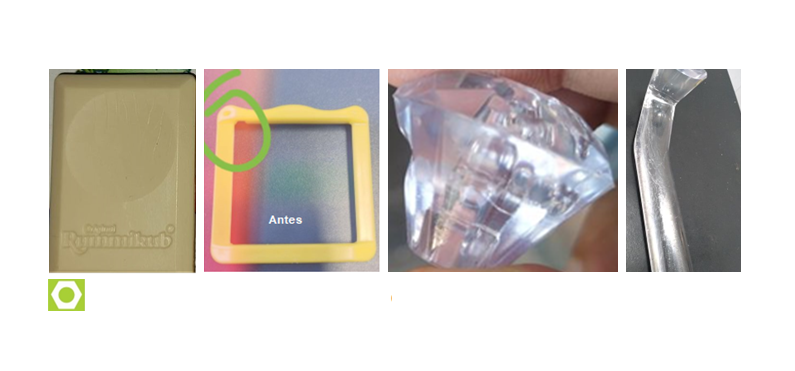
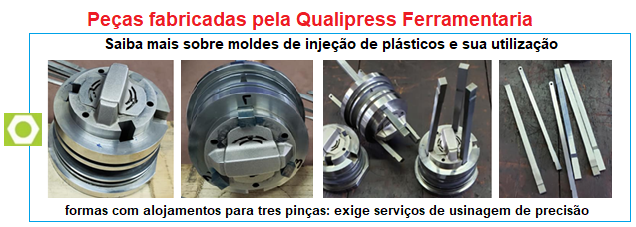
Defeito de injeção plástica em peças técnicas de PS
Este conteúdo abrange diversos problemas que ocorrem durante a injeção de diversos produtos plásticos no dia à dia. São resumos de casos apresentados e que receberam comentários e sugestões de profissionais. A ideia é levar a informação na palma da mão, para um melhor direcionamento no momento da necessidade. Se lhe interessa saber mais sobre molde de injeção, manutenção em molde e sobre defeito em peças plásticas indicamos nossos Estudos livres. http://moldesinjecaoplasticos.com.br/loja/
Acabamento com estrias / Material PS
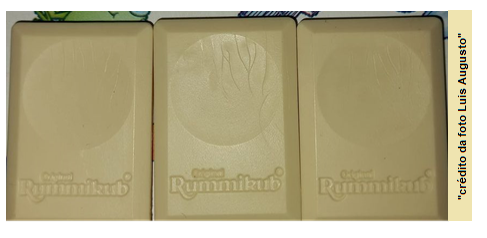
Problema: Peça saindo com estrias. Já alterei velocidade e temperatura, mas não resolvi.
Comentários:
– Coloca aquecedor 70C.
– A possível solução está na temperatura do molde.
– O ideal seria fazer um mapeamento e verificar algumas alternativas de temperaturas.
– A MP estando seca e estufada também ajuda.
– Abaixa velocidade pra 30 mm / s e injeta por tempo uns 6 segundos e vai aumentando aos poucos.
– Qual o local ponto de injeção?
Autor – Na lateral, mas na parte superior.
– Pode ser uma imagem de área interna.
– Qual a temperatura do resfriamento? Tenta colocar água industrial só no lado superior (lado da entrada injeção).
Autor – água gelada 10graus.
– Fecha a água só do lado superior e faz o teste, pode ser molde muito frio.
– PS é complicado mesmo, se tiver temperatura do molde muito fria o material durante a injeção encontra resistência fazendo essas rugas.
– Molde frio.
– Injeta lento até passar as letras e depois rápido, se não resolver, faz o inverso.
Autor – o canal é na lateral, mas não é centralizado, fica mais acima.
– Tenta preencher meia peça com a 1 injeção e o restante com a 2 com bastante pressão e tempo.
– Que tipo de material é esse?
Autor: PS.
– Aumente um pouco mais as temperaturas do material para ver o comportamento.
– Troca água para industrial, com certeza terá ótimo resultado.
– Para tirar essa estria tem que fazer a entrada de material em leque.
– Aumente o gate …aumenta a temperatura do canhão … e a velocidade de injeção.
– Faça também saídas de gás no molde.
– Aquecer o molde.
– Já injetei essa peça aqui no tabuado em uma indústria e realmente ela e muito chata… Isso aí é um quebra cabeça e dá para melhorar.
