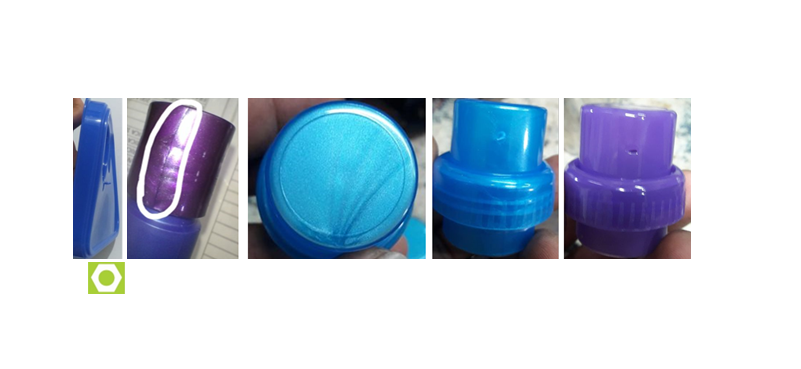
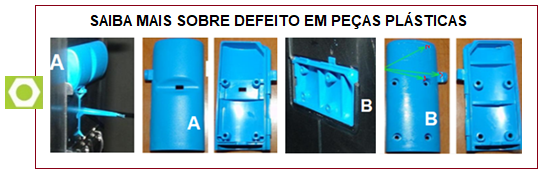
Problemas de injeção em tampas plásticas
Este conteúdo abrange problemas diversos que ocorrem no dia à dia, durante a injeção de tampas plásticas. São resumos de casos apresentados e que receberam comentários e sugestões de profissionais. A ideia é levar a informação na palma da mão, para um melhor direcionamento no momento da necessidade. Se lhe interessa saber mais sobre molde de injeção, manutenção em molde e sobre defeito em peças plásticas indicamos nossos Estudos livres e Cheklist Auxiliar. http://moldesinjecaoplasticos.com.br/loja/
Tampa de cosmético / Linha de junção / Material PP perolizado
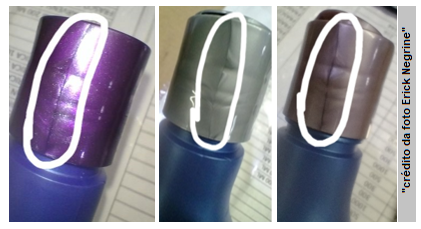
Problema: peça saindo com essa marca de fluxo alguém. Matéria PP pigmento procolor ( já mudamos de fornecedor de pigmento, mas o problema continua ).
Comentários:
– A única maneira que encontrei de sanar esse problema quando trabalhava com esse material vai acarretar o aumento do tempo de ciclo, pois vai ter que aumentar a temperatura do molde e a velocidade de injeção. E para não deixar com marca dos extratores pela compactação aumentar o tempo de resfriamento.
– Se chama linha de solda , isso consegue alterar se mudar o ponto de injeção.
-Isso é comum nos pigmentos perolizado, apresentam na linha de junção.
– Esse problema no perolizado ocorre mesmo, estamos injetando as tampas para natura, e ocorre isso também no master perolado.
– Essa marca só sai se modificar o ponto de injeção para o centro das tampas. Nesse caso a ferramenta já está pronta e uma sugestão é estrusar o material já com o pigmento para que fique com as cores mais definidas sem manchas.
– Se chama de solda fria, ela sai desse jeito mesmo aí. Para melhorar somente na construção do molde com 2 bicos de injeção, saída alternativas de encontro.
– Acho que vc consegue diminuir este tipo de problema mudando o canal de injeção do molde. Na foto parece que é a união do material, se de repente tiver a possibilidade de mudar vai melhorar.
– Pigmentos perolados geram marcas de fluxo, neste caso pode ser a solda fria também como disseram, aumentado a velocidade/pressão de injeção pode melhorar….
– Esse tipo de pimento perolado costuma dar manchas, o que eu consegui fazer para melhorar são: velocidade de injeção mais alta, temperatura da bucha alta, e aumentar temperatura da resina.
– Acrescentaria melhorar a saida de gás. Com molde feito é o que tem para fazer…..
– Melhor a fazer é tirar o bico do canhão e fazer uma boa limpeza
– Ajuda muito verificar saídas de gás, e na hora de injetar, mudar parâmetros de velocidade de injeção.
– Retirar ela totalmente não vai conseguir devido ser uma caracterização de todo pigmento metálico e perolado. Tenho bastante desta situação aqui onde trabalho, tenta aumenta mais a contra pressão e um pouco a temperatura da massa para amenizar.
– Isso é típico de pigmentos perolados/metalizados. No projeto do molde isso deveria ser previsto, pois a única forma de melhorar é modificando o ponto de injeção, deslocando a linha de solda fria para um lugar da peça onde fique mais escondido.
– Trata se de uma característica dos pigmentos perolados e alumínio. Pede para o fornecedor trocar o alumínio na fórmula, utilizar outro grade em específico.
– Injeto essa tampa em várias cores perolado e sai com essas manchas na junção. Já as cores não peroladas saem normal.
– No perolado não tem jeito em determinadas cores aparece mais.
– Com certeza não vai resolver esse problema só por mudar o ponto de injeção, isso também pode ser falta de uma boa regulagem, ao mesmo tempo essa peça tem as paredes muito fina.
– Linha de união de material não dá para tirar 100%, única forma de melhoria seria modificando o ponto de injeção para um ponto mais escondido.
– Também injetados pérolados e também ficam com essa marca.
– Isso acontece nesse tipo de pigmentos.
– Pelo que tenho de experiência está mancha é do próprio pigmento e as temperaturas dos bicos baixe um pouco elas.
– Material perolizado é complicado, mas ainda tenho a convicção de que saídas de gases em dois pontos de injeção resolva. Outra alternativa é chamar o fornecedor de master para analisar e tentar melhorar o pigmento. Pode se degradação.
– Pode até mudar o ponto de injeção porém as marcas de fluxo vão continuar isso devido ao pérola.
Tampa de vasilhame / Marca de Fluxo / perolizado
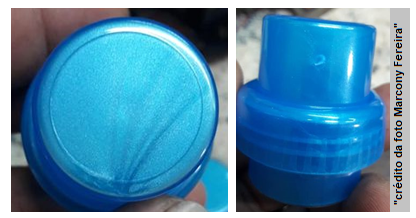
Problema: marcas de fluxo
Comentários:
-É saída de gás.
– Discordo. Os corantes com pérola são assim mesmo, já para não falar que fugas não há de faltar devido ao colapsível que faz a rosca, dissipa muitos gases. Aquilo é devido ao fluxo do material durante o enchimento da peça.
– Isso é normal é do master perola.
– Essa marca de fluxo é normal em masters perolados. Poderá amenizar, mas sempre vai sair essas marcas de fluxo no seu produto.
Autor – É porque o pigmento é perolado?
– Sim, com pigmentos ou master perolados é normal sair essas marcas de fluxo, principalmente em cores prata e dourado.
– Fizemos testes com vários tipos de pigmento e master e as marcas de fluxo continuaram.
– Master perolizado é muito comum acontecer isso, consegue amenizar, trabalhando com a temperatura um pouco mais baixa, e aumentando a contra pressão, trabalhando com baixa velocidade de injeção.
– Tenta bico misturador, mas com esses corantes é quase impossível ficar 100%.
– Essa mancha na lateral parece que o fluxo gerou uma “bolsa” de gás “preso”.
– Tente ajustar um perfil de velocidade de injeção diferente e, se necessário mude as temperaturas das cavidades, aquecendo.
– Pode ser também que as saídas de gases (se existirem) estejam obstruídas por resíduos de moldagem ou lubrificante ou ainda material.
– Baixe a temperatura do canhão só um pouco e diminuir a velocidade de carga.
– Aumente a conta pressão, baixe a temperatura do canhão e diminua a velocidade de injeção.
– Acredito que deva diminuir a mancha, mas por ser material perolizado, eliminar totalmente é bem complicado.
– Se fizer algumas saídas de gás, também pode melhoras bastante.
– Já sofri muito… Ameniza, mas saia… Cliente sabia e abriu um padrão generoso e honesto bom para as duas partes.
– Para amenizar esse tipo de manchas teria que mandar fazer o master, com a mesma matéria prima, ou seja, tira um saco de material e manda fazer o pigmento com o mesmo material.
– Faça saída de gás no molde diminui a temperatura do canhão.
– Normal no perolado.
– Esse tipo de marca de fluxo já é característico de matérias perolados e metalizado, geralmente para evitar que esse tipo de problema seja tão aparente o pessoal acaba projetando o ponto de injeção em partes estratégicas, como na parte interna da tampa, mas uma dicam para tentar amenizar esse problema, pode estar diminuindo a temperatura do canhão, aumentando temperatura do molde, uma granulometria definida, aumentar a contrapressão, irá melhorar um pouco a estética dessa marca de fluxo.
Tampa de vasilhame / Junção de fluxo / Perolizado
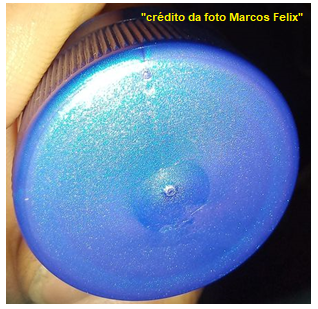
Problema: marca de fluxo
Injetando um produto no tom azul metalizado e sempre está ficando esse caminho do material. Com outras tonalidades sem ser metálico não aparece.
Comentários:
– Realmente nessas cores não há o que fazer, sempre irá apresentar esse risco. Quer seja produzido na injetora ou no sopro, não há ajuste de temperatura que dê certo. A única opção é sempre limpar o molde várias vezes durante a produção para amenizar.
– Isso é característica do master perolizado. Pode mudar alguns parâmetros, mas não vai eliminar totalmente. Consegue melhorar o visual da peça.
– Me parece falta temperatura do material ou matriz muito gelada.
– Normal dessa cor, na cor prata é a mesma.
– Inerente ao pigmento perolizado, como dito por grande parte do grupo, eliminar 100% um pouco difícil, talvez melhore com o escalonamento das velocidades de injeção, ou até mesmo um bolsão caso seja possível confeccionar na região.
– Sempre em cores metalizada fica essa linha, tem que trabalhar na contra pressão.
– Este tipo de material gera mais gases, aí a necessidade de correção aumento das saídas de gás nesta região.
– Concordo, já trabalhei muito com perolizado e só saída de gás e ajuste do ponto injeção corrigiu.
– Sempre que apresentar o problema, chamar o ferramenteiro pra limpar as saídas de gases. Mantendo o ciclo de confirmação não tentando aumentar o ciclo do molde.
– O que tem ali é uma ponta fria do teu bico, se tem câmara quente no molde, vai ter que aumentar temperatura, se não tiver, vai ter que revisar o ponto é injeção. Deve estar danificado ou teu tempo de ciclo está muito alto.
pode ser que a temperatura muito alta que deixar esse ponto, porque se aumentar o material corre o risco de evadir o molde.
– Contra pressão vai fazer babar também, utiliza a descompressão. Toda vez que o molde abre fica a ponta fria no ponto de injeção.
– Nas outras cores não tem isso pois não ocorre a marca do fluxo devido a essa ponta fria.
