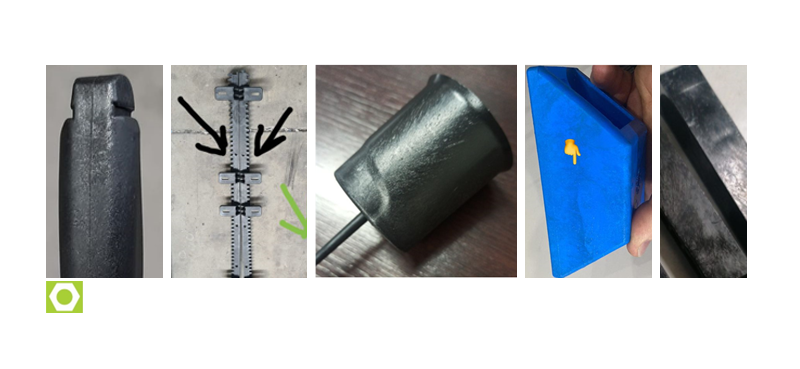
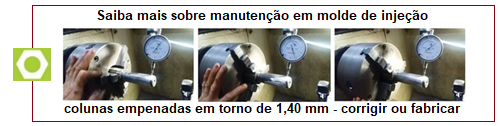
Problemas de injeção plástica em peças de PA
Este conteúdo abrange diversos problemas que ocorrem durante a injeção de diversos produtos plásticos no dia à dia. São resumos de casos apresentados e que receberam comentários e sugestões de profissionais. A ideia é levar a informação na palma da mão, para um melhor direcionamento no momento da necessidade. Se lhe interessa saber mais sobre molde de injeção, manutenção em molde e sobre defeito em peças plásticas indicamos nossos Estudos livres. http://moldesinjecaoplasticos.com.br/loja/
Defeito de injeção plástica em peças técnicas de PA
Pontos com excesso de brilho

Problema: Pontos com excesso de brilho.
Comentários:
– Não está copiando toda a textura do molde, pode aumentar temperatura do molde ou do fundido, limpar saída de gases, aumentar a velocidade de injeção
– Use acima de 80⁰c no molde.
– Use 215 ⁰c a 240 ⁰c na temperatura canhão.
– Use PA sem umidade, desmistificar dentro da especificação.
– Escape de gás.
– Tempo de injeção somente para completar a peça.
– Sem resfriamento, somente o tempo que leva para dosar, salvo se usar um controlador de temperatura no molde, pode usar um resfriamento o suficiente para extrair.
– Para este tipo de problema ajuda se mostrar uma foto com o canal de injeção na posição de entrada na cavidade, ou seja, foto do canal + peças.
1. A princípio precisa saber qual é o PA (6, 6.6, etc) pois terão ajustes diferentes.
2. Secar muito bem o material se possível utilizando desumidificador.
3. Molde com refrigeração superaquecida, em torno de 90 graus.
4. Tempo de enchimento da cavidade rápido (velocidade alta).
5. Compactação de material na cavidade alta.
– Este material é um PA 6 de alta fluidez; não é complicado para injetar.
– Secar bem, molde bem quente e não elevar muito a temperatura da massa, trabalhar entre 240 e 250 graus, pois pode degradar principalmente se não estiver bem seco.
– Talvez jateando a ferramenta. Segunda opção abaixando a velocidade de injeção .
– O ponto de injeção é do outro lado. Tem alguns fatores que podem influenciar no aparecimento deste brilho. Temperatura alta. Velocidade de injeção muito alta e pouca saída de ar nesta posição.
– Bico de injeção curto injeção rápida, se não melhorar coloca um aquecedor de água no molde.
– Calor no molde e escape de gazes
– Abaixe a rotação da rosca verifica se tem a hipótese de mudar a refrigeração do molde.
– Tem que acertar na textura do molde, aparentemente tem variações, uma parte mais brilhante e outras foscas.
– Qual o material e temperatura do molde velocidade de injeção?
– PA com fibra, veja o tempo de estufa se foi o suficiente ou se foi usado direto material.
Autor – Teve tempo.
– São gases… verifique se há umidade na matéria prima ou se no molde há escape de gases.
– Só dar um Jato de areia no molde.
– Temperatura do molde.
– Temperatura só diminuir.
– Falta massa nesse ponto, aumenta a velocidade de injeção, outra coisa, verifica como está a refrigeração do molde se as vias não estão entupidas ou se está ligada corretamente.
– Diminui velocidade de injeção e aumenta e aumenta o tempo da injeção ou pressão.
– Procure injetar mais rápido, isso aí é falta de fluxo do material quando está chegando nessa área da peça, diminua a posição da almofada que some.
Autor – Escapes estão ok.
Haste apresentando empenamento
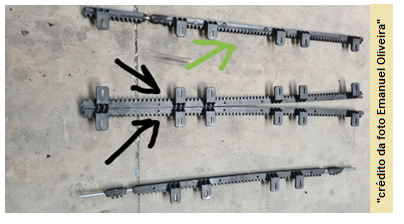
Problema: Haste apresentando empenamento.
Como compensar? Material PA6 20%GF.
Comentários:
– Dispositivo com resfriamento de água gelada após a injeção.
– O ideal é um berço de resfriamento este empeno é inerente ao processo berço de alumínio refrigerado tira o produto do molde e coloca no berço.
– Injetando cremalheira, depois do processo de injeção colocávamos em dispositivos para evitar o empenhamento.
– Já trabalhei com dispositivo de alumínio refrigerado com água gelada, ficava de acordo com desenho.
-Sim eu também, para reduzir o tempo de ciclo.
– Meu caso era manter produto em desenho para montar em contra peça e fazer solda ultrassom.
Autor – Qual foi o matéria-prima que injetou? Autor – PA 6 20% FV.
– Tenta arrumar uma espécie de gabarito, fazendo rodízio, tirando os mais “frios”.
– Para quem não sabe o recalque é usado para compactação, tirando o recalque vai descompactar aí não vai gerar pressão na cavidade, porém sem compactação não cria empenamento já tive problemas com PBT de empenamento por compactação.
– Injeta com menos recalque para descompactar a peça.
– Inicialmente tem que fazer balanceamento dos canais, para obter uma pressão homogênea. Após trabalhar com a refrigeração, colocar água quente no lado convexo, e no lado cônico gelada.
– Usaria água quente no lado dos dentes, e água gelada no lado liso, assim forçando a contração do material para o lado oposto ao empeno atual.
– Dá para fazer um conformador para usar depois de injetado.
– Fazendo estudo de ” Flow análise módulo warpage”
A) Reduza a post de contração da peça fora do molde com o tempo e a pressão do recalque.
B) Experimentar diferentes temperaturas de molde entre a parte fixa e móvel, a fim de criar um delta de temperatura entre a parte fixa / móvel do molde.
C) Verifique se o tempo de resfriamento é compatível com a espessura da peça. Ps. Lembre-se que o melhor resfriamento da peça moldada ocorre durante o tempo e pressão do recalque.
– Pode tentar colocar carga na poliamida para manter o dimensional e evitar empenamento como talco, fibra ou outras cargas para manter as medidas ou tentar o berço dispositivo refrigerado, segurando um pouco mais no recalque e ciclo de injeção
– Detectar os pontos de injeção através de simulação CAE.
– Já pensou em aumentar o tempo de cura água aquecida na parte fixa gelada na parte móvel e descansar em um berço com água gelada aí você obterá um resultado significativo.
– Se não quiser perder tempo no ciclo deve fazer um dispositivo para o resfriamento da peça após ser injetado.
– Dispositivo para travar a posição ao ser extraído e mergulhar em água.
– Ou usar um conformador externo.
– Mais tempo de refrigeração e água mais fria no lado dos dentes.
– Deixa a peça cair na água.
– Mais refrigeração.
– Já pensou em trabalhar com mais fibra, vai segurar mais a contração após moldagem!
– Reparei que o P.A. é sobre injetado em uma barra roscada, o dispositivo que alguns amigos sugeriram vai ser essencial, mais tente diminuir a pressão e velocidade, segure um pouco mais no recalque, e aumente o tempo se resfriamento.
– Só vai tirar o empenamento com resfriamento, mas isso vai te deixar com pouca produtividade, a ideia de um gabarito é a melhor, pode até ser na frente de um ventilador.
– Deve se seguir o seguinte tem que diminuir.
– A temperatura do canhão mantendo o ponto de fusão do polímero.
– Temperatura do molde pressão de injeção.
– Pressão de recalque, aumentar.
– O tempo de resfriamento do molde.
– E o índice de fluidez do material.
– Necessário sempre a peça cair em uma banheira de água fria, de preferência com serpentina, ligado a água do chiller para manter essa água em temperatura baixa.
– Caso o mesmo continuar com empenamento observar os pontos de extração, pois o empenamento pode ser causado no acionamento do mesmo.
– Como é o sistema de injeção? Quantas entradas? Qual a posição da (s) entrada (s)?
– Isso deve ser ciclo rápido.
– Pouco tempo de arrefecimento.
– Quando fizer a extração, tenha um recipiente com água fria e deixa as peças na água.
– Troque a água a cada duas horas.
– Vai melhorar se aumentar o tempo de ciclo não for possível.
– Verifica a refrigeração do molde.
– Compacta bem a peça.
– Mais refrigeração do lado dos dentes.
Marcas de estrias no diâmetro externo
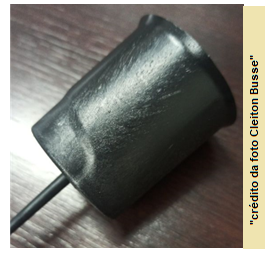
Problema: Marcas de estrias. Material PA66 sem fibra.
Comentários:
– Provavelmente umidade no material.
– Pode ser diversas coisas. Entre elas umidade na matéria prima.
– Neste caso amigo pode ser contaminação no Material ou umidade excessiva.
– Quase certeza que é umidade.
Autor – Então, o material ficou na estufa por 12h em 115°C.
– Então não é umidade se a estufa estiver tudo certo.
– Porque esse tempo é para ficar perfeito as peças em razão de umidade.
– Pode ser contaminação.
– Umidade, coloca o material 4 horas no desumidificador a 80 graus e depois pode injetar.