– Molde muito frio ou matéria prima muito fria.
Superfícies com rechupe / Material PS
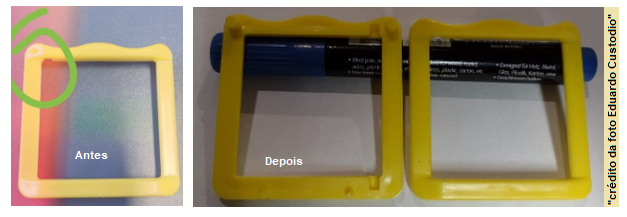
Problema: marcas de rechupe.
Comentários:
– Verifique:
-Tamanho e local do Ponto de injeção.
– Saida de gás suficiente.
– Temperatura do molde compatível com material.
– Capacidade de recalque.
– Verificar se não está resfriando o ponto de injeção antes de conseguir recalcar.
– Verificar possibilidade de alivio de massa no local.
Autor – Todas dica e informações vamos colocar em prática para ver os resultados.
– Falta uma saída de gás nesse local, tenta abrir um pouco o fechamento da máquina, já resolvi alguns problemas parecidos desta forma.
– Tenta fazer um perfil de injeção tente jogar o ponto de queima para o meio da peça injeta devagar no início e rápido no final p dar tempo de sair e gás aumente um pouco a temperatura p não ficar solda fria pecas pequenas queimam fácil no recalque o perfil seria ideal.
Autor – Material PS de auto impacto.
– Dá uma verificada na temperatura do molde e diâmetro do capilar, e reforçando:
– Verifique se não está congelando o capilar antes do recalque.
– É difícil ter certeza, porque na foto pode nos enganar, mas tudo indica que é a saída de gases deficiente, abaixa as últimas velocidades de injeção se não resolver pede para ferramentaria melhorar a saída de gases.
Autor – Já fiz a saída de gás, estou dando um suporte para a injeção.
– Mesmo que o material usado seja de alta fluidez, sempre é bom fazer um perfil de velocidade e não uma só, evita esses pontos de saída de gases.
– Devido ter um acúmulo de massa nessa área, ideal é fazer uma saída de gás tipo -poço frio. Isso vai resolver o problema.
– 100% não vai conseguir, a peça de parede grossa mesmo com todos os recursos, vai ter uma pequena deformação …
– Se o gás não sair ele vai queimar ou ocupar o espaço que seria preenchido cm o plástico.
– O mais fácil seria fazer uma saída ” eficiente” de gás ou acertar o perfil de injeção nesse ponto.
– Diminui a velocidade de injeção e tem atenção à 2a pressão, para a peça não ficar chupada.
– Deve ser saída de gás, talvez se você aliviar um pouco o travamento resolve.
– Provavelmente pode estar faltando uma saída de gás neste local da peça, tenta tirar um pouco do trancamento da máquina. Pode estar usando muito fechamento.
– Dessa forma já aconteceu comigo, estava com muita força de fechamento e abaixei resolveu, as vezes a capacidade da FF da máquina pode ser desnecessário para um molde pequeno.
– Essa peça já injetou sem chupagem nesse ponto? Ou são as primeiras peças? Teria que ver atrás da chupagem se tem algum relevo. Tipo um encaixe para parafusos.
– Se possível faça uma segunda entrada de material nessa região, ao recalcar conseguirá eliminar o chupamento, o que pode acontecer como resultado não satisfatório é uma marca de emenda em algum outro ponto aí.
– Teem que avaliar a relação se compensa ou não.
– Saída de gás e velocidade baixa resolverá o problema.
– Recalque.
– Diminui um pouco a velocidade de injeção, veja se está sobrando colchão para recalque.
– Saída de gás, faça uma saída de gás top.
– Adiciona expansor no material.
– Não é necessário.
– Então é injeção, pode até ser que tenha muita massa, mas não consigo eliminar.
– Marca da extração.
Lateral da peça com rechupe / Material PS
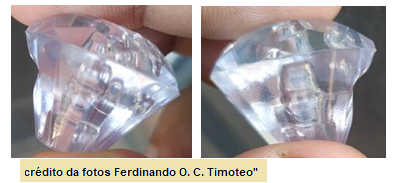
Problema: rechupe.
Comentários:
– Peças com excesso de massa, devem ser injetados com baixas velocidades e molde com temperaturas mais elevadas 60 a 70°C, para conseguir recalcar por mais tempo e dar tempo para esfriar a parte interna.