– Tem que ver se não está babando, após o molde abrir. Se for, diminuir contrapressão e aumentar descompressão deve resolver.
– Caso contrário revisar os pontos de injeção e torpedos da câmara quente.
– Creio que o colega está falando da linha de soldagem.
– Neste caso não, olhando atentamente verás o ponto frio arrastado e solidificado bem na curva. Causando esta linha se parece muito com uma linha de solda fria.
– Tente aumentar a temperatura do molde, do material, diminuir o tempo de resfriamento, dar mais recalque…e fazer uma saída de gás bem ampla naquela região.
– É normal dar está marca onde acontece o encontro de massa, pois o metal é mais pesado e o plástico flui na frente causando um encontro de materiais sem metalizar, então precisa calibrar a espessura da peça para que não aconteça o encontro de material na parte do visual.
– Isto está aparecendo também vazamento de material no bico.
– Importante verificar a temperatura, tempo de dosagem.
– Nunca irá tirar essa marca de fluxo em máster perolados.
– Características comuns em cores perolizadas.
– Isso aí é complicado. Pode ver em produtos com valor agregado como shampoos e desodorantes onde as tampas são assim. Sugiro tentar aumentar o tempo de recalque. Agora se quiser ir fundo, vai encontrar aditivos que melhoram.
– Está peça técnica não está bem compactada, pode ser o seu canal de injeção.
– Faz saída de gases neste local.
– Abre ramificações nas extremidades para dissipar o gás concentrado, outra dica seria tirar um pouco de travamento.
– Fazer uma pequena saída de gás.
– Esta emenda faz por falta de saída de gás, melhora a saída de gás para o material fluir melhor.
– Mude o ponto de injeção e tipo de entrada.
– Podem ser várias coisas: agulha muito quente (isso é sistema valvulado no gate certo?). Velocidade injeção muito alta…para ver se resolve, pode também colocar umas etiquetas a simular fugas de gases para ter a certeza de se não é falta de fugas de gases…
– Ampliei a foto e parece mesmo que é um pedaço do ponto de injeção que ficou preso no ciclo anterior.
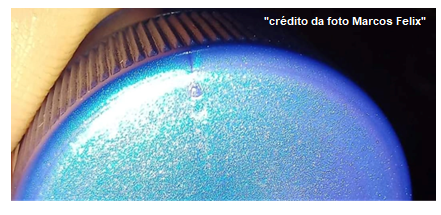
– Primeiro faça alguns testes, injetando peças falhadas para sabe se é gás preso ou então o ponto de injeção que está ficando “preso” no molde e quando injeta o ciclo seguinte esse material frio sai e faz uma “emenda” e essa marca de fluxo.
– Pode ser ainda uma condensação na cavidade.
– Depois de definir a causa, fica mais fácil solucionar.
– Aumenta a velocidade de injeção e um pouco mais a temperatura.
– Fazer alguma saída de ar na matriz resolve, ou limpar se tiver.
– Tenta escalonar o tempo de recalque em 2 fase,7 a 8 segundos dependendo do tamanho da peça e se possível aumente o resfriamento, recuo do bico da super certo só toma cuidado com a resistência para não ficar com material agarrado.
– Isso não vai sair, é difícil por causa do pigmento.
– Tendo em conta que o ataque é centrado e projeção circular, o molde tem desiquilíbrio (cavidade ou canal quente do molde), não significa que esse defeito não apareça na extremidade da peça, mas um poço frio, fuga de gases ou parâmetros de injeção não possam corrigir.
– Sugestão: Material perolizado de cor escura deve ser feito perfil de injeção parecido com o que é utilizado em PVC Rígido.
– A velocidade no ponto de injeção deve ser bem lenta para eliminar a marca de turbulência da entrada do material na cavidade.
– Se tiver pré injeção. Ajuda a eliminar os gases.
– Faça saída de gás que já ajuda.
– Aumenta a temperatura do bico.
– Temperatura da massa e trabalho mecânico no material, contra pressão e velocidade de dosagem.
– Trabalha no fluxo da injeção e pressão que vai dar uma melhorada, senão e só projeto mesmo do molde que tem que alterar.
– Põe uma fuga de gás nessa zona no plano de junta, resolve na hora.
– A única alternativa é esconder a marca empurrando para um lugar mais escondido, quando se faz o molde.
– O pigmento tem cargas demais, e segue o fluxo de material, acho quase impossível resolver isso sem um recurso de mestres da injeção tipo aquecimento da cavidade por indução. A melhor forma é melhorar a velocidade de injeção e tentar esconder a linha de fluxo na área de recartilhado da tampa, isso se o ponto de injeção permitir. Melhora, mas não some totalmente.
– O único jeito é esconder.
– O pigmento metalizado tem densidade e comportamento diferente do polímero e por isso jamais seguirá espalhando.
– Material metálico não tem jeito sempre saí uma linha é muito difícil de tirar.
– É característico deste pigmento, nada mais é do que o rastro do material e, neste ponto de junção houve maior concentração do perolizado trazido pelas duas frentes de material.
– Temperatura do molde, tenta subir ela, cuida a descompressão.
– Mais temperatura, verifica ponto de injeção e contra pressão.
– Em peças metalizadas sempre aparece essa emenda e norma.
– É molde câmara quente?
– Ou o bico está muito quente ou a descompressão tá pouca.
– Esse pigmento aí sempre sai com essa marca difícil de tirar.
– Escalonar a velocidade de injeção, aumentar a contra pressão.
– Todo master perolizado deixa essa marca não é possível tirar, pontos de injeção, linha de junção, até furos no perfil da peça vai ficar assim, pode até melhorar mudando pontos de injeção, mas não vai eliminar.
– Uma suspeita que pode ser gás, veja duas alternativas, tirando um pouco de travamento da máquina, ou fazendo uma saída de gás neste ponto.
– Pode mexer em vários parâmetros, mas isso é característico de masters perolizado.
– Como se trata só nesse pigmento, altera a temperatura dos bicos, baixa um pouco.
– Está sem saída de gás nesta linha, mexer na velocidade da injeção.
– Tenta mudar a velocidade de injeção para mais ou para menos.
– Tenta várias alternativas, baixa a temperatura do bico e aumenta a descompressão ou bico a recuar.
Tampa Flip Top / Quebrando no teste / Material PP
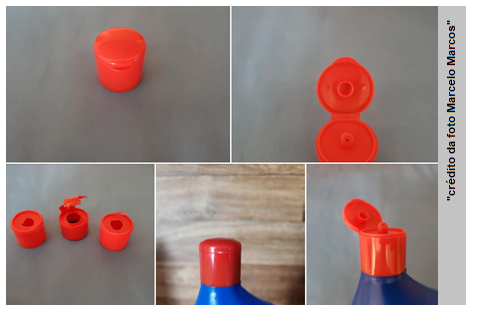
Problema: falta de resistência – quebrando em teste de queda.
Injetando tampa flip top, utilizando o RT400NAQ Randon e 1.5% de pigmento. Durante o teste de resistência na qual o produto é jogado de cabeça para baixo de uma altura de 70cm a tampa acaba quebrando. No mercado encontrei tampas que suportam até 1 metro de queda na qual a tampa absorve o impacto. Como melhorar a resistência deste produto?
Comentários:
– Uso PVB fica muito bom!!
Autor – Utiliza quantos % na aplicação?
– 5%
– Conhece o PVB? Autor – Ainda não, vou entrar contato com meu fornecedor de matéria prima pra me informar sobre esse material
– Esse material é difícil de se achar, se quiser te arrumo 1kg para teste, tenho certeza que vai gostar, vai poder jogar o frasco de uns 5 metros de altura.
– O PVB é uma resina usada geralmente para as aplicações que requerem uma adesão forte, que tenha claridade óptica e flexibilidade. A aplicação principal é na produção de vidros laminados, como os do para brisas.
– Já pensou em fazer blenda nessa aplicação? Talvez outra resina com propriedades de resistência ao impacto.
– Adiciona 5% PEBD e aumenta a contra pressão da dosagem pra homogeneizar.
– PP Randon é matéria homopolímero e suas cadeias são unificadas, se for submetido a este teste ele irá quebrar mesmo, adicionaria 10 a 20% de PP copolímero que irá melhorar.
– Essa tampa já sai com esse furo inclinado do molde?
– Trabalho com o mesmo material para fabricar mamadeira e fazemos os mesmos testes de jogar a peça no chão, porém ela não quebra. Verifica a temperatura se está certa e o pigmento.
– Tenta resina brasken191…pp copo.
– Vai precisar estudar a resistência da resina que vai querer usar, a resina 191 que foi citado pode até ser uma opção, mas somente ela, sozinha não vai resolver. Vai precisar formular ela com um outro material pra deixar mais “mole” como por exemplo usar um IF que geralmente é usado pra fabricar tampas de potes.
– Usar material Randon para cores fechadas acho desnecessário.
– Cuide com saídas de ar do molde.
– Trabalhe com a temperatura do molde. Resfriamento muito rápido pode aumentar a tensão residual da peça. (Choque térmico entre fundido Vs. superfície do molde).
– O ideal na pigmentação seria 2% e ver a temperatura do molde, a contratação do seu material e a pressão e o tempo de recalque.
– A velocidade de injeção pode estar causando uma taxa de cisalhamento acima do que indica o fornecedor da matéria-prima? A análise de Moldflow pode te dizer isso. Isso serve pra qualquer matéria-prima que esteja usando.
– Faz uma blenda com PEBD, pois é um material amorfo, isso aumenta a resistência ao impacto pois as cadeias poliméricas são ramificadas.
– Se for possível e tiver acesso, tente colocar pp copolímero. Começa com 10% na mistura. Ajuda muito e o custo quase não muda.
– Só pode ser a matéria prima.
– Já tive este mesmo problema. E foram feitos testes com várias matérias primas e misturas. O problema só foi resolvido na ferramentaria. Foi feito uma pequena calota no pé do bico do esguicho.
– Como seria essa calota?
– Cuidado com o tensionamento, excesso de recalque.
– Precisa verificar se o veículo do pigmento é em Pp, se por ventura for em PE pode ser isso que provoca a quebra da mesma, apesar da porcentagem do pigmento ser baixo pode ser isso que está ocorrendo.
– Tanto pode ser seu material, quanto o seu processo.
– Se for o material, deve estar sendo respeitada a contração dele, pois dependendo de como injetado se aplica logo ao produto final, ele contrai já no frasco e pode fazer fissura, originando a trinca. Se adicionar uma proporção de um material com strach, melhora muito seu problema.
– Pode ser também a espessura da tampa. Quanto mais grossa mais quebradiço.
– Coloca EPDM borracha termoplástica para PP modificador de impacto.
– Tampa Flip Top de encaixe, você vai conseguir uma performance excelente com o PP RP340R Randômico da Braskem.
– O RP340R possuí uma resistência mecânica melhor em relação a RT400, e não irá causar grandes alterações no seu processo devido ambas as resinas serem de alta fluidez. Tenho certeza que irá resolver o problema.PP RP 340R, o melhor para este tipo de produto. Verificar qual a resina base do master.sa cp141 + master.Pede pra retirar o CaCo3 do M.B.
– PP RP 340R, o melhor para este tipo de produto. Verificar qual a resina base do master.
– Usa cp141 + master.
