxo do canal de injeção para a entrada da cavidade e aumentar a velocidade de injeção drasticamente a partir deste ponto.
– Melhor resposta que vi aqui.
– Trabalho cm PC/ABS. É bem isso mesmo.
– Achar o ponto exato do gate para entrada na cavidade.
– Experimenta fazer o contrário, mais rapido ao início e depois mais lento no fim para minimizar os gases.
– Vejam que as dicas estão voltadas ao perfil de injeção. Veja se o bico de injeção tem resistência ou é acoplada direto no canhão, se for acoplado, troque o bico e controle a temperatura. Recomece a regulagem com perfil de velocidade injeção bem lento até entrar na cavidade e depois aumente.
– Pela foto parece ser efeito esguicho, sim com entrada de vazão menor minimiza ou resolve, porém deve estar muito estrangulado a entrada de material, recomendado nestes casos, direcionar a entrada para parede mais grossa do produto.
– Está parecendo gás tem que fazer saída de gás.
Peça técnica tipo varão com acabamento ruim
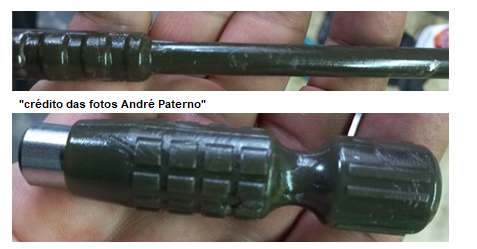
Problema: Acabamento ruim
Molde novo. Material policarbonato virgem
Comentários:
– Molde aquecido, canal de alimentação e gate não devem estrangular o material, material desumidificado, injeção lenta. Como tem inserto metálico, talvez aquecer o inserto para injetar. Veja se a folga entre o inserto e a cavidade, ou seja, espessura da peça não está muito restrita para fluidez do material.
– Molde acima de 95 graus, injeção lenta.
– Isto não é umidade, muito provavelmente queimando durante o preenchimento, por velocidade inadequada.
– Para injetar o Policarbonato o material tem que estar bem estufado. Tente utilizar um perfil de velocidade de injeção iniciando com velocidade lenta e aumentando gradativamente, em alguns casos recomenda – se aquecer o molde acima de 80 graus. Verifique também a contra – pressão e a descompressão.
– Injetei peças parecida com essa, molde tem que estar com água aquecida, material tem que estar muito bem estufado.
– Parece que injeta sobre um inserto de metal, tenta fazer o que comentaram acima, e aqueça o inserto.
– Pelo que vi na peça, tem vários fatores ocorrendo, aquecer bem o molde, estufar o material a 90 graus, se estiver secador na máquina pode colocar 120 graus por ao menos três horas, temperatura dos cilindros deverá estar entre 320 graus a 270, isso pode te ajudar.
– Umidade.
– Estufa e molde aquecido.
– Pelo que se vê pelas fotos parece ser jato livre. É necessário intervir no tipo de entrada e na posição da entrada na cavidade. O fluxo do material que entra na cavidade não deve ser perpendicular à cavidade, mas deve encontrar uma parede, (tanto quanto possível a 90° do próprio fluxo) para abrir o ventilador de um fluxo correto.
– Estufar 5 horas a 120graus.
– Usa o termo regulador a 95 na temperatura.
– Recalque, aumento.
Diminui a descompressão também.
– Abaixa velocidade, aumenta temperatura, estufa o material, melhor dá um pouco mais de contra pressão ou diminui a rotação da rosca.
– Abaixa aí a temperatura e coloca contra pressão e diminuí a velocidades da rosca e dá uma olha na descompressão.
Mancha tipo esbranquiçado – Material PC
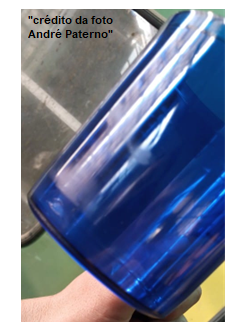
Autor – Injetando jarra em policarbonato, mas está apresentando mancha branca.