– Aqueça o molde e reduza a velocidade de injeção que terá sucesso.
– É isso mesmo, velocidade baixa e tempo de recalque mais alto, temperatura do molde da água também entre 45°a 50° graus, tendo tempo de resfriamento variante com recalque.
1. Qual o tipo de injeção?
2. Quantas cavidades tem o molde?
3. Qual o peso da injeção completa?
4. Qual a capacidade de injeção da máquina?
4. Qual diâmetro do furo da bucha e do bico da injetora?
A princípio tente utilizar:
– Temperatura de massa a mais baixa possível desde que mantenha a segurança de operação da injetora.
– Temperatura de refrigeração do molde em torno de 60 graus.
– Velocidade de injeção a menor possível desde não apresenta linha de fluxo, tipo ondulações, na superfície da peça.
– Pressão de injeção alta.
– Tempo de compactação alto; verificar o tipo de entrada, se for muito restrito ocorrerá solidificação da entrada e perda fé pressão na cavidade.
– Tempo de resfriamento suficiente para que a peça saia do molde com a superfície não muito “mole”.
– Só juntava a parte de estufar muito bem o material. E verificar fugas de ar no molde.
– Esse material não é hicroscópico (PS std), pouco interfere a secagem. Teu caso é mais de ajuste de processo é deficiência de molde ou máquina.
– Importante saber se for galho pode estar tendo o efeito bexiga enche e ao final do recalque no início de dosagem ele volta.
– Pode ser a temperatura do material muito alto ou tenta aumentar o recalque.
– Aumenta o tempo de recalque e pressão.
Autor – Cheguei a deixar 6 segundos de recalque e não deu resultado, vou aumentar o tempo de injeção. Que acha?
– Pode aumentar, mas faz um perfil de recalque, essa parede e muito espessa aumenta.
– Pode ser, diminui a comutação, tenta aumentar a pressão do recalque, pelo jeito é uma peça grossa.
Autor – Sim ela é grossa, tenho que terminar de resfriar na água.
– Veja se o molde está resfriando bem as vezes é a temperatura do molde.
– Eu colocaria refrigeração no molde, o PS aceita molde frio, não gelado e seguia as dicas de regulagem dos colegas.
– Eu deixaria o molde sem refrigeração, pois são peças pequenas, porém com parede grossa.
– Acelerar o ciclo respeitando tempo de preenchimento da peça com mais 2s, resfriamento o suficiente para extrair, aí pegar a peça sem rechupes, porém vai rechupar na sua mão depois, por isso deve cair na água fria para se manter. Ganha produtividade se conseguir resfriar na água e não no molde.
– Parede muito grossa, sai sem rechupe, mas contrai fora do molde, colocar em água ajuda.
– Pode ser o ciclo muito rápido.
– Tente reduzir a velocidade de injeção e aumentar o tempo de compactação, bom trabalho.
– Tempo de recalque e pressões alta e velocidade de injeção também um pouco baixa. A peça é muito espessa (grossa)
– Diminua a temperatura do material, Caldeira, aumente a contrapressão, mas diminua a velocidade de carga para tirar as bolhas, aumente o recalque e diminua a velocidade de injeção.
– Recalque e tempo de resfriamento, aumenta os dois e diminui a temperatura da água
Autor – Geladeira está em 13 graus.
– Abaixa para 10, e vê a saída de gás do molde. Às vezes é só limpar, diminuir velocidade de injeção também.
– Se realmente é rechupe aumentar o recalque, mas pode ser ar preso, daí reduz a velocidade de injeção.
– É um material não higroscópio o PS, mas se fizer uma pre secagem a 60 graus por 2 horas pode também reduzir bolhas internas, trabalhar com velocidade lenta.
– Tenta trabalhar com 20 a 30 % de recalque.
– Qual temperatura está usando no aquecimento do canhão, que tipo refrigeração no molde, qual a velocidade de injeção, onde está localizado o ponto de injeção, quantas gramas tem a peça?
– Para esse tipo de material tem que ser água aquecida no lado móvel e fixo e baixa o tempo de dosagem.
– Esse rechupe é no ponto de injeção? Se for baixa temperatura do bico e da zona logo depois do bico e use o mínimo de descompressão se estiver usando.
– Recalque tempo de resfriamento antes da dosagem baixa velocidade de injeção.