– Esta matéria está com umidade, para transformar uma poliamida reciclada necessário tempo de secagem de 5 horas a 100 graus.
– Pode ser umidade e temperatura elevada.
– Umidade na matéria prima ou contaminação.
– Observação, para cor preta 100 graus natural não pode exceder 80 graus para secagem.
– Gás, umidade, temperatura.
– Fazer umas 4 horas de estufa com uma temperatura de 85 graus.
– Não deixar degradar no canhão, limpeza do molde na saída de gases.
– Três possíveis causas!! Umidade na matéria prima, material degradado, gás.
– Pode ser o pigmento, não sendo de mesmo veículo ou úmido.
– Tem vários fatores que ocasionam isso, umidade, saída de ar do molde, velocidade de injeção alta, e temperatura.
– Até pode ser a contra pressão degradando o material e alta velocidade de injeção.
– Umidade no material, muita descompressão, molde muito gelado.
– Veja se está tendo vazamento na refrigeração na entrada da zona de alimentação.
– Verifique primeiro se o material não vem com umidade e se a temperatura não está muito alta, se não resolver, aumente o tempo de injeção e diminua velocidade de injeção.
– A descompressão traseira alta, também causa esse problema, mas o principal é a ideia.
– Se estufou o material e o mesmo ficou com no máximo 0.02% de umidade e a peça ainda está manchando a umidade está ocorrendo dentro do canhão…Isso significa que a refrigeração do pé da rosca pode estar vazando internamente. Caso não seja vazamento o material está úmido.
– Lembre-se que a água evapora à 90 graus e a temperatura do canhão está a 280 aproximadamente, neste o vapor queima e mancha a peça. Não propriamente a água está manchando.
– Acho que estudar neste caso não está resolvendo, então sugiro, ter um funil alimentador, na máquina, com secador. Ficando ligado e mantendo uma temperatura constante em 110 graus. Esse funil secador com ventilação forçada, serve para secar e desumidificar o material, eliminando a umidade.
– Se for reciclado não terá um bom resultado na injeção, estes materiais não são de boa procedência.
– Já identificaram corretamente o que deve estar acontecendo com seu produto, parece ser umidade, onde a Poliamida deve ser estudado por 3 horas a 100 graus (tudo isso é relativo, podendo ser um pouco mais ou menos), mas também pode ser material queimado, dependendo da fonte que se compra pode ser contaminação de outras matérias primas que não se compatibilizam com a Poliamida.
– Estufar a 120 graus por 3 horas. E trabalhar com a velocidade de injeção baixa.
– Umidade no material, se a máquina não tiver funil estufa, precisa abastecê-la aos poucos, descompressão muito alta também influência.
– Verifique primeiro se o material não está úmido e se a temperatura não está muito alta, mude velocidade de injeção.
– Descarregue o canhão, se sair material com bolhas é umidade é só estufar o material, se sair lizo está bom, aí pode ser degradação queima.
– Umidade, temperatura alta, material contaminado. Pode ser qualquer um destes fatores. Elimine por etapas os possíveis fatores.
– Provável queima de material ou material mal estufado…se for virgem põe em 110 graus por 3 horas.se não for virgem pode ser contaminação.
– Nem sempre se for material reciclado com umidade é melhor usar com dessecante porque no aglutinador vai gastar mais energia.
– Manchas de umidade, tem que secar a vácuo.
– Tem que estufar este material é igual ABS da estria colocar na estufa.
– Umidade deixa em estufa o material.
– Aparentemente é material úmido, faça um teste, descarregue um pouco se fizer fumaça muito espessa com certeza é umidade, precisa estufar esse material antes de processa-lo, nylon absorve muita umidade.
– Esse material por si só já não fica com aspecto bom, devido à alta concentração de fibra, porém há uma quebra brusca de fluxo considerando a distância do gate, o correto é escalonar essa velocidade, no intuito de fazer o fluxo de material ser mais uniforme.
– Pelo aspecto prateado tem cara de umidade.
– Material parece ter contaminante pelas marcas de fluxo.
– Para checar se é umidade quebre a peça e veja se tem bolhas.
– Deixa umas 6 horas na estufa, diminui um pouco a temperatura, agora se alimenta a máquina com alimentação automática, experimenta jogar o material direto no funil isso se puxa ele depois de seco.
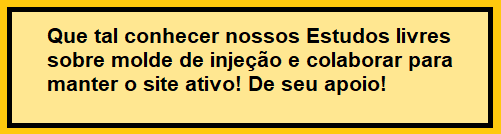
Aparência de manchas de umidade na peça
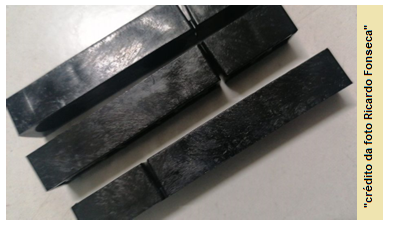
Problema: Manchas nas superfícies da peça. Teste de molde. Material PA6
Comentários:
– Pode ser mal estufado, verifica se não há umidade na estufagem dos grânulos, temperatura do molde, são alguns itens que podem auxiliar.
– Umidade do material.
– Se sua peça for maciça, é o que parece, vai ser difícil eliminar, mesmo com molde quente e material bem desumidificado.
– Temperatura alta , tirar um pouco a descompressão.
– Exatamente. Por ser uma peça com um bom volume de injeção e parede grossa, provavelmente o ciclo está bem alto, aumentando o tempo de residência do material. Está degradando.
– Material frio.
– Temperatura de massa e de molde, além de secagem.
– Põe o material pra desumidificar a 80 graus.
– Chegou a estufar este material? Se sim quantos graus e por quantas horas?
– Está com cara de material mal estufado.
Autor – estou a trabalhar acima dos 220º.
– Umidade.
– Já tive muitos problemas com esse material, tem que estar bem seco, deixa a sua descompressão o mais baixo possível, a temperatura vc pode trabalhar sem medo com um pouco mais alta, e aumenta a contra-pressão para ter melhor homogeneização, vai resolver seu problema, tem que observar com a descompressão baixa verificar a borra no bico.
Autor – acabei por melhorar bastante a qualidade da peça.
– O material ainda estava úmido,pois o tempo qe tinha colocado a estufar não tinha sido o suficiente.
– Primeiro verifique se seu material está com umidade!
– O PA tem que estar na temperatura de 240graus e menos descompressão pois provoca essa umidade ,ou se não melhorar pode está degradando devido alta temperatura também.
– Levar em conta se seu material é virgem ou recuperado.
– Tem que secar, certeza.
– À primeira vista todos concordamos que parece ser umidade. Caso já tenha verificado isso, sugiro avaliar a sua temperatura de processo.
– Entenda que vc tem uma peça de parede muito grossa, que demanda um tempo de ciclo muito alto. O que consequentemente aumenta o tempo de residência do material. É bem provável que o nylon esteja degradando. Sugiro trabalhar com temperaturas menores.
– Verifique a manutenção do desumidificador, troca da sílica e melhore a secagem.
– Umidade, temperatura da massa e do molde.
– Ainda vale lembrar da saída de gases no molde, na superfície da linha de fechamento e tentar injetar com baixa velocidade no início do preenchimento da cavidade e aumentar bruscamente depois.
– Isto é umidade ou material contaminado.
– Acredito que seja umidade, fora essas manchas a umidade apresenta purga com material “espumando” ou purgando pelo bico. Desumidificador com dupla torre de 80°C a 120°C; minimo 4h (mas é interessante verificar no datasheet a recomendação do fabricante).
– Parece que o material ainda esta com umidade, meter o material em um secador a 80° por 4horas no minimo e use um aquecedor de agua para o molde com a agua entre os 90° a 100°, com isto tudo tentar injectar o material no molde o mais rapido possivel.
– Já tentou aquecer o molde por água quente, ajuda a eliminar essas fibras.
Superfície com manchas escuras
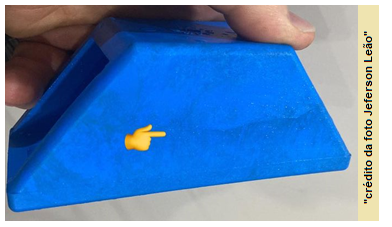
Problema: Manchas escuras na peça. Material PA66 50%FV, 2% pigmento e 5% anti-uv.
Comentários:
– Acredito ser a FV que causa estás manchas, pois você só tem metade de polímero para gerar um acabamento melhor.
Autor – Realmente pelo teor de fibra acaba tendo um acabamento ruim, mas no caso e como se estivesse queimando e as marcas mais escuras realmente é nas emendas do material.
– Então verificar a procedência do master, se é compatível, e o quanto de temperatura suporta o agente.
– Na verdade, só tem 43 % de polímero, estou achando que a quantidade de UV está muito elevada.
Autor – concordo, cliente pediu 5%, pois segundo ele seria compatível para 5 anos, farei o teste com menor percentual.
– Está estufando o material? Se sim, qual temperatura?
Autor – 6 horas 100 graus e a estufa continua ligada enquanto estamos injetando, to achando que pode ser o anti UV que queima e fica daquela forma.
– Veja como fica à 150/160 graus por mais 1h.
– Já aconteceu essas manchas antes? Também pode ser questão de alguma umidade na composição do material.
Autor – Acaba amarelando o material e alterando a tonalidade azul que o cliente quer.
– Pode melhorar com ciclo rápido, esses aditivos degradam fácil e a temperatura do PA6 já é alta.
Autor – a peça exige ciclo de 90 segundos para dar contração que o cliente quer.
– Baixa o tempo de ciclo e põe a peça à sair da máquina para uma caixa com água.
Autor – A peça tem um furo quadrado no qual vai em um tubo, tenho quatro pedaços de 60 cm e conforme sai a peça ela vai direto nesse tubo para resfriar dentro de água fria já no tubo. Cada um desses vai 5 peças. Se baixar o ciclo a peça trava no tubo e não sai e também o cliente não conseguirá montar.
– Temperatura de molde manter entre 60 e 80 °.
Autor – Está em 70 graus.
– Ok, em função da fibra está travando a massa, tenta aquecer mais o molde.
Autor – Farei o teste.
– Você está injetando vidro com 50% de polímero, espero que tenhas incluído o custo.
