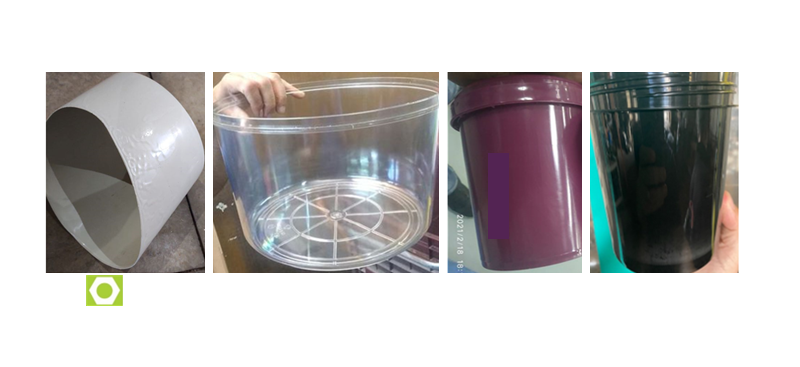
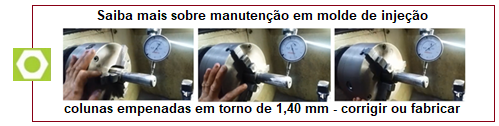
Problemas com injeção de potes e baldes plásticos.
Este conteúdo abrange diversos problemas que ocorrem durante a injeção de potes e baldes plásticos no dia à dia. São resumos de casos apresentados e que receberam comentários e sugestões de profissionais. A ideia é levar a informação na palma da mão, para um melhor direcionamento no momento da necessidade. Se lhe interessa saber mais sobre molde de injeção, manutenção em molde e sobre defeito em peças plásticas indicamos nossos Estudos livres. http://moldesinjecaoplasticos.com.br/loja/
Pote / Manchas brancas / Material CP 141
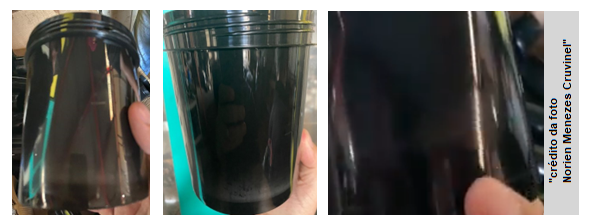
Problema: na injeção do pote somente na cor preto, estão aparecendo manchas brancas. Já trocamos o master/fornecedor do preto e continua com o mesmo problema, o material que estamos usando e o CP 141.
Comentários:
– Mistura o Master direto com a matéria prima.
– Possivelmente, saída de gás.
– Provavelmente fluxo da água passa por aí, experimenta deixar o molde um pouco mais quente, pelo menos parte móvel.
– Temperatura do canhão influência, quando tenho esse problema nas minhas peças, abaixo temperatura da cavidade – Uso CP-141.
– Aumentar a temperatura da água de refrigeração do molde e alterar a velocidade de injeção.
– Aumentar velocidade de injeção ajuda ou deixar a temperatura do molde da parte móvel mais quente.
– Vários fatores podem ocasionar isso, até o polimento.
– Tenta injetar algumas peças sem refrigeração na parte fixa e depois com uma injeção lenta, mas com pressão forte para dar tempo de o gás sair.
– Verifique a saída de gás do molde.
– Saída de gás.
– Parece master mal misturado.
– Dá uma olhada na contrapressão, dá uma homogeneizada.
– Faça um teste, afrouxa o fechamento da máquina até dar rebarba, se ficar bom, é que falta saída de gás e a velocidade da injeção está alta além da temperatura do bico TB estar alta.
Autor – Isto eu não fiz ainda, vou fazer no fechamento.
– Já tive problema assim, segue o pigmento e o material 2.5 horas de estufa já vai resolver.
Autor – Não deixei este tempo todo na estufa, mas vamos testar também, estou testando tudo.
– Manchas brancas, normalmente é de material úmido.
Autor – Já colocamos o material na “estufa” nada de melhorar.
– Sou polidor técnico em molde, tem que ter saída de gás.
– É só tirar a água gelada.
Autor – Já tiramos a água gelada, estamos fazendo com água natural.
– Reparou se onde as manchas aparecem o molde está bem polido? Porque às vezes o polimento interfere na cor, principalmente na cor preta que absorve todo aspecto das cores.
Autor – O molde está polido, mandamos fazer o polimento para ver se as manchas iriam sair, mas nada delas sumirem.
– O estufamento de 3 horas e meio irá sumir as manchas.
– Estufamento de 120 graus.
– Já verificou se as manchas são todas iguais, ou seja, se olhar duas peças, uma ao lado da outra, as manchas tem o mesmo formato?
– Isso está parecendo mancha na matriz do molde. Em outras cores pode disfarçar e não se percebe, mas no caso específico deste preto pode estar realçando.
Autor – Já fizemos polimento e continua com as manchas, e às vezes ela muda de lugar, não é sempre no mesmo lugar.
– Faça a peça falhar e abra o molde bem lento, se perceber que houve alguma melhora, aplique um pouco de desmoldante nesta região, pois está me parecendo que a peça está muito compactada e revela a marca da matriz.
– Tem saída de gás no molde?
Autor – Tem sim, até mandamos fazer outras saídas para ver se melhorava, mas nada, mesma coisa.
– Retira o recalque como teste e verifica se o resfriamento do molde está uniforme.
– Já tentou colocar água quente?
Autor – Já tentei, água natural continua a mesma coisa.
– Diminui a descompressão e baixa um pouco a temperatura, acredito que melhore.
Autor – Vou tentar.
– Outra coisa que pode testar também, aumentar um pouco a contrapressão, o material e o master dentro do canhão misturam melhor. começa na descompressão, zera ela e vê se melhora, e aí caso não funcionar, parte para temperatura.
Autor – Vou fazer as sugestões.
– Usar água natural e aumentar o tempo de ciclo talvez ajude é umas das opções…
Autor – Já fizemos e não resolveu.
– Velocidade de injeção.
Autor – Já baixamos e não resolveu o problema. Colocamos a velocidade bem baixa e não adiantou, continua com o mesmo problema.
– Já injetou sem master. Só material puro pra ver se continua a mancha?
Autor – Com outros master não deu este problema, só no preto que está me dando este trabalho.
– Mancha fria, molde frio demais, pode usar a refrigeração do molde com água em temperatura ambiente, ou por um aquecedor.
Autor – Já fizemos o teste com água natural continua aparecendo as “manchas” brancas.
– Tentou aumentar a temperatura do processo?
Autor – sim, já aumentamos, já baixamos e nada das manchas sumirem.
– Se colocar água quente na parte fixa esse problema acaba. Outro ponto esse pote passa por esteira fechada após ser injetada?
Autor – Está trabalhando com água natural, não passa por esteira após a injeção.
– Então o ideal mesmo seria colocar aquecedor na parte fixa do molde.
– O master não tá misturando direito com o material, tem que aumentar a contra pressão e talvez dar um tempo a mais de resfriamento.
Autor – Vou tentar mexer mais na contra pressão, já tentei aumentar, diminuir e nada das machas sumirem.
– Qual a temperatura da água na refrigeração do molde. Produto com muito brilho principalmente na cor preta necessita que o molde esteja mais quente.
Autor – Estamos trabalhando com água na temperatura natural, da torre.
– Qual a porcentagem de Master que está usando?
– Parece que não está homogeneizando o Master ou até parece que tem pouca % de máster.
Autor – Já colocamos 1%, 2% e 3%, e já mudamos de fornecedor do master e continua com a mesma mancha.
– Tenta colocar mais master apenas para fazer um teste. Se não melhorar não está tendo compatibilidade entre material e Master.