Comentários:
– Use 0.3% do aditivo AXEL da Audrix.
– Serve para dar mais fluidez?
– Limpa o molde com desengripante ou solvente.
– Veja se o molde não está soando.
– Material pouco estufado.
– Já injetava e não saia? Ou trocou de M.P agora? Pode ser saída de gases.
Autor – Matriz nova.
– Então pode ser saída de gases mesmo.
– Umidade e se estiver trabalhando com descompressão diminui ou desliga.
– Esse material tem q ser estufado 120 ºC.
– Trabalha com a água da parte móvel na metade e se possível água natural, pouca temperatura nas zonas e pouca sucção, pouca velocidade também ajuda
– Característica de umidade do material…
– Já injetou peças boas? Se afirmativo está queimando, ou por temperatura ou velocidade de injeção, ainda pode ser material. Ou o pigmento úmido. O pigmento deve ser próprio apara policarbonato se for a base de EVA ou PE vai queimar também…
– Geralmente isso é muita velocidade e muito calor ok?
– Precisa ler as instruções de utilização. Material higroscópico….
– Abre o fechamento para ver se sai a mancha branca, se saí é saída de gás.
– E aumenta a temperatura do molde.
– Velocidade de injeção baixa.
– Usa resfriamento com água natural na placa fixa do molde.
– O molde tem câmera quente? Se caso for deve está ficando material frio no gate, já aconteceu comigo.
– Temperatura da matriz.
– Policarbonato tem que ser estufado, verifica a descompressão se está muito elevada, pois isso causa essas manchas de espirrado.
– Se mais peças estão saindo com o mesmo problema no mesmo ponto, pode ser que seja o molde. Da uma olhada nas saídas de gases, podem estar entupidas, abaixa um pouco a velocidade de injeção, pode ser que esteja queimando em decorrência do atrito.
Mancha branca na lente do produto – Material PC Cristal

Autor – Material PC Cristal, mancha branca na lente do produto. Dá em várias partes diferentes da peça. Estava produzindo normalmente e de repente começaram a surgir essas manchas brancas que são constantes por aqui.
Não agora, mas acontece com frequência também as pintas pretas.
Temperaturas da câmara quentes em 285 °C. Máquina que roda somente PC e Acrílico. Foi identificado um problema no desumidificador.
Comentários:
Está com parecendo bico sujo…
Pode ser vestígio do acrílico ou alguma sujeira no sistema de abastecimento que está contaminando sua produção.
Retirada e limpeza do bico injetor, limpeza funil.
Verifique as saídas de gases na região da mancha, PC é chato precisa de um ciclo constante, estufar o PC muito bem faz parte do processo.
Quantas horas de estufa? Teste de 12 a 14 para ver, mas se dá em qualquer região da peça, problema está no material então.
Faz um teste, deixa mais tempo na estufa só para um pequeno teste e eliminar essa hipótese.
A secagem do PC deve ser feita a 120 °C de 2 a 6 horas utilizando secador com desumidificador principalmente se a peça injetada requerer alto esforço mecânico.
Caso não tenha essa exigência pode usar secador convencional com temperatura a 120 ºC por pelo menos 4 horas.
A mancha branca (leitosa) é mais característica de contaminação; a má secagem provocará alteração na viscosidade (o PC fica com menor viscosidade) e consequentemente peças mais frágeis, bolhas, listas prateadas e eventualmente variação na dosagem.
Injetei muito PC ao longo do tempo de trabalho e te garanto que é muito tranquilo de injetar desde que seja obedecido os parâmetros de secagem, a limpeza da máquina notadamente em cores transparentes e os procedimentos de parada e reinício pois em alguns casos as temperaturas poderão ser altas (acima de 300 °C) e neste caso qualquer parada prolongada degrada o PC e surgem o que mais se teme no processo – as famosas “pintas preta” de todos os tamanhos.