Autor – Bem isso, acaba com o canhão e rosca da máquina.
– Primeiro, o Master que está usando é masterizado com PA, também. E se misturar o Master e deixa estufar por no mínimo de 4 a 90 a 100 graus os dois.
Autor – Correto.
– Com essa quantidade de fv você precisa injetar com maior velocidade para o PA dar o acabamento liso, estufar no mínimo 4 horas. Já fiz try out com esse mesmo material e dá um certo trabalho para deixar o aspecto liso.
Autor – Farei o teste com velocidade de injeção mais alta.
– Se for molde com Câmara Quente, aposto que tem material degradado dentro do sistema. Aí, esse material degradado migra para as cavidades ocasionando essas manchas.
– Sugestão:
– Antes de guardar o molde, passar um material sem fibra (com molde aberto, papelão, etc).
– Esse procedimento limpa os canais internos, tira as fibras que ficam incrustadas e facilita o início processo de injeção.
Autor – Molde não é de câmara quente.
Tenta deixar o material do colchão abaixo do ponto de fusão do PA66, pode ser emenda também, bom conferir o material fora da moldagem pra ver se pode ser contaminação.
Autor -Vamos testar.
Tem que aquecer o molde para a resina (nylon que está “sem” a fibra) ir para as paredes e dar o acabamento. Mas não vai eliminar 100%, está com 50% de fibra de vidro.
Autor – Está certíssimo.
– É gás, ou emenda de material, as vezes fazendo saída de gás resolve.
Autor – O molde tem bastante saída de gás podemos ver se fazemos mais.
As manchas escuras é pigmento mal dissolvido e o esbranquiçado e a fibra de vidro, sugestão, aumentar a temperatura, velocidade de injeção mais alta colchão de recalque com pressão mais alta no recalque, dessa forma não tenho problema.
Autor – Vamos testar.
Houve um comentário acima que acho ser o mais provável. Conferir se o master é para PA e ponto de fusão do uv se são compatíveis, o restante ajusta no processo.
Autor – Acho que pode ser muita temperatura e tempo no canhão para o anti uv.
– Aumenta a temperatura da unidade de injeção…não sei quanto está usando… vê a especificação máxima…e programa…vai melhorar.
Autor – Farei o teste.
Nunca vai tirar, está injetando vidro e cuidado com a rosca, vida curta.
Autor – A rosca tem vida útil curta com este material certo.
-O custo hora aumenta muito. trabalho com PA / FV a mais de 20 anos, aprendi errando muito.
– Esse material é difícil injetar, mas a degradação de pigmento e UV, me parece ser o mais provável, depois comenta aí conosco para conhecimento nosso também.
– Mas tem que usar o pigmento com a mesma base.
– Sim, o que entendi é que a base do pigmento possa ser a base de outro material, mais sensível a temperatura.
– Aquece o Molde. Coloque temperatura de 140 graus.
– Água pressurizada ou óleo. Seu problema será resolvido.
– As manchas de fibras, me parece que sairiam esbranquiçadas, pela foto me parece não ser o caso.
– Qual material estava antes se for preto pode do material tenta passar o nylon natural se sair da a limpeza da rosa com material de limpeza.
– Acertar master é muito difícil.
– Está usando pigmento próprio para nylon? Qual tempo de residência do material dentro do cilindro? Se o tempo de residência for alto, tem que tentar compensar diminuído um pouco as temperaturas na zona próximo ao funil.
– Considerando a % de fibra, é bom verificar os tamanhos dos pontos de entrada de material nas cavidades, caso estejam pequenos demais, também geram degradações do composto.
– Aumenta a temperatura de estufagem para 120 graus, se não for manchas de queimas e não for molde com câmara quente deixa um colchão maior para aumentar um pouco o tempo de residência, aumenta um pouco a pressão de injeção e velocidade também injetando bem rápido.
– Pode fazer um teste, saída de gás, retire minimamente o fechamento do molde, se melhorar providenciar saídas de gás.
Autor – 100 graus 6 horas.
– Provável causa. Junção.
– Solução: aquecer da cavidade, lado que tiver acontecendo o problema temperatura de 30 a 45•c.
– Pode ser o pigmento que está usando. Se for a base de pead vai queimar mesmo.
Autor – Pigmento e anti uv próprio para nylon.
– Poder ser muita velocidade de injeção, anel de bloqueio gasto.
Autor – Velocidade está em 50%. Farei testes com outras velocidades.
– Bico muito fino também pode aumentar a velocidade de saída do material e queimar.
– Quando solta borra fica com o mesmo aspecto? Se sim, pode ser homogeneização do material, já tentou um retardo na dosagem? Tenta dosar no tempo final do resfriamento.
Autor – Tentei sim. Faremos o teste assim que possível sem o aditivo anti uv para ver como ficará. Borra também fica com essas marcas escuras.
– Se for emenda aumentar a velocidade pra ver se diminui.
Autor – Vamos tentar.
– Muda a injeção.
Peça aderindo e quebradiça
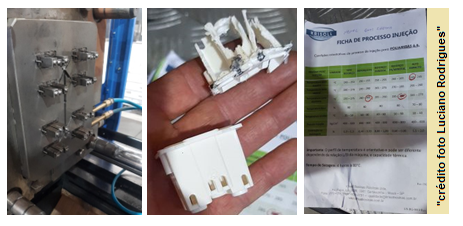
Problema: depois de fazer algumas peças o material começa a grudar no molde e fica quebradiços.
O começo sai bem… depois ele gruda no molde faz até barulho da peça saindo do postiço e se deixar até quebra a peça no molde. Usando água da torre somente na parte móvel. Material nylon com aditivo anti-chama estufado mais de 4 h a 80 graus. Temperatura do canhão com 270/280.
Comentários:
– É necessário diminuir mais a temperatura do lado do molde onde o Nylon está prendendo, talvez precise usar água gelada nestes pontos de retenção.
– Precisa de geladeira.
– Qual ciclo? Diminuindo o tempo de resfriamento pode melhorar, o molde aquece e a peça contrai menos no macho.
Autor – Uns 30s e tempo 12s de resfriamento.
– Pelo tamanho da peça parece ser muito, quanto mais tempo a peça resfria dentro do molde mais ela prende.
Autor – Não temos água aquecida, vou desligar refrigeração e diminuir tempo resfriamento.
– Tudo é tentativa em injeção, muitas vezes a pratica não corresponde com a teoria, fazer experimentos é o que vai direcionando a melhor performance do processo, muitas vezes tem que sacrificar o processo em detrimento a alguma falha no projeto do molde. Exemplo as paredes com pouca saída de extração, etc…
Autor – Vou tentar fazer isso.
– Olha no início da injeção a temperatura do molde e quando começa a quebrar a temperatura.
Autor – Não tenho como medir a temperatura. Sim, vou pedir para comprar e um aquecedor de água, só temos água gelada e o da torre.
– Tem que ver o tempo de resfriamento e a temperatura da água, pode tentar usar água industrial que seria um teste, as vezes o molde não está na temperatura ideal para a injeção.
Autor – Penso que o molde tá muito frio. Não tenho nada para medir temperatura do molde. Vou desliga a água e diminuir o resfriamento para ver.
– Pode fazer um teste, fecha a água deixa trabalhando por um tempo, eu tive um problema em um molde assim, era água gelada. E ele começava numa boa depois que abria a água ele começa a ranger na hora da extração, aí mudei para água industrial e ficou show.
Autor – Vou fazer isso.
– Diminua a temperatura, eu uso em torno de 230 graus. Diminua a compactação, muita compactação faz o nylon agarrar no macho.
– Exatamente….
– Pode aumentar um pouco esta temperatura de estufagem também de 90 a 100 graus.
– E diminuir a temperatura entre 250 a 270 graus, considerando que é um PA 66.
– Trabalhe com o molde em torno de 30 a 40 graus.
– O problema é na refrigeração.
– E se possível.
– Rever a possibilidade de pequenas retenções no molde na parte móvel, para que a aderência fiquei menor na matriz.
– Pode tentar usar água aquecida no molde com temperatura variando de 60 a 80 graus, pode ser que resolva.
– É necessário diminuir mais a temperatura do lado do molde onde o Nylon está prendendo, talvez precise usar água gelada nestes pontos de retenção.
– Polimento do lado fixo, tem ser bem feita ou banhado cromo.
– Esse tipo produto e ver retenção lado móvel.
– Aqueça o molde a 70 graus.
– Nylon não se refrigera, tem que ter velocidade na injeção, e descolorante….
– Diminui a dosagem. Coloca o molde em uma máquina de cilindro de aquecimento menor. O tempo de residência do material no cilindro pode estar muito alto e degrada o material no cilindro.
– Dependendo do tipo de material dá uma olhada também no colchão que sobra no canhão…as vezes está sobrando material para injetar outra peça, aí pode ocorrer degradação do mesmo…
– Para as resinas poliamidas(nylon) não há a necessidade de refrigeração.
– Diminuía a refrigeração do molde.
– Tenta baixar o ciclo.
– Talvez a peça esteja contraindo demais no macho.
– Pelo que vi na foto, tem 1 entrada e 1 saída para todos os machos, precisa melhorar a refrigeração, depois de uns ciclos o molde está aquecendo e a refrigeração está insuficiente.
– Precisa de geladeira.
– Melhor sugestão é pegar o datasheet da matéria utilizada e inserir os dados de temperatura do molde, residência do material e demais informações no processo da máquina. Ao molde fundamental o polimento das cavidades, ajuste das matrizes evitando rebarbas, pinos extratores dimensionados e ajustados.
– O material está degradando na câmara quente.
Bolhas de ar no interior da peça – Material PA6
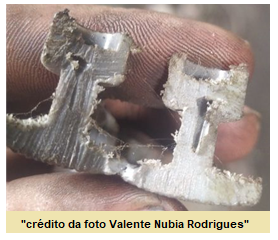
Auto – Bolha de ar no interior da peça.
Comentários:
– Aumentar a contrapressão, caso esteja trabalhando com bico valvulado.
– Ver quantos graus está a estufagem da matéria prima.
– Pode ser resina mal estufada.