– Pede pra retirar o CaCo3 do M.B.
– A carga mineral carbonato de cálcio que vai no masterbacth para redução de custo deixa o material quebradiço.
– O problema será resolvido com PP COPO, pode usar um de MI 7, que certamente terá a resistência ao impacto que precisa.
– Usa aí CP 141 com ft 120 aí a resistência vai melhora melhorar muito.
– Aditivo e o master adequados.
– Use cp241 e h301 50% de cada.
– Material… tem que ser o CP 241.
– Cabe uma análise de falha nesse problema.
– A resina que está sendo utilizada é destinada para parede fina. Não sendo na teoria, destinada para tampas flip top.
– Tente utilizar grade H 503 ou H301 que são destinadas para confecção disse tipo de tampa.
– O PP tem uma estrutura helicoidal que permite essa abertura e fechamento sendo excelente a resistência à fadiga por flexão, sendo o caso desses dois grade.
1: O CaCO3 não irá atrapalhar no processo e nem comprometer a sua peça.
2: Sobre utilizar grade de PP copo, também não vejo à necessidade de utilizar, mas tudo cabe uma análise do produto final, equipamentos e processo.
– Também verifique a resina matriz do masterbatch. A resina não pode ser em polietileno, mesmo em baixa aplicação pode comprometer a resistência mecânica ou stress por fadiga.
– Coloque 5% de modificador de impacto DURASUD 9330. Testa com RP 340 que tem maior resistência ao impacto.
– Dá uma olhada também na saída de gases do molde, mande uma foto da peça quebrada pra ter uma ideia melhor.
– Usa o RT100.
– Qual o diâmetro deste gate de entrada, está em 0,6.
– Troque a resina por PP Copolímero dê preferência com pouca fluidez. Pode ser 10 para baixo, sugiro o EP440L ou CP 442xp da BRASKEM. Caso não encontre PP nacional utilize importado desde que também seja copolímero.
Tampa / Furo na peça / Material PP
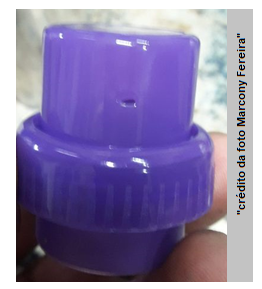
Problema: peça saindo com furo. Material PP H-103
Comentários:
– Se próximo do furo, está brilhante, possivelmente seja água. Pequeno vazamento ou ainda proveniente de condensação no molde. É muito comum quando refrigerado com água gelada.
– Manda recalque aí sem dó.
Autor – Por tempo ou pressão?
– Qual material? Autor – PP H-103.
– Melhora a saída de gás.
– Característico de espessura mais fina na região e ou saída para gases. Coloca uma pastilha de porceráx neste local se a espessura estiver correta. Faça um diretor de fluxo para que material possa chegar nesta região o quanto antes.
– Acredito que todas as tentativas em temos de regulagem de injeção já foi feito neste molde, não dá para avaliar sem ter mais fotos de como é o produto realmente, mas vou dar minha opinião em cima desta imagem. Vê a possibilidade de aumentar a espessura da peça nessa região (alterar o produto) para que o material chegue com mais velocidade e pressão.
– Canal de injeção submarino na lateral, isto que acontece. Abre um pouco o molde e limpa as saídas de gases que devem estar obstruídas.
– Se resolver retorna pra gente pra saber resultado.
– Já aconteceu comigo, no meu caso cavidade furou e entrava água.
– Limpar as saídas de gases e recalque observa se o colchão está muito pequeno.
– Use aditivo agente de fluidez axel.
– Corta ela e veja se as paredes estão iguais.
– Se for câmara quente limpar o bico quente do molde.
– Corta essa peça e verificar se a parede está fina, se tiver o macho está deslocado
– Sempre acontece esse problema com a mesma cavidade?
– O molde dessa tampa que está mostrando parece ser screw off, e devido a esse movimento de desenrosco da peça acaba gerando pó do material (PP) e esse pó acaba se alojando nas saídas de gás das placas do molde e obstruindo as mesmas, então o gás não tem por onde sair e acaba ocorrendo esse tipo de problema. Outra coisa que pode ser é se o molde estiver condensando e durante a movimentação do molde acaba pingando água na cavidade e gerando esse problema.
– Lembrando também o que pode enganar muito na hora da análise, é o caso de a cavidade ter uma pequena trinca, aí quando entra a força de fechamento, vaza uma gotinha de água e acaba trazendo esse transtorno, então se o problema estiver localizado em uma cavidade só, talvez pode estar acontecendo isso.
– Junta tudo aí tenta resolver o problema.
– Verificar saída de gás e o que for. Dar uma aliviada na altura de molde não é correto, mas é uma saída.
– Verifique a temperatura do molde e talvez aumentar um pouco a contra pressão, e a temperatura na área de homogeneização para ajudar na fluidez do material, jogar pouco mais de material sem mexer em velocidades e pressões faz muito a diferença.
– Pode ser vazamento de água.
– Pelo conceito do produto deveria ser com câmara quente com preenchimento pelo fundo do produto, mas como ele já existe, tem que criar alternativas, que corrige com material com alta fluidez e perfil de velocidade com escalonamento.
– É comum acontecer em moldes de cavidades profundas com preenchimento pelas bordas. É possível corrigir esse problema, trabalhando com material com alta fluidez, trabalhar com perfil de velocímetro.
– Vamos lá, essa tampa estava injetando antes com os mesmos parâmetros?
– Os testes com mais pressão de injeção e recalque foi feito como aumentar?
– Temperatura da massa está correta e as zonas do canhão estão corretas.
– Bico da cavidade do molde pode ter ferro ou tá amassado. Abre o molde e verifica se tem algum ferro que passou pelo sistema e ficou no bico da câmera quente.
Autor – Não é câmera quente.
– Vazamento de água ou óleo na cavidade.
– Saída de gás tá restrito.
– O molde não tá fazendo água Autor – Não.
– Tira um pouco o travamento.
– Diminua a velocidade de injeção e aumente a contra pressão.
– Material frio, ajustar parede deslocada, pressão de recalque.
– Se não tiver dando rebarba nas outras cavidades dá um pouco mais de pressão e velocidade de injeção, pode ser que resolva.
– Verificar a cavidade se um lado está com espessura mais grossa, corta a tampa.
– Alivia um pouco o fechamento do molde Autor – Cria rebarba.
– Para melhorar a saída de gás rápido, retire um pouco mais de (bar) tonelagem, diminua a velocidade de injeção e velocidade para controlar a rebarba.
– Têm várias coisas que você pode fazer para resolver isso. Primeiro aumenta o curso de dosagem para entrar mais material na cavidade do molde e depois aumenta um pouco a pressão e tempo de recalque, uma dica, a pressão e o tempo de recalque variam o tempo de recalque e 20% do tempo de ciclo e a pressão de recalque varia de 30 a 80% da pressão de injeção.
– Ponto de injeção e fechamento? Autor – Como assim?
– Diminui a velocidade de injeção Autor – Isso causa furos maiores.
– Tem ferramenteiro aí? Se tiver veja com ele se não dá pra melhorar a saída de gás.
– Essa situação é bem característica de saída de gás.
– Tenta ajustar pela velocidade de injeção Autor – Se diminui aumenta os furos.
– Deixa injeção mais rápido, então. Caso queime vai ter que ajustar em pressão de injeção ou recalque.
– Isso parece muito contaminação.
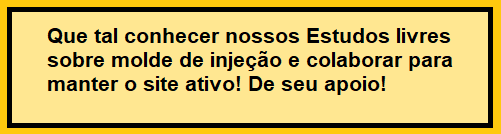
Tampa / Peça quebrando / PS cristal
Problema: injetando uma tampa de PS cristal e a peça está quebrando a trava.Qual a densidade do material?
Comentários:
– Realmente ele não pode esfriar ainda estando no molde.
– Tenta injetar com uma velocidade rápida, um tempo de dosagem curto…Com isso a peça não esfria muito no molde…Recalca menos ….
– Muito a ver com resfriamento. Recalque e tempo. Se estiver resfriando demais, ou recalcando demais, pois a entrada da água está próxima desta posição. O tempo de recalque tem que ser o mínimo possível, mas também a pressão do recalque tem que ser a menor possível.
Autor: achei o problema pessoal valeu pela Ajuda
– Fora todo seu processo de injeção, seria bom analisar se o molde não está com nenhuma contra saída que causa a quebra da trava.
– Se a parede da peça for fina é bom trabalhar com água controlada a 30 graus talvez, dependendo do ciclo.
– Fecha um pouco a água, tira um pouco do tempo de recalque, aumenta um pouco a temperatura e veja se o molde não está fora de centro. Verifique a extração se for hidráulica, diminua a velocidade se for pneumática coloque em posição correta se tiver ar do postiço coloca primeiro depois coloca válvula bem pouco tempo de as e finaliza com soprador só o postiço antes da extração hidráulica sempre com pouco ar.
– Tira todo Recalque e usa o tempo para preencher a peça
– São quantas cavidades? Se mais de uma, as outras apresentam o mesmo modo de falha?
– Se em alguma outra cavidade não apresenta o problema, pode ser que uma investigação na cavidade seja o caminho. Talvez algum pequeno raio, ou um bom polimento possa resolver, no entanto, necessário uma análise comparativa.
– Particularmente só pensaria em matéria-prima ou processo, após ter certeza que não há nenhuma anomalia na ferramenta.
– Apesar de ser uma área pequena, verifique o ângulo de saída, se não tem alguma restrição, e se estiver trincando ao extrair, diminua também a velocidade da extração.
– Às vezes o molde todo jampeado atrapalha para manter todas as cavidades na mesma temperatura, a água entra gelada em uma cavidade, e vai circulando pelo – molde e já saí mais quente.
– Eu já injetei uma peça muito semelhante, tampa de caixa de maquiagem, quebrava quando extraía, e para resolver eu injetava com molde mais quente.
– Falou que são 4 peças, verifica se é a mesma que está trincando, se for, então pode ser balanceamento da cavidade ou polimento, porque se fosse temperatura todas vão trincar, observação diminuir a pressão até falhar com isso você verifica qual das cavidades falha menos, porque elas têm que falhar iguais para balanceamento se uma estiver diferente você dar mais pressão ocasionando esse problema.
– Se tiver água natural pra colocar no molde é muito bom, também vai ajudar trabalhar com o molde aquecido.
– Análise a temperatura das cavidades pôs injeção
– PS, se trabalhar com tempo de injeção, baixa de repente que ajuda.
– A refrigeração tem que ser água quente no lado móvel e normal no lado fixo.
Se tentar dessa forma posso te garantir que para de quebrar. Também dá uma olhada na velocidade de abertura ok
Muita contração trabalha o recalque amigo que vai melhorar.
Diminui o tempo e a pressão de recalque
Diminui a pressão até falhar…depois aumente de 1 em um até completar …feito não resolveu, jogue desmoldante e pode diminuir o tempo de resfriamento pra ver tb. Pela foto eu acho que é polimento PS cristal, se não tiver bem polido quebra …também não sei se quebra na cavidade, ou depois da injeção…. podes testar um San gel também.
Pela foto parece estar arranhando
Diminui o tempo de resfriamento
– Veja a refrigeração desta cavidade se está normal e as demais. Se for refrigeração com bico valvulado, as vezes dá problema.