Na peça não a solução, no entanto o molde deve estar extremamente limpo e a matéria prima na temperatura correta, ou seja, a injetora e molde devem estar funcionando perfeitamente.
Com certeza contaminação:
1. Com grãos de PMMA que ficam no sistema de alimentação da máquina (secador, base do secador, entrada do extrusor) ou no manuseio do material.
2. Por alguma falha na limpeza da unidade de injeção; algum ponto deve ter acrílico retido e libera durante a injeção. Para não perder matéria prima cara e de difícil reutilização como o PC incolor transparente, o ideal é efetuar limpeza mecânica de rosca e canhão.
3. Por danos no conjunto de injeção os quais possam reter o acrílico das injeções anteriores ao PC; ao retirar a rosca verificar possíveis danos em rosca, ponteira, cilindro e assentamento de porta bico + bico.
Neste caso, aparentemente está ocorrendo uma contaminação externa.
Sempre que possível evitar a estocagem e manuseio de PMMA próximo ao PC, inclusive na pre secagem e secagem, pois os grânulos são muito parecidos e qualquer pequena falha na operação o estrago será grande.
Sempre evitar injetar PC após PMMA ou vice versa; utilizar máquinas diferentes.
Caso não seja contaminação, muito provável que a rosca da máquina seja adequada para PC, neste caso precisa fazer um processo errado para dar certo, deixa um colchão / almofada maior, bem maior que vai resolver seu problema.
Pode ser o desenho e o LD da rosca, já fiz isso várias vezes no PC funcionou que uma maravilha, achava que era contaminação e não era.
Faça limpeza no molde, saída de gases, a temperatura da câmara 260 ºC a 270 ºC, temperatura de processo 280 ºC a 260 ºC descompressão no mínimo possível.
Molde com câmara quente, tem que ter certeza na limpeza da máquina, se não contamina a câmera aí vai ter mais trabalho, vai subindo a temperatura da câmera para ver se a mancha some ou diminui.
Onde está essa marca se for o ponto de injeção isso é tensão na entrada terá que ajustar seu processo.
Manchas tipo arranhões – Material: ABS / PC

Autor – Estou com este problema na injeção desta peça. Material: Matéria prima virgem ABS/PC.
Material desumidificado a 95 ºC. A velocidade de injeção varia a posição destas manchas, mas nunca chegam a desaparecer. O jito já está feito com poço frio. Molde todo a 40 ºC. Já está com descompressão a zero e temperaturas a 235 ºC no bico.
O material está sem umidade, está a desumidificar em 9h a 95 ºC.
Comentários:
Quando fala que as manchas mudam de sítio e não desaparecem, será que tem saída de gases?
Vai abaixando aos poucos a temperatura da máquina e tira descompressão.
Com esse problema, abaixei a temperatura do cilindro uns 15 ºC e resolveu.
Olha o bico se não está amassado ou com obstrução.
Diminui a contrapressão, aumentando a velocidade de injeção aos poucos e se puder diminuir o tempo de ciclo.
Material úmido tem que estufar mais tempo.
pode ser temperatura alta.
Quatro causas: molde frio, temperatura alta, material úmido, falta de compactação.
Tem de residência do material na estufa, tem que dar 4 horas de estufagem.
Estava com esse problema, era a matéria prima, troquei por virgem de primeira, nunca mais tive problema.
99,99% de matéria contaminado.
Aumente um pouco os pontos de alimentação e injete com temperaturas mais baixas.
parece contaminação por fibra de vidro.
Já tentou colocar aquecedor no molde.
Pode ser material úmido, mas se está seco tenta fazer um perfil de injeção iniciando com velocidade baixa e vai aumentando. Verifica se o bico não está entupido e o material bem homogêneo.