– Temperatura mais baixa possivel,velocidade de injeção também,usa um perfil de injeção iniciando baixo e aumentando do meio ao final,e na descompresão traseira um minímo possivel,isso ja vai ajuda a evita essas bolhas.
– Umidade.
– Temperatura do cilindro muito alta.
– Pouco recalque.
– Contrapressão.
– Verificar o colchão.
– Até mesmo , faltando saída de gás no molde.
– Saída de gás ajuda bem.
– Temperatura padrão dosagem suave +- 60% injeção lenta de início depois rápido.
– Bolhas podem ser causadas por umidade, turbulência, falta de saída de gases, falta de recalque gate muito restrito também porque o canal resfria antes do recalque.
– Reduzir velocidade de injeção será o mais indicado, mais para isso tem que aumenta um pouco a temperatura do canhão para o material pegar mais fluidez.
– Aumenta a contrapressão. E vai aumentando o tempo de injeção até q suma a bolha.
– Tente recalquar mais, com tempo e pressão uma velocidade de injeção um pouco mais alta no final.
– Tem que ver também, se está bem estufado o material.
– Saida de gàs.
– Limpeza de saída de gás e observar o recalque e colchão…diminua um pouco a pressão do recalque vá completando a peça aos poucos até estabilizar processo….fique de olho no desumidificador da matéria prima…,mas aí é sua avaliação é que vale…se já existe um processo baseado a um tempo razoável em ficha técnica de engenharia.
– Fora a melhoria em molde…. Compra um Material de melhor qualidade…. Tipo Celanese, Dupont e Basf…. são mais caro, mas não acontece esse tipo de problema.
– Essa bolha é devido ao excesso de massa. Como as paredes esfriam, o material sofre a contração internamente gerando vazios internos. Saídas de gases vão ajudar, mas nesse caso sugiro colocar o gate com 2/3 da espessura da parede onde está localizado e um estudo de recalque aumentando tempo e pressão e conferindo o peso da peça. Até atingir o peso máximo. Acredito que 70 bar por 8 seg pode ajudar. Reduz o resfriamento para compensar o ciclo.
– Importante que tenha um colchão minimo de 10 mm estável. Ou mudar a geometria da peça que aparenta ter 8 mm de espessura nesse ponto.
– Recalque ajuda.
– Aumenta a saida de gás coloca água quente na parte da fêmea do molde ok.
– Correto tudo certo.
– Faça uma bolsa na linha de saída de gás.
– Melhorar a saída de gás, aquecer parte móvel, pode ser velocidade alta de inj. – Temperatura da m.p no cilo, temp. da m.p no cilindro, aumenta um pouco a pressão, inicia com uma velocidade média e aumenta um pouco no final, se não desaparecer aliviar massa nessa região do molde.
– Obs, fazer saida de gás, tipo bolsa no canal secundário de injeção o mais perto possível da cavidade.
– Injeta com velocidade baixa.
Você colocou os grãos na estufa. Vai aumentando. temperatura devagar.
– Tem que estufar bem.
– Diminui a velocidade de injeção, caso a descompressão estiver após a dosagem, muda para após o resfriamento. Limpa as saídas de gases e faz um teste. Caso a peça falhe devido a diminuição da velocidade, pode aumentar a pressão ou rever a posição de injeção para completar a peça.
– É um problema novo ou já ocorria? Se for novo tenta rastrear possíveis alterações como matéria prima ou parâmetros.
– Está utilizando recalque?
– Estufar melhor o material.
– Se está bem estufado, rpm da rosca pode estar muito alta ou a descompressão está muito alta, nylon o certo seria bico valvulado e para zerar a descompressão e aumentar um pouco a contrapressão.
– Estufar bem o material e injetar mais rápido e com recalque para zerar a bolha.
– E fazer saída de gás no molde.
– Duas situaçoes possiveis umidade ou injeçao muito rápida verifique seu anel de bloqueio, também.
– Na dosagem usar contrapressão, isso evita acúmulo de gás na rosca.
– Velocidade de injeção baixa.
– Saída de gás eficiente.
– Fazer bolsa pós cavidade e saída de gás.
– Mais recalque (pressão e/ou tempo), um pouco menos de temperatura na massa e no molde, ajustar o preenchimento para 99% na comutação.
– As vezes a única saída é aliviar o excesso de massa no design do produto.
– Usar uma poliamida 6 com aditivo de ciclo rápido e estufar bem ou usar a PA 6 da BASF B27.
– Pode ser uma variável na contrapressão.
– Ou então fazer um poço frio, mas geralmente aumenta o custo do produto, tem que analisar para ver se é viável.
– Provavelmente temperatura a mais… O nylon até a frio é possível dosear dependendo da velocidade de dosagem que estiver a usar.
– Mais recalque e menos velocidade de injeção.
– Regular contrapressão. – Compactar mais. – Faz saída de gás.
– Contrapressão e velocidade de dosagem mais baixas deve se ajudar e muito.
– Se for uma peça grossa velocidade de injeçao mais lenta ajuda.
– Pode ser umidade no material.
– Tem que aquecer o molde com ole óleo quente com oitenta 80 ºCpara o nylon corre mais fácil ,fazer uma saída de ar no molde.
– Está resfriando o molde muito rápido.
– A temperatura de recristalização da PA é alta, então trabalhe com o molde mais quente e procure usar tempo de injeção bem baixo, em torno de 0.5 seg a 1 seg…Como disse, como a PA recristaliza a temperaturas altas se injetar lento a pressão de recalque não será transferida pois a massa já estará solidificada resultando apenas em excesso de rebarbas…então…
– Suba a temperatura do molde.
– Aumente a velocidade de injeção.
– Opere no terceiro quartil da temperatura da massa.
– E por último aumente o recalque.
– Além, é claro de combinar as valiosas dicas de saída de gases, porque ao subir a temperatura e aumentar a velocidade de injeção seguramente irá dar marcas de queima de gases ( efeito diesel)… eu sempre costuma fazer saída de gases na eletroerosão nesta peça ai, penso que seguindo em todo perímetro de fechamento 1 a cada 8mm de distância tendo 2mm de largura e máximo 0.015mm de espessura…precisa ser na erosão se fizer na mão vai dar rebarba pois a PA é altamente fluída…
– Parece bolha de contração, tente usar recalque, baixar temperatura do material, ou então usar nylon com carga mineral ou fivra de vidro.
– Aumente a saída de ar e meta bronca.
– Aumenta o tempo de recalque.
– Saida de gás e aumente o recalque.
– Temperatura, saída de gás e talvez velocidade de injeção,podem ajudar .
– Primeiro passo é saber se o seu conjunto de plastificação é apropriado para nylon… Sem isso, não tem regulagem que vá lhe ajudar…
– Olha lá na contrapressão.
– Veja também as saídas de gases no molde.
– Nylon tem que ser desumidificado. Não basta estufar ou secar.
– Segurar mais no recalque para solidificar mais o interno da peça.
– Me parece bolha de contração, tente aumentar tempo e pressão de recalque.
– Vê temperatura do material se ta ideal ou a velocidade da pressão muito alta.
– Velocidade baixa, aumentar o colchão, recalque.
Marcas do tipo rajado nas peças – Material PA
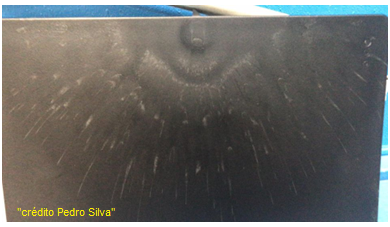
Autor – Marcas do tipo rajado nas peças. Material PA com fibra
Comentários:
Verifique o teor de umidade do material. Geralmente os PA precisam estar abaixo de 0,10 para ter um bom processamento. Pode verificar também temperatura do cilindro, temperatura de câmara quente se houver, velocidade de injeção e temperatura da água circulando no molde.
Como faço para medir o teor de umidade?
Existe um equipamento para medir, geralmente fica na metrologia, mais não são todas empresas que tem esse equipamento.
Porém uma característica de material com alto índice de umidade é o aspecto esponjoso durante a purga. Se seu material estiver assim, seria recomendado a máquina ficar parada estudando material por no mínimo 4 horas.
Autor – A umidade está ok abaixo 0,1.
O molde está aquecido também?
Autor – Sim está
É início de produção ou já produziu alguma coisa.
Autor – Faz sempre no início de produção durante as primeiras horas e depois o riscado desaparece, mas as marcas rugosas no local do jito nunca desaparece.
Autor – Para mim o problema, defeito estar no molde.
Autor – O ponto de injeção devia ser no centro da tábua de cozinha e não no local que está.
De fato, em peças com essa geometria o ponto de injeção ideal é no centro, mas infelizmente nem sempre se faz um estudo antes do desenvolvimento.
Agora sobra para a equipe do processo tentar “consertar” isso.
Em todos os casos o ideal é ter acesso a ficha técnica do material. Para assim conseguir determinar os parâmetros ideias do seu processo.
Pode ser que a carga de fibra de vidro seja maior do que o polímero PA e a cor também influi no aspecto.
Típico de umidade e temperatura alta, a fibra está aflorando.
A que temperatura está o canhão? Aumenta a temperatura e aumenta a velocidade de injeção. Para mim o material está entrando muito devagar e arrefece muito rápido nesses pontos.
Se a máquina for Haitian no canhão tenta colocar bico 265 ºC, 255 ºC, 260 ºC, 245 ºC e 235 ºC. As vezes achamos que o PA precisa de temperaturas muito altas mais isso queima tanto que a peça sai aflorada já trabalhei com PA6, PBT, PVC, AC.
ABS e PET, esses se não estiver bem seco estufados, é problema.
Abaixa um pouco a velocidade de injeção, e diminui o recalque.
Pode ser a velocidade de injeção “colchão” ou material.
Queima (redução de pressão e velocidade de injeção / redução das temperaturas do forno).
Contaminação (sem solução).
Estufar e também baixar temperatura canhão.
Material úmido. Coloca estufar por 5 h.
Muita umidade e deformação por temperatura excedente e talvez já tenha degradado o material. Mancha de umidade. Tem que estufar o material;
Estufou o material antes de usar? se não, tente estufar a 80 ºC a 90ºC por umas 6 h.
Umidade no material precisa estufar a 90 ºC por duas a três horas.
Parece ser umidade no material, tem que verificar se a estufagem está sendo suficiente.