– Outra coisa é relação ciclo x temperatura que está em utilização, caso o ciclo seja muito rápido, trabalhe com a temperatura do canhão um pouco maior.
– Veja se no molde não tem resíduo de outra cor, geralmente passar um algodão com benzina pode resolver.
Autor – Já fizemos novo polimento no molde para ver se poderia ser algo no molde e continua com as manchas.
– Polimento e água quente no lado fixo.
Autor – Já fizemos Polimento, e estamos usando água natural.
– Desobstrua as saídas de gás, dá um polimento no molde e experimente colocar aquecedor no molde.
Autor – Já fizemos até mais saída de gás, e estamos usando água natural.
– A mancha muda de posição quando se altera a velocidade de injeção?
Autor – Sim, muda.
– Tira todo recalque, observe se vai marcar.
– Tenta diminuir bem a contra pressão, não sei qual é seu ciclo e tempo de residência, mas parece que está empurrando material frio na dosagem. O brilho está em todo contorno da peça. Tente também dar um retardo na dosagem se o ciclo permitir, verifique também o bico quente a temperatura tente baixar um pouco.
Autor – Vou mexer mais na dosagem para ver se temos algum resultado.
– Qual seu ciclo?
Autor – Já testamos com ciclo alto de 45 segundos, como também com ciclo que usávamos em outras cores, 24 segundos.
– O problema persiste?
Autor – Sim, paramos hoje com o preto e mudamos de cor, pois outro cliente não pode esperar, mas vamos voltar para o preto novamente, e na nova cor (“bege”) não tem este problema.
– Como molde está de saída de gás. Ou master.
Autor – O problema está acontecendo somente com o preto, já aumentamos as saídas de gás, e mudamos o master, mas na cor preta está dando este problema
– Experimenta com mais de um perfil de injeção. Acrescenta mais uma ou duas velocidades.
Autor – Vou tentar.
– E varia também a pressão nessas mesmas velocidades.
– Utilize o método short shot, ou seja, preenchendo aos poucos e observe se a mancha permanece no mesmo ponto mesmo com a peça falhada, ou apenas totalmente preenchida. Pelo que percebi está logo após o ponto de injeção, possivelmente turbulência, avalie diferença de espessura nesta região, avalie aumentar o bico de injeção e bucha de injeção.
– Gás combinado com velocidade de injeção alta.
– A peça deve estar resfriando muito rápido tenta molde aquecido.
Autor – Estamos usando água natural, já tentamos até com o molde quente, continua aparecendo as machas.
– Tenta uma injeção com PP homopolímero.
– Pode ser resíduo de outro tipo de material na rosca.
– Diminui o tempo de injeção.
– Já fez o polimento no sentido de saída da peça?
Autor – Sim, foi o que fizemos esta semana, não resolveu.
– Alivia um pouco o fechamento até sair um pouco de rebarba.
– Tem mix para misturar o material com o pigmento antes de entrar na rosca?
Autor – Não entendi o que seria mix, seria misturador da resina com o master, se for sim.
– Isso mesmo.
– Aumentar a temperatura do molde.
Autor – Já fizemos isto, deixamos ele trabalhar quente, e não resolveu.
– Acredito que seja relativo a resina utilizada, pois tive um teste com um produto parecido onde utilizei este mesmo copolímero e apresentou resultado parecido, em outra tonalidade talvez não apareça mas no preto é visível então, sugiro que utilize um outro material mais translúcido, se preferir utilize um homopolímero Random que não fica quebradiço. RT 400 por exemplo seria uma boa matéria prima para realizar este teste. CP 141 é um pouco “leitoso” e interfere na tonalidade final no preto.
Autor – Vou testar, o ruim que para comprar matéria prima na situação de hoje está difícil de achar.
– A injeção é ponto quente?
Autor – 4 cavidades bico quente.
– Essa marca aparece no contorno todo ou só uma parte.
Autor – Às vezes em quase todo o contorno, às vezes de um lado somente, mas não estão sempre no mesmo lugar.
– Material não está homogeneizando, precisa rever, temperaturas do cilindro de injeção, contrapressão, tempo de residência, resfriamento maior, ver se a porcentagem de Master está de acordo, velocidade de injeção.
– Também acredito nestas hipóteses.
Tenta observar na hora da extração, daqui representa que o pote está estufando. Ainda mais se não tem uma válvula de ar para tirar o vácuo.
– Água gelada.
– Mancha de fluxo, molde quente, temperatura alta, o MB degrada.
– Qual a porcentagem de MB? Em pó ou granulado?
Autor – Fizemos com 1 a 3% granulado.
– Outro teste mais fácil, usar o pigmento preto em pó, sem veículo nenhum, (negro de fumo), as vezes a base do seu master está manchando a peça.
– Umas das coisas que tem que olhar é se tem alguma parte do molde que esteja negativo, ou 100 % paralelo, sem nenhuma conicidade, isso pode causar uma mancha parecido com o que está acontecendo.
– Uma tentativa para saber é injetar umas peças sem pressão de injeção até ir completando devagar a peça, se a peça não marcar mesmo que ela não complete, verifique a conicidade da saída da peça.
– Diminui pressão de injeção e fluxo e também aumentar um pouco contra pressão.
– Coloca o acionamento do quebra-vácuo e válvulas pneumáticas do macho, depois que sair totalmente da matriz.
– Se estiver usando água gelada no macho do molde, tenta deixar o fluxo menor pra não condensar o molde esse problema também pode ocorrer.
Faça um teste simples feche a água, injete algumas peças e observe se o problema continua.
– Falei pra usar água natural.
Autor – Estou usando água natural.
– Então neste caso coloque água controlada nas duas partes do molde, coloque água entre 40⁰ a 45⁰ nas duas partes do molde, se continuar o problema daí parte para um polimento ou algo mais específico porque o problema é no molde.
– Eu sempre verifico todas as possibilidades antes de fazer algum investimento, pois muitas vezes é feito um investimento alto e o problema continua.
– Olha aqui, pode ser molde muito frio, (injeta com água natural com 28°c,
Autor – Este teste da foto já estamos fazendo com água natural
– Ou pode ser material não desumidificador se for (pp) colocar o desumidificador em 110°c.
Autor –Vou colocar para testar.
– Já tentou escalonar a velocidade de injeção?
Autor – Tentamos, mas não resolveu o problema, fizemos teste de vários escalonamentos. Estou fazendo todas as sugestões que não tinha feito antes, ainda não tive um resultado 100%, mas estou tentando.
– Essa extração como é feita? Olhe se não está forçando a peça na hora de extrair
Autor – Vou verificar novamente com mais carrinho para ver se achamos algo.
– Provavelmente essas marcas são do outro material que você injetou antes.
Autor – Acho que não é resíduo de outra cor, pois já usamos outro produto para limpeza antes da injeção, e já injetamos bastante testando.
– Tive um caso parecido numa empresa, trocamos as ponteiras, testamos com saída de 2 furos, de 4 furos e de 1 furo ……só a de 1 furo deu certo, mas a cor que saia com mancha em amarelo, o resto era normal ……..tente algo assim, vai que dá certo.
Mas parece mesmo que o material está aquecendo muito, o preto absorve mais o calor ……talvez de certo.
– Aumenta o canal da injeção no molde.
– Também tivemos problemas com essas manchas, a causa era o material utilizado, uma dica é injetar somente a resina e observar se a mancha continua.
– Só acontece isto na cor preta.
– Então é gás gerado na plastificação, tentou fazer uma blenda para ver se há diferença?
– Pelo vídeo a mancha está localizado em uma posição bem definida da peça, parece que tem uma diferença de temperatura na cavidade, indico instalar um termo regulador e testar com água quente.
– Já observou a cavidade do molde? Se está com alguma oxidação?
Autor – Sim, está boa, até mandamos fazer um polimento nela.
– Essa mancha é só por fora? Se passar uma flanela não sai?