Autor – São 4 peças só uma da está problema.
– Deve ser algum problema na cavidade, veja se tem “canto vivo” na região ou retenção.
– Use lente de aumento para ver melhor.
– Pode ser retenção também, excesso de pressão.
– Tenta misturar um pouco de estearato de zinco no material, vai ajudar a evitar a quebra
– Talvez esteja gelando demais, trabalhei com PS cristal e geralmente acontecia isso quando muito gelada a matriz.
– A temperatura das resistências não pode ultrapassar 210 graus.
– Diminua a pressão de injeção e esquenta o molde e diminuir o tem de refrigeração
– Está usando as temperaturas com quanto. e o recalque com quanto?
Autor: 230 Gruas 2.50 de recalque
Tampa / Marca na peça (solda no molde)
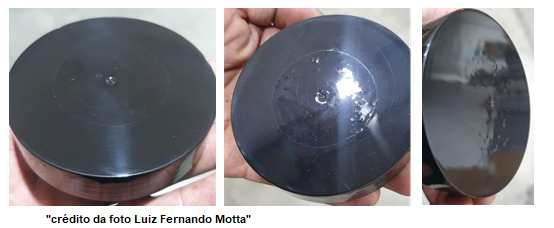
Problema: marca na peça devido retrabalho feito com solda.
Comentários:
– Parece que a solda não foi feita de acordo, e ainda o polimento não irá ajudar Cavidade nova ou refazer a solda.
– Tem que fazer uma cavidade nova, onde eu trabalho. Tem um molde parecido com esse.
– Algumas canecas racharam aqui e teve que fazer as 6 canecas novas. E outra, de cor preta todo risco que tiver na caneca vai aparecer, a cor ajuda muito para mostrar.
– Se o produto poder ficar fosco resolve o problema com um jateamento fino ou um polimento funcional, não brilhoso do jeito que está na peça. Quando tem solda quanto mais brilho mais realça a marca de solda.
– Faça uma cavidade nova caso o aspecto cosmético (visual) seja fundamental para o produto, quanto mais escura a peça mais realçara a marca.
– O certo é fazer tudo novo, a solda deixa marcas que não somem com qualquer quebra galho que fizer na superfície.
– Se a aparência do produto final aceitar faça uma texturização química que vai disfarçar a solda.
– Rebaixa a cavidade, se for possível. Assim vai ter uma cavidade nova no molde antigo.
Tampa de pote / Empenamento / Material PEBDL
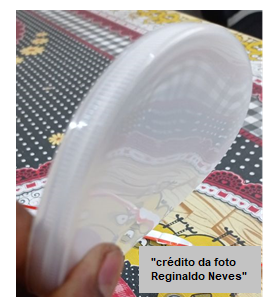
Problema: Peça com empenamento
Injetando essa tampa com PEBDL 48 de fluidez só que não consigo tirar o empenamento. Injeto com PP e sai boa.
Comentários:
– Desbalanceamento térmico do molde e excesso de pressão de recalque
– Está compactando demais.
– Temperatura do cilindro em 160-180°C e vai ser que nem tirar com a mão.
– Injeção rápida e temperatura de molde baixa também devem ajudar.
– Verifique os parâmetros de passagem para recalque é recalque. Pode estar tencionando.
– Sugiro que sempre quando houver essa situação, pare o que está fazendo e verifique a refrigeração do molde.
– O problema aí é a temperatura do canhão, porque PP é uma e PEBD é outra. Trabalhe sempre com a temperatura entre 160 a 170 graus.
– Tenta colocar uma porcentagem de PEAD misturado, mas acredito que o PP seria mesmo a melhor opção…acredito que essa mudança foi feita por questão de custo.
– Comece pelo básico tempo refrigeração, resfriamento do molde comece alto e vai baixando, segundo velocidade alta, tempo de recalque no máximo 4 segundos, abertura inicial lenta… pressão de recalque também a menor possível.
– PE a contração é muito grande, só tirando a peça gelada do molde. Ou colocar em um gabarito após a injeção. Não vai conseguir tirar o empenhamento injetando normalmente.
Faça um teste com polietileno HC 7260 e muito bom para este tipo de tampa.
Autor – Sabem me dizer porque acontece esse tipo de empenamento? Será que o material e muito mole?
– Muito provável que seja a fluidez do material, se a espessura for muito fina na aba da tampa, ela vai empenar.
– Pode ser excesso de velocidade de injeção.
– Desbalanceamento no enchimento da cavidade.
– Compactação de material na cavidade, por comutação tardia ou excesso de pressão de injeção.
– Aumentar tempo de recalque e tempo de resfriamento, isso se a peça não estiver prendendo no molde ou extração e também abaixar temperatura o máximo que der.
– Velocidade de injeção alta, tempo de recalque alto também, mas baixa velocidade só pra não rechupar a peça, resfriamento e mais alto também.
– Aumenta bastante a velocidade e pressão inicial, pressão baixa de recalque com tempo um pouco maior que o tempo de injeção, temperatura acima de 200graus.
– Tempo recalque, mas cuidado para colocar muito, pode aumenta o peso da peça.
– Qual a temperatura do PEAD? Baixar o tempo de recalque.
– Tempo de resfriamento da peça ou de um choque térmico mergulhando as peças em água gelada.
– Pressão de recalque alta, velocidade alta causa esse problema a peça fica com muita tensão, tente começar com pressão mais baixa.
– Coloca uns 20 ou 30% de PEAD junto que resolve o problema.
– Para PEBD, tem que dar um pouquinho de recalque no final da injeção só pra tirar o empenamento, comece aos poucos até tirar o empenamento.
– Quando dá empenamento aqui, tiramos um pouco do recalque ou aumentamos o resfriamento do molde.
– Baixar temperatura do molde e temperatura da injeção…baixo tempo de compactação.
– Diminua a pressão de recalque, veja se ela está tencionada, ou diminuir o material.
– A contratação do PP é diferente e também a orientação molecular.
– Tenta colocar para recalcar mais, ou um pouco mais de resfriamento pode ser que de certo.
Tampa / empenamento / material PP
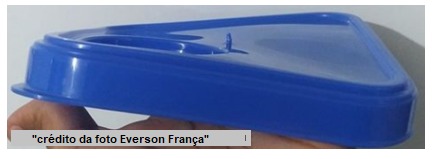
Problema: Dificuldade para injetar tampa devido estar ficando muito empenada
Material PP – Falta de água gelada para o molde.
Comentários
– Isso sempre é por tensões internas do material. Para trabalhar PP com paredes finas, procure equilibrio aumentando temperatura e velocidade de injeção, e também diminuindo pressão de injeção ao mínimo. Diminuir também o recalque mas aumente seu tempo. Se aumentar a contrapressão ajuda a aplanar também, mas é importante não injetar exceso de material.. Se aumentar a contrapressão, diminuir dose.
– Como sua peça tem parede muito fina e grande área de preenchimento, se recomenda trabalhar com maior velocidade de injeção, e com o mínimo de recalque possível…
– Para peças de parede fina em PPs e PEs, o molde não pode ter diferencial térmico entre a parte de injeção e a parte de extração. Isso provoca stress nas peças e elas empenam!
– Conforme o tipo de produto as vezes temos de aquecer partes específicas do molde para evitar esses empenamentos! Mas tenta compactar o máximo possível a peça antes de abrir o molde, e quando o molde abre verifica se a peça não descola durante a abertura do molde e provoca esse empenamento.
– Isso é comum em produtos com essa geometria devido a nervura que existe na borda do produto, e agrava mais quando injetado com PP copolímero, pois aumenta a deformação. Procurar fazer a injeção em tempo curto, sem tempo elevado de recalque, pois quanto maior o tempo de recalque maior a deformação.
– Material, PP com 10% de talco pode dar a estabilidade dimensional que você precisa ou um material com menos fluidez resolve o problema.
– Esse problema pode ser tensão, por isso o tempo de injeção deve ser o mínimo possível, pois existe a possibilidade de estar entrando material em excesso na cavidade e isso faz com que esse problema ocorra.
– Aumenta a temperatura do material assim vai poder diminuir a pressão, Esta deformação pode ser causada pela tensão do material que foi injetado com muita pressão.
– Aplique o recalque apenas para tirar as ondulações / deformações no produto.
– Observar se a fluidez do material é a mais indicada para esse produto.
– Faça um teste com resina virgem, se manter pode ser o resfriamento agora se ficar boa provavelmente é o master,pode ser resolvido com aditivo. Se o master for veiculado em PEBDL IF33 já ajuda, porém tampas feitas com pigmento azul tende a empenar a não ser que use um pigmento específico (LOWOPE).
– O problema maior pode estar na refrigeração do molde. Infelizmente peças com estes perfil tem que ser bastante resfriada antes da extração.Tem que resfriar dentro da cavidade devido as paredes finas e perfil muito plano e alongado.
– O ideal é ter a geladeira para esfriar a 10º-15º graus. Se usar água da torre na matriz, dá pouco mais de tempo e deixa peça numa superfície plana resfria. Tem que trabalhar com o resfriamento alto para poder compensar a falta da água gelada.
– Primeiro de tudo deve verificar o estado da refrigeração do molde, depois o recalque.
– Tenta regular a vazão de refrigeração do molde para trabalhar +- 38º, aí vc consegue diminuir a velocidade de injeção e a pressão, injeta 98% da peça e completa com o recalque. Cuidado com o tempo de recalque a rosca tem que parar e o tempo acabar depois.
– Como não possui a geladeira, coloque o retardo de extração para que a peça refrigere naturalmente, após o molde estar aberto. O ciclo será prejudicado, porém dará tempo para a peça “refrescar” e o molde obter uma troca térmica enquanto aberto, trabalhe também com a velocidade de extração moderada.
– Providencie uma geladeira com urgência.
– Tempo de resfriamento. Trabalho com peças de parede fina e com ciclo rápido temperatura da água chega a 12 graus o ciclo é de 10 segundo com robô pegando a peça e ainda não sai 100%.
– Outra sugestão é fazer um gabarito de madeira para resfriar com um ventilador na frente. Sem água gelada vai ser a única forma de não empenhar.
Tampa / Canhão sujo / PP e PE
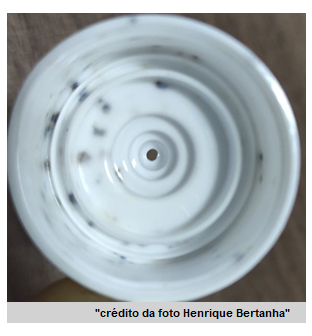
Problema: manchas escuras na peça.
Sempre que paro a injetora por no mínimo 1 dia, outras vezes sai no meio da injeção, aleatório. Uso PE de alta e baixa, no PP não tenho esse problema.
Comentários:
– PE puxa sujidades da rosca, compra aditivo e limpa a rosca.
– Onde trabalho é normal quando se inicia, purga um pouco e com o processo de trabalho vai limpando, mas se tem isso frequente antes de parar passa um pp só pra não ficar assim e perder tempo.
– Verifica as temperaturas porque essas pintas são resíduos de material queimado.
– Material queimado.