Material com no mínimo 4 a 6 horas de secagem a 95 ºC. Observar também a vazão nos canais de injeção, veja se não está obstruído na máquina com o canhão muito quente.
Liberar um pouco de velocidade na injeção com cautela.
É possível que haja obstrução no bico, ou a compreensão da saída do bico pode influenciar, tive problemas parecidos por aqui, um boa limpeza e abertura da saída do bico resolveu.
Acredito que diâmetro do furo do bico da máquina não esteja compatível ou perfil de entrada de material na cavidade esteja estrangulando o material causando efeito turbilhão. Um bom polimento na entrada do material na cavidade pode dar uma melhorada e pode ser também saída de gás.
Diminuir a temperatura do material e diferenciar temperatura do molde.
Aumenta a temperatura de desumidificação para 120 °C por 4 horas e tenta injetar com velocidade mais baixa.
Verificar as resistências, e se não tem obstrução no bico, aumentar a temperatura do bico e escalonar a velocidade de injeção da menor para maior.
Coloque o molde todo a 80 ºC e o material a estufar a 120 ºC.
Geralmente isso resolve com a descompressão depois da injeção, baixando-a, ou então a separação do bico pós injeção.
Aumenta a temperatura do molde para 60 ºC e baixa a velocidade de injeção
Faça o teste de umidade no material, aparentemente o material está com umidade, aumente um pouco mais a temperatura do molde, vai melhorar o acabamento superficial da peça.
Canal obstruindo, ponteira do bico injeção do canhão com algum tipo de obstrução também pode causar. Mas baixa no limite a temperatura, pois temperatura alta gera isso aí também.
Avalie o desumidificador, pois pode ser que não esteja secando de forma eficiente. Se tiver sílica, veja a validade dela.
Faça um polimento no bico e analisa qualidade do material.
Material não está sendo bem seco, verificar a eficiência do secador, os filtros, pois o material está úmido, causando essas bolhas, injetar mais lento sem atrapalhar a performance da produção.
Qual o percentual de PC no ABS que está usando?
Pode ser contaminação, umidade do material, temperatura de molde ou falta de saída de gases.
Marca de espirrado – Material PC

Autor – Na injeção, óculos saindo com marca de espirrado.
Comentários:
PC é um material meio chato na entrada do canal mesmo.
Verifique se o material foi corretamente estufado.
Molde aquecido a pelo menos 70 ºC (temperatura mais elevada depende do seu processo).
Primeiro o perfil de velocidade mais baixo possível (se abaixar demais vai começar a dar marcas “coloridas” e aparência de “digital”)
Descompressão o mais baixo possível (de preferência 0).
Contrapressão média.
Se nada disso resolver o problema está em sua matéria prima.
Verificar se o molde não está riscado nessa área, caso esteja só polindo.
Onde trabalho temos muito esse problema, bom fazer a solução por etapa, as vezes começamos a fazer ajustes em regulagem, quando o problema está no molde, aí só mais refugo e nada de resolução.
Aumento de temperatura do molde e criação de mais saídas de gás nessa área.
Temperatura do material ou velocidade de injeção.
Diminui a descompressão, se estiver muito grande dá gás na peça dando essa marca.
Tenta aumenta o recalque também, pode ser que o material não está espalhando direito, aumentando a temperatura ajuda também.
Este material e complicado mesmo pior que se deixar este material muito tempo ele pode até queimar.
Começa com a velocidade e pressão baixa e depois aumenta e enche de vez. Isso aí é gás, se começar com os parâmetros lento dá tempo de o gás sair, porém não pode demorar para preencher a peça senão vai ter outros problemas relacionado ao fluxo.
Molde não está na temperatura correta, porque se esquenta fica bom.
Pode usar também um termorregulador de temperatura no molde
Veja extração, pode ser que na extração a peça possa estar enroscando, forçando o lado que apresenta essa fissura ou marca.
Pode ser material frio no ponto de injeção, sobe a temperatura do molde, ou do bico, e reduz um pouco a descompressão.