– Eu trabalhei com potes 10 anos, por incrível que pareça isto é molde e problema está na parte fixa, com o tempo o aço vai criando ondulação, é necessário fazer uma regulagem da extração pneumática na parte fixa em 0,1 mm, e o primeiro curso de abertura 20mm aproximado bem lento, reduzir o tempo e pressão de recalque o mínimo possível, injetar bem rápido e aumentar o tempo de resfriamento ou refrigeração + gelada.
– Nas cores claras você vai perceber com reflexo da luz, que contém ranhuras também, porém menos visível.
– Fluidez do material também deve ser bem alta.
– Um polimento na parte fixa vai ajudar também.
– Também pode ser que o alimentador na puxa a quantidade de pigmento certo para pesar, aí tem que abastecer na mão e fazer um teste se sair a mancha e só o alimentador que não está jogando a quantidade certa de pigmentos.
– Se for possível e tenha a disponibilidade e equipamento, faça um teste de MFI (índice de fluidez), na resina matriz, lote atual e anteriores e também da fluidez do master.
– A demanda de insumos disponível no mercado está bem complicada no sentido de preço nas alturas e qualidade na contra mão.
– Possivelmente possa estar exclusivamente acontecendo na cor preta por fluidez baixa, “possivelmente”, mas também possa estar relacionado ao molde especificamente naquela parte se acontecer somente lá pode estar relacionada a alguma sujidade onde seria necessário limpar a região de resfriamento do molde.
– Em uma segunda etapa, também se possível, faria alguns testes com aditivo auxiliar de fluxo a base de fluoropolímero. (como ação ele reduz a viscosidade, aumentado a fluidez, mas apenas durante o processo, assim melhora o escoamento do fundido).
– Apenas algumas observações, espero que ajude no seu problema, vendo por foto e vídeo acaba sendo um pouco mais complicado.
– Verificar saída de gás e o molde. Sugiro molde principalmente se a mancha for no mesmo lugar.
– Verificar a velocidade da extração, velocidade da injeção ou polimento da matriz também as saídas de gás
– Já calculou o tempo de residência do material?
– Umidade do material.
Pote / Diferença de tonalidade / Material PP
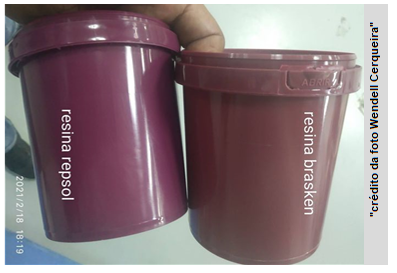
Problema: Poderiam explicar quimicamente a diferença de tonalidade entre as resinas copolímeros, ambas utilizando mesmo pigmento, sendo que a resina Repsol é a cor padrão.
Comentários:
– Precisa ver se a Resina que você utilizou tem a mesma organização molecular, saber se é PP Randon, PP Copolimero heterofasico ou PP Homo, precisa assimilar as resinas com os datashets dos fabricantes.
– Quando se usa um master com uma determinada resina e for trocar de resina, o ideal é VC mandar para o fabricante de master a resina q VC vai utilizar com a cor desejada…
– Ou vai ter que fazer na tentativa e erro… mas demanda tempo….
– Parece que teve aumento no tempo de residência do material no canhão.
Autor – Injeção simultâneo com mesma regulagem, temperatura normal. Realmente o lote da resina está dando esses problemas precisamente no pp copolímero e nos master vermelho.
– Isto está relacionado ao grau de empacotamento das moléculas, pois isto interfere na difração dos raios de luz no polímero, ou seja, por mais que ambos sejam PP copolímero um tem maior distanciamento molecular que o outro.
– Então em uma cor ficará mais aberta e no outro mais fechada.
– As propriedades dos materiais são diferentes, para se conseguir deixar parecido as cores teriam que desenvolver um pigmento para cada resina.
– Existem três tipos de polipropileno. PP Homopolimero; PP Copolimero random; PP copolímero heterofásico. No caso em questão afirma ser ambos copolímeros. Parece que o BRASKEM é um copolimero heterofásico (PP com borracha) por isso, a cor opaca. Já o outro PP se for copolímero, é copolímero RANDOM. Pode se verificar pelo código do Grade: geralmente o PP RANDOM começa com R tipo RP345 e o Copo Heterofásico começa com CP tipo CP241, CP 442XP.
– Ao carregar levou mais tempo, tendo mais plastificação e provavelmente modificou a atuação do pigmento. Motivo rosca gasta, ou material não uniforme ao entrar no canhão.
Autor – Foram injetados nas mesmas condições, um após o outro.
Sei, mas uma deve ter demorado mais ao carregar e teve um tempo de residência maior dentro do canhão.
Autor – Não. Resinas diferentes.
– Com certeza não existe mágica neste negócio.
– Colocar menos pigmento na matéria-prima … Veja se resolve.
– Tivemos um caso semelhante, após testes verificamos que um lote da resina Braskem correspondia a cor padrão e outro lote não. Igual a imagem. Nesse caso foi comprado um master com resistência térmica maior. Custou mais caro, porém solucionou o problema.
– Infelizmente não tem o que fazer, vai ter que mudar a porcentagem do pigmento, para chegar no padrão.
– Estou lendo os comentários e tem a resposta mais assertiva. Há diferentes tipos de copolímeros e % de coponomeros. Daí a cristalinidade diferente e temperatura de processo também.
– Aqui na empresa ocorreu o mesmo problema o copolímero da Braskem reagia com alguns pigmentos que com outros matérias não ocorreu. Pedimos para o fornecedor de pigmento desenvolver o pigmento com o material da Braskem.
– O primeiro com mais temperatura e o segundo com menos temperatura.
Autor – Não.
– Isso não tem nada a ver com temperatura, tem a ver com a resina, provavelmente a da Braskem está aditivada com algum clarificante que interfere na cor do produto
– Acho que pode ser isso mesmo as vezes tem materiais que tem concentração diferente de alvejantes como clarificantes
– Com certeza o pigmento está degradando com a temperatura
Autor – Mesma temperatura 190 200 c°, injeção simultânea, mesmo master, resinas diferentes.
– Braskem % de master tem q ser menor absorve mais.
– Temperatura do material.
– Cada um dos materiais, podem apresentar características diferentes …a partir do momento em que são aplicadas temperatura e de contrapressão…como também velocidade de dosagem…!! se o pigmento apresenta tom diferente…os processos devem ser observados passo a passo …as resinas de cada um também podem ter reações diferentes …com base nesses nas propriedades mecânicas de cada um!!
– Sou colorista de masterbatch e gostaria de saber qual grade da Braskem foi usado nesse teste.
Autor – mp091 0066/21.
– Não entendi esse código.
– Está usando PP homo, copo ou Randon?
Auto – Copolímero.
– Sabe dizer qual o ponto de fusão, e fluidez de ambas?
– Nenhum PP de fornecedores distintos vai apresentar a mesma cor, pois são processos diferentes de produção, aí a diferença de distribuição das cadeias interfere diretamente na cor.
– Acho difícil isso ter relação com a resina. Mais fácil ser processo ou mistura
– Trabalhei como colorista e normalmente era o alvejante óptico que é colocado para a resina ficar mais branca… levando em consideração que ele usou a mesma máquina…Master e regulagem de processo.
– Se for PP pode ser um homopolímero e outro copolímero.
Autor – Ambos, homopolímero.
– Estranho, foi produzido no mesmo dia mesma máquina.
– Calor de temperatura.
– Veja um exemplo, a Braskem trocou o PP RP 347 pelo PP RP DP 179A dizendo que era contra tipo e quando utilizava o mesmo master nos dois Grades, tinha resultado diferentes devido ao aditivo que vinha incorporado na resina.
– Está queimando no processo.