– Estranho o comentário da máquina ser nova e acontecer no meio da produção. Neste caso avalie o processo externo se o material não está sendo contaminado (transporte, abertura da sacaria, …)
– Para início com problema:
Material usa pigmento? Se sim antes de parar a produção injeta algumas peças em natural. Pigmento degrada antes e pode impregnar o conjunto.
Tem Câmara quente? Fazer limpeza junto com cilindro.
Sistema de alimentação automático ou manual? Pó no circuito.
– Fora acompanhar o processo se está de acordo: temperatura, contra pressão, tempo de residência, ….
– Antes de terminar o serviço ou parar a máquina faça o expurgo, ajuda bastante. E sempre quando iniciar a máquina nunca estará estabilizado a temperatura do cilindro com o material.
– Ou fecha o funil e vai injetando e descarta do as peças, você pode moelas e não perder o material, a borra é mais difícil de moer.
– Isto depende do moinho que se têm. Também depende da disponibilidade de hora máquina.
Autor: Vou fazer isso, deixar injetando até a máquina zerar o canhão… meu moinho não consegue moer borras grandes, só pequenas… é preferível moer as peças, também pela perca de material.
– Cada um tem uma realidade, só podemos ajudar nos processos que são comuns a todos. Provavelmente vai ter que retirar a rosca para uma limpeza.
Autor – Vou verificar isso de limpar a rosca, a máquina é nova… sempre usei para injetar branco.
– Está muito estranho por ser máquina nova. Procure utilizar um produto de expurga antes.
– Material queimado na rosca desprendendo devido a diferença de fluidez. Use um material de purga para a limpeza de canhão.
– Isto é sujeira acumulada oriundo de arranhões na rosca e cilindro.
Autor – A máquina é nova, só tenho esse problema com PE… mas obrigado pela ajuda!
Tampa / Vestígio no ponto de injeção
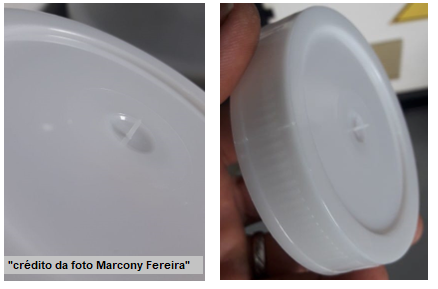
Problema: Vestígio no ponto de injeção
Comentários:
– Caso seja câmara quente: Verificar se existe direcionador de fluxo “gate”, pode ser desgaste do mesmo ou estar quebrado por inserir objetos para possíveis desobstrução quando não injetando a cavidade.
– Na maioria das vezes esse problema é do ferramental (molde) vai precisar aproximar mais o canal, muitas vezes consegue corrigir no processo, porém outras só ajustando o molde.
– Aumente a Descompressão.
– Abaixe temperatura do bico.
Autor: tempo da descompressão ou a pressão da descompressão?
– Tente aumentar a descompressão para 8 se tiver a opção de despressurização, verifique qual a melhor se adapta. Pode utilizar também a opção de após a dosagem recuar o bico. Aproximadamente 2 mm já é o suficiente.
– Molde tem Câmara quente?
– Isto é tampa de balde? Autor – Não, pote de 500gramas.
– Verificar tempo e pressão de recalque muito alta…contra pressão alta.
Tampa de vasilhame / Vestígio no ponto de injeção
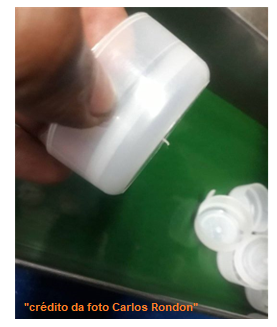
Problema: Vestígio no ponto de injeção
Comentários:
– Tem câmera quente se tiver aumenta um pouco a temperatura ajuda.
– Descompressão, baixa temperatura, abrir um pouco mais rápido.
– Aumente a temperatura da câmara quente, se persistir limpe o torpedo da câmara quente do molde.
– Geralmente neste caso, aumenta a temperatura do bico correspondente e verifique descompressão traseira no fim de dosagem.
Autor – Acho que são as ponta mesmo com desgaste, já fiz tudo nada resolveu.
-Baixar a velocidade da injeção ajuda, melhora, mis para resolver só trocando as ponteiras.
– São todas ou uma única cavidade? Autor – A maioria.
– Tenta aumentar a descompressão traseira.
– Provavelmente desgaste do torpedo, ou ele não está faceado com a placa.
– Trocar as ponteiras, bico quente por estar com desgaste, estão muito recuados e calibrar os Gates devem estar arrombados.
– Tinha molde aqui assim 8 cavidades, cada um com sua câmara, estava com o mesmo defeito, o gate estava com 1.2, somente resolveu com solda e 0,7 – Verifique o diâmetro do gate e o assentamento do diretor de fluxo do bico quente
Tampa quebrando com facilidade / Material PP
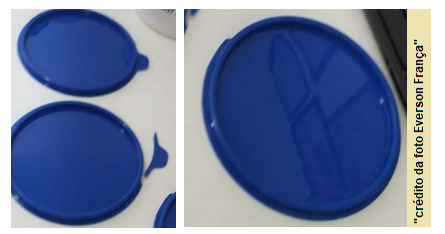
Problema: tampa quebrando com facilidade
Injetando PP novo com temperatura por volta de 200 graus
Comentários:
– Experimenta injetar a peça com material natural (sem o Master). Pode ser problema com o Master.
– Aqui injetamos propolietileno da Braskem. Nesse caso tem que ver se o PP está degradando com a temperatura do cilindro alta, programação da extração ou mesmo material ruim.
– Tivemos esse mesmo problema injetando uma tampa com PP HOMO, trocamos para o PP COPO, nada resolvido aí tivemos a ideia de injetar com PEBD, solucionamos o problema de quebra e o encaixe ficou perfeito.
– Se estiver rodando com água gelada ou industrial fecha um pouco pela metade o registro, pode resolver, onde trabalho acontece o mesmo problema eu faço isso e da certo.
– Aparentemente ela parece estar quebrando na abertura do molde, experimenta colocar água gelada só na parte móvel e água na temperatura ambiente na parte fixa, e na questão da abertura do molde faça com que ele abra mais lento.
– Para abordar este problema em uma base técnica, precisa alguns dados que não foram mencionados. Se o ponto de injeção for lateral na região oposta a ruptura, parece solda fria. O material flui mais rápido pelas laterais e mais lento no centro, o ar fica ocluso na região e a solda fria ocorre, gerando um ponto de fragilidade. Para verificar injete falhado meia peça e vai aumentando o enchimento, assim ira vendo como a frente de fluxo avança e onde a luinha de solda ira ocorrer.
– PP homo com H 503 copo 60 % homo 40 copo vai dar brilho e flexibilidade.
– Talvez o material chegue frio até o ponto onde está quebrando, caso a tampa quebre sempre no mesmo local, aumentar um pouco a temperatura e dá um pouco mais de velocidade de injeção.
– Material está muito tensionado, tenta injetar com perfil, mantém as pressões de recalque, e ponto de comutação pequeno.
– Pela foto problema no molde, deve ter um ponto onde quebra negativo e fazer um bom polimento.
– Aumenta um pouco a temperatura, 200 é baixa pra PP, assim você consegue baixar um pouco o recalque.
– Deve olhar as temperaturas do canhão, na maioria dos casos acontece isso quando a temperatura está muito elevada, ou o tempo de resfriamento muito alto, muito recalque resulta nisso também. Tem suas variáveis, mas esses pontos são importantes.
– Tempo de residência do material não pode ser longo.
Quanto % de cor estas a usar? Aqui no reino unido o padrão de qualidade aceitável no máximo só pode ser 2%, no PP se usares demasiado material para colorir perde a flexibilidade e fica quebradiço.
– Sim, o excesso de master pode afetar a resistência da peça.
– Trabalho com vários tipos de tampa específica essa PP de alta densidade nunca tive problema, temperatura zonas 180 graus.
– Importante verificar Compactação também deve está em 10 a pressão da mesma.
– Vários fatores podem ocasionar este problema. Podemos citar material de baixa qualidade ou material não indicado para a aplicação deste produto. Saindo do material para o processo, podemos citar alguns parâmetros que fazem com que a resistência mecânica do material se torne inferior, o primeiro é a temperatura em geral, as poliolefinas tem um range de temperatura nominal de 230 °C podendo variar 30°C para mais ou para menos dependendo do tempo que o material ficará dentro do canhão, ressaltando que temperaturas excessivas causarão a degradação do material tornando-o quebradiço ou com resistência deficitária, outro ponto a ser verificado é se o material não foi contaminado com outra resina, isso pode ocasionar delaminação e deixar a peça quebradiça também.
– Na injeção existem casos raros de peças de parede fina que ficam quebradiças por tensionamento no preenchimento, para isso recomendo uma verificação com injeção utilizando o mínimo de pressão e velocidade para que a peça seja totalmente preenchida, deixe o recalque desativado para este teste, após verifique a disposição da peça injetada de forma leve, sem excessos.
– Recomendo testes com materiais que possuam adição de elastômero na disposição como copolímeros destacando o grade CP da braskem que possui um índice de fluidez elevado e facilitará o preenchimento ou um Copolímero Randon RP340R que possuí fluidez média e também dispõe de aditivação de borracha em sua disposição.
– Lembrando que quanto maior a fluidez do material menor será a resistência mecânica do produto e vice versa.
– Muita pressão de recalque.
– É temperatura um pouco alta, deixa com 190 no máximo.
– Pode ser tensão. Tenta diminuir pressão injeção e deslocamento do recalque, aumentar temperatura da água.
– Use PP copolímero ou use estearina na injeção de PP Ho.opolímero. use uns 2 a 3% de estearina e você verá que não vai trincar mais.
– Pode ser molde muito gelado e está causando tenção nas moléculas aí fica frágil.
– As vezes isso acontece por causa da baixa gramatura, da maís carga na peça.
– Tenta muda o material usa com mais fluidez porque pelo jeito a parede da peça é fina, um material mais fluidez excelente para esse tipo de processo use o PP randon 40 de fluidez.
– Use PP copo.
– Está parecendo emenda fria, talvez o molde esteja muito gelado aí dá a quebra na emenda, eu tentaria uma temperatura do molde uns 15 ou 20 graus.
– Pode ser o master.
– Se essas opções de temperatura não resolver tenta diminuir pressão de fechamento, pode estar com muita pressão, também de fechamento.
– Se o master for a base de ftalocianina pede para trocar por low warping azul ultramar.
– Saída de gás.
– Já aconteceu comigo injetando com o 400 braskem, estava usando muito tempo e pressão de recalque.
– Experimenta baixar a pressão de injeção pode solucionar seu problema.
– Têm como baixar a comutação.
– A fluidez desse PP, está de acordo?
– Abaixa a temperatura.
– Material com muita fluidez.
– Temperatura muito baixa, aumenta em escala de 220 230 235 225 220 que pode resolver seu problema.
– Se essa temperatura ainda não resolve, aumenta 5 graus em cada zona.
– Trabalho injetando esse tipo de peça, tampas para potes de sorvete e aqui na empresa nós usamos uma porcentagem de E.V.A assim o material fica maleável evitando a quebra .
– Recomendo usar PP H103 Braskem, material de qualidade, 25% de copo.
– Deve ser o material e a fluidez dele.
– Material de baixa qualidade tive essa problema injetando hélice de ventilador e grades.