– Tem que aliviar massa, projetar saídas de gases ou injetar em baixa velocidade…
– Diminuir bem velocidade da RPM e aumentar contrapressão ajuda muito e trabalhar também com ciclo baixo.
– Contra pressão alta.
– Velocidade baixa.
– Pressão alta.
– Pode ser que resolva.
– Verificar saída de gás.
– Velocidade de injeção e abaixa velocidade de plastificação.
– Testa fazer as peças caírem na água gelada ao extrair do molde, fazemos assim com os cabides de roupa em ps cristal.
– Pode ser refrigeração.
– Aumenta a contrapressão que resolve.
– Diminui o tempo de injeção aumenta velocidade e pressão.
– Velocidade baixa, pressão alta, se o canal for direto muito tempo só recalca o canal
– Isso só pode ser o tempo de recalque muito curto. Faz o teste aí.
– Qual a grade que você está usando?
– Embora nunca tenha tentado, pode ser o recalque aumenta um pouco, em PP sempre ajuda.
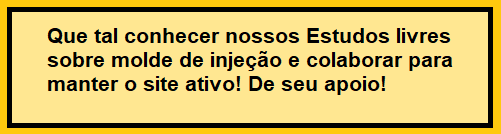
Peça com estrias internas / Material PS
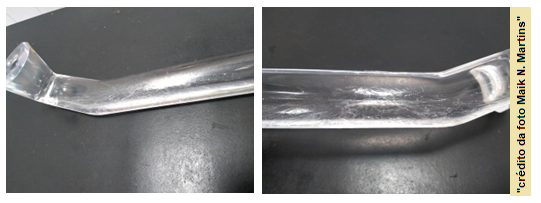
Problema: estrias brancas internas.
Comentários:
– Tenta aumentar a temperatura. Verifica também a entrada de material, se não está muito pequena restringindo o fluxo do material.
Autor – Vou verificar.
– Antes, aumenta um pouco a temperatura antes de mexer no molde.
– Você está com problema nas entradas de material no produto. Está estrangulada.
Autor – Estou entrando com canal laminar de 5 décimos, mas vou verificar isso.
– 0,5 é muito pequeno. Este material é muito pastoso.
– Aumente aos poucos, tanto na altura como na largura.
– Analisando assim, por foto fica um pouco difícil de saber o real motivo, mas a princípio parece marca de desmoldante, depois aumenta um pouco a temperatura do bico ou câmara quente para aumentar a fluidez do material, olha nas especificações do material o ponto de fusão e coloca uns 25° a mais.
Autor – No primeiro momento eu também achava que era desmoldante, mas foi bem limpo a cavidade.
– Então sem dúvida é a temperatura baixa do molde, o material está se solidificando muito cedo, isso causa essas estrias, aqui conhecemos como junção ou emenda fria
– Tira a água industrial e coloca aquecida. 65° já melhora isso.
– Põe água aquecida, entre 65 e 70°, mais pressão e menos vazão de injeção…
– Aumenta o canal de injeção, aquece o molde, sobe um pouco a temperatura do material, aumenta a velocidade de injeção e usa menos desmoldante……vai melhorar o seu processo….
Autor – Não estou usando desmoldante, mais obrigado pelas orientações.
– Terá que fazer alguns testes entre pressão e vazão….
– Se nenhuma das dicas deu certo, pode ser material úmido. Tenta deixar estufando conforme data shift do fornecedor. Geralmente para PS usamos temperatura da estufa em 80°C por 3 horas, baixando para 65°C à 70°C após o período de estufagem inicial.
– Exatamente, eu trabalho com esse material e tem que estufar o material a 70° e também a temperatura do molde é primordial….
– PS cristal, PMMA acrílico, PC (policarbonato), são chatos para injeta, muita calma….
Autor – Vou fazer outro teste em PMMA. Qual temperatura você indica para estufar PMMA, e temperatura do cilindro.
– Tem que controlar também a velocidade de injeção se não a peça trinca, começa devagar a velocidade, o molde não pode estar gelado (água industrial) material estufadinho…vai com calma que consegue.
– 210/230 graus dependendo do canhão.
– Pode tentar estufar o material por 3 horas a 65 graus.
– Fazer polimento onde entra o material.
– Aquecer o molde a 60 graus.
– Fazer canais de escape de gases no molde.