Auto – Não.
– É que dá diferença entre fornecedores.
– Talvez esse material tenha mais fluidez, trabalha com menos pressão e temperatura, pelo menos no PS.
– Temperatura.
– Temperatura do processo muito alta.
– A impressão é que esse pode ser um material mais sensível.
– Apenas temperatura.
– A temperatura alta está queimando o material por isso essa mudança de cor.
Autor – Não.
– Acho que é muita temperatura está queimando material.
Autor – Não.
– Olhe no datasheet de ambos a rampa de temperatura pois a resina pode ter uma rampa menor e ter causado uma leve degradação levando a diferença de tonalidade.
Autor – Não funciona.
– Tá usando master?
Autor – Ambos pp homopolímero, usando master.
– Pode ser temperaturas de um material para o outro ou limite de tolerância do pigmento. Para mim é a cor base da resina, as vezes muda de um fornecedor pra outro.
– Respondendo quimicamente: Monômero de polipropileno da resina de peso molecular diferentes, resumindo temperatura de processo diferente uma da outra altera N coisas, uma delas coloração do produto final, por isso fazer várias amostras de processos diferentes.
– Começa comparando o granulado das duas empresas antes de pigmentar se for natural a resina, caso contrário faça amostras com diferentes temperaturas do cilindro e contrapressão.
– A cor não bate com a tonalidade amigo, pigmento diferente.
Autor – Mesmo pigmento.
– Sim a diferença está na resina, a Braskem puxa para tonalidade amarelo, testa aumentar a % do pigmento.
– Isso tem relação com a resina base da fabricação do master.
– Parece dois grades bem diferentes, não são nem semelhantes, fluidez, viscosidade e outros…
– Essa diferença sempre vai haver quando os fornecedores forem diferentes.
– É comum ocorrer essa mudança de tonalidade por alta temperatura de processo ou cisalhamento através da contrapressão.
Autor – Não funciona nesse caso.
– Devido a cor da base da resina, também pode apresentar alteração de tonalidade.
– Depende se um é copolímero e o outro homopolímero, o material copolímero naturalmente é na cor mais leitosa devido as ramificações da cadeia, já o homopolímero é na cor mais natural transparente, pois não tem ramificações em sua cadeia molecular, agora, se as duas resinas têm a mesma tonalidade, o que está pegando é temperatura de processo, no qual se deve acertar para cada resina, pois normalmente o master já é com base em PE.
– Difícil o mesmo fornecedor já é difícil manter o padrão fornecedor diferente então só
– Qual é a cor correta o mais escuro ou o mais claro se for o mais claro aumenta a temperatura do cilindro se for o mais escuro abaixe a temperatura
Autor – Não funciona.
– Deve ter branqueador óptico em uma delas.
– Qualidade de material diferente
– Faz a injeção das duas resinas na condição virgem, aí você consegue tirar dúvidas… Veja a diferença de tonalidade entre ambas…
– O que fazer? Peça pro seu fornecedor de Master desenvolver a cor com a sua resina. Forneça pra ele uns 5kg de resina e peça pra desenvolver duas formulações diferentes.
– Quais as resinas utilizadas? O master e o mesmo lote? O processo teve alterações?
– A diferença na tonalidade não é bem na resina e sim no pigmento. O que aconteceu foi uma reação química por causa dos tipos diferentes de catalizadores que é usado em cada uma das empresas. Braskem usado um tipo e a outra usa outro tipo.
– Normal. Fornecedor diferente. Chama um colorista pra ajustar seu pigmento.
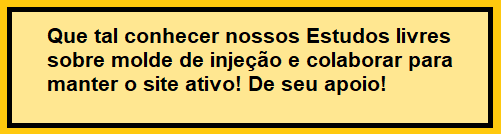
Pote / Peça amarelando / Material San
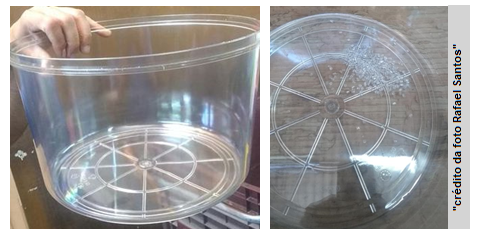
Problema: estou injetando San, o material é cristal, porém na injeção está amarelando, a temperatura do processo já está abaixo do especificado, geralmente eu uso a 230° estou a 200° e continua amarelado, o tempo de ciclo está em 40s.
Comentários:
– Nas fotos não ficou tão aparente, mas está amarelado
– Tempo de residência no canhão, vê se o tempo de dosagem está compatível com o tempo de resfriamento. Se o resfriamento for tempo alto, não tem porque dosar logo no começo do resfriamento, coloca um retardo de dosagem aí
Auto – Está sim, o tempo de resfriamento termina junto com a dosagem.
– Usa água gelada
Autor – Infelizmente não possuo geladeira aqui.
– Também acho que se diminuir a velocidade da rosca pode melhorar, pois o atrito queima o material.
– Exatamente….
– Injetei San muitos anos… pede para o seu eletricista verificar se todas as resistências do cilindro de injeção estão funcionando. Já passei por esse mesmo problema e no meu caso a resistência do meio do cilindro estava queimada. Mas antes tenta as opções citadas pelos colegas acima.
1. Como está a secagem do material? Não está oxidado? Compare o material depois de seco com o material sem secagem (do saco de MP).
2. Verifique se a temperatura registrada pela injetora está correta em relação ao programado (medir temperatura através de um equipamento externo).
3. Reduza velocidade de rotação da rosca e contrapressão.
4. Verifique se a borra já está saindo amarelada ou somente o produto injetado está apresentando o amarelado?
5. O molde é bico ou Câmara quente?
Autor – Esse o material não está oxidado, quanto a temperatura estou sem equipamentos para realmente ter certeza. Reduzimos a velocidade ajudou um pouco, está sem contrapressão, a borra está saindo amarelada, sem bico ou câmera quente.
– Então está mais para parte eletroeletrônica da injetora ou algum ponto de retenção de material no conjunto de injeção.
– Se a leitura de temperatura estiver correta, ou seja, a malha de temperatura estiver ok, seria bom checar a própria rosca, cabeçote, porta bico, bico atrás de algum ponto de retenção.
– Tem algum outro tipo de SAN ou outro lote desse mesmo SAN? Há muitos anos atrás tive problema com um lote de SAN com problemas de estabilidade térmica.
Autor – Eu tenho outro lote, porém não é cristal, vou dar uma atenção nas resistências, são de cerâmica. A injetora aqui é oriente 3000.
– Folga no anel de bloqueio ou rosca.
– Temperatura baixa demais também queima o material.
– Veja a densidade da ficha técnica qual é a temperatura de processamento
– Me deram uma aula. Trabalho com inject blow máquina AOKI. Injetamos pet, e sempre que produzimos frascos na cor Branco temos esse problema de os frascos saírem amarelado.
– Como está a descompressão?
Autor – Não estou usando, o bico está encostado no molde.
– Se já verificou todas as alternativas anteriores e não resolveu, veja se o furo da bucha injetora no molde não está menor do que a saída do bico da máquina.
– Verifique também pressão e velocidade de dosagem também pode estar dosando muito rápido aí o material fica residindo no cilindro aí degrada, tenta conciliar o tempo de dosagem com a abertura da máquina.
– Correto… aliviando um pouco na contra pressão.
– Verificar a relação LD da máquina, e verificar o volume de material.
– Tente mudar de lote da matéria prima! Se persistir a anomalia aí é máquina o molde, verificar todos os termopares se estão fazendo leituras corretas.
– Tenta deixar o mínimo de coxão pode ser por tempo de residência do material na rosca.
– Estufa o material a 60 graus por 3 horas.