– Molde deve estar com algum ponto negativo.
– Tem que ver a temperatura no bico.
– Aproximadamente 35c a 40c.
– Coloca um pouco de elastômero na formulação.
– Tinha muito esse problema com dobradiças, resolvi usando 70 % de PP homo e 30% de PP random e usando no máximo 2% de master (pigmento).
– Coloque o mínimo de EVA que acaba o problema.
Autor – Qual a porcentagem que coloco mais ou menos de EVA, por quilo?
– Vai ter que testar, comece com 1%, 1,5 %…. e vá aumentando até o resultado satisfatório.
– Para tampa deve-se usar o PP copolímero por ser mais flexível, o homopolímero é mais rígido por isso acontece a quebra ou trincas.
– Exatamente já injetei algumas tampas com cp 141 da brasken, é o mas indicado nesse caso por ser um material com boa flexibilidade.
Manchas efeito fosco – Material PP
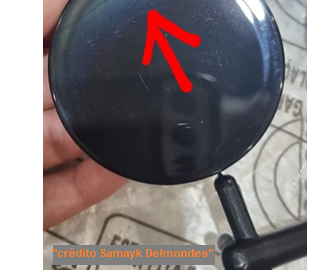
Autor- Problema na injeção de tampas em PP RT virgem +2% pigmento granulado preto. Em algumas tampas está causando essa mancha, parece um efeito fosco, arco íris.
Molde de 8 cavidades. Temperatura bico 200 °C.
Z1 190 °C / Z2 190 °C / Z3 185 °C. Refrigeração do molde com água temperatura ambiente.
Comentários:
Parece saída de ar, dá uma verificada como estão as saídas, provavelmente está com sujeira ou alivia a pressão de fechamento, ajuste para travar mais suave.
Oposto ao ponto de injeção, me parece gás. Coloca um pino poroso para saída de ar.
Essa mancha aí é de gás do material, pede para melhorar saída de gás do molde pode ser que melhore, mas as cores pretas sempre dão essas manchas mesmo.
Pode ser saída de gás, água gelada no molde pode dar essa mancha, material com umidade. Saida de gás insuficiente ou master queimando.
PP estufa ele com até 40 ºC, vai dar uma melhorada nesta estria.
Põe o material para estufar por 1h +/1 a 100 °C, talvez possa melhorar.
A entrada restrita do canal de injeção, pode causar atrito ao entrar na cavidade, gerando alterações no polímero virgem com pigmentos granulado. E também concordo com melhorias nas saídas de gás.
Aconteceu caso semelhante. Estávamos injetando PP, móveis para cervejaria, na cor vermelha, o pigmento do mesmo fornecedor um lote estava degradando, fiz muitas experiências, em outro caso uma das zonas de temperatura o cabo termopar não estava informando a temperatura real, estava acima do programado.
Reduz a % de corante para 1%. Comuta com a peça cheia e com temperaturas baixas, mas antes faz um polimento ao molde porque já tem resíduos acumulados nessa zona. Mas polir mesmo.
Corrija a temperatura de processo, porque o seu pigmento está sendo degradado. Na primeira zona, diminui um pouco da temperatura que vai ficar perfeita. Depois de um retorno para nós.
Aumenta o canal de injeção, a passagem do material está restrita. Problema é que o material não está copiando o molde devido pressão diferente dentro da cavidade.
Se tiver como, dá uma polida nessas cavidades, parece ser emenda fria. Provavelmente desbalanceamento de cavidade. Não é fácil corrigir assim molde, precisa injetar, então equaliza pressões de velocidades de injeção e recalque. Não pode ter muita diferença.
O problema pode ser que o material injetado no centro, percorre pelas laterais (provavelmente as paredes laterais, sejam mais espessas que o centro, e chega no final antes do material que está percorrendo pelo centro, desta forma, você terá ar preso nesta região e consequentemente, linha de solda fria. Para verificar é só injetar a peça falhando e ir acompanhando o fluxo do material, vai fica um vazio no ponto de em questão. Outro problema é a umidade do masterbatch, visível na lateral da peça, ou seria marca de extração?
Não está com água muito gelada no molde ou temperatura baixa no pé da rosca?
Parece que essa entrada de material não é apropriada para tampas, faz ângulo sem mexer na passagem final do material, assim o material não esfria nessa passagem final. Parece que está queimando no final do preenchimento.
Solução: autor:
– Consegui resolver aliviando um pouco a pressão de fechamento, reduzindo as temperaturas e estufando o material.
Manchas na cor preto brilhante – Material PP
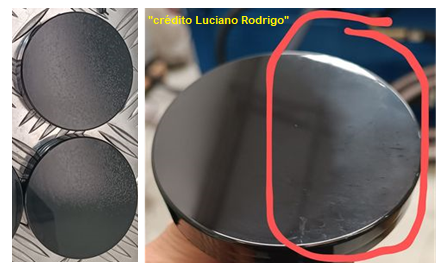
Autor – Dificuldade para eliminar essas manchas, que estão saindo na cor preto brilhante. Material H103 pigmento CPE 4050 ER (Polipropileno H 103).
Comentários:
Verifica o polimento do molde, aumenta um pouco a temperatura do cilindro e baixa a pressão de injeção… aumenta a contrapressão para homogeneizar melhor seu material… se for molde de Câmara quente baixa um pouco a temperatura… verifica tudo isso com atenção para não compactar demais a sua peça.
Verifica a descompressão se tiver muito alta abaixa um pouco.
Autor – Já abaixei subi e não resolveu
Esquenta mais se não melhorar é material contaminado.
Veja se o ponto de injeção está no lado oposto da mancha. Se tiver você deve verificar a saída de gás.
Autor – Sim está do lado do oposto, mas já verifiquei deu rebarba e não resolveu.
Não consegui ver claramente, porém observe se a saída de ar está legal.
Primeiro verificar a saída de gás, segundo verificar a o capilar do canal se está balanceado, caso estiver estrangulado pode gerar esse tipo de problemas em umas das cavidades. Verificar o perfil de regulagem isso pode causar .eu precisava saber que tipo de produto e material para saber da uma resposta mais objetiva.
A causa da mancha é a saída de gás. As vezes se resolve com menos velocidade de injeção também. Mas o molde tem saída de gás? Pode também ser que você esteja trabalhando com muito pouca contrapressão, daí forma muito gás na rosca na compactação do material. Alta temperatura do material pode também causar gás.
Já aconteceu comigo, para eliminar e com saída de gás. Só dá um pouco de abertura na máquina.
Autor – Já tentei TB e não resolveu.
Aumenta a Temperatura do bico e as 2 zonas para trás, tenta deixa o material mais fluido pela temperatura e não pela pressão ou velocidade.
Algumas possíveis causas, tem que ver se o bico está trabalhando apoiado ou com recuo, pode causar isso dependendo como está. Outra coisa e secar o material pode estar úmido. Também pela foto não se vê mais se a rajada está mais grande no ponto de injeção, pode ser a entrada do material que seja pequena ou que está injetando muito rápido. Pode testar também abaixando a velocidade de carga e subir contrapressão de carga. E abaixar a sucção de carga todo que puder também.
Está mais para umidade ou saída de gás do molde.
Autor – Já fiz o teste, mas não é.
Verifique se o molde está bem limpo e polido, trabalhe com as temperaturas baixa, rotação de rosca baixa para gerar menos gás, limpe as saídas de gás e use água industrial.
Tive um problema deste a muito tempo atrás. O problema era a resina base do Master. Falei com o fornecedor e fizemos um Master com o mesmo material a injetar. O problema acabou.
Também acho que é algum tipo de contaminação, resta descobrir qual.
Está parecendo ser pigmento.
Umidade na matéria prima.
Este brilho pode ser muita velocidade na injeção, baixar um pouco a velocidade de injeção e também baixar a pressão de injeção espero ter ajudado, precisa fazer mais escape de gás também.
Parece delaminação, se for é contaminação ou degradação do material ou corante
se só aconteceu com o preto, experimente usar negro de fumo ao invés de máster
Este molde trabalha com câmera quente?
Considerando que seja saída de gás. Qual o peso do molde e o tamanho da máquina? Verifica se o molde é muito pequeno para trabalhar nesta máquina se for o ideal é colocar numa máquina menor se não tiver outra máquina vai ter que reduzir a pressão de travamento aí deve-se ajustar os parâmetros novamente para não dar rebarba.
Verificar como estão as canecas do molde se elas estão bem polidas e espelhadas, se essa mancha está lá vai sai na peça também… trabalho com um molde desse de 6 cavidades e na cor preta deu a mesma marca.
Ainda não conseguiu eliminar a mancha? Você já verificou a refrigeração do molde, as vezes a água pode estar passando mais na parte da mancha. As velocidades de injeção também podem causar manchas se não tiverem corretas.
Umidade sem dúvida.
Ou material úmido ou saída de gás.
Material contaminado e úmido.
Tampa saindo empenada

Autor – Injetando tampa de saladeira com reciclado, porém ela está empenando, como resolver!
Comentários:
Pode ser tanto o resfriamento do molde, ou resfriamento que vai usar, se ela está dentro do colchão, temperatura do material, tanto de recalque que você está usando, tudo isso vai influenciar para ela não ficar reta.
Dá uma olhada no peso se não está alto também
Injetando com qual material “reciclado” – PEBD ou PP? (lembrando que para peças que poderão entrar em contato com alimento não é aconselhável usar reciclado).
Pode verificar se está mesmo circulando as águas para resfriar o molde ou pode tentar com mais ou menos tempo de recalque, verificar se não está preenchendo a cavidade com muita carga ou com muita pressão de recalque
Aumentar o arrefecimento da peça e ir baixando velocidade de injeção da peça
Dê uma olhada se uma peça que falhou está assim também, pode ser canal de injeção muito fino, aí a pressão de injeção ou de recalque vai lá em cima, aumentando a contração da peça.
Sabe que vai ser difícil, pois o material pode não ser o indicado para peça, aumente a temperatura gradativamente, aumente a pressão e vai subindo a passagem para recalque com a pressão reduzida. Deverá reduzir a contração melhorando o empenamento.
Além das observações colocadas, caso a extração esteja forçada, isto favorece o empenamento. Caso além da extração mecânica houver pneumática, é importante ajustar posição e tempo de atuação.
Muito Recalque também contribui para empenamento.
Tente injetar só com pressão e velocidade de injeção.
Verificar as mangueiras de resfriamento do molde para ver se está funcionando corretamente. Aumentar um pouco do resfriamento pode ajudar também. Caso você não esteja usando o robô para a extração da peça, verifique se a rampa onde a peça está caindo não tem ondulações ou deformidade. Tente recalcar também um pouco menos.
Isso nada mais que tensão na massa injetada, independentemente de qualquer coisa.
Velocidade de injeção no máximo possível e pressão de recalque no mínimo possível.
Mistura homogênea da resina virgem / reciclado.
Tínhamos problemas de empenamento, mas a mistura PEAD/ PEBD estava errada.
A tampa deve ser injetada com alta velocidade de injeção, com certeza não vai empenar, já trabalhei com esse tipo de peça.
Aumenta o resfriamento e quando sai espera a peça esfria.
Seria bom água gelada no molde.
Aumenta a compactação e o recalque que resolve.