– Está trabalhando com refrigeração água gelada no molde?
Autor – Eu tirei só um teste no molde, ainda não tenho refrigeração.
– Está com cara de umidade.
– Parece problema de fluxo, verifique temperatura do material do molde, canal de injeção.
– Esse tipo de peça, grande e parede grossa, é fundamental uma câmara quente valvulada!
– Gate no mínimo de 4 mm de diâmetro.
– Material está entrando espirrando! Gate deve estar estrangulado.
– Pode medir o teor de umidade da sua matéria prima, deve estar acima do especificado pelo fabricante.
– Temperatura do cilíndrico de injeção e refrigeração do molde com água natural e não gelada.
– Parece mancha de desmoldante.
– Saida de gases, molde frio, temperatura do material baixo, velocidade de injeção bico instruído
– Isso parece um vazamento de água
– O molde tem que trabalhar com temperatura de 60 graus água controlada tenta colocar pra ver se melhora
– Talvez o termopar de temperatura da zona não está lendo corretamente pedir para a manutenção verificar todas as zonas pra ver se tá lendo corretamente.
– Só existe 2 causas para este problema…temperatura ou umidade.
– Dá para ver que a peça está espirrada, se for injeção direta deve está quebrando a ponta do canal de injeção e injetando em cima da peça na injeção seguinte, se for Câmara quente ou sequenciador verificar o acionamento e temperatura!
– Já tive esse tipo de problema, principalmente no início de processo, consegui resolver aumentando a temperatura do molde e recalque.
– Parede muito grossa o material está entrando em spray, uma mudança no canal de injeção para o plástico não entrar direto no vazio ajuda, tem a peça com o galho.
– Acho que pode fazer algumas saídas de gás no molde. Melhorando assim o escape do ar retido e liberando espaço para o material fluir.
– Molde está frio
– Precisa ser molde mais quente e pressão mais alta e velocidade de injeção tão baixa quanto possível
– Pressão alta com velocidade baixa não funciona. Pressão é resposta da velocidade.
– Verifica a contra pressão… Uma contra pressão mais alta vai melhorar a homogeneização do material
– Pode ser umidade, pode ser baixa temperatura do molde, pode ser baixa temperatura da massa. Outras coisas que podem ser, mas não acredito por conta de ser na peça toda são posição do gate e alta velocidade de injeção.
Estrias junto ao ponto de injeção / Material PS
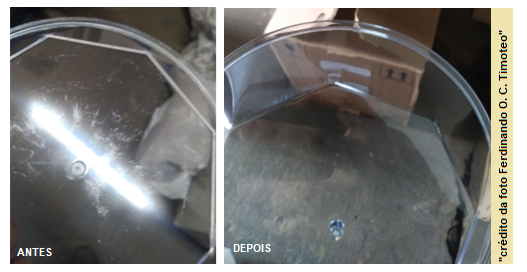
Problema: com estrias junto ao ponto de injeção. Material PS Cristal.
Comentários:
– A descompressão é um recuo da rosca após terminar a dosagem para aliviar a pressão do material na frente da rosca, ajuda a evitar que fique babando material no bico ou na bucha, mas pode gerar manchas como essa da foto e também queima de gás próximo ao ponto de injeção, é necessário ajustar outros parâmetros, também.
– Tem também a descompressão dianteira, é o recuo da rosca após o término do recalque e /ou retardo de dosagem para aliviar a pressão na frente da rosca após injeção e antes da dosagem.
– Muito obrigado pela excelente explicação. Sabia da possibilidade da sua descrição, mas não sabia que havia um termo específico.
– Excelente explicação, isso mesmo. É importante salientar que o tempo do retardo utilizado deve se somar ao tempo da dosagem e ambos precisam ficar menor que o tempo de resfriamento, para que não haja perda no templo de ciclo.
– Pode ser, descompressão, temperatura do bico alterada, estufa, tem várias opções de ajustes deste problema tem que ir com paciência, passo a passo, mas e relativo a questão de temperaturas, ou atritagem, velocidade pressão descompressão, aí por diante.
– Descompressão é o recuo da rosca de plastificacão.
– Descompressão traseira no caso.
– Nas máquinas que trabalho uso uma margem sempre para descompressão e sempre trabalha de boa, tipo se a posição final de dosagem é 100 eu padronizo 10 pra mais de descompressão aí a máquina faz sozinho, caso baixe a posição final tipo para 80 a máquina baixa sozinha a descompressão, sempre fica 10 para mais e aí, não tem problemas de esquecer a descompressão alta.