– Sangel geralmente amarelo um pouco após passar pelo processo de fusão e quando mais alto o tempo de ciclo mais amarelo ele fica, o tempo de residência do material e muito baixo, espero ter ajudado.
– Verificar material na estufa se não está amarelado.
– Pode material muito tempo de estufa.
– Pode ser muito tempo na estufa …verificar se tá usando algum tipo de aditivo.
– Faz um teste retira todo material já preaquecido e coloca outro …espera uma hora e injeta pra ver… utilize material virgem em embalagens lacrada.
– Material está difícil de atender as recomendações de fluidez mais baixo, mais alto.
– Retira a descompressão de dosagem, com certeza o que está queimando é o ar da descompressão.
– Trabalho com SAN injetando jarra de liquidificador… Pode ser umidade.
Autor – Tentei bastante coisa, todas as sugestões que falaram. A que mais ajudou foi diminuir a velocidade de dosagem para não ter tantos atritos, ainda sim continua um pouco amarelo, mas já mostrei ao cliente e ele aceitou.
– Uma questão. Esse amarelamento é só no fundo ou na peça toda?
Autor – Na peça toda, inclusive na borra.
– Já verificou a resistência do bico? Está queimando na hora de injeção? Ou quando você injeta fora ele já sai amarelado?
– Primeiro tenha certeza de que a rosca está com os parâmetros corretos na taxa de compressão…
– Já tivemos muito problemas com matéria prima, provavelmente é o lote de material. Experimenta testar um outro lote, por mais que seja novo às vezes dá problema.
– Precisa avaliar o tempo de dosagem com o tempo de resfriamento, as vezes o tempo do resfriamento é muito maior do que o de dosagem, deixando o material parado sem movimentação dentro do canhão, ocasionando a queima, também importante trabalhar com o mínimo de colchão possível nesses casos, e a temperatura do bico, não muito alto, pois pode degradar o material na passada. Espero ter ajudado.
– Quer saber o resultado final do processo, não use reciclado.
– Quanto está a temperatura e o tempo de estufagem?
– Se ficar muito tempo no funil na temperatura de 80 graus, amarela no funil …. trabalho com esse material sempre, e o problema de amarelamento é esse.
– Se conseguir diminua o tempo do ciclo; recalque dependendo pressão e velocidade de pressão, isso depende da peça se for lente coloca água quente.
– O tempo de residência no cilindro está muito alto devido ao tempo de ciclo.
– Provavelmente não está bem seco ocorre a queima por hidrólise do material experimente secar bem antes de usar.
– Eu creio que vai ajudar bastante.
– Verificar se o diâmetro de entrada do molde está no mesmo diâmetro do bico da máquina.
– Verifica se o volume do canhão não exceda 3 ciclos se sim diminuir as temperaturas pode ser residência.
– Já verificou o tempo do material no canhão?
– Verifique com seu fornecedor qual o tom do material. O SAN é cristal, mas ele tem tonalidades diferentes. Existe SAN azulado, lilás, cinza, totalmente translúcido e amarelado. Quem sabe este não seria o seu caso.
– Outra questão é seguir o tempo de secagem conforme ficha de processo.
– Problema difícil, acredito que o atrito está aquecendo o material quando está dosando.
– Verifique a descompressão e velocidade de dosagem.
– Não acredito que seja o material …
– Para esse tipo de matéria prima, sempre é bom usar todo o material que está no funil, porque depois que fica parado muito difícil a secagem dele.
– Tem que abaixar esse ciclo.
– Trabalha no tempo de secagem a hidrólise acaba com o processo mesmo que ele esteja 100% calibrado.
– Já passei por isso algumas vezes, e sempre é algo diferente, mas se em último caso não resolver, a solução é uma limpeza de rosca manual e posteriormente um ciclo adequado.
– Secar bem o material e aumentar a contrapressão, diminuir a velocidade de rosca, pois o que está acontecendo é a parte química da estrutura do material que se chama acrilolitrila que está amarelado. Também olhar o tempo de residência do material no cilindro, abaixar a descompressão a aumentar o retardo.
– Tamanho do cilindro também influência…
– Se estiver usando moído precisa peneirar para retirar o pó pq degrada facilmente, e tenta diminuir o colchão ao máximo
– Se for molde de câmara quente é bom verificar os bicos, se tive estrangulando na bucha causa atrito e degrada
– Tempo de residência no canhão, temperatura do molde e refrigeração. Verificar descompressão.
– Antes de abrir a sacaria, se o caso, verificar se não existe sujeira grudado nas embalagens, ou até mesmo se o material esteja contaminado.
Balde / Falha de injeção / Material PP

Problema: Não consegue preencher totalmente a peça, pois ocorre falha de injeção.
Máquina Battenfeld BKT3500/2800 em perfeito estado e condição normal, mas está dosando pouco material. É a primeira vez que está sendo injetado. Já foi aumentado o curso de dosagem. Só um lado que não preenche, a está torcendo no molde.
Comentários / sugestões:
Aumenta a pressão.
– Molde muito frio ou embolou material embaixo do funil.
– Pressão/tempo de injeção.
– Carga baixa.
– Faz um teste de ponteira. Pode ser vários tipos de problema ou processo.
– Se aumentou o curso máximo e está injetando até o final, você pode usar a intrusão (tempo + pressão) se sua máquina tiver esse recurso no caso…
– Observa se o material está voltando pra garganta do canhão, puxa o funil e olha…
– Cheque a saída de gás do molde.
– Qual o material? Aumenta a 2a pressão. Atenção às temperaturas do processo todo (molde, fuso, sistema de injeção).
– Ajusta a contra pressão de dosagem conforme o seu material.
– Injeto um balde parecido e tive muita dificuldade para preencher. Tive que tira um pouco no travamento, só assim consigo tirar peça boa.
– A máquina pode até dosar, mas se tiver baixa a contra pressão irá dosar em “vazio” atingindo o curso final com muita facilidade.
– Diminui a contrapressão para ganhar no tempo de dosagem e aumente a dosagem… aumente a pressão de injeção.
– Faz teste de anel de bloqueio.
Autor – E como testa se é o anel sem tira a rosca primeiro.
– Um indício se é o anel o problema, é a variação na almofada.
– Aumenta a temperatura.
– Contra pressão, mas se ela tiver pelo menos com 70% da peça.
– Várias possibilidades “temperatura do cilindro ou do molde baixa, velocidade de injeção, ou contra pressão, material de baixa qualidade, tempo de injeção, material empastelado no cilindro…….
– Veja, se ele não está torcendo no molde as paredes estão iguais. Não comprou um material de sopro? Quanto tem este material de fluidez?
– É canal, câmara quente ou bico quente? Pode estar obstruído.
– Verifica se não empedrou material no canhão.
– A entrada de material, está livre?
– A válvula na ponta da rosca da injetora pode estar com desgaste é o material está retornando pela folga e não enche a cavidade.
– Essa máquina trabalha ou trabalhou longo período com material abrasivo ou corrosivo?
– Pode ser o anel de bloqueio, ou ponta da rosca gasto.
– Anel de bloqueio gasto ou quebrado. Com certeza.
Aumenta a contrapressão.
– Podem ser várias coisas:
– Se já injetava esta peça e começou o problema, verifique o índice de fluidez do material, se não tiver o equipamento de teste, troque o material para ver antes de sair desmontando o canhão.
– Apostaria no anel de bloqueio.
– Passa aí qual a sua injetora, as dimensões da sua peça o tempo, pressão a velocidade e o curso que você está usando, qual a temperatura do molde, tem anel de bloqueio? Verifica pressão hidráulica da máquina se está havendo variações, verifica descida do material no funil, tamanho grande de reciclado junto ao material virgem ou excesso de pó junto ao material virgem.
– Aumenta o tempo injeção começa por ele.