Pode utilizar choque térmico com a peça caindo diretamente em água fria, costuma resolver.
Empenamento de tampa dez minutos, após injeção
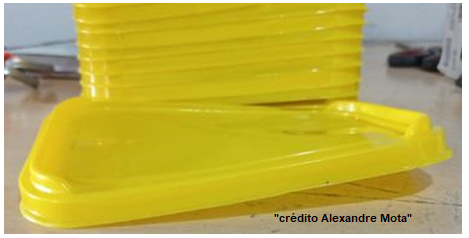
Autor – Estou com problemas de empenamento em tampa com parede fina de 0,6 mm. A tampa sai plana e após 10minutos começa empenar, já testamos 3 Copolímeros distintos com fluidez de 45 em 3 injetoras diferentes, inclusive moldes distintos e o problema só altera o tempo para empenar, umas já saem empenadas. Qual seriam os parâmetros mais importantes para não provocar empenamento em tampa de parede fina?
Você está usando material randômico?
Autor – Copolímeros de fluidez superior a 40, vários grades foram testados.
Qual temperatura você está usando no processo? E na câmara quente?
Pode ser falta de resfriamento.
Aumenta o resfriamento, tenta diminuir a pressão de injeção, velocidade de injeção e pressão de recalque.
Temos uma tampa de porta frio igual, parede fina e bico quente, o único material que resolveu foi h103. O único que usamos em paredes finais, não empena.
Faz teste se o tempo de resfriamento está sendo adequado para não acontecer esse empenamento.
Como é a refrigeração do seu molde, é água gelada na parte fixa e móvel ou industrial na parte fixa e móvel.
Autor – Sim, ambas com água gelada.
E quanto é o tempo de resfriamento?
Autor – 0 segundos, o tempo de dosagem é suficiente para resfriar a peça.
Coloca nos 10 segundos de dosagem e 60 de pressão de dosagem para o material misturar bem na rosca.
Faz um teste de resfriamento, coloca uma bacia e deixa a peça cair dentro da água e aguarda 1 uns 2 minutos.
Se a maioria das tampas saem boas e empenam depois, pode verificar resfriamento e diminuir a pressão de injeção e recalque, vai fazendo isso por etapas.
Use água gelada, menos recalque e mais tempo de abertura do molde e tente um conformador.
Isso é tensão no polímero. Pois foi injetado com um estresse muito grande, então durante o empacotamento molecular é natural que a contração aumente.
Mapeie seu processo e verifique o que pode estar gerando isso.
Mas eu injeto essa tampa também e não temos mais este problema.
Diminuir a pressão de injeção e vai baixando até quase falhar, aí entra com o recalque só para segurar o dimensional, já vai melhorar, aí é só acertar o resfriamento.
Sobe a temperatura gradativamente, aumenta a pressão de injeção e velocidade, antecipe a passagem para o recalque e diminui a pressão do recalque para evitar rebarba, vai mudando o tempo do recalque para mais ou menos e observe o empenamento.
Como que está a refrigeração do molde, está bem gelada.
Abaixa a comutação.
Temperatura mais baixa e recalque.
Dormiu o tempo de injeção, isto é muito material em pouco espaço.
O recalque ou 2°pressão tem de ser o mínimo possível e aumentar número de circuitos de água.
Aumentar a calota no ponto de injeção, faça com 1mm de profundidade por 5mm de diâmetro.
Diminuir pressão de injeção, diminuir velocidade de injeção, faça testes aumentando e diminuindo o tempo de recalque, aumentar tempo de resfriamento, essas são possíveis soluções para seu problema.
trabalhei com tampas de balde de 3 litros, e esse problema ocorria também, vai conseguir resolver esse problema com tempo de recalque e resfriamento. Repare as entradas de água (gelada) se for o seu caso, se na parte fixa e móvel estiver a ligação de água com as entradas no mesmo lado, inverte…. ou trabalhe com água gelada na parte móvel e industrial na fixa. O molde é câmera quente ou bico valvulado?
Autor – Câmara quente sem bico valvulado.
Tente trabalhar a compactação (diminuir), tempo de recalque e resfriamento.
O molde é de múltiplas cavidades? Pode estar desbalanceado.
O processo de injeção de parede fina, é injeção rápida até completar 95% a 98 % da peça, a partir daí trabalhar com pressão e tempo de recalque, parede fina = tempo baixo e pressão alta de recalque, realizar variações destes parâmetros e analisar.
Injetar qualquer produto com parede fina não é fácil principalmente tampas. Trabalho com esse tipo de tampa e dificilmente conseguimos uma peça 100% plana. Geralmente tentamos amenizar, abaixando as pressões de recalque e injeção, o molde deve ter uma boa refrigeração com água gelada, aumenta o tempo de resfriamento. Caso não esteja conseguindo, faça um gabarito e coloque as tampas uma sobre a outra e colocar um peso pelo tempo necessário para serem resfriada em uma posição que elas fiquem plana.
Veja seu ponto de comutação, geralmente é sobre compactação na entrada do material para a peça, gerando contrações diferentes.
Diminui pressão de injeção e aumenta velocidade de injeção e resfriamento.
Só aumenta o tempo de recalque, vai devagar para não aumenta o peso.
Verifica o resfriamento do molde, pode ser entupimento nas vias de resfriamento do molde. Observa se a contração é na fixa ou na parte móvel do molde. Tenho certeza que será isso. Trabalho com pote de sorvete e tampa.
Já tentou resfriá-los em água imediatamente, após saírem do molde? Se impressos automaticamente, eles podem cair em uma calha que os leva para um recipiente com água resfriada. Muito provavelmente a deformação, além de ser causada por pressões muito elevadas, também se deve provavelmente à diferença de espessura entre a parte central plana de 0,6 mm e a borda que certamente tem espessuras maiores, por razões técnicas. Como a parte central é mais fina (0,6mm) tem uma pós-contração em % menor, em comparação com as bordas com maior espessura que têm uma pós-contração em % maior que a parte central, portanto, criam-se tensões.
Processo, pode diminuir o tempo de recalque e trabalhar com a pressão de recalque um pouco alta para compensar o empenamento.
Recalque maior e velocidade de injeção maior.
Onde trabalho fizemos ralador de legumes e isso também acontece, nós empilhamos montinhos de 10 e colocamos um pezinho em cima até esfriar bem e fica bem retinho, se não conseguir acertar a injeção e uma dica boa.
Pressões altas de recalque e injeção, e tempo de resfriamento baixo causa esse empenamento, outro método utilizado em empresas é a peça cair dentro da água, com esse choque térmico na peça diminui a contração do material posteriormente. Mas por ser tampa tem que se atentar ao fazer alguma modificação, pois influencia diretamente no dimensional da peça.
Dá um choque térmico com água para resfriar mais rápido, assim tira o empenamento. Coloca uma caixa de baixo que a peça cai logo, após a ser extraída.
Isso se chama refugo. Se antes do teste de alta temperatura já sai do molde assim, imagina como ficará após o teste.
Injeção parede fina, e uma tecnologia diferente da convencional, sugiro, fazer um estudo estrutural da tampa, alterando as espessuras de parede, como defletores de fluxo, o outro problema está, nas possíveis diferenças de temperatura entre matriz cavidade, não deve ser superior de 3 a 5 ºC, por esse motivo é inserido postiço de cobre berílio no fundo da cavidade para aliviar as tensões (shear stress)…ideal injetoras com acumulador, com ciclo de injeção, entre 3/5 seg. (sem recalque) é volume de injeção mínimo o dobro das injetoras parede grossa, (360 cm3/seg) ou seja 760/980 cm3/seg.
Por exemplo para parede fina as injetoras Husky, fornece 3 tipos de diâmetros diferentes de rosca, e pressão de injeção superior a 180 Mpa, das injetoras convencionais, podendo chegar facilmente a 320 Mpa. o dobro….
A matéria prima é PP copolímero heterofásico, tipo CP404XP.
O PP por ser um plástico cristalino contrai bastante 1-2%. A distorção deve-se a contração desigual e pode ter várias causas, as principais é o recalque (pressão e tempo), por ser parede muito fina, imagino não dá tempo de recalcar, velocidade de injeção muito alta e o pigmento.
1)Injetar sem o pigmento ou com pigmento de outra cor.
Pois o pigmento dependendo do princípio ativo, interfere na contração.
Aumentar o resfriamento da cavidade, parece que está empenando para fora.
Se não resolver, reforçar as abas laterais. Boa sorte. Atenção no pigmento.
Tem de ter injeção rápida, fluxo alto, tempo de injeção somente o suficiente para preenchimento com porcentagem mínima para evitar rechupe, (não trabalhar com recalque) zero tempo de recalque.
Avaliar além das condições de processo, se houve troca do pigmento usado. Dependendo do tipo, o pigmento pode atuar como nucleante e causar contração da peça.
Fazer direcionamento de fluxo, interno para chegar ao mesmo tempo na lateral e nos cantos.
Excesso de rebarbas de repente
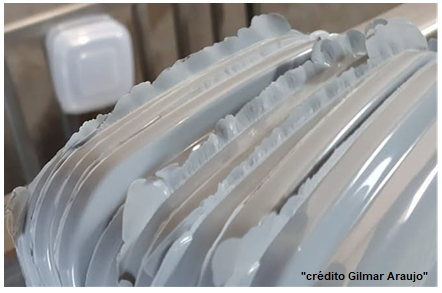
Autor – Máquina ajustada, após algumas horas de trabalho começa a sair rebarbas enormes e depois de um tempo normaliza.
Comentários do grupo:
Verifique a refrigeração, se estiver ok veja o curso de dosagem. Qualquer coisa diminua o curso de dosagem até a peça falhar e vá ajustando. Outra coisa que pode ajudar, veja se a contrapressão não está muito alta.
Já vi casos assim, fechamento do molde, depois que aquece a dilatação melhora o fechamento ou não.
Autor – Parece que está ao contrário começa bem depois acontece as rebarbas.
A máquina não está segurando a tonelagem, diminua tempo de injeção e curso de dosagem, verifique se está circulando água no molde.
Acontece muito quando é material moído, aí muda para material novo preparado, isso interfere na regulagem.
Às vezes é alguma instabilidade no lote do material, pode estar com índice de fluidez alternando de saco para saco.
Pode ser algumas coisas, uso de moído, travamento da máquina, refrigeração do molde.
Coloca um tempo de retardado de injeção, pode ser que o molde está abrindo na hora que injeta.
Verificar variação no índice de fluidez, verificar temperatura do molde, se tiver polímeros com índices de fluidez diferente pode acontecer isso, ou variação de temperatura no molde, tenta diminuir temperatura do molde, velocidade e pressão de injeção, temperatura do canhão.
Dá mais fechamento, o molde pode estar quente e dilatado.
Pode ser variação na posição de injeção, verifica se está chegando no colchão, tenta injetar com menos carga e mais velocidade, assim ela não fica incompleta, assim ela vai atingir o colchão e daí pode controlar a rebarba.
Acontece muito se está sobrando muito no colchão, horas ela injeta mais, horas injeta menos.
Pode acontecer de estar perdendo o travamento do molde…. refrigeração…
Pode ser refrigeração.
Tá trabalhando com moído / extrusado?
Autor – moído.
Pode ser o moído, mudando a fluidez.