Autor – Duas estufas ao mesmo tempo, estufando a matéria prima.
Manchas brancas espalhadas – Material PA 6.6

Autor – Manchas brancas espalhadas. Material nylon 6.6 com 30% fibra vidro.
Comentários:
Por conta da carga de fibra.
Equipamento:
Antes de tudo é necessário saber se as zonas de aquecimento estão funcionando corretamente. Verifique se não há resistência sem funcionar. Certifique-se que as temperaturas indicadas estão certas.
Importante saber também se ao injetar o material não está retornando devido a desgaste no anel de retenção da rosca.
Processo:
Estando o equipamento em ordem o problema pode estar sendo ocasionado pelo afloramento da fibra de vidro. A solução é aumentar a temperatura do canhão tornando o material mais fluído, daí a importância de o equipamento estar aquecendo perfeitamente.
Outra providência é aumentar a pressão e o tempo de recalque. Esta etapa vai fazer com que a poliamida, mais fluida em virtude do aumento da temperatura, seja pressionada contra a parede do molde e não retorne até que o resfriamento esteja concluído, dando a peça moldada o acabamento desejado. Por isto é importante saber se não está retornando material quando este é injetado no molde.
Tenta aumentar a velocidade de injeção e aquecer o molde.
Aquecendo o molde pode ajudar, trabalhamos com algumas peças de nylon e aquecemos os moldes de 70 ºC a 80 ºC.
Umidade, necessita de melhor secagem.
Princípio de degradação térmica, geralmente devido à temperatura do bico alta demais (injetora / molde) influenciada pela umidade (hidrolise).
Autor – Qual temperatura ideal? Estou com 240 ºC na alimentação, 250 ºC na homogeneização e 280 ºC no bico.
Difícil dizer a temperatura ideal; teoricamente para PA 6.6 com 30% de FV a temperatura de plastificação está até baixa.
Teria que verificar o diâmetro do furo da bucha e deixar o diâmetro do furo do bico 0,5 mm menor. Caso o furo seja muito restrito e o bico muito longo haverá necessidade de elevar a temperatura para poder injetar e consequentemente ocorrerá degradação agravada pela umidade.
O PA 6.6 com essa quantidade de fibra é um material muito chato de injetar peças que necessitem aspecto visual portanto deve-se ficar atento aos detalhes do processo para a injeção.
Estou trabalhando com esse material e usando 250 ºC de perfil, o material tem que estar estufado a 100 °C durante 3 horas. Essas manchas são de umidade e o molde tem que trabalhar com 80 °C, somente com água industrial.
Velocidade de dosagem não pode estar alta, pois pode aquecer material, a poliamida que é o Nylon 66 com 30% de fibra as vezes é reciclado.
Tenta assim: bico 260 ºC…homogeneização 250 ºC……..alimentação 250 ºC.
Umidade. Pode ser excesso de umidade ou temperatura muito baixa.
Aumenta tempo de residência do material, aumentando um pouco a rotação da rosca.
Diminui a velocidade de injeção e deixa mais no aquecimento o material, no mínimo 5 horas a 100 ºC para ver se melhora.
Verificar temperatura, velocidade da rosca e estufa. Parece umidade.
Verifique se o molde tem algum vazamento de água, se o material for virgem pode ser temperatura, mas se for material reciclado pode estar contaminado.
Manchas espalhadas na peça – Material PA6 15%.

Autor – Manchas diversas espalhadas por toda a peça
Comentários:
Material novo ou reciclado? Fibra de vidro ou carga mineral?
Estas manchas geralmente aparecem no material reciclado por motivo de umidade ou contaminação.
Se for material virgem falta estufar, agora se for moído pode ocorre risco de estar contaminado o material.
Não está trabalhando com temperatura muito alta da câmara quente ou tenha alguma zona do canhão de injeção que está sobre aquecendo, não.
Nylon com fibra dá essas manchas, acrescenta um nylon sem fibra fazendo outra porcentagem que chegara num resultado mais rápido.
Acrescenta um percentual de pa6 virgem que vai ajudar e ver a temperatura do cilindro se não está muito alta.
Material com umidade coloca na estufa da noite para o dia e vai ter um resultado bom. Estufar material, secar material. Tempo de secagem.
Material úmido. Parece que o material está úmido. Material está com umidade.
Umidade, precisa desumidificar com tempo e temperatura certa.
É bom sempre consultar o fornecedor do material para essas informações.
Material não está estufado. Parece ser mancha de umidade. Secar a matéria prima.
Autor – Material virgem, tempo de estufa 3 horas a 80°C.
Aumenta a temperatura para 90 ºC e estufa de 3 a 4 horas. Creio que resolva.
Pelo menos 3h de estufa a 80 °C. E na injeção temperatura de 240 ºC para cima, talvez possa ajudar. Tem duas possibilidades, ou o material está úmido ou é excesso de temperatura na programação, ou por atrito na dosagem.
4 horas a 80 °C resolve, como tem moído uma hora a mais no aquecedor.
Falta de estufagem 3h de 90 ºC a 100 ºC sem medo.
PA: 3 a 4 horas a 105 ºC.
Secagem 6h mínimo a 120 ⁰C se for mancha de umidade, gás também se gera pela umidade.
Se não for umidade, coloca água quente, se não resolver aumenta a contrapressão.
Marcas de umidade – Material PA / Nylon reciclado.
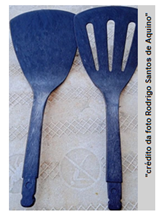
Autor- Injetando utensílios de cozinha. Peça saindo com rajados e quebradiça.
Material Nylon – não tem carga. Qual a temperatura ideal para trabalhar com nylon?
Comentários:
– Precisa desumidificar o nylon antes de injetar. Coloca no silo a uma temperatura de 100 ºC, de 3 a 4 horas. Se possível aferir a umidade após desumidificar, ideal que estivesse com menos de 0,20 %. Vai melhorar o processo e a tendência é desaparecer essas marcas de umidade.
– Igual PE no filme se está úmido raja tudo e fica tipo sem resistência.
– Para evitar a quebra, o correto seria deixar as peças 24 horas em água quente de preferência em 90 °C, mas creio que para essas peças não seria necessário.
– O material é novo ou reciclado, pois eu já coloquei material reciclado na máquina e estava contaminado. Pode ser isto aí, não tem o que fazer.
Autor – Material reciclado.
– Nylon ou poliamida por ser material hidroscópico e para se processar é necessário desumidificar por pelo menos 3 horas sendo virgem, e reciclado 4 horas a temperatura de secagem 80 ºC a 120 ºC. Após processamento é necessário hidratar as peças em um tanque com água aquecida de 50 ºC a 80 ºC por pelo menos 1 hora dependendo da espessura 4 horas. Temperatura de processo dependendo da característica da poliamida PA ciclo espessura varia entre 250 ºC a 280 ºC em perfil da menor para maior entre zonas.
– Qual PA e quanto de carga se houver? É preto ou azul a cor?
Autor – É preto reciclado sem carga.
– Material úmido tem que ser desumidificador.
– Quando disse que o desumidificador “suga” a umidade interior do material… é uma forma de explicar que existem diferença de “aquecer” o material através do secador e tirar a umidade do material pela interferência do desumidificador. O próprio nome já está dizendo desumidificador.
– Tem que estufar, e depois de injetado hidratar.
– Isso aí, primeiro retira a água (secagem) e depois repõe a água (hidratação por 2 a 8 horas, dependendo da espessura da peça, a 80 °C).
– Caso o PA não esteja degradado ou contaminado ficará flexível como um PEAD.
– Realmente estufar 4 horas e depois hidratar à 90 °C à 4 horas….
– Tem que ver temperatura de secagem e tempo. A temperatura de processo depende da matéria prima que se está usando se é 66 ou 6 com fibra sem fibra, virgem ou reciclado depois da injeção tem que dar um tempo de contração e fazer a hidratação das peças.
autor – Não tem carga.
– Deixa ele na estufa umas 2 horas a 80 ºC.
– Umidade, contaminação, material de baixa qualidade com muito moído ou temperatura errada ou tudo isso.
– Sem ter mais informações e/ou medições do processo a resposta vai ser genérica. Mas eu coloquei na ordem de importância.
– Colocar o material em estufa. – Pode ser temperatura excessiva
– Nylon 6 de 220 ºC a 230 ºC e Nylon 6.6 de 25 ºC a 260 ºC.
– Hidratar a peça com água quente.
– Pode ser a temperatura próximo a degradação.
– As poliamidas por serem altamente higroscópicas devem ser desumidificadas conforme data sheet do fornecedor. Processo também deve ter a ficha do fornecedor.
– Este material precisa estar bem desumidificado.
– Precisa estufar a 100 ºC por umas 3 horas, com temperatura a 248 ºC distribuída, se não funcionar sua matéria prima está comprometida com a qualidade, estufa com misturador central, evaporação da umidade.
– Acima de 240 ºC já se consegui trabalhar, o material tem que ser estufado entre 80 ºC e 90 ºC por 6 horas ou mais.
– Hidratar com temperatura de 60 ºC por 2 horas ajuda a não quebrar.
– Matéria prima pode estar contaminada, matéria prima pode estar úmida, 3 horas o mínimo para estufagem do material.
– 250 ºC a 290 ºC.
– Não deixar entrar umidade no material, temperaturas do cilindro 300 ºC a da garganta deixa em 80 ºC, verificar dosagem e contrapressão, contrapressão coloca em 100 bar a 1 passo e velocidade de dosagem baixa uns 230 ºC ou 170 ºC, aí você vai ter uma homogeneização melhor no momento de injetar.
– Com relação a quebra precisa hidratar a peça deixar na água.
– Estufar o material por 6 horas e baixar temperatura de processo para evitar degradação.
– Dependendo do material de duas a três horas.
– Manchas características de umidade do material.
– É preciso estufar material, está com umidade. Primeiro, precisa ver se é 6 ou 66, porém está com umidade devendo estufa mais, precisa ver também se o pigmento é para nylon.
– PA com fibra. Temperaturas baixas.
– Desumidifica o material durante umas 4 horas a 280 ºC as manchas vão sumir e sobre a peça quebradiça tem que ver se não há contaminação no material também são hipóteses.