– Fecha a contra um pouco pressão, caso não resolva verifica também o anel de bloqueio…
Autor – Como verificar o anel?
– Tem que retirar o bico e em seguida o contra bico, depois fazer a retirada do cabeçote pra conferir a rosca e o anel de bloqueio.
– Tempo, velocidade dosagem, pressão, velocidade injeção, temperatura do material, borra no bico, controlador se tiver e vários detalhes podem ser, vai eliminando.
– Já verificou se material não tá embolado na base do funil?
– Já tive muito problema com isso. Pior que é quase sempre a última coisa a checar.
– Aumenta a temperatura e a pressão. Tempo de recalque deve ser maior.
– Se ele disse que a máquina injeta bem, se entende que não é falta de pressão.
– Para tirar sua dúvida com relação a desgaste de risca ou anel bloqueador, faça a seguinte observação:
– No momento da injeção, se a rosca entrar no cilindro de injeção rodando ou torcendo, é problema de desgaste de anel bloqueador ou do conjunto de injeção. Se for desgaste na rosca, o material irá a retornar, não deixando que a próxima dosagem seja completa.
… ou se achar melhor?
Injeta no molde e não extraia a peça. dose e injetar novamente sobre a peça que está dentro do molde. Se a rosca não for para frente injetando, é porque não há desgaste nem no anel bloqueador, nem no cilindro e rosca. Só com isso já vai saber se seu problema é máquina ou material inadequado.
Também tem que verificar a posição de recuo de rosca. Não adianta nada aumentar a dosagem se a posição de recuo de rosca está menor.
– Já injetou essa peça antes?
Autor – Nesta máquina não.
– Se já verificou a possibilidade de o anel de bloqueio estar com problemas (material retornando na boquilha/entrada de matéria prima), pode ser que a ponteira da rosca tenha quebrado…
– Mas isso sem mencionar as coisas mais básicas que suponho que já tenha conferido.
– Pode ser o capilar que está pequeno.
– Tem várias possibilidades, mas a que tem de eliminar primeiro é a fluidez, se injetava normal com esse material legal, mas se não injetava com esse pode procurar outro.
– Verdade … tinha uma lixeira aqui na empresa que só conseguia bom resultado com material de alta fluidez.
– Dá uma olhada na contra pressão ela pode estar muito baixa e a rosca vai pra trás sem material.
– Desliga a descompressão… e liga a dosagem com velocidade média da rosca e no máximo 5 bar na descompressão final com o curso em 2% da dosagem…
– Poderiam ser vários fatos, mas pode ser resistência do bico não aquecendo perfeitamente o bico, ponteira pode estar muito avançada dificultando a passagem do material, material não ser o mais indicado, umidade do material …
– Verifica se a agulha do molde está recuada com o molde parado, pode estar invertida a ligação do ar…
– Anel de bloqueio da rosca da máquina gasta ou quebrado.
Colocou em debate um processo de injeção, mas não deu informações de molde, material, máquina, temperatura de processo deste material. Sem informações ficam ajudar.
– O molde tem refrigeração? Com qual água está trabalhando, ambiente de geladeira ou aquecedor?
– Dar polimento no molde para material fluir melhor.
– Verificar se o anel de bloqueio está gasto! (A rosca da máquina não pode girar no momento da injeção).
– Aqui vou passar algumas fontes que pode ajudar! Fluidez do material, câmara quente do molde, bico injetor com impureza, anel de bloqueio desgastado, caso molde tenha bico valvulado não está movimentando, contrapressão, curso de dosagem descalibrou.
– Qual é peça que está injetando e qual o material que está usando?
– A câmara tem capacidade para a totalidade do material da peça? Pode também o anel de bloqueio não fazer efeito. É puxar a tremonha à frente, dosear e injetar e ir vendo.
– São vários fatores que podem fazer com que não consiga completar a peça…eu não me arriscaria um palpite, é o tipo de situação que eu precisaria estar presente, mas vai tentando o que os colegas estão opinando. Tudo que ler no grupo tem fundamentos.
– A ponteira pode está quebrada.
– Material retornando.
– Nesse caso aí, pode ser até o anel de bloqueio que já era.
– Precisar especificar melhor e dar um contexto. Tem um milhão de possibilidades. A peça funcionava antes? Foi do nada ou após troca? Ouve alteração de máquina? De material? Precisa se entender o conceito para se ter uma ideia, pois cada um aqui vai dizer uma coisa diferente, e você vai se perder.
– A peça é de parede fina?
– Faça o processo de intrusão… utilizado em algumas máquinas para compensar a capacidade de preenchimento. A rosca gira constantemente preenchendo parte da cavidade do molde, passando para a fase de injeção que fará o preenchimento final da peça.
– A ideia é muito boa, já me aconteceu isso e fiz o processo de intrusão.
– Se a máquina dosa pouco, ou seja, não tem capacidade de carga suficiente para encher a peça, você pode tentar usar a função de intrusão, onde você programa o tempo em que a máquina vai ficar carregando e injetando, na prática é mais ou menos como se a injetora virasse uma extrusora. Porém, algumas máquinas não tem a função injeção por intrusão.
– Pode ser anel da ponteira trincado, ou material estranho na rosca que não plastifica na temperatura do material usado.
– Matéria empedrada no início da rosca.
– Veja se o anel de bloqueio e a ponteira da rosca se não está danificado, estava com esse problema e foi isso fiz o anel e ponteira ficou show de bola pode desmontar que vai dar certo.
– Numa boa comece do começo: carga plastificação versus peso da peça, refrigeração do molde, parede fina requer maiores pressões; aparentemente esse é um pp; o molde tem câmara quente? É passível fluidificar mais o material? (Aumentar temperatura); zere recalque, preencha por tempo, acompanhe os valores de material que entram no molde, compare os colchões… muita coisa meu amigo pra verificar! Me preocupa o fato da dificuldade em encontrar caminhos próprios pra encher a peça, precisa estudar mais, ler mais, conhecer a fundo o básico de um processo de injeção.
– Pode ser que plastificou material na zona de alimentação.
– Ou anel de bloqueio trincado.
– Comece pelo básico, aumentando a pressão de injeção e o tempo de comutação, se preciso aumenta a temperatura até um pouco abaixo do limite que o material suporta.
– Pode estar com desgaste no anel na ponta da rosca e quando ela injeta o material retorna.
– O anel de bloqueio pode está danificado e o material retorna para o cilindro plastificador. Verifique se no momento da injeção a rosca faz um pequeno movimento de rotação, se isso acontece é o caso de se verificar urgentemente anel de bloqueio.
– No momento da injeção ou descompressão não há rotação da rosca.
– Anel de retenção da máquina ou desgaste da rosca, se for molde confere se não está vazando pelos bicos, enchendo a câmara quente, se não for nenhuma, saída de gás ajuda também em espessuras finas.
– O bico não está entupido.
– Quanto está a contrapressão.
– Tente preencher a peça 100 % sem o recalque. depois vá ajustando a posição de comutação até a peça falhar uns 5%. Redefina o tempo e as pressões de recalque.
– Qual a capacidade de injeção da máquina? Autor: É um 350ton.
– Tinha uma peça parecida aqui na empresa para piscina. Em uma 380T da Haitian, apanhou para injetar. Não sei o tamanho correto da peça.
– Veja a temperatura da água de resfriamento do molde, e também se á saída de gás no molde, faça shortshots (injeções de menor curso para ver onde está parando de completar o molde). Qual o material?
Balde / Preenchimento
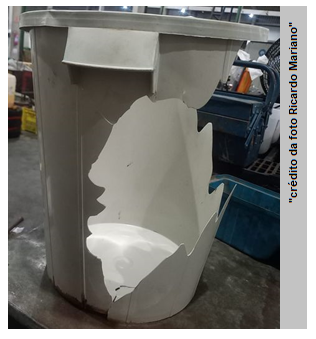
Problema: Preenchimento.