Ai bem provável seja temperatura bem próximo o canal ou velocidade de injeção
Fazer saídas de gases injetar, injetar mais lento no início e utilizar um pouco de contrapressão, utilizar água quente no molde também dosar, diminuir pressão de recalque aumentar entrada do gate, usar diâmetro maior do bico.
Descompressão, pela cor da peça temperatura alta gerando gás, velocidade de injeção alta, secagem de material bem feito com a temperatura correta da secadora, tempo muito alta de resfriamento são vários requisitos para tentar e resolver.
Estufar o material pelo menos umas 4h antes ajudaria.
Se não tiver o desumidificador, não consegue injetar.
É preciso desumidificar o material.
Ao invés de estufa, creio que está precisando desumidificar.
Material precisa estar bem estufado e faz o teste e injeta com menos velocidade e mais pressão, qualquer coisa aumenta a temperatura para fluir melhor o material.
Isso é característica de material úmido, para injetar PC ainda mais transparente o interessante seria o uso de desumidificador eficiente.
Caso o Material esteja bem desumidificado, tenta trabalhar na velocidade de injeção, pois parece estrangulamento do material na passagem do canal de injeção para o produto.
Solução: autor
Problema resolvido, defeito na resistência da estufa, não estava aquecendo corretamente.
Marca de fluxo – Material PC

Autor – Cliente que não consegue minimizar esta marca de fluxo. Alguém tem ideia como minimizar? Espessura média da peça 3 mm.
Comentários:
Não consigo perceber quais as marcas, mas se forem na entrada, injetar muito devagar até o material entrar na cavidade e depois aumentar o necessário para encher e compactar a peça.
Aquecer o molde a 120 °C.
São muitos parâmetros a serem analisados, mas comece verificando os escapes de gás, e a temperatura de plastificação. Quanto mais alta, maior a produção de gases.
Primeira velocidade bem lenta e segunda velocidade um pouco mais rápida, molde com uns 90 ºC.
PC é um material que precisa ser bem estufado, o molde precisa ser aquecido a 90 ºC a 100º, temperatura do canhão 280 ºC a 270 ºC, descompressão no mínimo possível.
Abre a velocidade, como parede é fina tem que injetar rápido e com pressão, molde aquecido para o material correr bem, extrai e choque térmico em água.
Velocidade ou descompressão.
Escape de gás ou um pino regulador de fluxo.
Aquecer o molde a 100 °C, aumentar a temperatura da matéria prima, tudo isso visando aumentar a fluidez. O policarbonato precisa ser injetado rápido mesmo, caso contrário cria outros problemas como efeito casca de laranja e rechupes.
Tenta fazer um perfil de injeção.
Policarbonato precisa estar bem desumidificado. Senão, aparece essas manchas mesmo, é complicado.
Velocidade lenta de início vai aumentando velocidade lenta no final.
A localização do ponto de injeção está criando uma área de super compactação.
O desenho do canal de injeção não é o mais adequado.
Pela imagem não tem espaço para lay-out dos canais de saídas de ar.
Se a marca que comenta é a que está na peça de baixo, está parecendo um jato livre, devido a velocidade alta e espessura baixa da peça. injete por partes primeiro o canal até a entrada da peça e veja como entra o material no molde. Preencha gradativamente avaliando em que momento cria o jato e neste ponto diminua a velocidade e compense com pressão e temperatura caso necessidade.
Marcas de espirrados próximo a entrada do material – Material PC
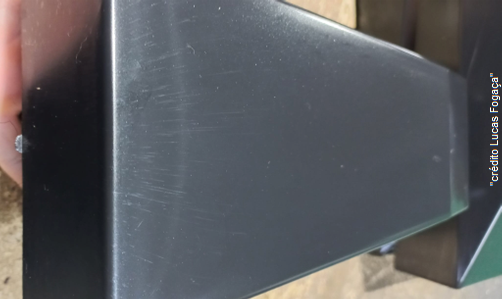
Autor – Formação de espirrados, bolhas próximas à entrada do material – bico quente a 180 ºC. Material PC preto.