Tem quer ver a fluidez do material com seu fornecedor, está oscilando muito, pode ser que seu fornecedor esteja usando um pouco de carga junto, é só pesar e comparar os pesos, do material pronto.
Controla a temperatura do molde quando estiver bom e quando estiver saído a rebarba.
Uma variação de 10 ºC já pode fazer isso a depender do molde e máquina.
Verificar a posição até onde está fazendo leitura da régua de injeção, pode ser régua com problema ou forno ou ponteira gasta.
Ver estrutura do molde, ver também entradas de material se estão balanceadas.
Verifique o anel de bloqueio se não está querendo.
Além de todas possibilidades citadas, verifique se não há corpo estranho na câmara quente ou no bico.
Uma boa forma de tentar resolver este problema, pela situação que falou seria fazer um passo a passo do seu processo de injeção novamente, completando esta peça com volume de dosagem, pressão e comutação deixando seu recalque por último, talvez a pressão deste parâmetro possa estar gerando esse problema, uma variação no tempo de injeção também é uma opção a ser avaliada.
Pela rebarba … Acho que está mais para perca de pressão no travamento …
Dá uma olhada na temperatura do óleo, óleo muito quente ou de má qualidade pode ocasionar perda de pressão.
Pode ser bico entupido!
Anel de bloqueio do canhão com problema.
Autor – Já tirei e verifiquei.
Já observou a temperatura do molde, se está havendo circulação de água no interior do molde, qual a fluidez do material? Temperatura de canhão e câmara quente.
Temos alguns defeitos que podem acontecer, sendo eles analisados na máquina: válvulas com retorno de óleo, precisa fazer limpeza e verificar molas e o carretel se está gasto, pistão dando passagem pelo embolo, fazer teste soltando a mangueira de retorno, se acontecer perde pressão. Rosca gasta e alterando comportamento ao plastificar, tirar rosca e verificar diâmetro do canhão, rosca e Anel de bloqueio. Variação de temperatura, problema elétrico de sensores de temperatura ou fases das resistências queimada, principalmente as próximas ao bico.
Autor – Estou verificando isso.
Se depois de um tempo normaliza, pode ser o tempo de residência que ficou parado no cilindro.
Pode ser variação de pressão da própria máquina.
Pode ser pressão de fechamento, já tive este problema, sistema eletrônico com defeito.
Pode ser temperatura do canhão oscilando eleva temperatura da rebarba.
se está usando moído, acredito ser variação do próprio material.
Autor – duro que fiz teste com virgem e aconteceu também.
Pode ser pistão de fechamento que está com vazamento interno retorna no momento de injeção (montar um relógio comparador que já elimina essa possibilidade).
Molde fora do centro. Força de fechamento baixa.
Pode ser ar no sistema de refrigeração do molde as vezes inicia bem, mas depois sai rebarba.
Come está sua refrigeração. Faz uma medição de temperatura do molde. A 15 minutos dei início do processo e quando está saindo rebarba.?
Verificar a pressão de fechamento da máquina.
Acho que a máquina está perdendo a altura não está segurando a tonelagem.
Com certeza está variando a pressão de injeção aí ela está abrindo.
Será que não está perdendo o travamento?
Autor – Pensei nisso, mas do nada volta ao normal.
Pode ser que tenha algum vazamento de óleo interno no sistema de fechamento.
Autor – Duro que não, fizemos teste com material virgem.
A máquina deve estar abrindo a altura de molde durante o processo. Aconteceu comigo. Desligue a altura de molde na válvula.
Isso pode ser rosca gasta, mal circulação de água no molde, material com fluidez diferente, bico ou bucha quente entupida. Esses são alguns fatores que levam acontecer isso.
Talvez seja máquina… Verifique válvulas, atuadores e demais periféricos hidráulicos tanto do conjunto injetor como do conjunto de fechamento… Avalie se as resistências tem dado pico de aquecimento…
A intermitência do processo pode ser do equipamento…
Pode se porcentagem de material reciclável está muito alta.
Tem que mandar uma foto da tela das pressões e velocidades, o material e as condições da máquina se está com manutenção em dia para agente te ajudar melhor, só a peça com rebarba não tem como.
Pode ser a Temperatura do óleo que sobe, fica mais fino altera o ajuste.
Verifica se o colchão está alterando na hora da injeção e tempo de dosagem, aí pode ser anel de bloqueio.
Deve trabalhar com almofada e ver se sobra sempre material, mesmo quando faz rebarba.
Se tudo estiver bem, então tem um problema no fecho da máquina.
Material pode estar variando.
Autor – Já fiz vários testes, até com material virgem.
O molde tá demorando muito para esfriar no início do processo, verificar as águas e veja se a refrigeração está em bom funcionamento.
Se a máquina está de acordo com área projetada do molde, se sim ver a possibilidade de fazer escalonamento da pressão de injeção e velocidade, vendo assim me parece que está com muita sobra de material, outra coisa evitar contrapressão excessiva.
Ou problema na contrapressão da máquina, água, travamento do molde.
Anel de bloqueio gasto, troca ele e já era.
Variação no travamento.
A máquina não está estável, tenta estabilizar a dosagem, o molde repare que está sempre a mesma temperatura, e pode ver também o fecho da máquina se está bem afinado.
Esse problema que você colocou nos dá uma série de resoluções…
Mas vou falar alguns itens que na minha opinião podem estar afetando seu processo.
1° No decorrer do dia depois de ajustado o processo verifique se o travamento da máquina está variando (abrindo durante o processo de trabalho).
2° Verifique se as águas do molde estão corretas e se não tem nenhuma entrada ou saída entupida e ou que tenha pego ar.
3° Verifica o material, se for algum tipo de moído pode ter algum tipo de variação decorrente a isso.
4° Outros fatores também, podem ser o anel de bloqueio que pode estar danificado, fechamento e pinos da máquina e até mesmo alguma válvula variando pressão.
5° E por último e mais importante, de uma nova verificada no processo, olhe se depois de estabilizado ciclo da máquina e as temperaturas do material, se não é alguma pressão/velocidade/posição na injeção.
Pode ser variação no material. Se for reciclado as vezes acontece isso.
Analise a câmera quente, pode ser um dos fatores.
Problema estético por má homogeneização – Material PP
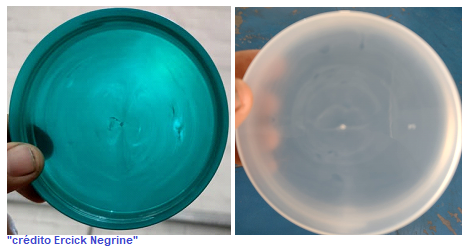
Autor: Problema estético na tampa, parece que o material não está com boa homogeneização, deixando a peça fora do padrão de qualidade. Material PP h103.
Comentários do grupo:
Tem que aumentar a rotação da rosca para homogeneizar melhor, aumenta um pouco a contrapressão e veja a temperatura.
Aumenta temperatura e contrapressão.
Com estas dicas se não resolver pode ser contaminação com outro tipo de material, veja com o fornecedor. Qualidade do master, percentual do master. .
Contrapressão aumentar.
Aumentar temperatura do cilindro e contrapressão + 5%, se não resolver tenta trocar a resina, colocar o PP FT120, para esse ø de tampa essa resina é a mais indicada.
Contaminação no material.
Aumenta a temperatura do canhão.
Diminui a contra pressão e aumenta o tempo de dosagem.
Já tentou aumentar a contrapressão e abaixar a velocidade de dosagem e se usa uma carga 250 mm, aumenta ela pra 500 e um colchão alto, que de para ajudar com nesse problema de homogeneização.
Temperatura e contrapressão é só aumentar um pouco.
Diminuir velocidade de rotação da rosca, aumentar temperatura do canhão.
Homo media 220 °C.
Isso aí é contaminação porque são em pontos diferentes.
Se quiser uma solução fora de aumentar contrapressão utilize um bico homogeneizador.
Aumentar temperatura e contra pressão e um pouco o curso da dosagem e também existem flanges para colocar no canhão que ajudam muito na homogeneização.
O material não está homogeneizando direito, para isso tem que alimentar a contra pressão e baixar a velocidade da rosca, porque o master pode ter uma dureza maior que o material de trabalho, talvez precisa aumentar um pouco as temperaturas do processo.
Isso é contaminação no PP. Pela foto parece que estava na cor branca anteriormente. Se for bico quente é só aumentar a temperatura e esperar um pouco depois baixar para temperatura correta.
Tente aumentar as temperaturas do cilindro de aquecimento +- 10 a 20C.
Melhorar a plastificação aumentando a contrapressão.
Checar rotação da rosca e por vai tentando.
Aumenta a temperatura, a contrapressão de dosagem e faz o escalonamento da velocidade da injeção da menor para mais, vai te dar um ganho considerável no fim do processo.
Seu máster e mais duro que o pp h 103 aumenta.
A temperatura de acordo com o processo.
Se o MFI (índice de fluidez) do Master for menor que a o da resina, não vai abrir tão fácil e possivelmente mudar radicalmente parâmetros e degradar a resina. Converse com o fornecedor, se tiver incompatibilidade de fluidez, ele corrige rápido.
Com certeza tem PP Randon misturado com pp homo isso faz não homogeneizar devido a fluidez de cada um.
Abaixa a velocidade da dosagem e aumenta um pouco a temperatura.
Qual a capacidade de plastificação em kg/h do canhão? Você pode ter estourado a capacidade de derreter o material do canhão logo, está injetando o grão em estado sólido… são grãos não plastificados nesta peça.
Temperatura e contra pressão.
Aumenta um pouco a temperatura e a contrapressão.
O problema é contaminação. Dois materiais diferentes, um funde outro nem tanto. Troque o material e o problema estará resolvido. Isso acontece porque as recicladoras não usam telas apropriadas.
Autor – A matéria prima e virgem PP h103.
Material virgem não significa que ele não esteja contaminado.
Eu sugiro contatar o vendedor de resina. O H103 é um material de fluidez alta, não justifica dificuldade em homogeneizar.
Autor – Essa máquina e molde são novos, três meses de uso só .Já produziu com outro molde, mas a mesma matéria prima, não temos outro tipo de matéria prima na empresa.
H103 é top o problema é outro com certeza material moído contaminado.
Está usando master errado, é muito comum, todo mundo faz isso.
Pode ser um master com base em polietileno e não dispersar em PP com fluidez alta. Porém parece pontos brancos também na peça sem master.
Seu material está com umidade, colocar em estufa por meia hora.
Atualizado em 17/01/25
Esperamos ter colaborado com os profissionais!
Fonte: Grupos Técnico em Plásticos e Injeção Plástica
Criação, edição e resumos: Moldes Injeção Plásticos
Acesse, isso também irá facilitar o trabalho do profissional:
TABELAS COM VALORES PARA APLICAÇÕES DE TERMOPLÁSTICOS
INDICAÇÕES PARA O PROCESSAMENTO DE DIFERENTES MATERIAIS PLÁSTICOS – 01
INDICAÇÕES PARA O PROCESSAMENTO DE DIFERENTES MATERIAIS PLÁSTICOS – 2
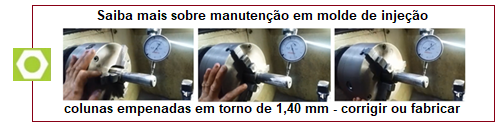