– Desumidifica que para de quebrar e fica sem as manchas de unidade.
– Na verdade, o desumidificador tem que ser ligado ao Secador, o desumidificador faz com que o secador trabalhe com ar a circuito de fechado para alcançar o ponto de orvalho.
– (Tem sílica gel e peneira Molecular e tem sistema regenerativo).
– Mas dá para fazer isso no seu secador (fiz em vários), só vai dar trabalho, vai ter que direcionar o ar de saída para a entrada, e colocar uma válvula para reduzir ou abrir a entrada de ar (existe no mercado o nome é filtro reciclador de ar, no filtro coloque elementos de sílica gel (não duram muito pois não tem o processo regenerativo) se puder colocar um movimentador de material, um motor e uma rosca para que o material tenha o mesmo tempo de núcleo como da lateral de secagem e desumidificação.. se não quiser gastar com o desumidificar, isso é um paliativo.
– Funciona, mas sem precisão, isso vai depender o que a peça exige.
– Além de pré secar, injetar com NYLONFLEX HIGHTERM também ajuda.
– Para Nylon não pode ser usado Secador…Tem que ser Desumidificador…O Secador aquece o material e no núcleo continua a umidade. o Desumidificador “suga” a umidade e joga no ambiente.
– Material tem que ir para secador, uma estufa para tirar umidade, geralmente e isso e também injetando um pouco mais rápido.
– Avalie se esse master tem a base correta para nylon, outro ponto é a desumidificação do material.
– É necessário também aquecer o molde no mínimo a 90 ºC para o material fluir melhor.
– Pode ser umidade da matéria prima, a temperatura ideal 290 ºC, 280 ºC e 270 ºC.
– Depois de injetado hidratar na água quente.
– Estufa bem o material antes de injetar e depois coloca as peças para hidratar.
– Material contaminado e falta de desumidificar o Nylon.
– No mínimo 3 horas de estufa a pelo menos 90 °C e baixa a vazão de injeção.
– Se estufou bem o material pode ser contaminação o material é novo ou reciclado.
– Material pode estar úmido, porém pode está forçando a injeção também, se aumentar o fluxo de material vai ajudar.
– Nítido a umidade nas peças. – Sinal de umidade ou material contaminado.
– Deixa o material estufar no mínimo 4 horas – Pode ser umidade no material.
– Colocou material na estufa, temperatura dele 250 ºC a 280 ºC eu uso.
Excesso de bolhas – Material PA12
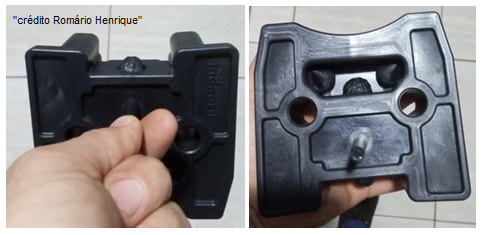
Autor – Injetando peça e se não colocar na água imediatamente ela estoura, as vezes até na água dá umas bolhas. Nylon 12 com 30% de fibra de vidro.
Comentários:
Qual água está utilizando quente ou industrial?
Coloca água gelada na parte móvel.
autor – Usando água temperatura em ambiente (torre de resfriamento).
Qual é o tempo resfriamento e ciclo da máquina.
Autor – Tive que deixar o tempo alto 90s e ciclo total deu 115 s.
Tentou compactar um pouco ela para ver se não vai romper ou aliviar
Qual a temperatura de processo?
Autor – 210°C a 230°C.
Está muito alta. Tente trabalhar na faixa de 200 ºC
Autor – Já abaixei a temperatura do cilindro.
– Aumentei a temperatura da estufa.
– Aumentei resfriamento.
– Aumentei tempo e pressão de recalque.
– Melhorou muito o resultado, porém ainda sai algumas peças estouradas.
– Cheguei a pensar que poderia ser umidade, só que o material estufou por 8 horas a 120 °C.
Provavelmente o material está contaminado.
Pode ser contaminação da matéria prima. Esse material é reprocessado? Se for, tem que abaixar a temperatura da massa e fazer testes com velocidade, pressão e resfriamento.
Autor – Material virgem, já aumentei o resfriamento, abaixei a temperatura e melhorou, mas não resolveu.
Qual o peso da peça e a espessura?
Autor – Peso em torno de 350 g e a espessura deve ter uns 12mm, ciclo está em 95 s.
Já tentou alimentar o ciclo para melhorar o resfriamento?
autor – Sim
Reduza a temperatura da Câmara quente se estiver usando.
Geralmente uso de 235 ºC a 255 °C.
Estufar o material por 4 horas de 70 ºC a 80 ° C.
O principal motivo que causa esse problema:
O aquecedor de água tem que estar em temperatura até 40 °C.
O resfriamento tem que estar mais alto por exemplo: se estiver com 30 segundos, coloca 45, se não melhorar vai aumentando.
Aquele problema ocorre devido a peça ter mais volume de material em determinados lados da peça. Não dá tempo do material se solidificar por completo e quando a peça é extraída o material ainda plastificado tende a buscar algum canto frágil para sair, como um vulcão prestes a entrar em erupção.
A peça é muito espessa, motivo de o material do núcleo estar muito quente. Então o principal é aumentar resfriamento, para garantir a estabilidade, se não tiver problema com manchas tenta água industrial no lado da extração.
Muita massa nesse produto, segurar um tempo maior na cavidade e conseguir um resfriamento para estruturar o externo, pois o núcleo estará muito quente.
Excesso de temperatura de matéria prima, pouco eficiência da refrigeração do molde e pouca compactação (recalque).
Compacta com recalque e dá mais tempo no resfriamento.
A causa principal é o baixo tempo de resfriamento, a peça apresenta grande espessura, e ao ser extraída o núcleo não está solidificado, e não se tendo a ferramenta para segurar a expansão térmica do material, o mesmo rompe de dentro para fora.
Independe de abaixar a temperatura da massa e aumentar o recalque, deverá aumentar o resfriamento.
Experimenta um tempo de recalque maior comparado a injeção, e escalona esse recalque, para ir mantendo o ponto de injeção aberto enquanto a parte externa da peça já vai se solidificando, o ponto de injeção vai se mantendo aberto e preenchendo a peça com pouca velocidade, vai manter a compactação, sem estufamento e sem estourar esse material para fora.
A sua peça necessita de mais tempo de refrigeração, pois ao cair na água a temperatura superficial da peça vai baixar e o material que ainda está fundido dentro da peça não vai reaquecer e como está sob pressão libertar-se nas zonas mais quentes da peça.
Se não for umidade pode ser que esteja saindo muito quente. Tenta injetar com mais tempo de injeção e menos fluxo. Se der faça um perfil de injeção em rampa.
Esse tipo de problema é temperatura alta, tempo de resfriamento é bom verificar como está a refrigeração do molde também.
Estufa o material umas 3 a 4 h e hidrata em água quente. Depois de injetado é sempre bom colocar em água quente umas 3 ou 4 horas de molho.
Pode aumentar o tempo de resfriamento, aumentar o recalque para compactar melhor, colocar um retardo na dosagem para ficar menos tempo no canhão, verifique o sistema de circulação de água no molde para ver se não está com pouca vazão de água.
já tentou várias alternativas de regulagem e não resolveu troca o material testando um novo lote.
O material ainda está fundido no interior da peça quando é extraída, como o tempo de resfriamento já está alto, abaixe a temperatura das zonas traseiras do canhão.
Manter mais tempo no molde, e aumentar o tempo de recalque e também a pressão de recalque
Solução: autor
O problema foi resolvido aumentando em 40s o tempo de resfriamento, deu certo, porém a peça ficou mais cara.
Acredito que o problema seja a matéria-prima utilizada (PA 12 30% FV), pois quando a peça é injetada com PA 6.6 30% de FV a peça sai perfeita. Como nunca tinha injetado este tipo de material pensei que pudesse estar fazendo algo errado, mas pelas dicas imagino que eu estava no caminho certo.
Marcas de esbranquiçado – Material PA66

Autor – Preciso de informações. Estou injetando o nylon 66 e acaba saindo esse esbranquiçado na peça. Máquina própria para nylon, não injetamos outro tipo de matéria prima nela. Material Nylon 66 com fibra fornecedor LANXESS.
Comentários:
Deve estar úmido, tem que secar bem o material. Material não deve ter sido estufado.
Se material estiver úmido tem que estufar. Isso com toda certeza e material úmido
Deve estar úmido, tem que secar bem o material.
Coloca o material numa estufa. Material com umidade
Umidade, ou contaminação. Pode ser sujeira no cilindro. Tem que ver o que foi injetado antes.
Está espirrada a peça. Pode ser umidade então.
Material higroscópico, tem que estufar. Umidade ou contaminação ou temperatura e ciclo.
É só excesso de umidade, tem que desumidificar.
Esse nylon tem fibra, tem que está bem desumidificado.
Estufar bem o material e diminuir a temperatura e tempo de residência do material no cilindro.
Material úmido, pode ser novo, em saco laminado, mas existe vários fatores que possa afetar o material, é necessário estufar ou desumidificar. Precisa avaliar o tempo de residência tanto no funil quanto na retirada da umidade.
Material mal estufado vê se melhora a velocidade perfil se não verificar a estufagem temperatura.
Pode ser temperatura alta no bico ou descompressão alta e rápida, se o material estiver bem estufado.
Precisa estufar se caso não for estufagem é velocidade de injeção baixa e temperatura alta. Também diminuiria o tempo de residência do material no cilindro e por último deixar pouco colchão.
Esse material tem que estar bem estufado e comece injetando com velocidade baixa
Parece ser muita umidade. Porém, faz uma limpeza no cilindro da máquina, com um material sem abrasivos. (PP ou PA natural).
Autor – Segui algumas dicas aqui do pessoal sobre estufar, mas mesmo assim continua esse esbranquiçado na peça.
Este é um material que resseca muito e bastante rápido. É necessário hidratar, ponha num tanque de água.
Analisar a espessura da entrada podes estar muito restrita gerando cisalhamento do material.
Aumenta a velocidade de Injeção para as fibras não aflorar.
Velocidade baixa as fibras afloram.