Comentários:
Conheço isto como espirro, podem ser por vários motivos, umidade de material, temperatura alta, excesso de descompressão ou velocidade de injeção alta no início da injeção.
Perfeito todos esses citados e o que leva a isso umidade e turbulência.
Aparentemente não parece umidade no material (geralmente o sintoma de umidade expande para mais áreas da peça).
está aparentando ser 2 causas queima ou umidade no material.
Deixou quanto tempo em qual temperatura de secagem? Isso é sintoma de umidade ou contaminação. Tem certos materiais que podem ficar uma semana secando, mas se estiver contaminação nada vai adiantar.
Se for estufa só de ar quente sem sílica ainda sim pode ser umidade ou temperatura de secagem abaixo de 120 ºC. Tenta diminuir bastante o recuo da rosca / descompressão, aumenta um pouco a contrapressão e diminui o fluxo da dosagem. E se tiver escaneando pode ser contaminação.
Se a mancha for sempre no mesmo lugar dificilmente vai umidade, isso pode ser perfil de temperatura, problema na saída do gás ou degradação do material na câmara quente. Experimenta fazer um perfil de injeção e trabalhar com recuo de bico.
Já tentou injetar com a temperatura do bico maior (para uma maior fluidez) e a velocidade final de injeção menor?
se o material for de primeira linha aumenta esse bico quente para uns 250 ºC, se a peça for de parede fina / média aqueça o molde por volta de 80 ºC e o principal, no primeiro perfil de velocidade injete muito lento para evitar esses espirros.
Como é bico quente não há necessidade de se usar descompressão e nem recuo de canhão.
Trabalhei com PC virgem, desumidificado a 120 ºC por 4 h e na garganta 290 ºC e bico 320 ºC para DVD e CD.
Material tem que ser estufado por 5 h a 120 °C, aumenta a temperatura do termo controlador c para 60 °C, e essa temperatura do bico é muito baixa para injetar PC aumenta para 270 °C, tira o máximo de descompressão, e abre a contrapressão, tenta escalonar a velocidade de injeção baixa e depois aumenta.
Não parece ser umidade, eu aumentaria a temperatura do bico para 250 ºC, verificar também o diâmetro do bico e do molde, é melhor que tenham o mesmo diâmetro, o bico tem filtro? Outra coisa o PC gera gases na plastificação, portanto é importante deixar o tempo de plastificação próximo ao do resfriamento, diminuindo o tempo de residência do material no canhão.
Aumenta a temperatura do bico quente e vai melhorar teu processo.
Verifique se não está com a velocidade de injeção muito alta. Peguei um caso desse era um filtro que tinha no bico da injetora, tirei o filtro e causa resolvido.
Verifica se o ponto de injeção está muito fechado ou se o bico da câmara quente está contaminado.
Pode ser que o tempo de residência do material esteja alta, e está causando degradação. Verifique as temperaturas talvez diminua e tente abaixar um pouco a velocidade de injeção.
Com certeza isso é material mal desumidificado, 4 horas 120 ºC já é suficiente. Mas sua temperatura está bem baixa também, trabalho sempre com PC com temperatura no mínimo 280 ºC.
controlador c para 60 °C, e essa temperatura do bico é muito baixa para injetar PC aumenta para 270 °C, tira o máximo de descompressão, e abre a contrapressão, tenta escalonar a velocidade de injeção baixa e depois aumenta.
Sugiro pedir data sheet desse material, para um policarbonato a temperatura que está sendo usada é muito baixa.
se a anomalia for localizada e não na peça inteira, tudo indica que seja parâmetros de processo.
É temperatura está muito alta, vai baixando a os pouco que dá certo. Diminuir a velocidade de injeção e aumentar a pressão de injeção.