Molde de balde com30 litros. O molde está bem centralizado, mas na injeção apenas um lado fica completo. Alguma dica?
Comentários:
– Bico do canhão deve estar descentralizado?
– Explicado porque esse baldes são tão frágeis.
– Depende muito do reciclado que comprar.
– Tenho que parabenizar todos nós profissionais da área, com a colaboração de tentar ajudar um amigo com esse problema de injeção, isso mesmo esse é o caminho, uma análise do molde, máquina, e matéria prima terá a solução.
– Pessoal muito obrigado pelas sugestões.
– Foi feito direcionador de fluxo e resolveu o problema.
– Diversas causas devem se analisar na máquina.
– É comum quando o molde não tem boa estrutura no macho, acontece do mesmo flambar ao injetar.
– Você corrige facilmente dividindo a refrigeração no macho, deixando sempre mais quente o lado que está ficando fino. O ideal é utilizar ao menos um termo regulador.
– Tem que analisar o anel de bloqueio, pode ser que esteja voltando material. Pela foto falta muito material pra encher.
– Além de tudo que comentaram dá uma olhada na coluna da máquina pode ter alguma quebrada.
– Checar as guias/centralizador do macho.
– É comum esse tipo de molde deslocar o macho durante a injeção deixando uma parede mais fina dificultando o preenchimento.
– Como só tem a foto do produto e não do molde fica difícil opinar, mas aparentemente há uma descentralização do macho em relação à matriz.
– Depois de checar isso deve ser verificado a MP, o processo de injeção, etc.
– É complicado, pode ser regulagem de máquina ou molde Veja se ela está obedecendo os parâmetros, se está injeção contra pressão e etc. Aí tenta partir ela com a água fechada, até talvez encher a cavidade, temperatura do material e etc.
– Molde que normalmente trabalha numa máquina maior que precisa.
– Difícil de analisar com pouca informação, o anel de bloqueio pode ser, mas se tiver mudado de material, pode ser gás, contaminação, carga…. uma experiência que tive parecida foi devido ao fornecedor colocar talco para dar peso. Mudei o material e resolveu. Faz o seguinte, experimente diminuir a rotação do fuso pela metade.
– Nossa…. esse molde está com folga nas colunas de centralização quando entra a injeção ele c desloca… faz um teste calça a parte que está preenchendo…. acredito que vai ter um resultado e conclusão da situação.
– O ideal de um molde deste é 35% de encunhamento. Caso não tenha teria que ter um material com boa fluidez. EX H103 ENTRE 35/40 DE FLUIDEZ.
– Tem que estar bem cunhado, 30% do tamanho do produto.
– Pode ser a fluidez do material, tem que ver se o molde precisa ter canal quente, pode ser que precise aumentar a velocidade de injeção. E por aí vai.
– Verifique as espessuras das paredes devem estar todas com a mesma medida para não ocorrer o fenômeno chamado de “frozen layer”.
– Tem que ver o tempo de injeção, pressão e velocidade de injeção, pode ser que esteja pouco para completar a peça, ou o bico do canhão pode ter algum pedaço de ferro empatando o material de entrar com fluidez dentro do molde.
– Bom, a princípio não está centralizado, o que pode tirar o molde de centro é a máquina estar abrindo aí, o cone não segura. Começa injetando com uma pressão bem baixa para ver se está centralizado, aí já elimina se é a máquina ou o molde.
– Como já citaram, importante verificar como é feita a centralização entre macho e fêmea do molde, deve garantir de forma robusta para manter em posição durante a injeção.
– Refrigeração bem balanceada e eficiente.
– Quanto a máquina, realmente se não estiver com o sistema de fechamento em bom estado pode ocorrer esse problema, mesmo com molde bem centralizado.
– Para testar de a máquina está boa mesmo.
– Faça o teste fazendo uma rotação de 180⁰ (a parte de cima do molde virar para baixo).
– Se a peça encher na mesma posição de antes é o molde, se ficar na mesma posição que antes a máquina está com problema no paralelismo de placas ou o estiramento de colunas não balanceado.
– Qual é o material e qual a refrigeração do molde.
– O macho está cedendo, para preencher isso aí tem que ser um tiro.
– Molde sem estrutura, talvez encunhando você vai ter um resultado perfeito.
– Se possível aumentar fluidez material, ou fazer direcionador fluxo molde caso não tenha.
– Primeiro passo analisar o sistema de resfriamento esse lado pode estar mais gelado.
– Tem que conferir se o macho ñ está se movimentando na hora da injeção.
– Pode dar uma olhada nas saídas de gás vê se não está um pouco surja.
– Parede muito fina.
– Se o molde tem parede fina, fica difícil de completar a injeção.
– Veja se a carga de material enviada para dentro do molde e o suficiente.
– Da uma olhada se a carga da sua máquina está calibrada.
– Analise as réguas do molde se tem necessidade de colocar calço neles, vê se também a parede está deslocada se não vê o recalque da máquina com a pressão de injeção BAR, com certeza vai preencher.
– Abre um pouco mais o canal de injeção pra ver.
– O que não falaram ainda tira travamento até dar rebarba espessa na borda se a peça completar e claro, se sim, pronto, aumenta a temperatura e trabalhe na saída de gás. Mas quase todas as dicas acima de aplicam a esse problema.
– Falta de material para preencher o molde, ou abertura do molde antes do tempo.
– Se o molde não estiver resfriando rápido demais o material. Pode ser as saídas de gases. Impedindo o fluxo do material.
– Tinha que tirar foto do molde junto… dizer o tipo de matéria prima, se tem câmara quente no molde, se tem aquecedor, se tivesse essas informações ficaria mais fácil pra dar uma resposta mais concreta….
– Realmente está falhando bastante aí, tem uma grande probabilidade de ser pouca carga, ou seja, canhão pequeno ou coluna quebrada também sai rebarba onde falha parede fina muita pressão máquina pequena na verdade vários fatores muitos
– Pode estar centralizado certo, mas e nivelado está?
– Aparência de injetora /molde desnivelado.
– Passa uma foto do molde aberto; este molde tem quanto de encunhamento?
– Em parede fina isso acontecia muito, centralizar bem o molde na hora que vai colocar em máquina, refrigeração do macho com água natural e não gelada, de repente dá certo.
– Pode ser o molde descentralizado ou a tonelagem da máquina.
– O molde deve estar mexendo.
– A analise a saída de gás.
– Verificar a refrigeração do molde.
– Impossível estar no centro, corta os lados e faz a medição no parquímetro… se fosse fluidez de material um lado não enchia.
– Tenta dar mais Fluidez ao material, temperatura… Enfim, ou já aconteceu por conta de material ruim.
– Olá quantos bicos de injeção?
– Pode ser pressão de injeção e temperatura também.
– Já tentou usar o direcionar de fluxo para esta região da peça?
– Tem aquelas estrias no fundo para ajudar a direcionar o fluxo?
– O molde é de câmara quente, sequenciador?
– Macho pode estar frouxo e causando variação de parede, fluidez baixa, molde gelado demais.
– A princípio tente aumentar a velocidade de preenchimento, um balde desse comprimento e parede delgada tem que encher rápido, verifique a refrigeração, se um lado do molde está mais frio do que o outro lado, com certeza esse material é PP com carga mineral (Carbonato de cálcio) dependendo do porcentual reduz muito a fluidez do material, aparentemente é falta de velocidade de injeção.
– Corte o fundo e verifique se não está estrangulando a passagem de material desse lado, tanto o fundo quanto o detalhe que contorna o fundo. Já tive problema semelhante e era isso.
– Material recuperado muito ruim, só por ver a peça.
– Este tipo de matriz sempre se inicia com a carga baixa.