– Está úmido.
– Veja também se não está ficando material frio no ponto de injeção.
– Bico quente, baixa temperatura.
– Diminuiria a temperatura do bico, tirava o máximo possível de descompressão e estufava o material.
– Estufa o material, absorver muita unidade.
– Todas as dicas são boas, a descompressão é o primeiro fator, mas pela imagem dá para ver que o produto tem uma parede fina e um diâmetro regular…. seria bom para tirar proveito, adicionar + velocidade de injeção…e acompanhar com um pouco de temperatura…peças assim depende de um ciclo rápido…para manter uma constante, evitando esse problema.
– Descompressão, alta.
– Matéria prima degradada ou contaminação.
– Parece ser umidade, mas não é, só aumentar a carga e usar mais contra pressão, isso irá resolver.
– Se for matéria prima úmida, resolve se deixar um pouco mais desumidificando, mas também aparenta ser muita descompressão.
Solução:
Autor – Somente diminuindo a descompressão consegui injetar com qualidade.
Peça circular com acabamento ruim / Material PS
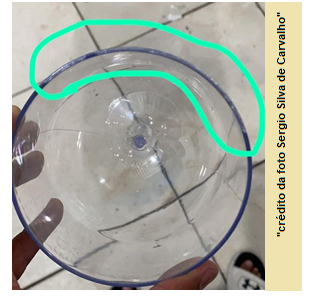
Problema: Acabamento ruim.
Comentários:
– Falta ventilação na linha de junta.
– Utiliza contrapressão elevada.
– Injeta rápido.
– Abertura e fechamento do molde rápido.
– Aumenta a temperatura da massa.
– Reduz o curso de abertura o máximo possível.
– Não dá pra ver bem pela foto, qual o material?
– Se está leitoso é contaminação, bolhas pode ser umidade, faz um teste aumenta a contra pressão.
– Fluidez do material.
Autor – média fluidez
– Quando tem bolhas aqui trabalho com menor fluidez.
– PS?
– Tem reciclado no meio?
Autor – Não, material novo.
– Então pode seguir a orientação dos colegas com maior cizalhamento do material.
– Pouco mais de contrapressão e ou baixar rotação do fuso.
Autor – ok
– Limpa a linha de fechamento do molde, isso é gás. Aparece bastante no poliestireno.
Autor – melhorou.
– Tira um pouco de material, está recalcando muito.
– Faço uma peça semelhante, tira um pouco o travamento.
– Falta de uma boa saída de gás no molde, pode ser a causa dessas manchas aí…
– Falta de saída de gazes ou regulagem do colchão.
– Saída de gás, caso não possa abrir muito, tente baixar a velocidade de injeção, mas pode deixar a peça ondulada.
– Isso mesmo… saída de gases… para resolver tem vários caminhos… limpar bem as saídas com álcool, reduzir velocidade e pressão de injeção… se isso te fizer perder muito tempo de ciclo tenta fazer um perfil e reduzi-las só no final de injeção e verificar se o recalque não está com pressão demais.
– Projeto do molde, sem travamento do macho, assim como em moldes de parede fina, resultado, deslocamento devido a excesso de pressão, com parede da peça com diferentes espessuras.
Não sei porque no Brasil os moldes são geralmente construídos, com as dimensões mínimas de aço, que na construção do molde não ultrapassa 10% do custo total do molde.
– Saida de gás só isso.
– Talvez saídas de gases obstruídas.
– Fora obviamente o desenho das saídas de gás….
– Não estou vendo as saídas de gases na planta da matriz / cavidade do molde…
– Ou é saída de gás ou é cola na cavidade.
Esperamos ter colaborado com os profissionais!
Fonte: Grupos Técnico em Plásticos e Injeção Plástica do Facebook
Apenas Resumo: Moldes Injeção Plásticos
Acesse: isso também irá facilitar o trabalho do profissional:
TABELAS COM VALORES PARA APLICAÇÕES DE TERMOPLÁSTICOS
INDICAÇÕES PARA O PROCESSAMENTO DE DIFERENTES MATERIAIS PLÁSTICOS – 01
INDICAÇÕES PARA O PROCESSAMENTO DE DIFERENTES MATERIAIS PLÁSTICOS – 02