Sendo com fibra, e depende da percentagem, pode ser a entrada de material para a peça “jito” parece pequena! A velocidade da injeção é alta pode provocar isso devido às fibras! Fugas de gás têm de ser boas.
Pode ser espirro e a contrapressão está muito alta, baixa um pouco a temperatura do bico e baixa a contrapressão.
Pode ser por má homogeneização entre a fibra e o P.A. Alguns lotes vem assim, para ajudar no processo é preciso tirar a umidade do material e nesse para ajudar na resistência está peça você pode tirar o ciclo da máquina e largar em um tanque com água para reidratar a fibra.
Homogeneização do material incompleto, material de viscosidade sensível à temperatura, um material resistente.
Aquecer o molde à 90 ºC, e aumentar um pouco a contrapressão, assim homogênea mais o material.
Autor – Material novo.
Autor – Máquina própria para nylon não injetamos outro tipo de matéria prima nela.
Autor – Está na estufa sobre recomendação do fabricante.
Mas quanto tempo? Se não for unidade é contaminação.
Com que temperatura está a estufando o PA.
Estás com que temperatura na máquina?
Autor – O fabricante aconselhou 110 ºC na estufa durante 4 h e cilindro está 265 ºC, 270 ºC, 275 ºC e 278 ºC, bico 270 ºC fabricante da matéria prima forneceu.
Aconselho baixar a temperatura para z4 – 235 ºC, Z3 – 240 ºC, Z2 – 245 ºC e Z1-250 ºC, quase certo que está degradando. Faça um teste.
As temperaturas parecem bem, o material não tem cargas certo é natural só com corante?
O corante é base de EVA, ou é próprio para PA?
Autor – Já vem na cor preta mesmo.
Geralmente é gás, estufagem e uma boa saída de gás.
Possível umidade no material e falta de saídas de gás no molde.
Deixa o molde com mínima pressão de fechamento para gerar rebarba no contorno se for falta de saída de gás já consegue analisar.
Gases, tem que observar a refrigeração e as saídas de gases. Falta de saída de ar.
Limpar bem o molde na saída de gás.
Solução – autor
– Tentei várias dicas, mas falaram em melhorar a saída de gás que iria resolver. Era saída de gás muito curta.
– Deram a dica aqui no grupo fui lá aumentei a saída de gás resolveu o problema.
– Na correria acabei esquecendo de colocar mais foi saída de gás no molde que estava curta, aumentamos acabou o problema.
Só saída de gás. Que bom que resolveu. Às vezes é tanta coisa complexa que pode estar acarretando isso. Uma simples saúde gás.
Peça quebradiça – Material PA

Autor – Começamos a injetar essa peça em nylon 6.6 – Está muito quebradiça, tive a informação que tem que colocar na água quente. Procede a informação?
Qual a temperatura e o tempo?
Comentários:
O Master é com resina compatível, ou seja, a base é nylon?
Verifique se o veículo é a base de PA porque senão vai ter problema de delaminação.
Trabalho com o mesmo material, mas com 15% de fibra. Em média 3-4 horas de hidratação com água a 90 ºC.
Isso mesmo, aqui cozinhamos as peças de 3 a4 horas.
Verificar se o material está bem desumidificado, após injeção, como é peça em Nylon precisa hidratar.
Aqui usamos o material estufado por 4 horas e o molde com água a 70 ºC, e o canhão com uma temperatura 260 ºC, 240 ºC,240 ºC e 220 ºC.
Autor – Sim, aqui estufamos também, porém fica quebradiça.
Tem que hidratar depois de injetado.
Onde trabalhei era 90 ºC por 2 horas na banheira.
Já tentaram usar GFN (glass filled nylon), vai ficar mais resistente e vai eliminar a necessidade colocar a peça para hidratar (reduz o tempo de produção).
Coloque na água quente por duas horas e depois pode até deixar na água com temperatura normal de um dia para o outro. Hidratada vai resistir aos dados especificados do fabricante.
Pode também trabalhar com PA com elastômero, acho que vai resolver seu problema.
Dê uma olhada na estufagem, desumidificação e % de reciclado.
Procede sim. Após a injeção, mergulhar as peças, por exemplo, em água a 80 ºC por 5 horas se a espessura da peça for 4 mm. Se for espessura menor, menor o tempo.
Temperatura maior, menor o tempo.
PA não é um material quebradiço, o material pode estar com muita umidade, precisa estufar por 4horas ou mais em uma temperatura de 90 ºC a 120 ºC.
Sim. Tem que hidratar ela. Só que antes da injeção tem que tirar a umidade do PA.
O nylon após injeção, se torna quebradiço e para ficar resistente tem que absorver a unidade novamente.
Caso for ferver, deve deixar mais de 5 horas.
Ou coloca em um tambor com água e depois deixa exposto ao tempo, em 24 horas ele retorna à umidade correta, e vai ficar resistente.
Após a injeção, o nylon necessita de hidratação. Com água aquecida é melhor ainda. O tempo vai muito da peça. Faça testes para ter o tempo.
A poliamida 6.6 tem que absorver água após a injeção para com isso ter um alongamento maior, ela satura somente com aproximadamente 4% de água enquanto a 6 pode absorver 8% de água no total.
Autor – Obrigado a todos.
Queima e falta de preenchimento – Material PA

Autor – Ponto da peça está dando queima e não preenche – Material PA 6 com 30% de fibra. Injetada com velocidade 145 cm3/s – Pressão 95 bar. Recalque de 4 segundos a 30 bar. Molde com sistema de bico quente e nenhuma saída de gás.
Comentários do grupo:
O correto seria fazer saída de gás, mas se poder aliviar um pouco o fechamento pode melhorar e se caso ao aliviar o fechamento der alguma rebarba diminua a pressão de injeção. Pode usar um pouco mais da descompressão. Se não melhorar faça um teste com dois pedaços de fita durex ou similar, colocando do ponto da queima até o final da placa.
Se está queimando e não preenchendo sô fazendo saída de gás difícil tirar na velocidade.
Saída de gás e velocidade de injeção.
Saída de gás pode ser sim, vê o tempo de injeção e temperatura, dá uma olhada na passagem do material se não está estrangulada, ou presta atenção na desigualdade de parede, veja que se estiver um lado mais fino que o outro dá esse problema também.
Espessura da mínima folga no fechamento.
Faz o inverso diminui a velocidade de injeção 75, aumenta a pressão de injeção 135 e também o tempo de recalque 5,5, vai tentar tirar o gás de dentro do molde lentamente e descompressão menor possível para não acumular mais gás ao injetar.
Pode ser irregularidade no molde, peça fina. verificar espessura da peça.
Diminuir a velocidade de injeção e tirar o travamento o máximo possível possa ser que esteja com muito travamento impedindo a saída de gás.
“Sem nenhuma saída de gás” impossível.
Quantos bicos? Se for só 1 a única forma é adicionando material até fazer o fluxo de injeção preenchendo do meio para extremidades. Abrir um pouco o molde e fazer muitas saídas de ar. Também pode colocar um pino nesta posição para saída de gás.
Será preciso confeccionar uma saída e uma verificação pela ferramentaria.
Se diminuir a velocidade e aumentar a pressão pode resolver. Porém sem saída de gás vai ser difícil. Pode até diminuir o recalque para 2 segundos, pois o recalque só vai servir para segurar até os gates solidificarem.
O material está mal, estufado. Caso seja material recuperado o tempo de estufagem é de 6 a 8 horas. Caso seja PA de qualidade tempo de estufagem 4 horas. Um detalhe a velocidade de injeção não pode ser maior que o bar de injeção. Caso isso não resolva verifique se não há vazamento no molde ou na cavidade do molde.
Saída de gás, velocidade de injeção, alivia o fechamento.
Já tive muitos problemas com pontos de queima, fazíamos saída de gás nas áreas afetadas, só dessa forma eliminava a queima, o gás fica preso, com isso provoca a queima.
Saída de gás, não há outra solução.
Depois trabalhe com a temperatura do molde e velocidade de injeção, deve ser lenta ao contrário do que alguns dizem.
Para ter a certeza, primeiro criar uma saída de gás nessa zona com fita cola.
Se nas primeiras resultar é depois voltar ao mesmo, já sabe onde está o problema.
Secar o material. Se não der rebarbas tirar força de fecho durante a injeção.
Tentar fazer um perfil de injeção para adequar a velocidade de entrada do material com a velocidade de saída do ar de dentro do molde.
Tira um pouco da altura e se necessário baixar um pouco as velocidade e pressões até fazer a saída de gás.
Se é PA6/30% FV, deve estar com o molde aquecido a aproximadamente 90 °C, isso permite que o material flua por mais tempo e permite o preenchimento de áreas mais difíceis no molde, e óbvio nesse caso de material de engenharia a saída de gás também é essencial, com saídas de gás eficientes e molde aquecido na temperatura certa essa peça ganha brilho e fica sem queima, sem saída de gás vai ser impossível.
A saída de gás é essencial, verificar se as espessuras do produto estão por igual em diversos pontos. Estufa o material, outro ponto importante.
Solução: Autor – Foram feitas saídas de gás e o problema resolvido.
Realmente sem elas se fazia impossível resolver este problema.
Marca de estrias – Material PA
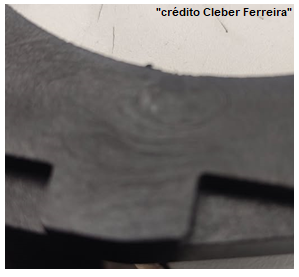
Autor – Como tirar essa marca no material….. Pa66
Comentários do grupo:
Quanto mais fibra tiver, mais fácil ficar aflorada, mas quanto menor for a porcentagem compacta bem no recalque que ela melhora.
Se for alta 30, 40% acerta na dosagem para ter menor atrito nas fibras e fluxo de material no canal.
Isso é no ponto de injeção ou na zona mais distante da injeção?
Canal quente ou frio?
Qual a temperatura do molde?
Qual o tipo de extrusão? Chapa, perfis e tipo de cabeçote, nylon com fibra ou liso? Tem uma foto mais nítida?
Aumenta um pouco a temperatura de trabalho, tira a umidade do material (o mais importante) e trabalha com mais velocidade de injeção.
Cara tira um pouco da descompressão, depois da injeção, as vezes dá certo.