Trabalhe por posição com velocidade o mínimo possível. Atenção no tempo que o material fica no cilindro, opção retardo de dosagem tira um pouco o travamento para o gás sair. Isso pode ajudar.
Trabalhe com tempo de injeção baixo, aumenta aos poucos que já vai ter uma ideia, se realmente é isso, pense bem, como pode ser pouco tempo de injeção, logo já inicia a dosagem e fica purgando para a cavidade o material aí causa essa dita bolha.
Faze perfil de injeção. Inicia bem devagar nesta região, depois aumenta a velocidade.
Temperatura pode estar um pouco alta, dá uma olha na descompressão pode estar alta também, verifique a carga do canhão, pode ser que esteja com muito colchão.
Policarbonato trabalha a temperatura mais altas.
Faz um polimento no canal de entrada de material e aumenta essa refrigeração do molde para no mínimo uns 60 °C na parte fixa e vai jogando com a velocidade de injeção até achar o ponto zero.
Molde frio (Processo ideal acima de 80 ºC).
Material tem que ser estufado por 5 h a 120 °C, aumenta a temperatura do termo.
Ajuste a velocidade de injeção, aqueça o molde a 35 ºC a 40 °C estufe a 3 horas a 90 °C.
Material úmido, verifique se sua estufa está funcionando perfeitamente.
Qual a temperatura de estufagem que ficou o material e por quanto tempo?
Trabalha com água quente no molde, velocidade de pressão baixa e pressão de injeção alta.
Velocidade de injeção… ou matéria prima úmida. Dependendo do material se não foi desumidificado pode acontecer isso.
Matéria prima mal estufada ou o material está contaminado.
Deixa estudando por no mínimo 4 a 5 horas e depois começa a fazer as configurações do processo. Observação, não usar a matéria prima do mesmo lote.
Diminui o recalque.
Marcas de espirrado – Material PC

Autor – Peças saindo com marcas de espirrado.
Comentários:
Material úmido.
Verificar o tempo de estufagem precisa de 4 a 6 horas.
Teria que deixar o material estufando de 4 a 6 horas, caso já tenha feito isso tente diminuir a descompressão ou baixar velocidade de injeção, ou baixe a primeira pressão de injeção, mas aconselho fazer um teste por vez.
Pode ser material mal estufado, queima por atrito, verificar se canal tem diâmetro correto para passagem de massa, dosagem colocar contrapressão para uma melhor plastificação, não gosto de usa descompressão para esse material, molde tem que ter saída de gás e estar com temperatura no mínimo a 80 °C.
Autor – Material estufado.
Se tudo que falaram ainda não resolveu, solta um pouco o fechamento e verifique se o molde tem uma boa saída de gás.
Molde aquecido também auxilia no processamento do PC.
Peguei um caso desse, era filtro no bico tirei problema resolvido. Estava causando atrito consequência queima do material.
Este tipo de “espirrado” não está parecendo ser por falha no processo de secagem.
Pergunta essa marca sai sempre no mesmo lugar ou alterna?
Autor – Alterna.
Então descarta saída de gás.
Tira descompressão. Diminuir a descompressão resolve.
Parece ser próximo ao ponto de injeção. Pode ser descompressão.
Atualizado em 14/01/25
Esperamos ter colaborado com os profissionais!
Fonte: Grupos Técnico em Plásticos e Injeção Plástica do Facebook
Apenas Resumo: Moldes Injeção Plásticos
Acesse: isso também irá facilitar o trabalho do profissional:
TABELAS COM VALORES PARA APLICAÇÕES DE TERMOPLÁSTICOS
INDICAÇÕES PARA O PROCESSAMENTO DE DIFERENTES MATERIAIS PLÁSTICOS – 01
INDICAÇÕES PARA O PROCESSAMENTO DE DIFERENTES MATERIAIS PLÁSTICOS – 02