– Diferença de parede, mede as paredes do molde e balanceia para deixar todas iguais.
– Provavelmente o que ocorre é que apesar de estar bem centralizado, durante a injeção, o macho se desloca para uma das laterais, devido alta pressão do polímero, isso é até comum em moldes assim, o ideal é tentar injetar com menos pressão, mais velocidade, e tentar aumentar a fluidez do material através da temperatura do cilindro, contrapressão ou até mesmo algum aditivo.
– Ao injetar deve estar saindo do centro. Confere pinos guia se estão bem fixos para não deslocar com pressão.
– Isso já aconteceu comigo com molde de bacia, a placa onde estava preso o macho até tinha bastante parafuso, mas a placa era muito fina não era adequada, o macho deslocava. A estrutura do molde era muito frágil.
– Tenta cortar o fundo e verificar deverá estar com alguma restrição de passagem do material.
Balde / Marcas tipo linha
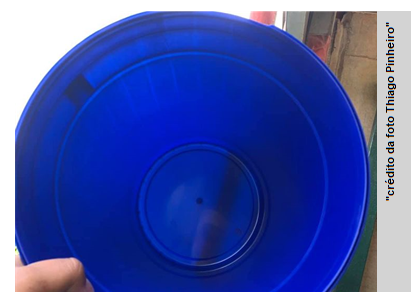
Problema: marcas tipo linha.
Balde de 20 litros com marcas de linha. A máquina não tem muito recurso, é uma Romi Prática 450.
Comentários:
– Pode estar usando uma matéria prima bem transparente.
– Outro passo é diminuir a velocidade de dosagem, para desta forma o material misturar melhor.
– Aumenta a quantidade de Master, mas antes verifica se o Master é dedicado para o polímero em questão.
– Falta master mínimo 2%.
– E outra, se tiver as mangueiras suada bate um ar para tirar o suado das mangueiras, aí, vai ver, depois a diferença se bate umas duas vezes ou se tiver o dia todo assim
– Trabalha sempre com água fechada.
– Pode ser defeito no pigmento, ou troca, ou faz teste com outro master. Pode estar velho o pigmento.
– Depende também da resina que se usa.
– Aumenta um pouco a temperatura e o tempo de injeção.
– É pode ser temperatura ou tempo mesmo.
– Aumenta a pressão de injeção e o tempo.
– Faça o seguinte, coloca um pouco de contra pressão e usa o recalque 1 baixo e ainda posição um pouco maior. Pode ser que resolva.
– Aumentar tempo de dosagem e colchão, e trabalha com master ver a porcentagem.
– Talvez esteja vazando água do molde pelo bico de injeção do molde.
– Pode ser saída de gases insuficiente…
– Homogeneizador estático.
– Aumenta a dosagem do Master vai ficar bom.
– Ajustar processo, pode ser temperatura ou pressão de injeção.
– Se a estrutura da PC está boa concordo que pode ser o master.
– Qual a porcentagem que está usando.
– É isso mesmo… falta master… E a causa, mais provável para esse tipo de bronca.
– Faz tempo que trabalhei com balde, mas está parecendo que o balde está claro, com falta de master.
Manchas em todo corpo da peça
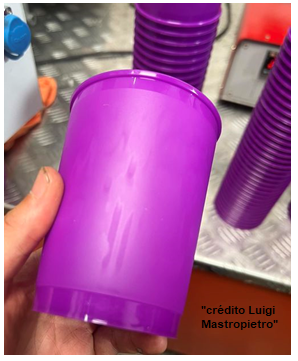
Autor – Como tirar essas manchas, já subi e desci temperatura, tirei e coloquei recalque e nada…
Comentários:
Limpa o molde pode ser alguma mancha.
Talvez possa ser o master utilizado, qualquer coisa posso ajudá-lo.
Pode ser água muito gelada ou mancha na cavidade.
Verificar se a matéria prima está com umidade ou molde vazando água.
Material contaminado.
Sujeira no torpedo tem que limpar e polir.
Aparentemente parece ser diferença de temperatura na parede do molde.
Onde está localizado o canal de injeção. É no fundo. Caso for abra o fechamento um pouco e limpe as saídas de ar. Se for canal submarino lateral aí tem que aumentar as saídas de ar e diminuir velocidade de injeção. Aumentar a temperatura do molde. E aumentar um pouco a contrapressão
Contrapressão ou segunda injeção, já tentou?
Aconselharia o molde a 20 ºC também.
Diminua a velocidade da plastificação.
Temperatura da água está muito baixa ou molde está vazando água na cavidade
Parece molde muito quente.
Umidade ou vazamento de água, para ver se não é gás tenta tirar um pouco da altura do molde.
Está usando molde com água gelada?
Isso ocorre por o molde haver textura, água gelada tem que deixar um pouco mais fechado.
Mancha de água tem que diminuir pressão da água, deixar só metade do registro aberto.
Material de baixa fluidez e úmido que está injetando, pigmentou?
Parece umidade no material, tenta estudar o material…
Ondulação na parte fêmea, utiliza abertura inicial uns 30mm bem lento e aciona o pneumático da parte fixa em 0,1 mm retira o recalque e injete bem rápido por posição e aumenta as temperaturas do cilindro entre 3°C a 5°C utilize água quente ou normal na parte fixa e água gelada na parte móvel, utilize o menor curso de abertura possível e velocidades de abertura e fechamento bem rápidas com exceção da (1° posição de abertura).
O molde deve ter ondulação em ambas as partes já passei por isto.
Contrapressão para misturar o material.
Diminuir os rpm de carregar o fuso. Aumente os bicos e faça testes de aumentar muito pressões e diminuir a ver diferenças.
Pode ser má homogeneização no master que está utilizando.
Material que está usando pode estar úmido.
Pelo jeito é polipropileno que tá injetando, esse material extremamente resistente absorção de umidade, a não ser que choveu encima, está molhado, ele pode estar usando material contaminado ou com PS ou ABS, por isso dá essas manchas aí no frasco.
Qual é a matéria prima?
pp certamente
Utilizando reciclado, pode ser gás.
Por se tratar de molde com textura e espessura de parede grossa acredito que esteja fazendo o uso de água gelada.
Autor – Utilizando água gelada.
Autor – Molde está transpirando um pouco.
Verdade!
Está parecendo vazamento de água ou mancha na cavidade.
É marca d’água, acho que é molde condensando.
Autor – Problema quase que resolvido.
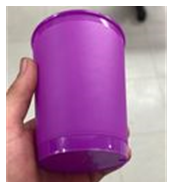
Autor – Aumentei a temperatura do material e diminui pressão e velocidade.
Autor – Teriam mais opiniões.
Se for condensação ou diminui o fluxo da água gelada para não suar na cavidade ou diminui o ciclo para não acontecer esse problema.
Verifique se está condensado (caso esteja usando água gelada), também verifique se tem alguma mancha no molde.
Isso pode ser água que fica condensada no molde, poder dar um jato de para tirar a condenação do mandril ou diminuir a pressão da água.
Manchas também pode melhorar com fluxo de injeção baixa.

Autor – Problema resolvido.
Solução – Autor: Abaixei a velocidade e pressão de injeção, aumentei a temperatura para melhorar a fluidez.
Esperamos ter colaborado com os profissionais!
Fonte: Grupos Técnico em Plásticos e Injeção Plástica
Resumo e edição: Moldes Injeção Plásticos Atualizado 13/01/25
Acesse: isso também irá facilitar o trabalho do profissional:
TABELAS COM VALORES PARA APLICAÇÕES DE TERMOPLÁSTICOS
INDICAÇÕES PARA O PROCESSAMENTO DE DIFERENTES MATERIAIS PLÁSTICOS – 01
INDICAÇÕES PARA O PROCESSAMENTO DE DIFERENTES MATERIAIS PLÁSTICOS – 02