Esse material parece ter algum tipo de carga, a peça uma boa espessura, subir a temperatura do cilindro para 260 ºC, mais ou menos, crie um perfil de velocidade lenta inicial, em seguida liberar toda, essas marcas devem sumir.
Fecha um pouco da contra pressão e também tem de conferir a saída de gás.
Velocidade está baixa. Se já estiver estufado corretamente, sobe essa velocidade aí que vai dar certo.
Sugiro verificar temperatura do molde, velocidade de injeção ser escalonada, quantidade de reciclado utilizado, estufagem e tempo de recalque.
É nylon com fibra ou natural?
São muitos fatores, entre eles a temperatura do molde que pode estar baixa e até mesmo a entrada de injeção que pode estar um pouco estrangulada não dando um fluxo eficiente na injeção.
Qual refrigeração tá sendo usada no molde, água normal, ou água gelada?
O material está com quanto tempo secando?
Geralmente está relacionado a umidade do material, o ideal é fazer uma estufagem adequada e notará melhora grande no aspecto das peças.
Vazando material pelo bico – Material PA
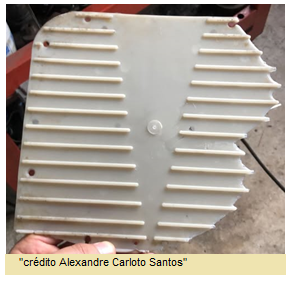
Autor – Dificuldade para injetar uma peça de nylon com espessura de 1,5 x 200 x 200 mm. Máquina uma Oriente IHP 60/100 mcp2. Tento dosar a máquina e o plástico fica vazando pelo bico e não completa a dosagem.
Comentários:
Tem que estufar o material.
Não conheço essa máquina, mas tanta zerar contrapressão.
Material úmido 150 ºC, estufa 12 horas no mínimo.
Fecha o molde e encosta o bico, aí abre a máquina e tira o que foi dosado e coloca para injetar.
Se tiver bolhas transparente está queimando, se tiver bolhas branca está úmido (bolha ou mancha).
Abre a contra pressão e pode ser que dose.
Estufagem, bico quente, e termopar pode não estar fazendo leitura correta da temperatura ou está aberto.
Pouca informação, está tentando dosar manual ou no ciclo?
O ideal é usar um bico valvulado para esse material.
O bico valvulado é bom, mas se o canhão estiver condenado, não vai ajudar.
Tente diminuir a rotação da rosca, reduza também a contrapressão e caso esteja trabalhando com bico recuando, programe para ele recuar um pouco antes de terminar o tempo de resfriamento.
Nylon é complicado, tem que ter certeza se está desumidificado.
Deve estar com compressor de dosagem acionado.
Verifique se o material está bem estufado e tente reduzir a temperatura do bico de injeção.
O seu material está úmido, o que dá para fazer só para estabilizar, é usar material virgem por enquanto até secar o próximo material, se precisar desliga o recuo de bico para iniciar a máquina e depois de uns 5 ciclos estáveis ligue de novo o recuo, tenta aí uma hora dá certo, e o nylon ele baba mesmo.
Já trocou a válvula de retenção da rosca, pois se diminuir a contra pode faltar carga.
Diminuir temperatura do bico, utilizar a descompressão, estufar o material, diminuir contrapressão, diminuir velocidade de rosca, diminuir diâmetro do bico e utilizar bico valvulado.
Saída de gás, temperatura de molde, mais temperatura no material, e pelo que aparece nesta peça o molde está mais aberto no sentido que está completando.
Anel de bloqueio já era, tenta dosar ela com o bico encostado ou até mesmo baixando a temperatura do bico, isso dificulta um pouco a passagem.
Aumentar a altura da dosagem e depois vai tirando na pressão de injeção.
Primeiro corrigir esse desbalanceamento do molde, pois quando conseguir completar a injeção, pode ocorrer rebarba de fechamento no lado que preencheu primeiro. Pelo visual do produto o ciclo é alto, tem que trabalhar com temperatura do molde alta. A temperatura do cilindro para evitar o vazamento, poderia por um valvulado ou mudar a bucha por bico fator.
Simplesmente a máquina está no limite de dosagem, por isso fica girando sem parar, a gramagem é pouca para essa peça.
Diminui a posição de dosagem e observa se a rosca para de girar. Pode ser por esse motivo de vazamento ela não preenche a peça.
Seu material deve estar úmido, precisa desumidificar.
Tudo indica que o material está úmido, mesmo virgem é bom estufar no mínimo 2 horas, e tira a contra pressão.
Abaixa um pouco a temperatura do bico.
Umidade, com certeza. O material deve estar com muita umidade, se possível troca o mesmo e observa.
É umidade no material, deve estufar o Nylon de 4 a 6 horas em uma temperatura de 90 a 120 ºC.
Tente aquecer o molde a uns 60 ºC, pode ajudar a completar a peça.
As vezes pode ser bico mal encostado na ferramenta, aí vaza e falham as peças.
Veja se está sobrando carga.
Coloca na estufa para secar, deve ser umidade do material.
Com certeza e escape de gás, coloca vai resolver.
Máquina muito pequena tem que trabalhar com bico valvulado, temperatura bem alta, também pode ser a rosca do canhão gasta.
Primeiro tem que saber se a máquina tem carga para injetar este produto, segundo tira toda contrapressão para visualizar a carga que tem e se vai sobrar pelo menos 5 mm de colchão para compactar seu produto, terceiro, coloca intrusão para completar se não der carga ok.
E se sobrar carga e não encher alivia o travamento, pois a saída de gás foi mal dimensionada.
Nylon tem que estar bem estufado.
Material trabalha à 240 ºC, tem que estufar 4 horas e nada mais.
Vamos começar pelo básico: Máquina e sua capacidade, nylon tem que ter seu tempo de desumidificação de no mínimo 4 horas, acredito que por umas 3 a 6 horas em uma temperatura de 50 ºC. Bico não está vazando? A contrapressão está toda aberta, não está estourando o tempo?
Abaixa a temperatura do bico e trabalha com o bico colado e abaixe a contrapressão e veja a temperatura do funil na entrada do material para o cilindro.
Parece estar vazando, também precisa saber se o material está estufado, se não estiver vai ficar jogando material direto.
Pode ser que a contrapressão está muito alta.
Deixa o molde bem aquecido antes de injetar. Se tiver como colocar óleo seria o ideal. Caso não tenha óleo, comece a injetar com PE ou PP ou PS mantendo a água fechada para aquecer o molde. Troque o bico, uso com cone reverso.
Poderia estar usando Intrusão para completar a carga.
Já tentou aquecer o molde com um aquecedor com água pressurizada, isso ajuda a fluir o material, e a temperatura do cilindro pode estar influenciando também.
Tem de ser mais específico quanto aos parâmetros que está usando para poder ajudar.
Qual a temperatura tem no material, qual a contrapressão, qual a temperatura no molde, tem bico quente ou canal frio? Pode ser muita coisa.
Quantas gramas é a peça?
A máquina é compatível com a peça em termos de dosagem e fechamento?
A máquina fica dosando com o bico afastado?
O material foi estufado?
PA 6.6 natural ou com fibra de vidro? Molde deve ser aquecido e a matéria prima estufada……mais cada processo tem a sua variação……..precisa analisar tudo isso……a máquina comporta essa peça?
Usar bico valvulado. Deixa o bico encostado no molde para dosar
Estufagem… aquecimento do molde ….
Instalar um bico valvulado para trabalhar com nylon, evita ficar purgando material.
Tenta estufar o material em uma estufa, sobre o material vazando tenta descompressão, mas pode ser que de mancha na peça. Tenta também por um aquecedor de água no molde e deixa a unidade injetora encostada.
Coloque um bico valvulado, o molde tem que estar bem aquecido, coloque um controlador de temperatura no molde de preferência à óleo e verifique a procedência desse material, parece Nylon com fibra e estufar esse material.
Se o anel de bloqueio estiver gasto o material vai carregar e vazar mesmo tempo.
No caso de umidade do material ele vai vazar e estalar. Precisa estufar de 4 a 5 horas a 90 ºC.
Coloca um bico valvulado na máquina.
Material deve estar molhado, já tirou o bico da injetora para limpar, às vezes.
Bico valvulado ou material está com umidade.
Verifique a temperatura do processo e estufagem do material ideal.
Troca o bico com uma passagem maior.
Aumenta a carga da dosagem.
Tempo de injeção também pode ajudar a encher, pressão velocidade.
Tenta aquecer um pouco mais o molde e estufar mais um pouco o material
Se for vazamento pelo bico, pode colocar um bico valvulado ou então verificar a contra pressão da máquina de não está muito elevada.
Aumentar a temperatura do canhão
Podem ser por vários motivos, mas pela área projetada do molde, me parece que a máquina não tem volume de injeção suficiente, pode começar verificando isso.
A contrapressão deve estar fechada, abre, dosa até o final, cola o bico e fecha um pouco.
São vários fatores que precisam ser analisados.
Material úmido (aquecer)
Capacidade de plastificação de tiver no máximo (ver se máquina tem recurso de intrusão)
Verificar bico se for normal (colocar bico valvulado)
Verifique se o valor do curso de dosagem na IHM está alcançado o set point que você colocou e se isso está batendo com a posição real do cilindro, se estiver diferente talvez o problema seja ajustar o sensor de posição do curso de dosagem.
Se a máquina estiver com folga no anel da rosca e o material muito quente, ele volta por trás, contando que a máquina parece um pouco pequena. Tenho uma peça bem parecida e precisei de uma máquina com no mínimo 150 Ton.
Atualizado em 15/01/25
Esperamos ter colaborado com os profissionais!
Fonte: Grupos Técnico em Plásticos e Injeção Plástica do Facebook
Apenas Resumo: Moldes Injeção Plásticos
Acesse: isso também irá facilitar o trabalho do profissional:
TABELAS COM VALORES PARA APLICAÇÕES DE TERMOPLÁSTICOS
INDICAÇÕES PARA O PROCESSAMENTO DE DIFERENTES MATERIAIS PLÁSTICOS – 01
INDICAÇÕES PARA O PROCESSAMENTO DE DIFERENTES MATERIAIS PLÁSTICOS – 02